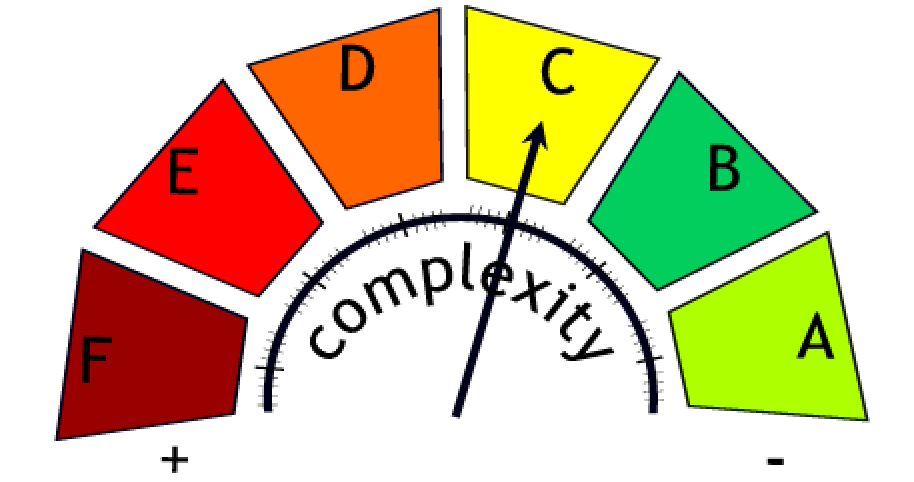
Tips for handling rebreather cylinders safely
For my thetis as a safety expert, I spent two years studying safe handling of oxygen under high pressure. It is therefore very tempting to write very extensively on this subject. However, the purpose of this page is to give very concrete tips to help the upcoming but also the experienced technical diver to handle his cylinders and more specifically his valves and taps safely. As a rebreather diver, you deal with cylinders that are used with oxygen or oxygen mixtures. If you are going to blend your own gases for your rebreather as a technical diver, it is important to gain in-depth knowledge about this before you start this activity. This page therefore does not replace training for blender or service technician.
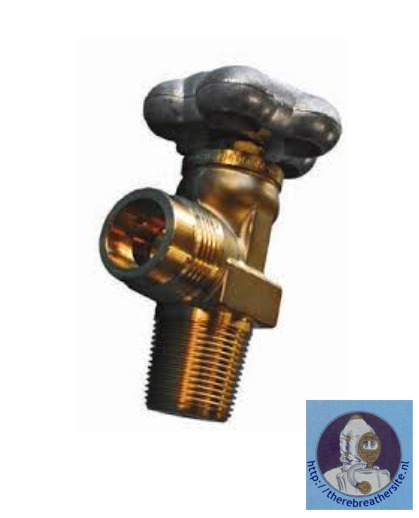
Shown above is an industrial oxygen valve. What makes this crane now suitable for high-pressure oxygen and used in large numbers problem-free worldwide? For that, the properties of material, how clean a valve is and the construction of the valve are important. Here in a nutshell:
- designed for use in high-pressure oxygen
- cleaned for use in high-pressure oxygen
- material properties suitable for use in high-pressure oxygen
- regularly inspected for safe use in high-pressure oxygen
- well protected against breakage and contamination
Notes:
Designed for use in high-pressure oxygen: the valve has a feature rarely mentioned in regular dive training. The valve has only 1 deflection of the gas flow, so there is in fact only 1 angle in it. This angle is often also specially shaped so that the oxygen flowing out under high pressure encounters minimal resistance and therefore no or very little heating.
Cleaned for use in high-pressure oxygen: All parts that come into contact with high-pressure oxygen are cleaned to the maximum with an oxygen-compatible cleaning agent (for example. simple green) in an ultrasonic cleaning bath and then rinsed with demineralised water and dried with high-pressure steam.
Material properties suitable for use in high-pressure oxygen: The body of the valve is made of a brass alloy that has the best properties for use in oxygen (maximum fire resistance). The seals in the tap are in an oxygen-compatible design. Tables of compatibility listings follow later in this article. By constructing the tap with a thick wall, heat dissipation is optimal. Brass conducts heat quickly unlike, for example, stainless steel.
Regularly inspected for safe use in high-pressure oxygen: industrial cylinders for high-pressure oxygen are inspected and cleaned by the manufacturer before filling. Due to the relatively high turnover rate, industrial valves will be regularly inspected by professionals.
