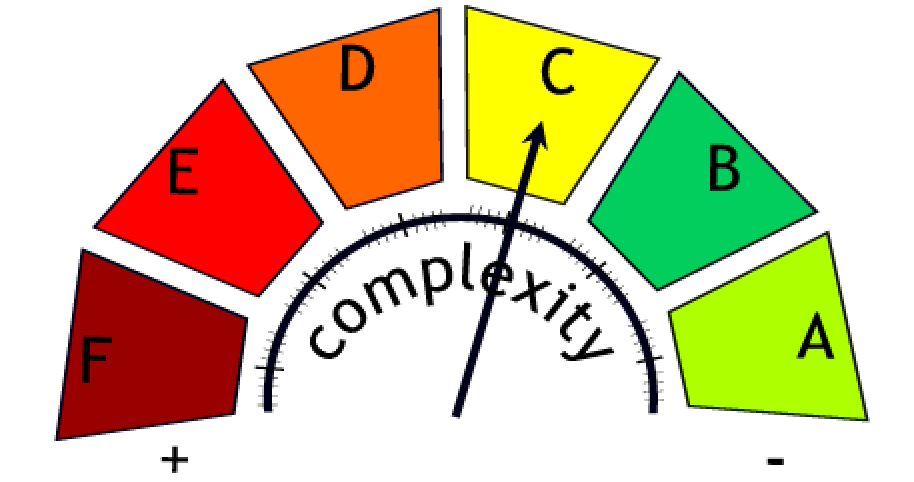
Liquid air & oxygen systems
The 1960s created high expectations of people living in underwater habitats. Large-scale investments were made in new technology, including the development of cryogenic breathing systems. Extensive research was carried out on this type of technology. Only a very limited number of models were actually produced. In general, developments were limited to a small number of prototypes. This page aims to provide as much information as possible about these developments. Cryogenic rebreathers have in their basic principle that with liquid oxygen or liquid air and heat exchangers the liquid oxygen is made gaseous and the man-made carbon dioxide is washed out with extreme cold.
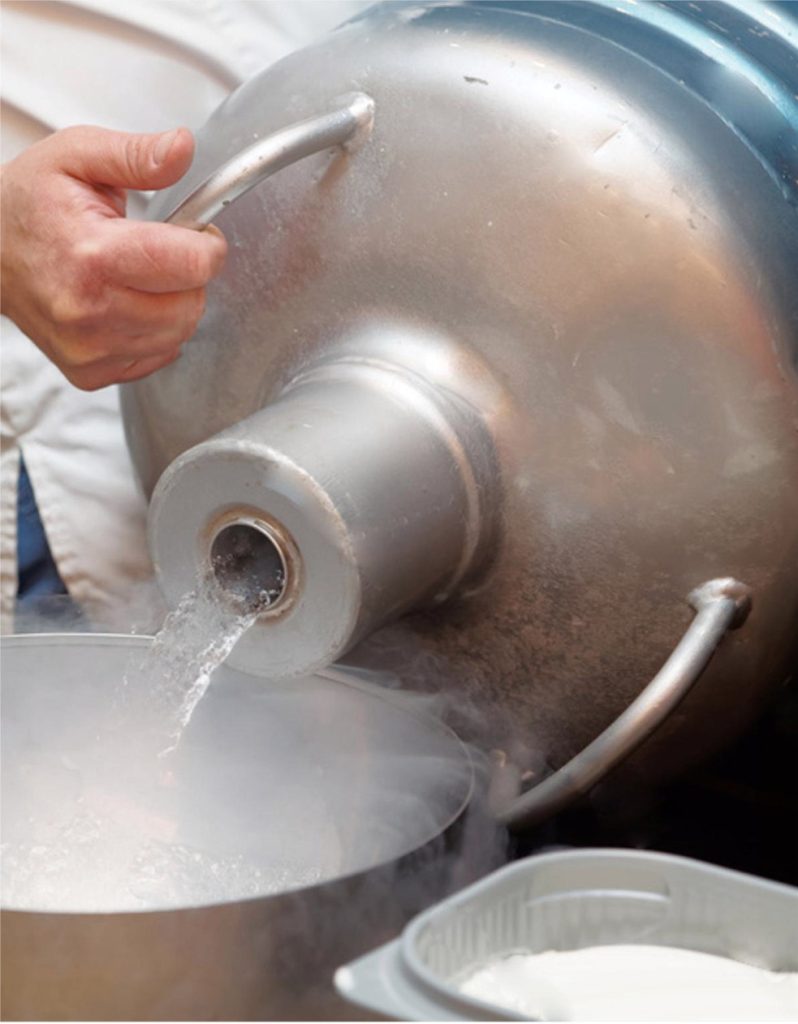
The use of liquid gases for breathing systems dates back to the 19th century. Linde’s invention to liquefy gases opened the door to the development of this type of breathing system. The most important development after liquefaction was the development of a method to preserve the gases in a liquid state over a longer period of time. In 1893, James Dewar demonstrated his Dewar flask, a thermos flask in which gases could be kept in a liquid state for a long time. Already 17 years later, the first rebreather was developed that worked with a mixture of oxygen and nitrogen. A technical problem that is still being worked on today (2022) is reliable filling indicators. Also the refilling of these systems on an industrial scale is still part of research programmes in both the UK and the USA.
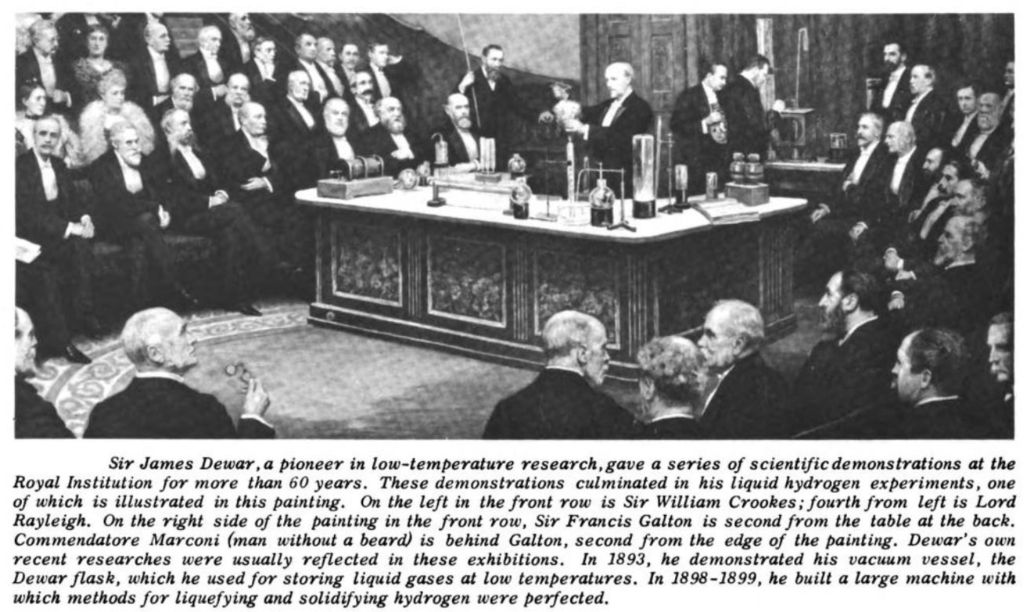
One of the first known systems that worked with liquid air was the Aerolith. This unit was developed in the Czech Republic by Mr. Otto Suez and the design was later sold to L. van Bremen.
CZECH REPUBLIC: 1906 Aerolith Liquid Air Breathing Apparatus
article originally written by Karel Pešorma 2014
No one realised earlier that air that could been liquefied and be used for breathing systems. Among the important properties of liquid air is that it converts liquefied air back into gas to a considerable extent. This circumstance has led Czech mining engineers to wonder whether the air thus liquefied could be used for breathing. The result of their hard work was the Aerolith breathing apparatus. Its inventor was the chief engineer Otto Suez in Vítkovice in Moravia (Tjechie).
Aerolith consists of a container containing liquid air, which as is known can only be stored in vacuum containers called Dewar flasks. These containers have a double glass wall, forming an airtight space that prevents the container from warming up.
The container into which the air is poured, is carefully insulated against heat. It contains asbestos wool on which 3,5 kg of liquid air is poured. To ensure that no more liquid air is poured in than this quantity, the apparatus is hung on a special segmented spring balance (Fig. 1), care being taken not to exceed the weight of the whole apparatus, which is 8,5 kg. Once the specified amount of liquid air is in the container, it is closed (but not hermetically). The container alone can hold up to 5kg of liquid air, which is enough for 3 hours. The specified amount of 3.5 kg is sufficient to breathe for 2 hours.
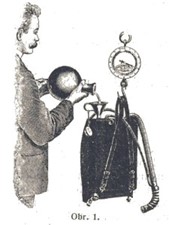
Through the top opening (see picture below) the air in gaseous state comes out of the container and through the nickel tube, which ends in a small hose with a diameter of 20mm, the air is led directly into the mask or into the mouthpiece which the firefighter has in his mouth.
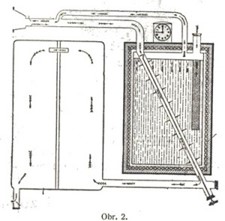
The exhaled air is passed through a special hose through a bottle of liquid air diagonally in the form of a ribbed tube. Under the bottle it ends at a branch to the left and reaches a special bag through which it passes in the path indicated by the arrows, after which it escapes through the lower opening into the atmosphere. During this journey, the exhaled air heats the container of liquefied air.
However, this respirator had a particular defect in that the gaseous air output was not sufficient to breathe at full load, and further, that the inhaled air was too cold. To avoid these two defects, the circulation of warm air described above was established.
Figure 3 shows the screw plugs for the lower pipes. Their purpose is to allow cleaning of the tubes because by removing the heat from the exhaled air, water is formed which is drawn into this bag.
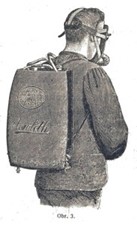
The device is also equipped with an alarm clock to alert the person in time that the air is running out.3.5 kg of liquid air is sufficient for two hours of breathing and the alarm clock is set to ring in 1.5 hours.
Aerolith performed invaluable services in the mines. According to reports, he was professionally examined several times by Prof. Schwarz in Mor. Ostrava and proved himself excellently. Also, even large city corps began to introduce this apparatus, as it has the advantage that there is no need for any hoses for air supply and its weight is only a fraction of similar apparatus which often weigh 13-15 kg whereas this one weighs only 8.5 kg.
The manufacture of this breathing apparatus has been handed over by the inventor to the factory of L. Bremen and Co. in Hamburg and the price is about 400K even with the weight. In the Czech Republic it was possible to buy these devices through the company R. A. Smekal in Smichov.