Well-protected against breakage and contamination: manufacturers equip filled oxygen cylinders with a (plastic)cover cap. This will prevent contamination during transport (wasp in valve = oxygen fire!). Because valves in the Western world are protected with a bottle cap, if the bottle falls, the valve will not be able to break off.
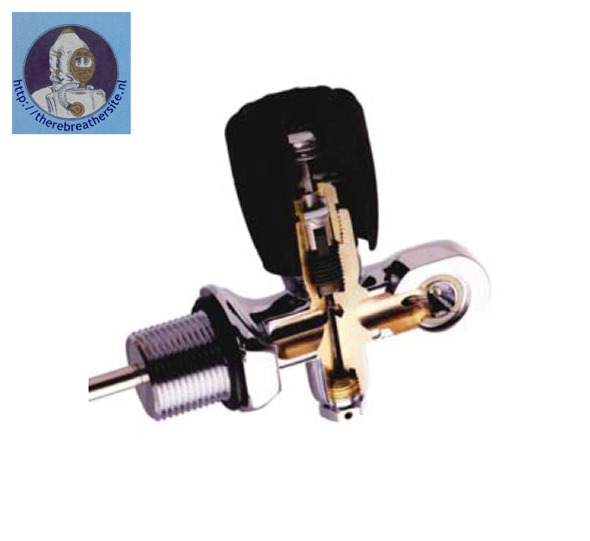
Accidents happen because divers do not realise that their valve is unsuitable to contain 100% oxygen. Many manufacturers will state that their valve is suitable for 40% oxygen and as such is a nitrox valve. Unfortunately, this assumes by many divers that the valve is then also suitable for 100% oxygen. The opposite is true! In Europe, EIGA (the counterpart of the US ASTM) has stated that all mixes containing more than 23.5% oxygen should be treated as being 100% mixes. The 40% rule deeply rooted in the diving world is a myth and should be consigned to the realm of myths.
So why would the above valve be unsuitable for 100% oxygen?
Designed for use in high-pressure oxygen? No this valve has multiple bends and sharp deflections and constrictions that allow oxygen forced through the valve at high speed and volume to heat up and lead to ignition!
Cleaned for use in high-pressure oxygen? A tap where it is not explicitly stated by the manufacturer that it has been cleaned for oxygen service will then usually fail to meet the cleanliness requirement. For example, the spindles are often lubricated with silicone grease and the sealing rings are greased. Grease and oxygen = fire
Material properties suitable for use in high-pressure oxygen? Although this tap is brass, it is then nickel-plated and chrome-plated. This can often lead to sharp edges where small metal particles can detach. These then collide with other particles which can also cause fire (particle impact). Also, the manufacturer will not bother to burr all edges optimally and make the flow path as smooth as possible.
Regularly inspected for safe use in high-pressure oxygen? In diving, bottles are often used under the most extreme conditions. Seawater and dirty hands will contaminate the valve. It is notable that good inspection stations always bring the entire bottle into oxygen service, including completely disassembling and cleaning the valve. This is not a half-hour job and therefore costs more than just hydrostatic testing of a compressed-air cylinder. Unfortunately, this statement is often deviated from under the pressure of price wars in the diving industry.
Well protected against breakage and contamination? A technical diver who takes care of his gear and body will always seal oxygen cylinders with a plastic protective cap. Sea salt and grease but also other contamination can lead to oxygen fire if used carelessly. Often heard is that divers have been handling their cylinders like air cylinders for many years and have never experienced an accident. This will certainly be true because divers who have experienced one will tell a very different story about it! Oxygen fires can cause very serious accidents where an exploding cylinder is no exception!
So how do I know that my tap is suitable for 100% high-pressure oxygen? In fact, the answer is not complex! It must be specified in writing by the valve manufacturer. Often Nitrox = 100% oxygen is said, but so this is pertinently not always correct. Only if the crane is supplied in oxygen service by the manufacturer, issuing a written statement with it, can its suitability be established with certainty. But beware: in addition, you should also have thorough knowledge of how to handle high-pressure oxygen!
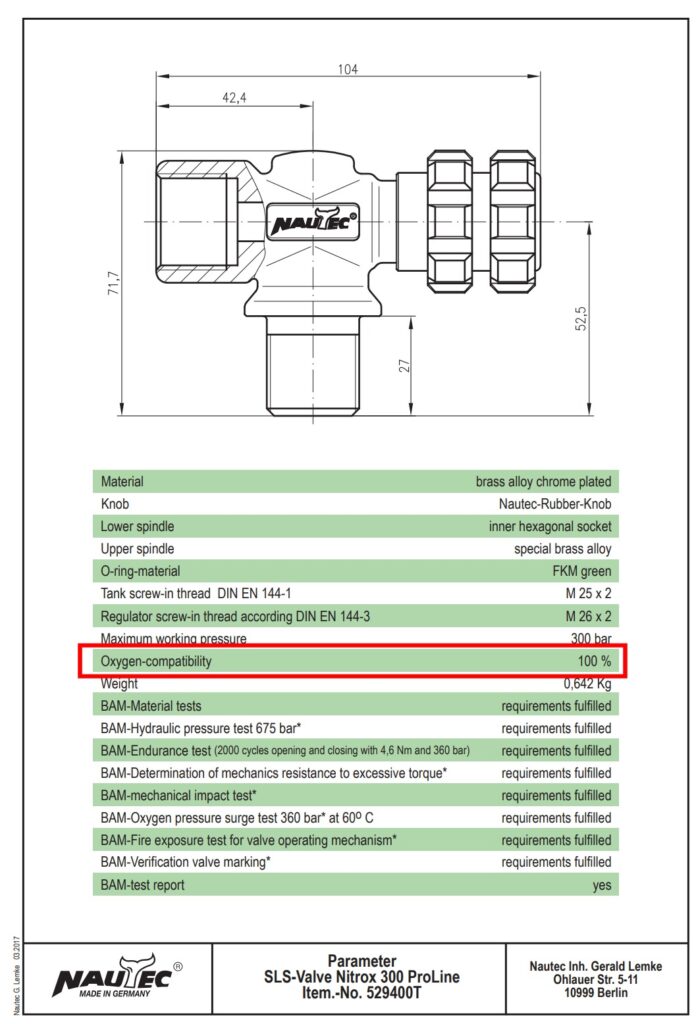
Tip 1: Always open the valve of an oxygen cylinder slowly until the final pressure is reached, open fully and turn it back a quarter of a turn
Tip 2: Always properly mark the contents of the cylinder
Tip 3: Always open the oxygen valve of the rebreather before hanging it on your back
Tip 4: Without too much pressure, blow the opening of the valve clean before connecting the pressure stage
Tip 5: Preferably use DIN connections
Tip 6: Use suitable O-rings and replace them annually
Tip 7: Have bottle and valve both cleaned in oxygen service
Tip 8: Ask the company about cleaning methods. If they use hydrocarbon-based solvents, find another shop
Tip 9: Fill cylinders slowly maximum 10 -20 bar pressure increase per minute
Tip 10: Oxygen first then top up with inert gas
Tip 11 Read this page when you fit a new valve
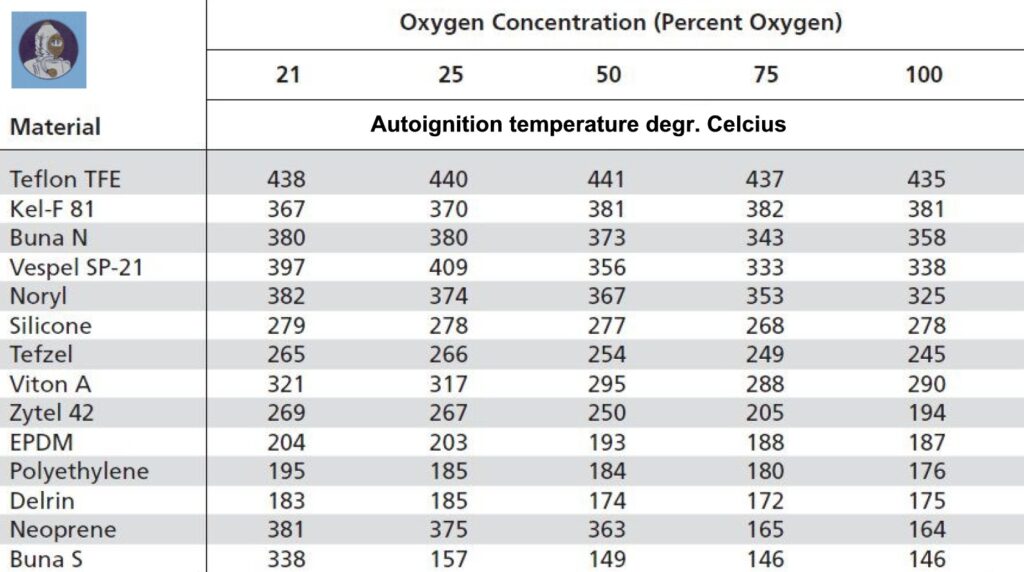
The table above clearly shows what happens to the oxygen compatibility of Buna S a widely used material for seals and O-rings. In a normal compressed air environment, Buna will only ignite at 338 degrees Celsius. In 100 per cent oxygen, this happens as early as 146 degrees Celsius!