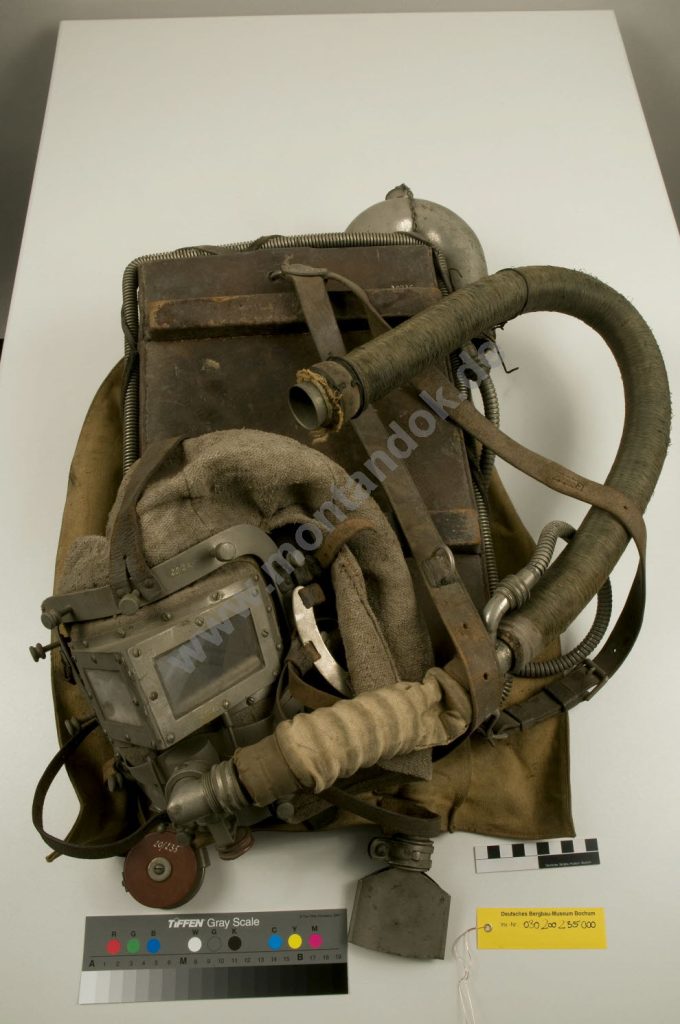
Around 1904 the production was transferred to Hanseatische Apparatebau-Gesellschaft, form. Ludwig von Bremen. After 1906 several models were further developed by von Bremen of which a fine example is shown above. The photo shows a machine that is in the mining museum. This picture was published with permisson by: Deutsches Bergbau-Museum Bochum – Leibniz-Forschungsmuseum für Georessourcen. “Aerolith-Gerät, Modell 1906” last modified 2021-11-29. https://westfalen.museum-digital.de/object/14739
liquid oxygen or liquid air?
The term “liquid air” can be misunderstood. Liquid air contains approx. 50 % oxygen when it is freshly liquefied, and over 60 % oxygen after standing for some time. Liquid air is produced by the expansion of highly compressed air (up to 200 at) and the resulting cooling in the countercurrent air liquefaction apparatus (Linde process). There it is brought to its boiling point, which is – 195°, and is then as liquid as water, and can be kept and used in specially designed open vessels. In this state, liquid air has the tendency to evaporate with all its force. Its evaporation is only stopped and impaired by the fact that it cannot obtain the necessary amount of heat, which is necessary for the transition from the liquid to the gaseous state, from the environment with any speed. The better the storage vessel is protected against the supply of heat, the longer the stored quantity of air remains liquid. Air consists of 1/5 oxygen and 4/5 nitrogen amongst others. A liquefaction apparatus can initially only liquefy the air. However, the apparatus can be equipped with a rectification device to separate the nitrogen in the gaseous state. In this case the plant supplies liquid oxygen. When the liquid air evaporates, the nitrogen evaporates first because the boiling point of nitrogen (- 194.4°) is lower than the boiling point of oxygen (- 181.5°). In a breathing apparatus for liquid air, there is therefore a risk of suffering from a considerable lack of oxygen in the first half of the breathing time, especially right after the start. Only gradually does the breathing air become more oxygenated. To avoid the danger of oxygen deficiency, liquid oxygen is preferable. In previous literature on liquid air breathing apparatus, the term “liquid air breathing apparatus” has become commonplace, although it is well known among experts that in this case the term “liquid air” means liquid oxygen or liquid air with a high oxygen content. In the descriptions, the term “breathing apparatus for liquid air” is used in the following sense.
Germany 1920 Draegerolithe
Dräger produced its first liquid air device in 1920. The system had no recycling function.
United Kingdom 1910: Blackett’s Aerophor Brown-Mills type
The Blackett’s Aerophor, from the Greek, meaning air-carrier, was a form of breathing apparatus, introduced in the Durham area in 1910 by Col. William Cuthbert Blackett (1859-1935).
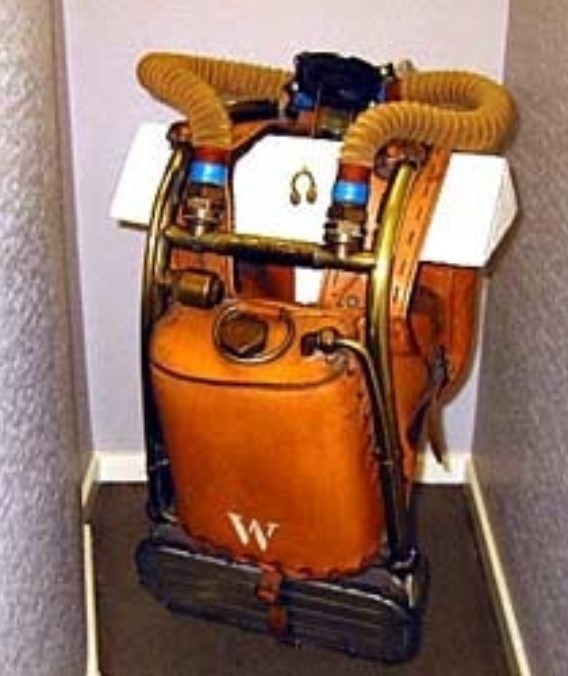
Col. William Cuthbert Blackett
William Cuthbert Blackett was born in 1860. The son of Dr. W. C. Blackett, he followed his father to Durham School and went on to the Durham University College of Science at Newcastle. He worked in fitting shops and coalmines, became a mine manager and chief engineer, and specialised in colliery explosions and rescue work. He was managing director and mining engineer of the Charlaw and Sacriston Collieries, and a director of the Houghton Main Colliery and other companies.
Blackett was elected a member of the Institute as a student in 1876, became an associate member in 1885 and a full member in 1889. Blackett was a member of the Council and Vice-President, before becoming President between 1912 to 1914. He was also an honorary member of the American Institute of Mining and Metallurgical Engineers.
During the First World War he commanded several territorial battalions and served in France in 1918 (being made a CBE). William Cuthbert Blackett died on the 15th of June 1935.
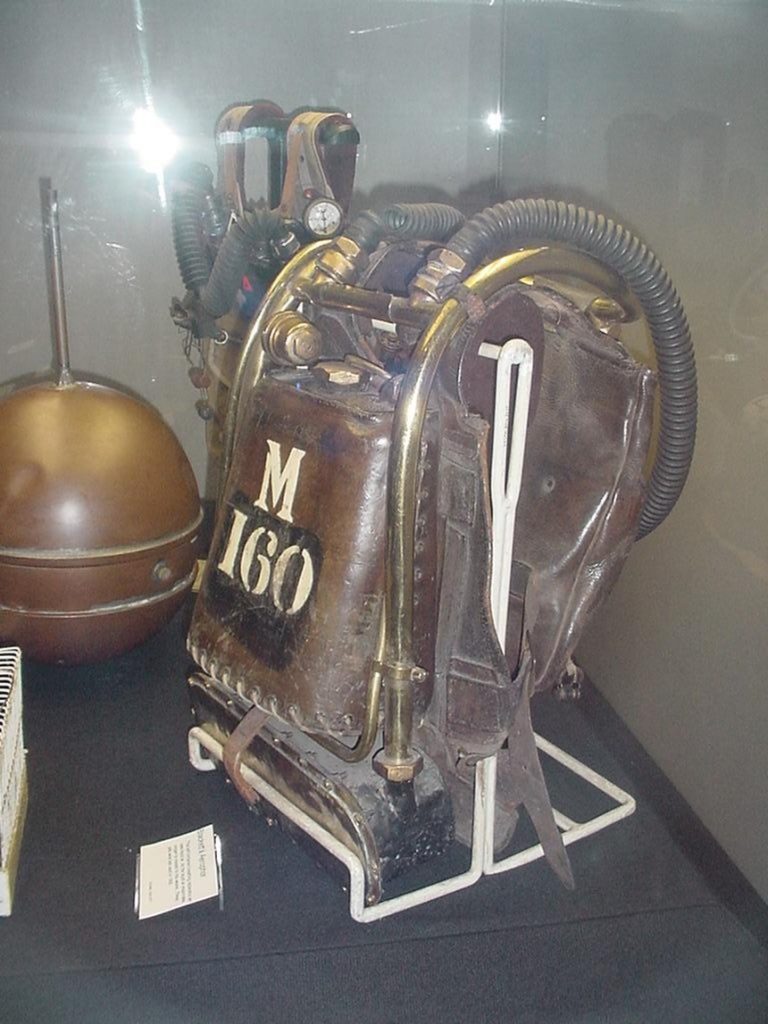
Blackett’s Aerophore
The device is a further developed type of the “Aerolith” from SueB. In contrast to the basic design, it is a regeneration device. The exhaled carbonic acid is bound by a potassium cartridge (subject of the Blackett patent). Walker, Haldane, Briggs give the following description of the device, which is practically used in England: A special feature is the curved connecting tube A, which wraps around the neck of the wearer like a wide collar. It connects the device bag to the rest of the circulatory system and allows the device to be carried through the shoulders. The head cap, nose clip, breathing mouthpiece, saliva trap (with ball check valve) and the flexible breathing convoluted hoses are essentially the same as in the Briggs device. A chin guard is provided to prevent the chin from dropping down and possible inhalation of outside air. The container P for liquid air is provided with an opening in the middle for filling. Filling is done by means of a funnel. The liquid air is sucked up by burnt asbestos wool WW, which is tightly packed in a box B made of nickel silver. There is a cavity C around B; it serves to distribute the liquid air during filling and to collect the evaporating air. It flows through the pipe G into the space E, which is loosely filled with asbestos. From the upper part of room E, the gas flows into the metal heating tube H, through which it enters the collar tube A. D and F are nickel boxes. Box F serves as insulation and retards the entry of heat by layers of magnesite asbestos J. Felt K and by a cover L of strong leather fastened on the outside with cords. The chamber E has a threefold function: 1. it allows air to move in order to absorb heat; 2. it acts as a barrier to the liquid which would escape through the tube G if the container P were overfilled; 3. it prevents and regulates to a certain extent the flow of heat to the inside of the container P. The breathing bag M, which is placed on the chest of the wearer, is protected by a canvas cover, is made of rubber fabric and is almost circular;
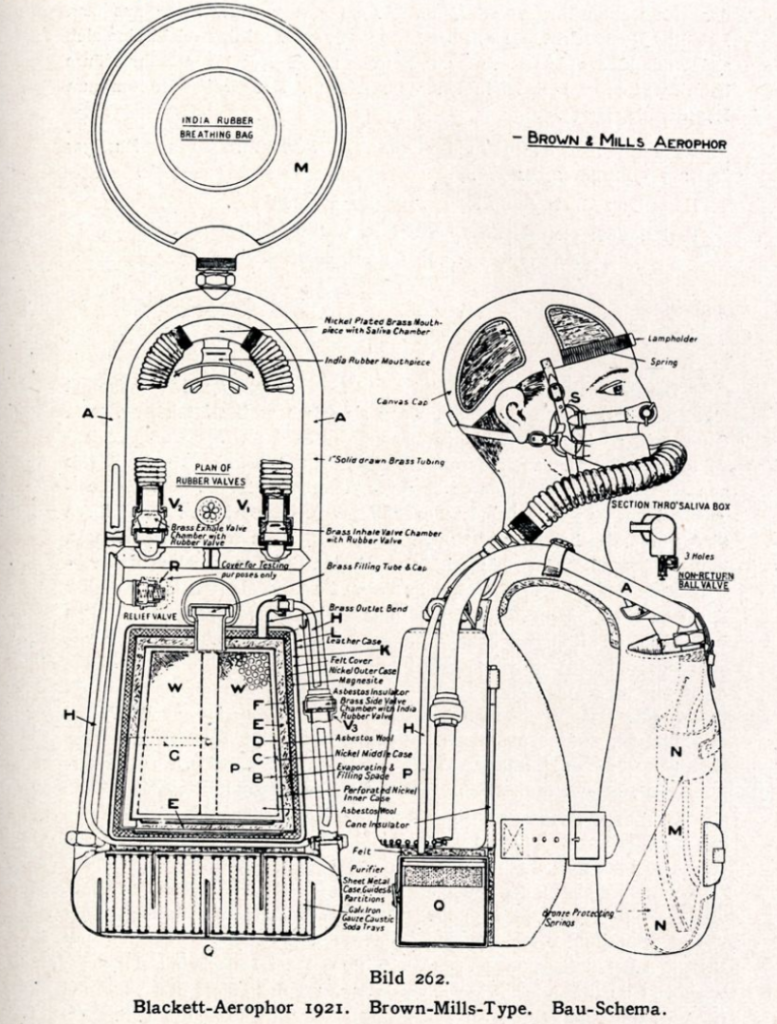
It has a capacity of 6 litres. In order to prevent the bag from being pressed flat, strong curved bronze pieces NN are attached inside its cover, which enclose the breathing bag at the top and sides. V J is the inhalation valve, V 2 is the exhalation valve. In order to prevent a backflow into the regeneration cartridge Q in case of a strong excess of air, the check valve V3 comes into operation. Excess air escapes through valve R, which opens at an overpressure of 3.5 inches. When a water test is carried out to check the tightness of the unit, valve R is closed with a screw-on cap. The regeneration cartridge does not represent a new type. It consists of a metal housing divided internally by 5 walls to define a zigzag path for the air flowing through. Between each pair of walls are three shells of strong iron mesh protected by a galvanically produced coating; the air flows in parallel between the shells. The cartridge is filled with 2 pounds (0.906 kg) of granulated caustic soda (sodium bicarbonate), insulated with felt against the container of liquid air and against the body of the apparatus carrier. The back of the wearer is protected against the container P for liquid air by a vertical tube frame and by a canvas jacket supporting the whole apparatus. Breathing procedures. When the device is put into use, more air flows into the respiratory system than it requires. It is therefore not yet necessary to let the wearer breathe in purified exhaled air again. During this time the regeneration cartridge is not yet needed; the exhaled air flows out of the tank P through the excess air valve R together with the excess air. If, however, less air* escapes from the reservoir P than is needed by the lungs, an increasing amount of exhaled air flows to the cartridge Q, where it is freed from carbon dioxide and re-enters the breathing circuit. The device now becomes a regeneration device. Weight (loaded): 40 pounds (18.120 kg). Weight of liquid air charge: 5½ pounds (2,491 kg). Manufacturer: Guest & Chrimes, Rotherham (England),
Variations: Rotherham type by E. Ellinson; Brierley type at Brierley Station.
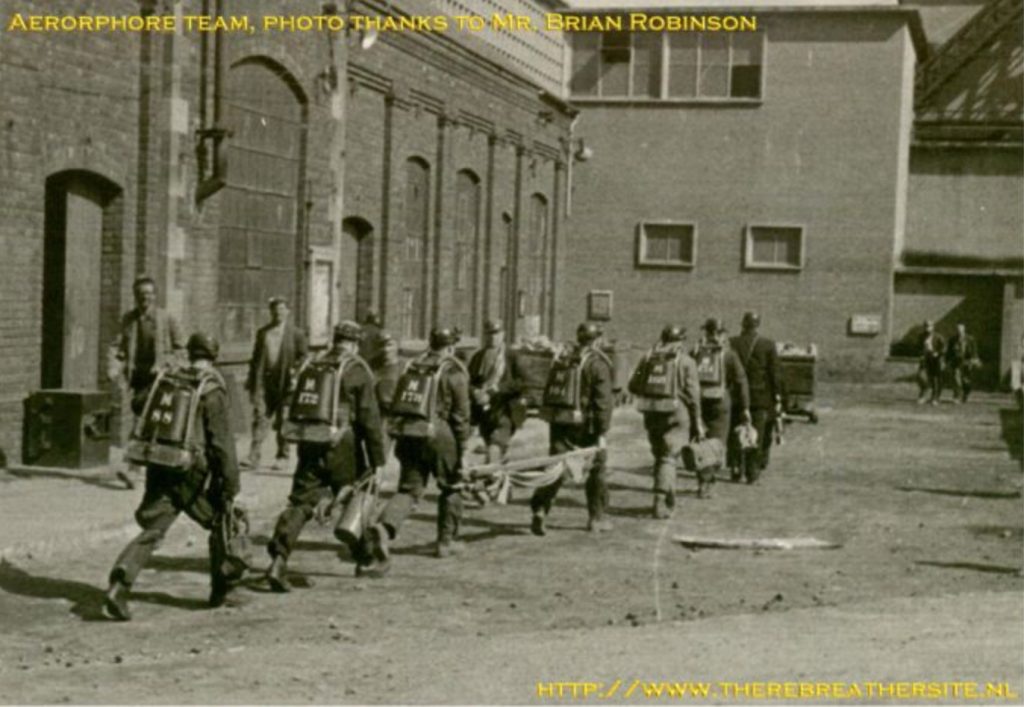
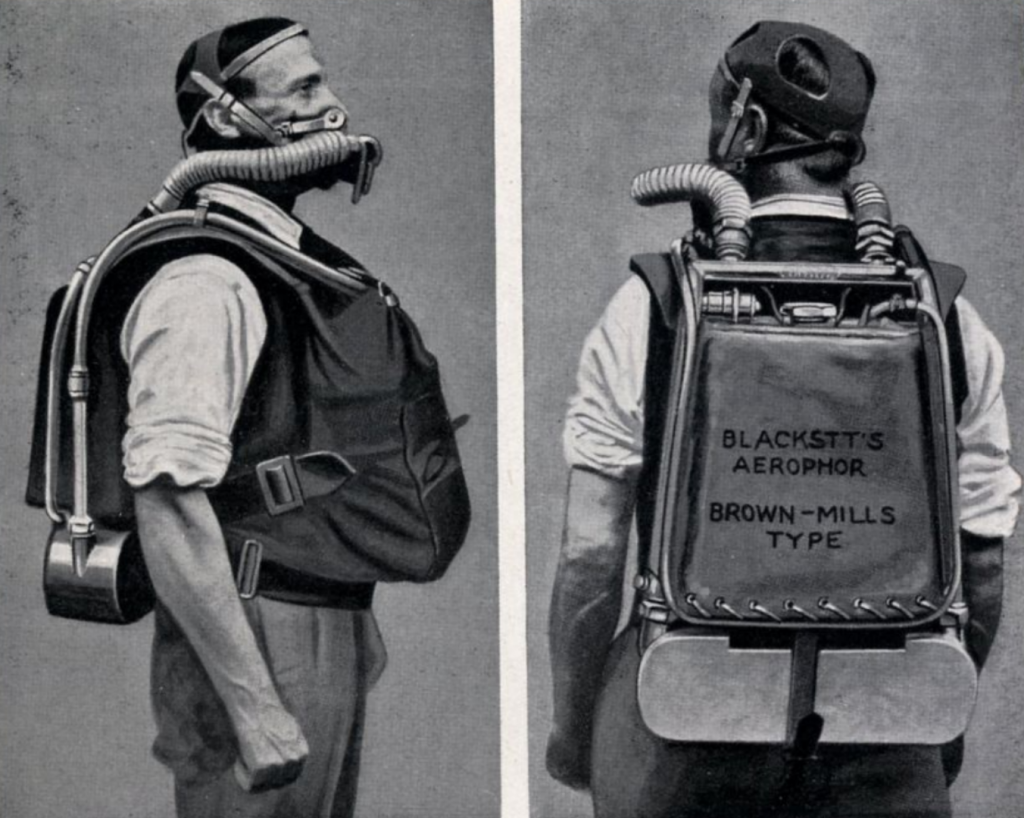
A second model of Aerophor of an improved type was the Brierley type introduced in 1922
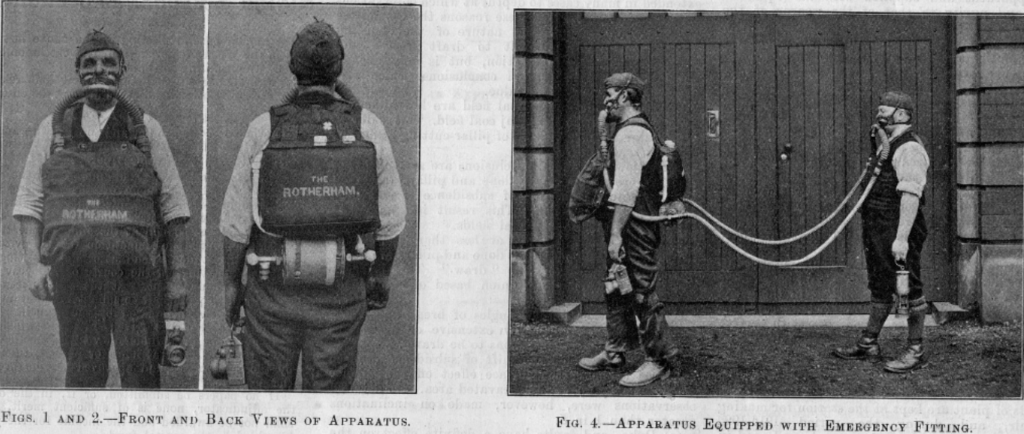
A third type called the Rotherham Aerophor introduced by E. Ellison.