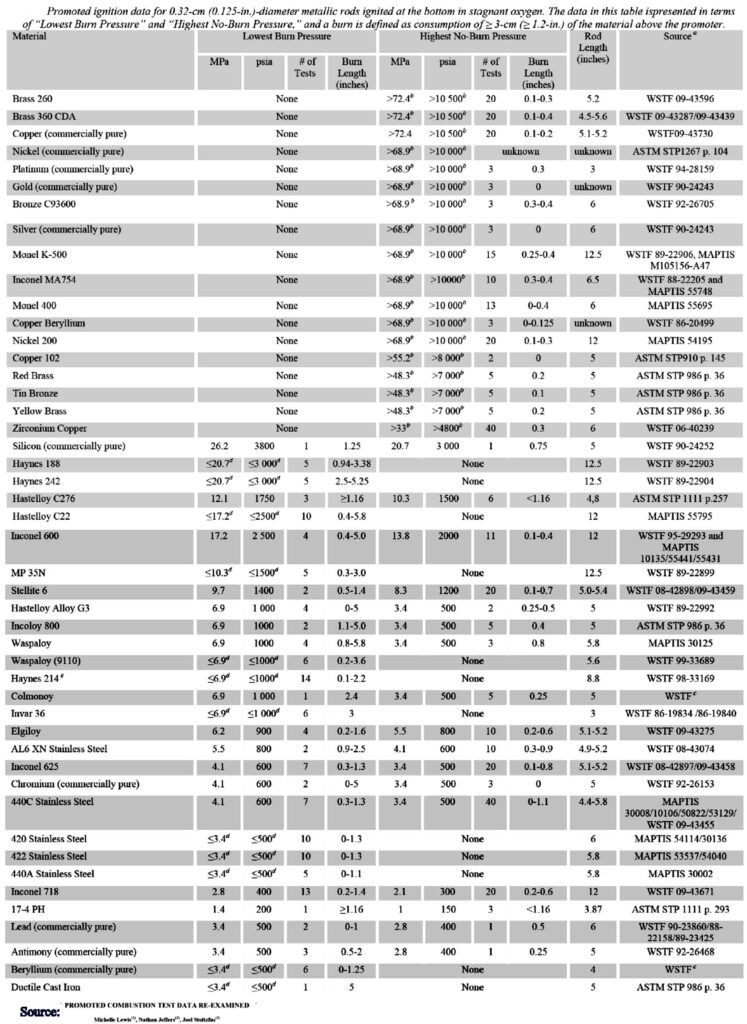
This list shows the compatibility of ferrous and non-ferrous metals where the material was ignited at different pressures. The highest pressure at which it just barely succeeds is shown here. It can be seen from the table that brass 260 only ignites at the top in 100% oxygen at a pressure of 72.4 MPa (720 bar!). Brass 260 is made up of 68.5-71.5% copper and 28.5-31.5% zinc. It can also contain up to 0.07% lead and 0.05% iron.
In contrast, 440C stainless steel will be able to ignite at 34 bar. This makes it clear why oxygen systems are often made of brass.
Titanium is completely unsuitable as a material for use in oxygen because fire tests show that in a 100% oxygen environment the material becomes flammable under 7 bar pressure!