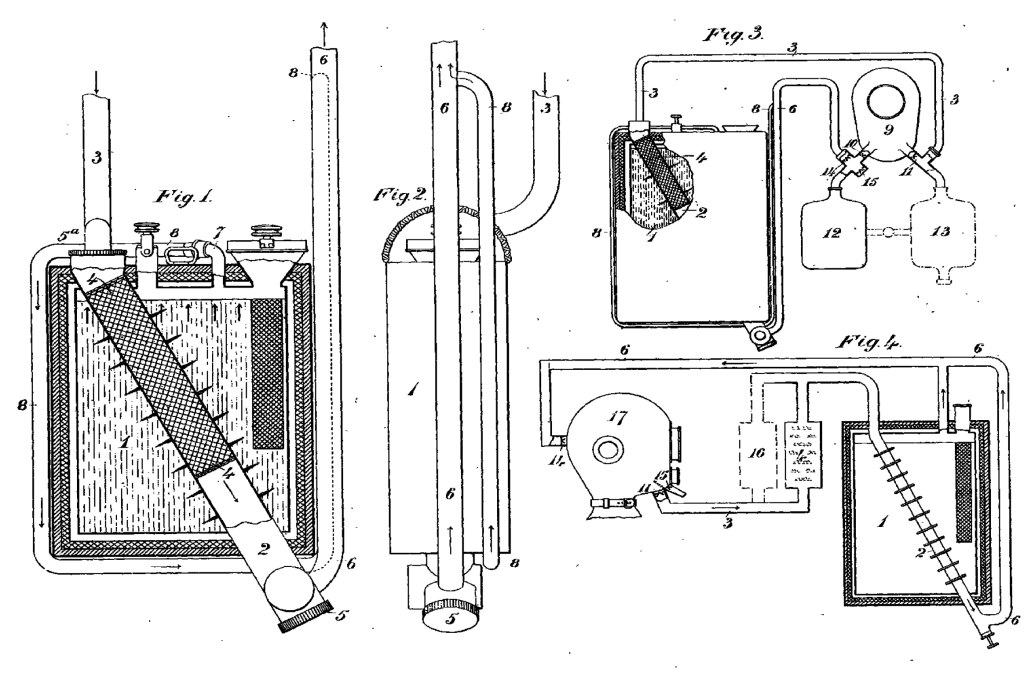
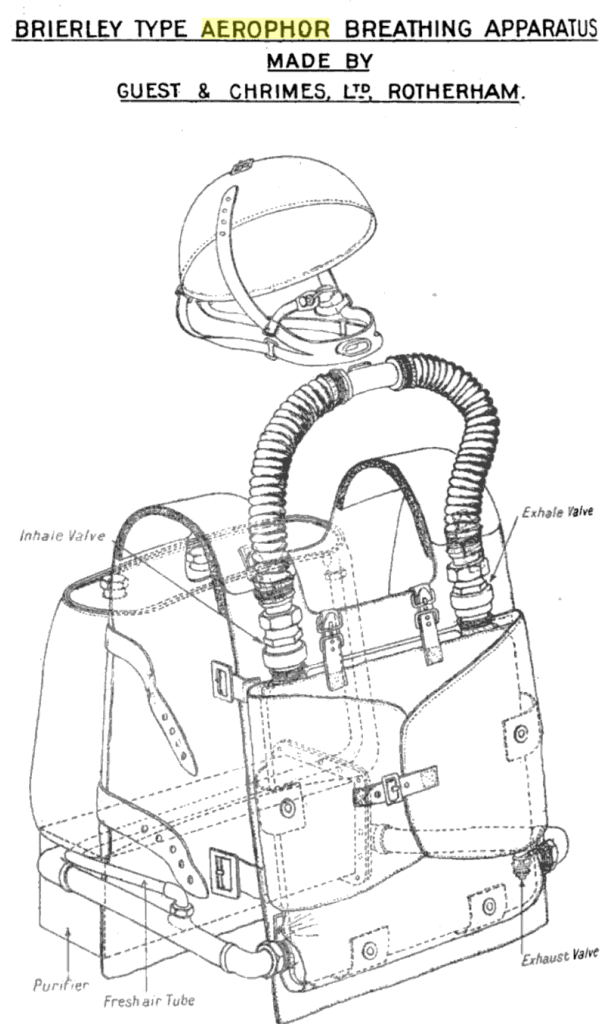
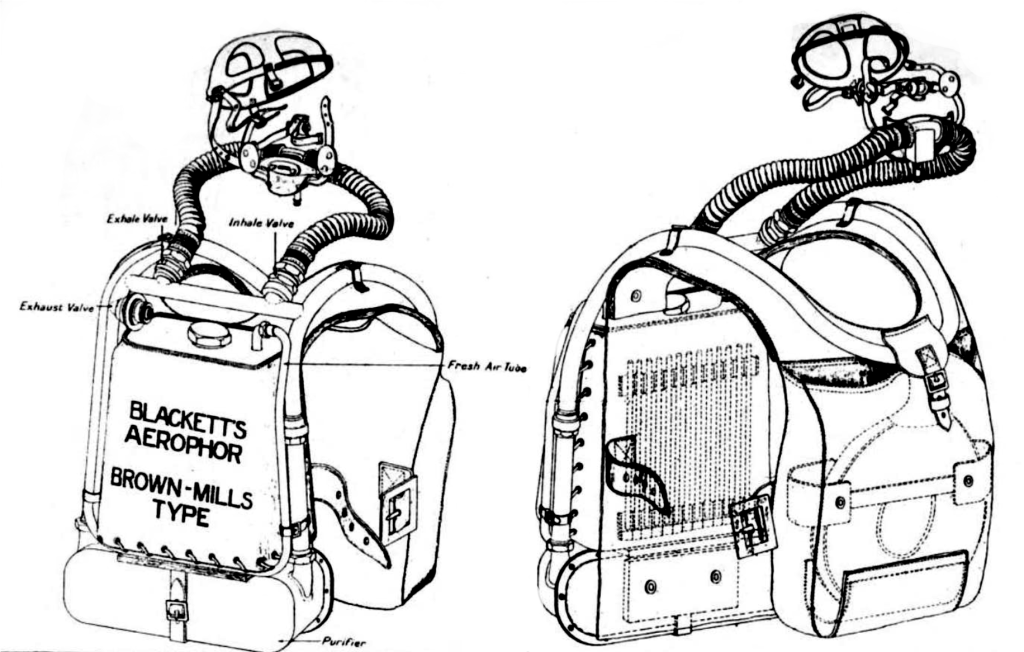
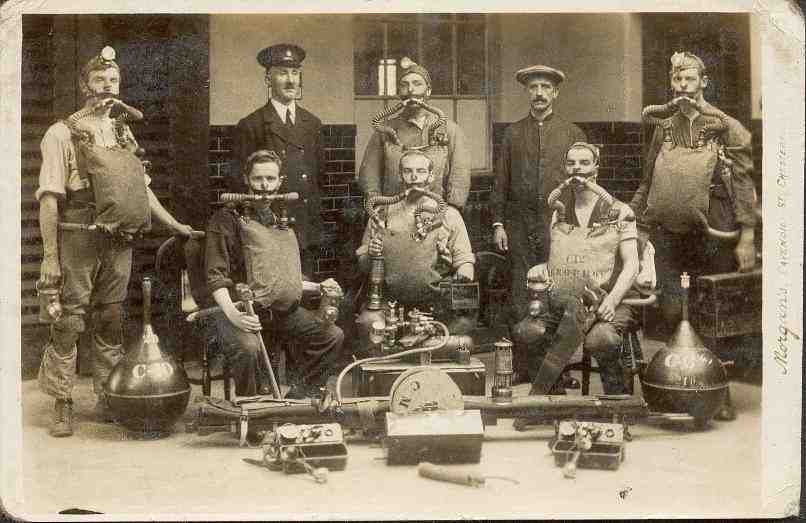
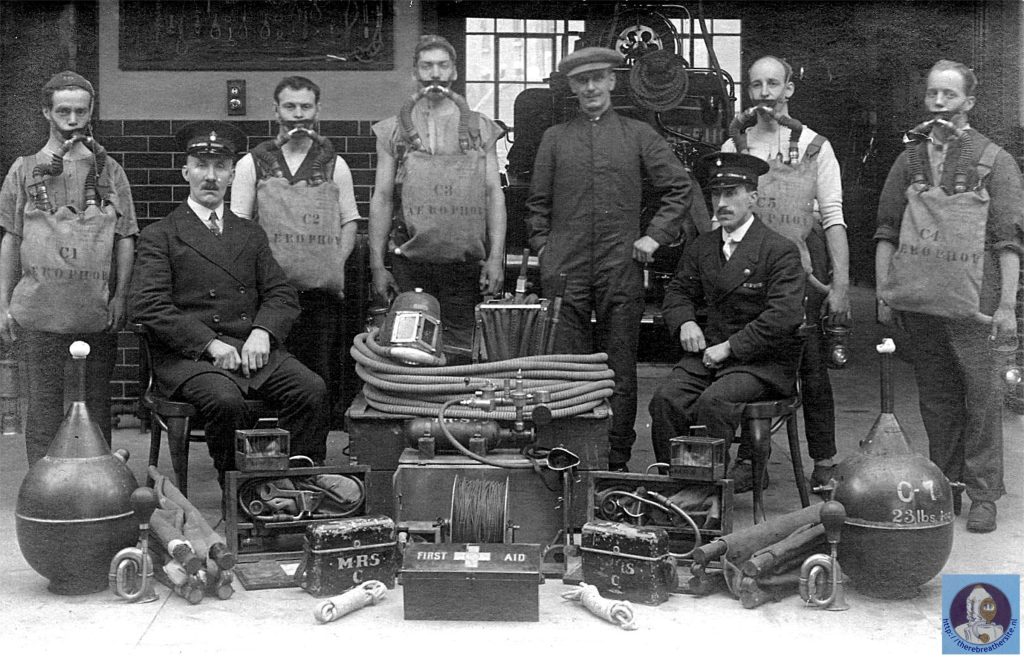
Man in Aerophor set C3 is Bob Harrison.
Photo courtesy of Christopher Green (Mr Harrison’s great nephew)
this picture shows the smoke fighting helmet, the co2 detection birds, the liquid air flasks and the AEROPHOR!
I would like to thank Mr. Harrison for his permission to publish this fantastic photo!
Professor John Singleton of the Sheffield Hallam University kindley gave me permission for the publication of this paper:
Breathing Apparatus for Mine Rescue in Britain, c. 1890 – c. 1930, thanks John! Highly appreciated!
I received the following three beautiful photos from Danny McGurk, for which I would like to thank him. A fantastic set of photos of his own Aerophor!
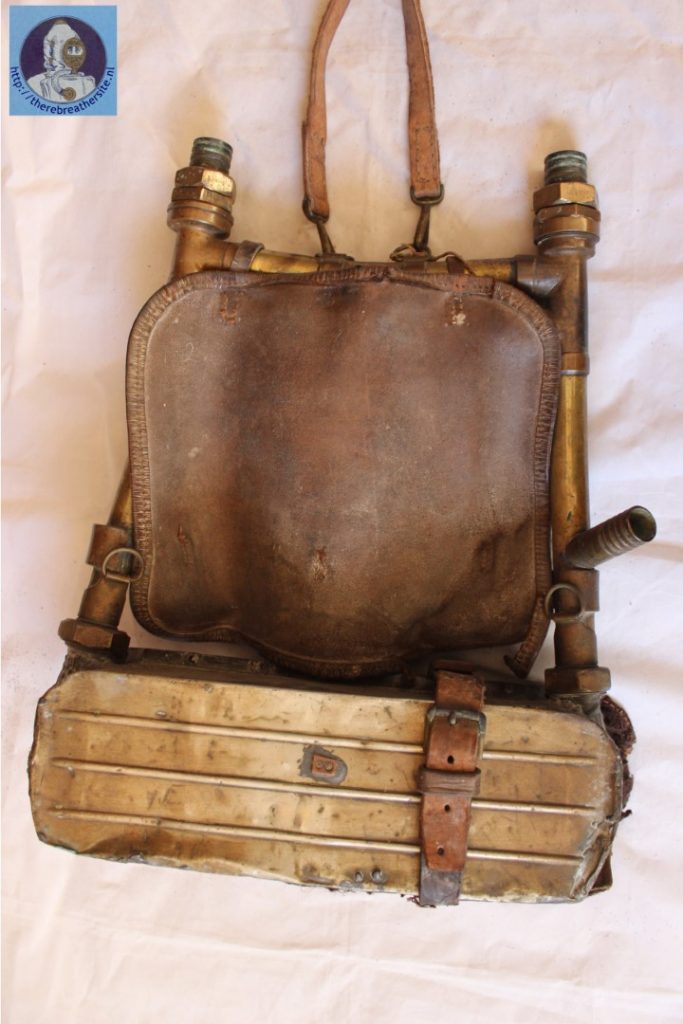
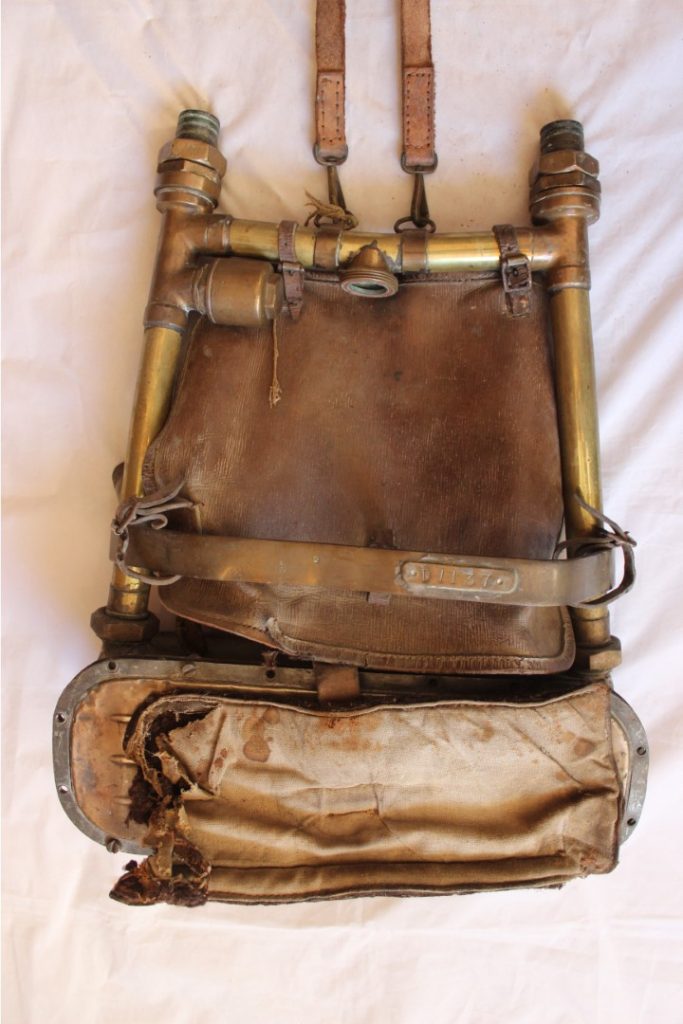
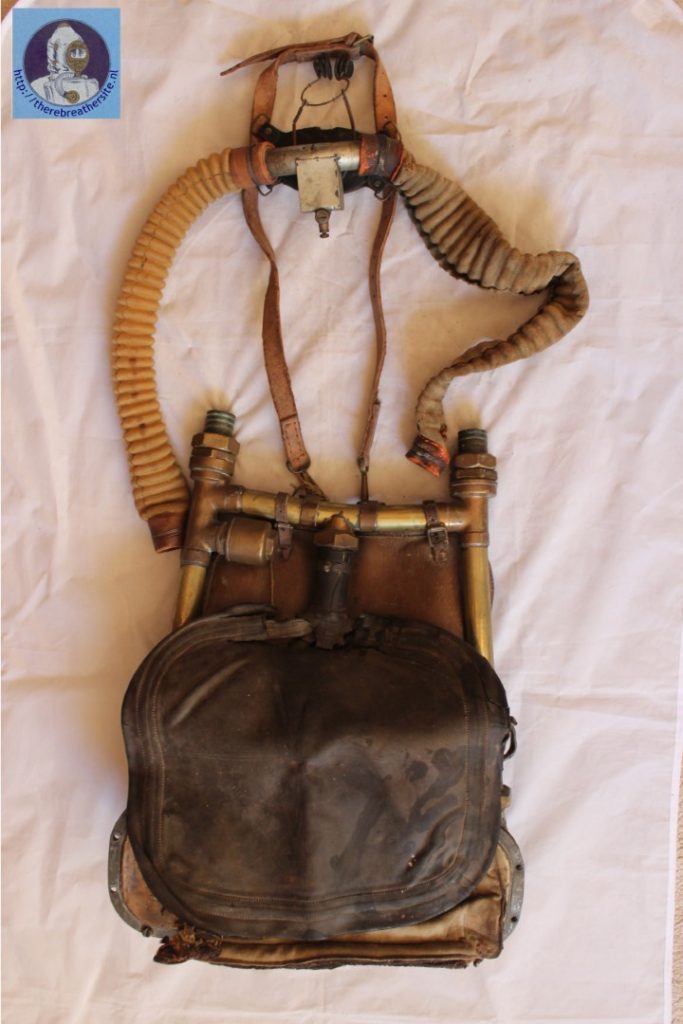
UK Siebe Gorman Aerorlox 70’s
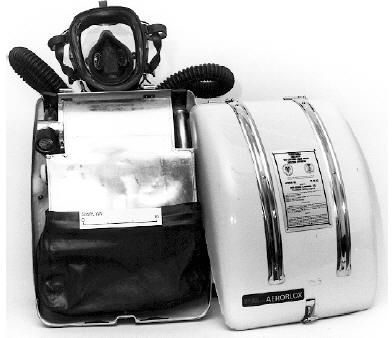
Another cryogenic unit that was build in larger numbers was the 1914 Aerophor. Another known unit from the UK was build by Siebe the Aerorlox.
In the early 1970s Siebe Gorman produced the Aerorlox cryogenic rebreather. The lightweight unit of 13.4 kg was produced for several years but died a quiet death due to the complexity of filling and producing liquid oxygen. Apart from the fact that the production of liquid oxygen was difficult to achieve on a small scale, liquid oxygen also posed an explosion hazard because it was susceptible to detonation by mechanical impact. The device received a certification from the US Bureau of Mines and OSHA. The device was classified for 3 hours of operation. Tests showed that it could be used for 210 minutes. A practical problem was that due to the use of the liquid, a manometer did not function in such a system. The user had to work purely in time, so a built-in clock was part of the standard equipment. The unit delivers a volume of 6-12 l/min through vapourisation of the liquid oxygen, so that during low-energy use, gas regularly escapes through the overpressure valve fitted in the circuit. The radial refillable scrubber was filled with protosorb, a mainly CaOH-based CO2 absorber. The device was filled with 3 litres of liquid oxygen. Since 1 litre of liquid oxygen after evaporation delivers approx. 860 litres of gaseous oxygen, a comparison can be made with compressed air. 3 litres of liquid oxygen is equivalent to a similar amount of compressed air in a 13 litre cylinder at 200 bar. However, if this is used in a rebreather with only 1-2 litres of oxygen, theoretically 22 hours of breathing is possible. Unfortunately, this is not a realistic value because the evaporation is not controlled and the excess gas will escape through the pressure relief valve. Another problem is that the scrubber functions for a maximum of 3 hours in atmospheric conditions. However, it is a great advantage to use liquid oxygen as a gas source compared to compressed oxygen.