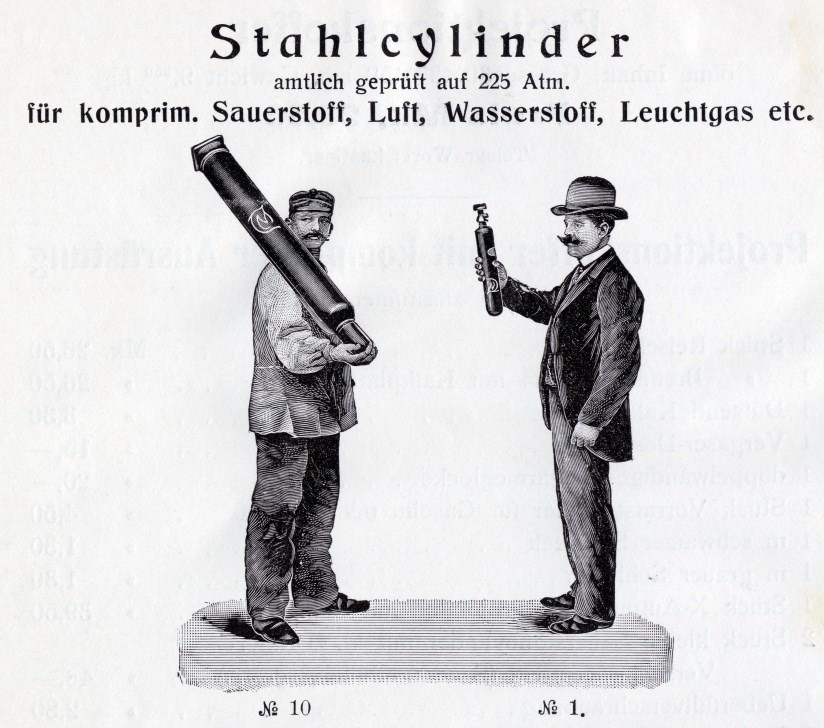
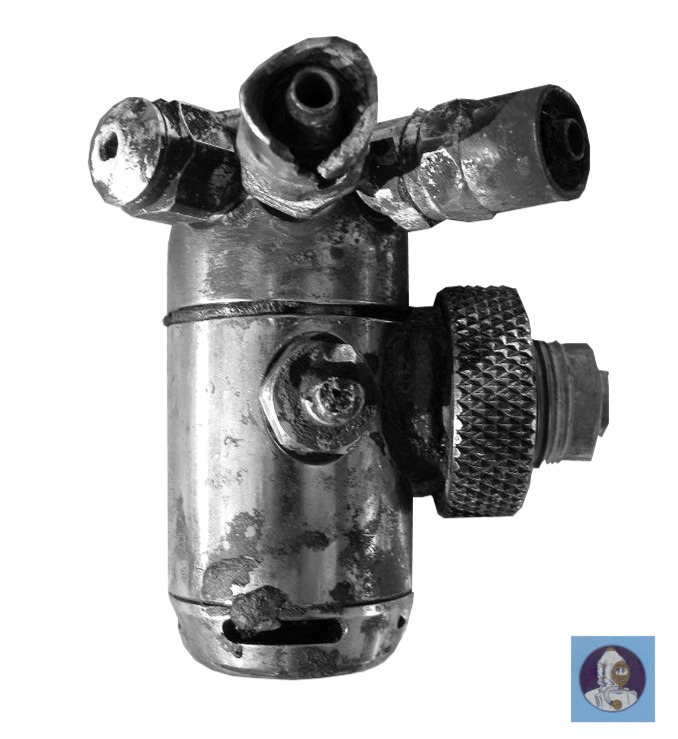
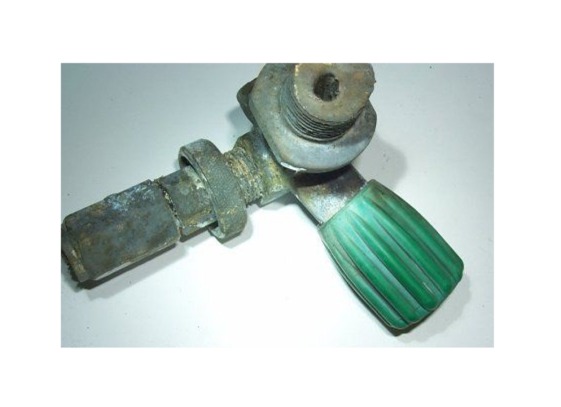
Please also read this https://www.divegearexpress.com/library/articles/why-40-max-oxygen-premix

Therebreathersite was founded by Jan Willem Bech in 1999. After a diving career of many years, he decided to start technical diving in 1999. He immediately noticed that at that time there was almost no website that contained the history of closed breathing systems. The start for the website led to a huge collection that offered about 1,300 pages of information until 2019. In 2019, a fresh start was made with the website now freely available online for everyone. Therebreathersite is a source of information for divers, researchers, technicians and students. I hope you enjoy browsing the content!