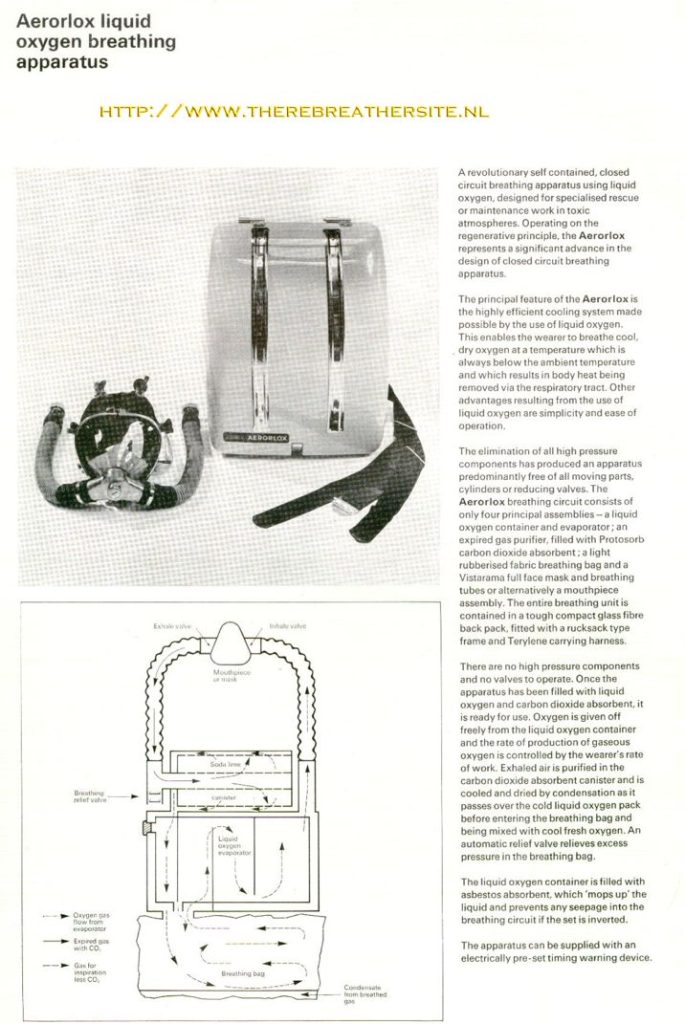
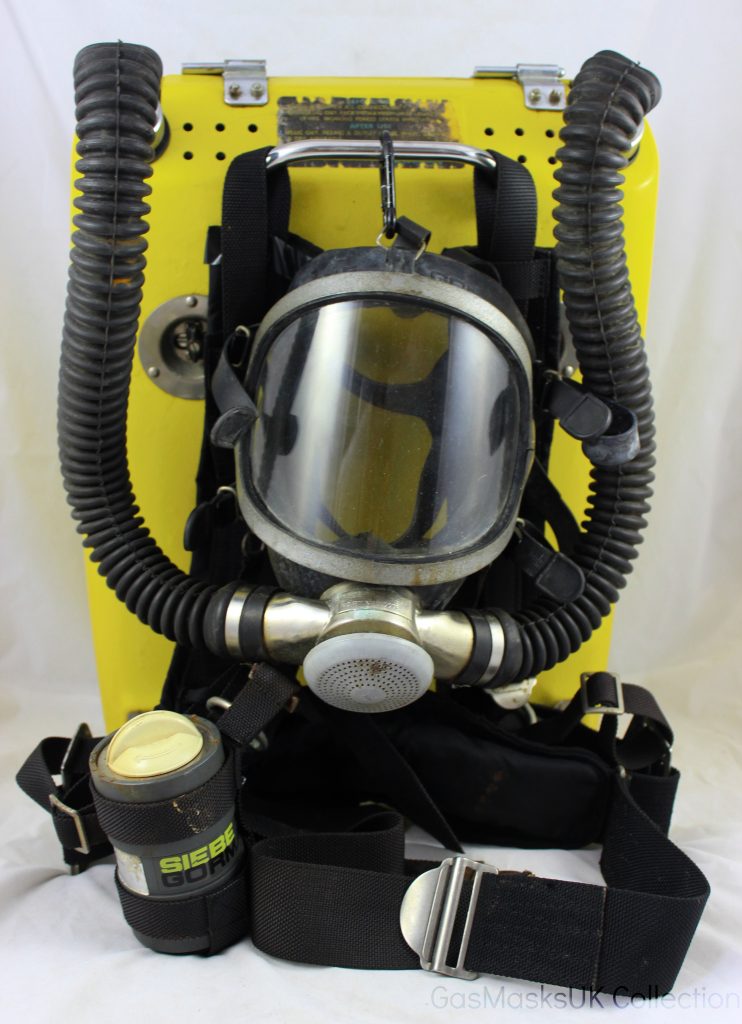
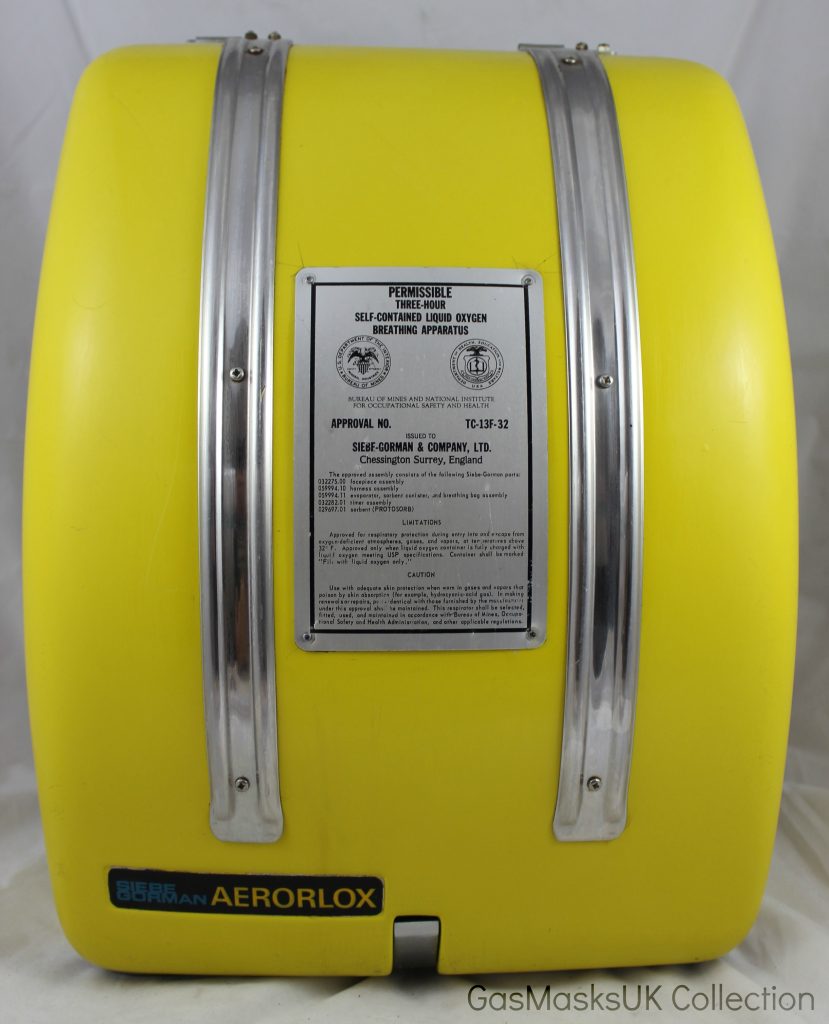
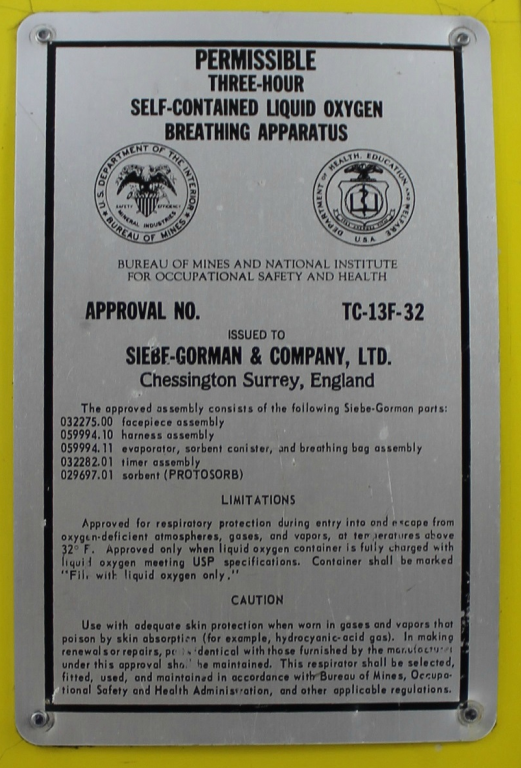
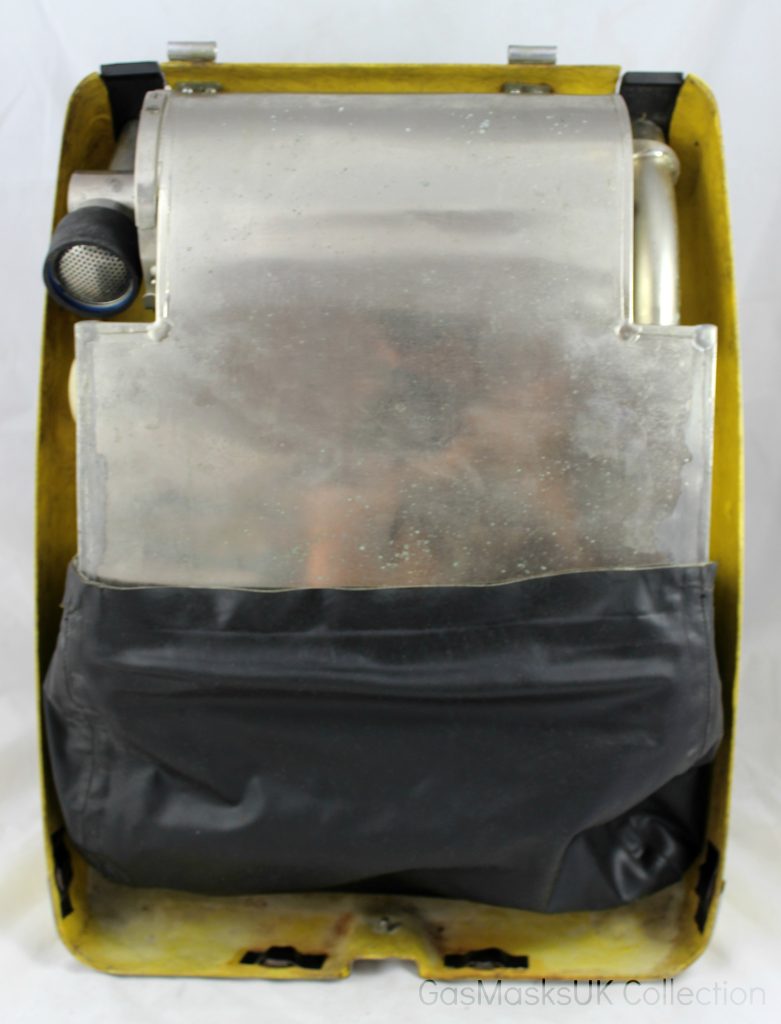
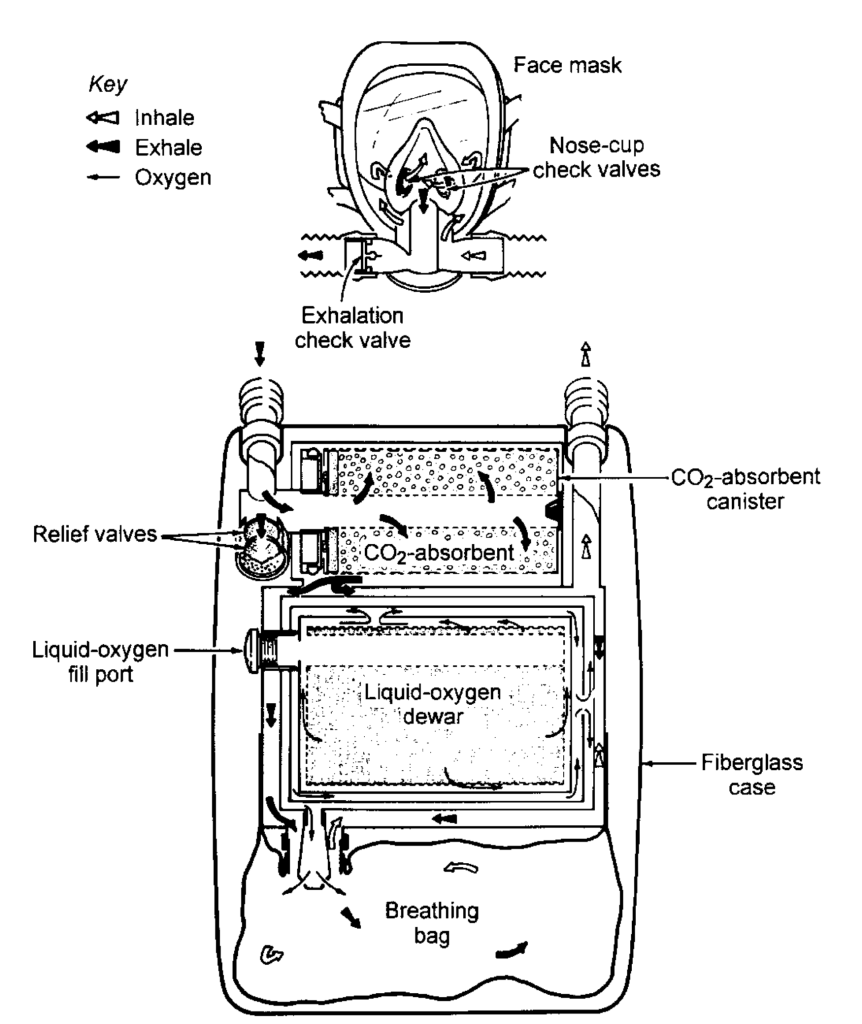
If you are in possession of the original Aerorlox manual, I would like to include it in my collection. All information about the above Aerorlox is welcome. Please realise that this unit is now 50 years old and can be quickly forgotten. Let’s make sure the information about this special rebreather is preserved!
This Aerorlox manual has been made available to me by the Grampian Speleological Group in Edinburgh, for which I am very grateful!
Russia Cryolang
Article from popular mechanics Russia,
Source -https://www.popmech.ru/diy/9239-zhidkaya-voda-zhidkiy-vozdukh-kriolang/
The article was published in the Popular Mechanics magazine ( №7, July 2009 ).
A LOOK INTO THE PAST. LIQUID WATER, LIQUID AIR: CRYOLANG
Very little is known about the history of Soviet breathing apparatus in liquid air – cryolangs. In fact, the only source of reliable information on this topic is an article in the “Sportsman-Submariner” magazine for 1977, which describes the AK-3, developed at the Kharkov Institute of Low Temperature Physics and Technology (KFTINT). But there are many rumors about cryolangs.
They are said to be complex, cumbersome, heavy and unreliable. They also say that since the gas in them was stored in a liquid form, the inhaled air was very cold and the breathing stages were often froze to the devices. They also claim that they were economically disadvantageous. And all this is not true.
The life of Anatoly Vityuk, who entered the Odessa Technological Institute of the Refrigeration Industry (OTIKHP) in 1969, was changed by a note in a foreign scientific journal. It mentioned a promising approach to the design of a breathing apparatus, in which air was stored not in thick-walled high-pressure cylinders, but in light and compact Dewar vessels. This made it possible to increase the battery life three times and significantly reduce the weight and dimensions of the devices.
“I was fond of scuba diving, I finished DOSAAF courses,” Anatoly recalls. – I had to constantly carry heavy cylinders, and then I thought – why not develop such an apparatus? As you know, laziness is the engine of progress. This predetermined the theme of my diploma and dissertation, as well as further work. “
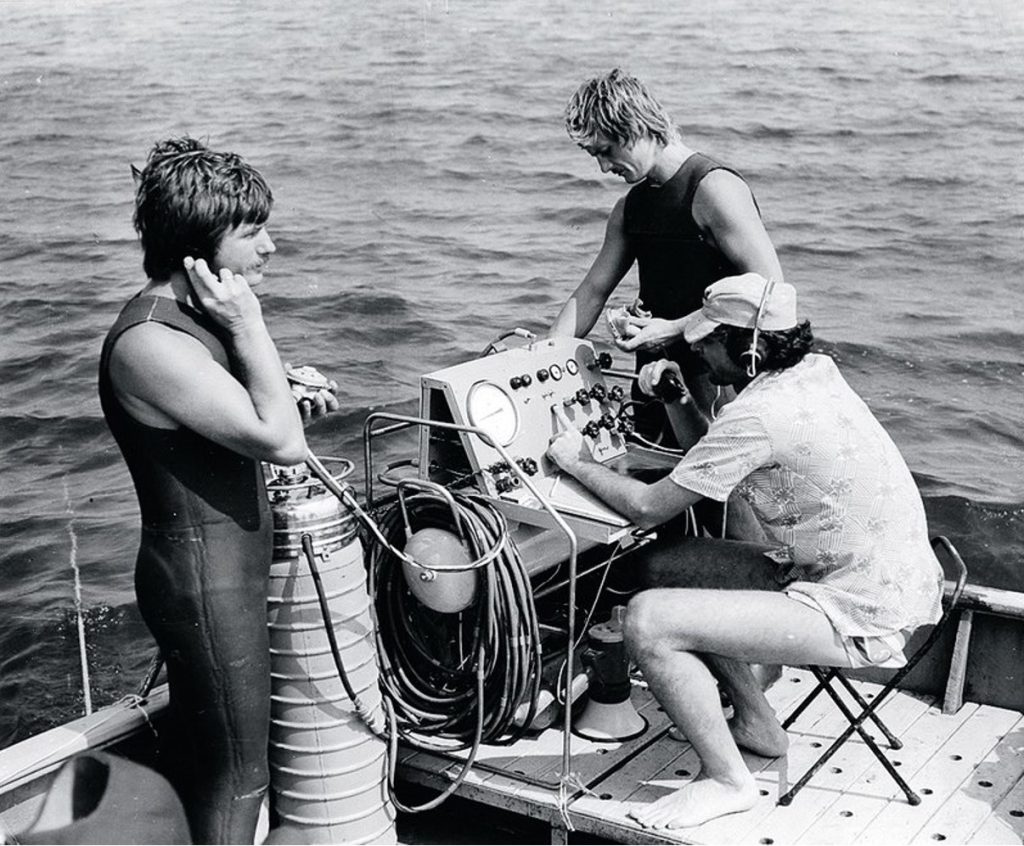
A BIT OF HISTORY
The first attempts to create cryogenic breathing apparatus date back to the beginning of the 20th century. Then in Germany (1905) and in Russia (1911), similar devices were proposed for mine rescue operations in mines (the low temperature of liquid oxygen also made it possible to reduce the temperature of the inhaled gas, which reduced the likelihood of overheating). Cryogenic diving apparatus began to be developed in the late 1960s. American and French engineers planned to use cryolanges when servicing offshore drilling platforms. In the USSR, the first devices were developed and manufactured at KIPTINT. By order of the military, they created cryogenic apparatus with a closed breathing cycle using liquid oxygen and nitrogen and gaseous helium, and the composition of the mixture was regulated depending on the depth without any electronics – based on the dependence of the boiling point of the gas on pressure. In Kharkov, civilian devices with an open breathing circuit, which are easier to use, were also designed – cryolanges AK-3 and AK-5, an experimental batch of the latter was transferred in the mid-1970s to the Kiev Emergency Rescue Service for testing.
In 1974, Anatoly Vityuk, who had already graduated from the institute by that time, proposed to organize a new laboratory of cryogenic life support systems on the basis of the Department of Cryogenic Engineering, headed by Professor Vyacheslav Andreevich Najer. The head of the department supported the initiative, and work began in the new laboratory.
“For six years, my colleagues Alexander Baletov, Alexander Sysoev and Nikolay Teshin have developed several models of gas and heat protection systems for work at high temperatures for firefighters and rescuers,” Anatoly recalls. “But our favorite topic was future diving systems.”

CLOSED AND OPEN LOOP
In the laboratory, an autonomous cryogenic breathing apparatus of a closed breathing cycle AKDA-1 was developed, which ensured human breathing in a gassed environment or when diving to shallow depths. It was simply impossible to come up with a simpler design. The apparatus had two regenerators, a porous nozzle impregnated with liquid oxygen, a breathing bag and a mouthpiece. When you exhale, the gas entered the moisture accumulator, and then into the regenerator, where it was cooled due to the evaporation of liquid oxygen. The carbon dioxide in the exhaled air froze, no chemical absorbers were required. Having passed through the second regenerator, the gas was heated and entered the breathing bag. When inhaling, it again passed through the regenerators, and then, cleaned of carbon dioxide and moistened in a moisture accumulator, entered the mouthpiece.
The apparatus weighing 3 kg provided breathing for 30 minutes. To work under water, a nitrogen cylinder was connected to the breathing bag through a reducer, which provided the necessary decrease in the oxygen concentration in the mixture.

How cryolang AKDA-2 works
The apparatus consists of a double-walled cylinder 1, made in the form of a Dewar vessel with screen-vacuum insulation 2 and a filling neck 3. Inside the cylinder, in the upper and lower parts, there are cryogenic phase separators 4 with nozzles made of porous nickel (pore diameter 6-10 microns) , which ensure the selection of liquid air at any position of the apparatus under water. For evaporation and heating of liquid air in the apparatus, heat exchangers 5, 6, 7 and 8 are provided. To regulate the operating pressure and supply of breathing air, an automatic valve 9, a reserve valve 10, a safety valve 11 and a lung valve 12 are installed. screw cap; due to small heat gains from the environment, the pressure inside the cylinder rises. When the lung valve 12 is turned on, liquid air flows from phase separators 4 in series to heat exchangers 8, 5 and 6, where it is evaporated and heated. Heat in heat exchanger 5 is transferred to liquid air, which causes an increase in pressure in the cylinder. The air heated in the heat exchanger 6 through the automatic valve 9 enters the lung governed demand valve. When the working pressure in the cylinder 1 is reached, the valve 9 shuts off the air supply through the heat exchangers 5 and 6, and further air supply to the lung demand valve occurs only through the heat exchanger 8. The apparatus is ready for operation. After the liquid air has been consumed, a reserve air remains in the apparatus (about 0.5 kg), since the phase separators are not installed at the very bottoms. The porous tips are no longer wetted by the liquid, and breathing resistance occurs: the gas phase, due to the small pore size, does not pass well through the nozzles. In this case, the diver sets the valve 10 to the “Reserve” position, and air begins to flow from the cylinder directly through the heat exchanger 7. The liquid air level is controlled by a magnetic float and a set of reed switches.
But when designing the AKDA-2 open-cycle breathing apparatus, the designers faced a problem. The fact is that liquid air is a mixture of liquid nitrogen (79%) and oxygen (21%), the boiling points of which are different. Nitrogen boils at a lower temperature, so the oxygen content in the gas phase is only about 7% and cannot be used for breathing. It is necessary to take liquid air from the vessel, evaporate it (gasify) using heat exchangers and supply it for breathing to the lung demand valve, and in any position of the Dewar vessel.
“For this purpose in Kharkov devices, intake pipes swinging on bellows and a movable gravitational valve were used for this. technicians who use the capillary effect to supply fuel from tanks to engines in zero gravity, installing special “sponges.” Experiments with water and felt showed the concept to work, and for work with liquid air, as a result, porous nickel with pore sizes of 6 was chosen −10 microns. ”
Packings made of porous nickel worked as phase separators – they took out liquid air due to wettability, and did not let the gas phase through. Two such nozzles in the upper and lower parts of the cylinder provided air supply at any position of the diver. Such a system made it possible to significantly simplify the apparatus, leaving only two valves and removing the reducer (in the AK-5, a reducer and eight valves were used), which had a positive effect on its reliability.
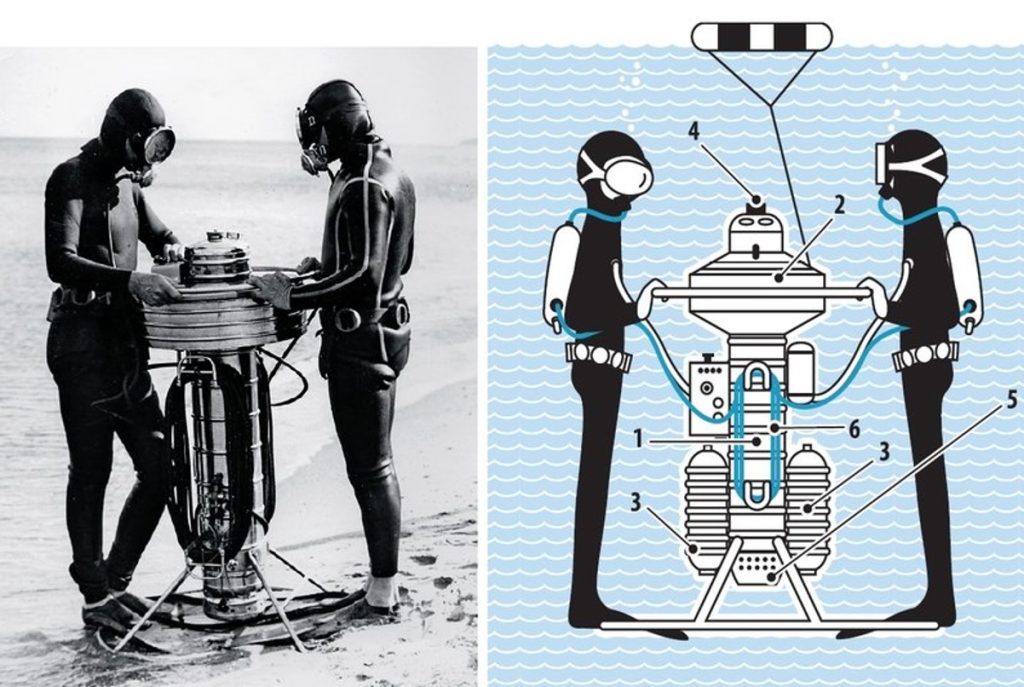
Light diving station
With the help of the MAKS-1 station, the ascent and descent of divers, working tools, air supply and blowing of small pontoons and ballast tanks were carried out. The absence of hoses connecting the divers with the floating craft, and the overall breathing apparatus behind the diver’s back made it possible to carry out underwater work in hard-to-reach places. Station design: 1 – storage unit, 1 – buoyancy compensator, 3 – insulated containers, 4 – upper dome with instruments and control handles, 5 – lower dome with heat exchange equipment, 6 – hoses for supplying breathing mixture and hot water.
Pros and Cons
The first to appreciate the new devices were divers Mikhail Borgul and Vladimir Bernatovich. According to testers, cryolangs not only were not inferior to conventional scuba diving in terms of simplicity and ease of use, but also surpassed them in many respects. The apparatus was filled with liquid air by a simple overflow from Dewar vessels, while it was possible to quickly and easily provide any concentration of oxygen. Anatoly Vityuk recalls: “We simply put the Dewar vessel on the scales and mixed the required amounts of liquid gases by weight. It took a few minutes, but for the uninitiated it looked like alchemical experiments – with boiling air and puffs of steam. ”
Another important advantage of cryolangs was that the liquid air was guaranteed to be free of carbon dioxide and carbon monoxide. When refueling ordinary scuba tanks, special filters are used to clean the air from these gases, since under pressure they can be fatal to humans: there is a known case when Jacques-Yves Cousteau and his partner Frederic Dumas almost died during a dive in August 1946, due to for the fact that carbon monoxide got into the cylinders from the exhaust of the compressor engine.
The device was very compact and light: for example, a two-cylinder scuba gear has a volume of 14 liters and weighs more than 25 kg, and a cryolang with the same air supply – 3 liters and 4 kg. Of course, when scuba diving, weight in the air does not play a special role, because you still have to carry a lot of weights to compensate for the buoyancy of the wetsuit. From this point of view, the low weight of the cryolang is rather a minus (you need to take more cargo), but its compactness is very useful when diving in tight spaces (for example, on sunken objects).
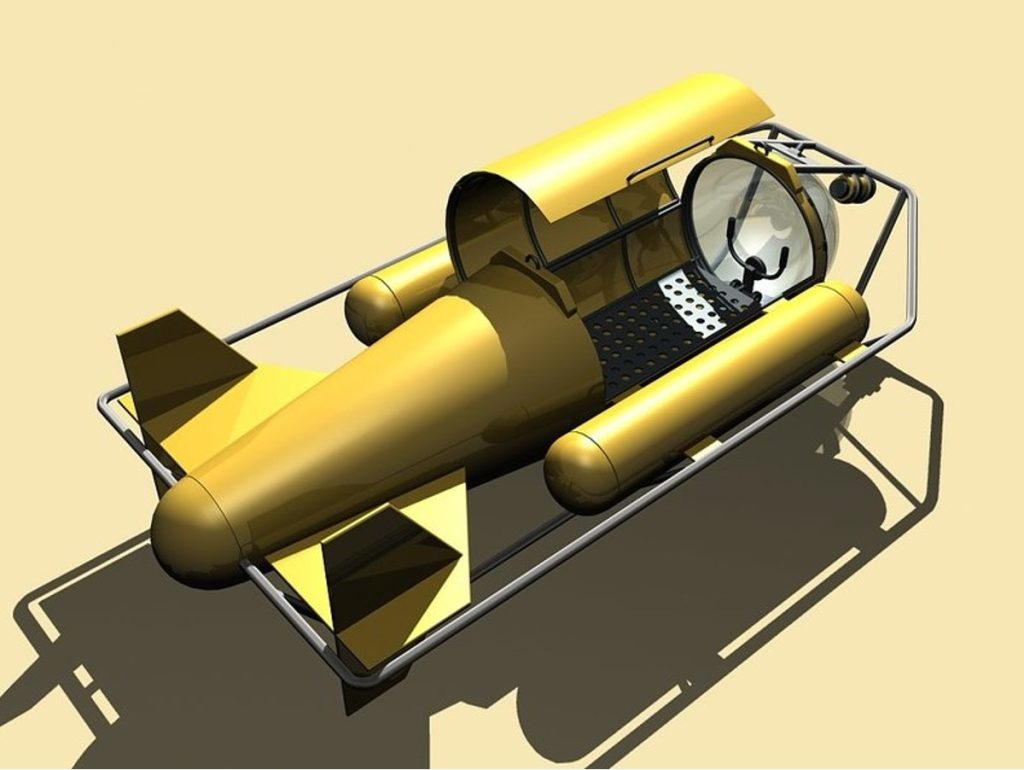
Contrary to the widespread misconception, the temperature of the air supplied from the cryolang for breathing was not lower, but higher than that of the scuba. “The fact is that in scuba diving there is an adiabatic expansion of the gas, which leads to its cooling,” explains Anatoly. – The air simply does not have time to heat up to ambient temperature, which is not only unpleasant, but can even lead to icing of the structure. Heat exchangers are provided only in some models of “frost-resistant” gearboxes and lung demand valves, but still the temperature of the supplied air is 5-7 ° lower than the ambient temperature. Our cryolang did not have a reducer, and developed heat exchangers were an obligatory part of the design, so the temperature of the supplied air differed from the water temperature by only 2-3 °.
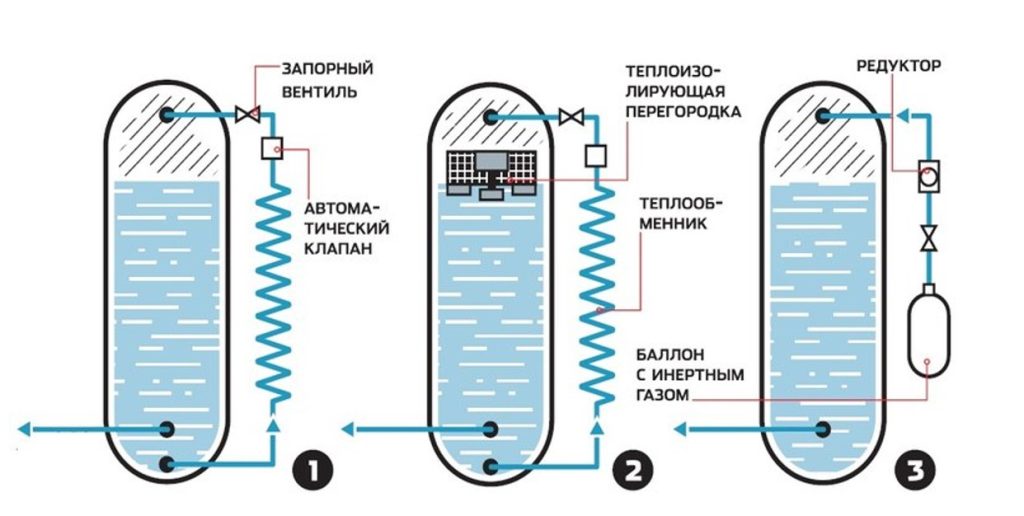
Working pressure stabilization systems
One of the key technologies in cryogenic breathing systems has been the working pressure stabilization system. For vertically oriented side units, closed-type evaporative systems (1), especially with a heat-insulating floating partition (2), have proven themselves well. She quickly established and regulated the working pressure due to the nonequilibrium temperature state of the vapor and liquid phases. In this case, the liquid air is not heated and is not discharged into the environment. Such systems were used in the MAKS-1 light diving station and the YUG-7m towed underwater vehicle. In the gas cylinder stabilization system (3), the working pressure was regulated by supplying an inert gas to the vapor phase from the cylinder through a reducer. Such a system made it possible to very quickly regulate the working pressure with high accuracy,
However, the cryolang had one drawback. Due to the weak thermal insulation of the cylinder, in about a day, all the air evaporated, and it should have been refilled immediately before the dive. But given the fact that it only took a couple of minutes to refuel, this was not a big problem.
The years of succes
In 1980, a group of cryolang developers moved to the South Center of the Academy of Sciences of the Ukrainian SSR, where an underwater research laboratory was organized. There, a group of four engineers and five divers created a cryogenic diving complex, which later became extremely successful. “For ten years, all scientific expeditions of the Southern Center for underwater biological, chemical and geological research, mapping the seabed and searching for sunken objects were provided only by our systems,” Anatoly recalls.
The main element of the complex was a cryogenic unit (BC) – a cylindrical vessel with a large supply (22-24 kg) of liquid breathing mixture. The BC had a screen-vacuum insulation, in the lower part there was a heat exchange apparatus for gasification and heating of the working mixture, in the upper part there were control valves, a filling neck and a system for stabilizing the working pressure. Filling the BC from standard Dewars took about 5 minutes, start-up (increasing the pressure to working pressure) – about 3 minutes. The BC had a quick-release connection for connecting lung demand valves and was versatile – it could be used as a system for supplying breathing mixture from the board, from the shore, storing liquid mixtures or refueling light autonomous AKDA-2 apparatuses. The BK could also be installed as a source of breathing mixture on a small towed wet underwater vehicle “YUG-7m”, which was developed in the laboratory for seabed research, search and inspection of sunken objects. The last element of the complex was the MAKS-1 light diving station, equipped with a telephone connection.
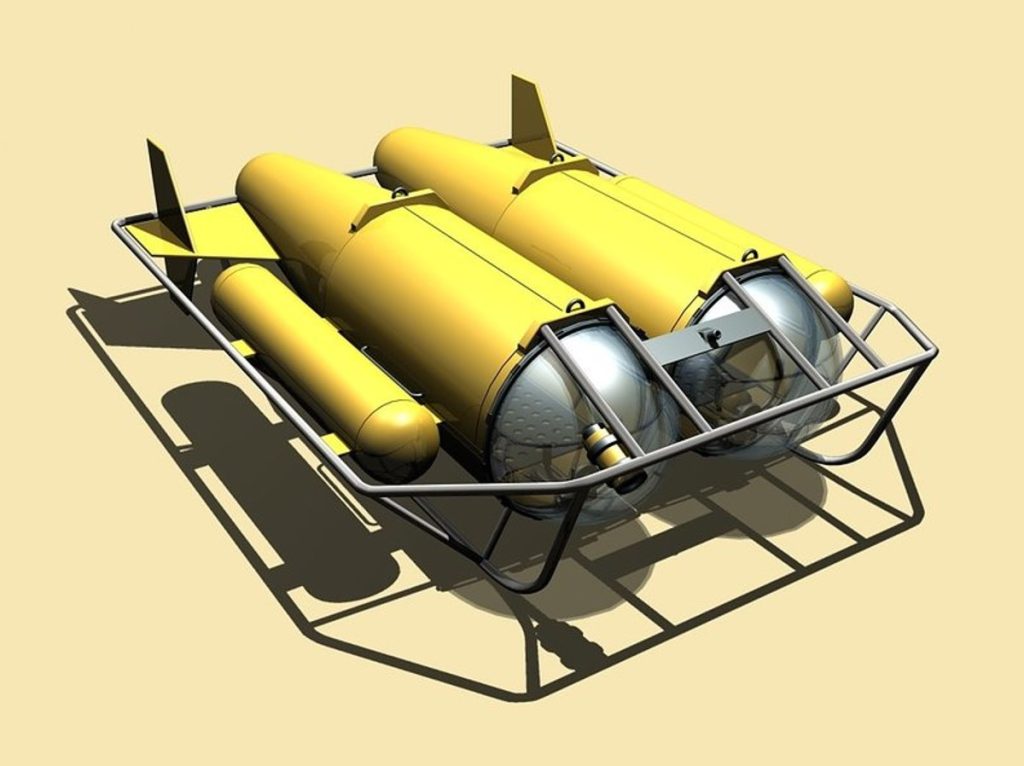
THE SAD FATE OF CRYOLANG
For ten years, the design has been worked out almost to perfection. With the development of the appropriate infrastructure, this device could well become a serious competitor to scuba gear. “Cryolanga has, of course, its own specifics,” says Anatoly Vityuk. – But in general, its use is no more difficult than ordinary scuba gear. I’m sure he had every chance of success. ” But the fate of the promising technical solution was different. In 1990, perestroika began, the underwater research laboratory, which had existed for all these years on self-financing, simply had no customers left, and it was disbanded.
Maybe the designers will “reinvent” cryolang in the future, as happened with rebreathers?
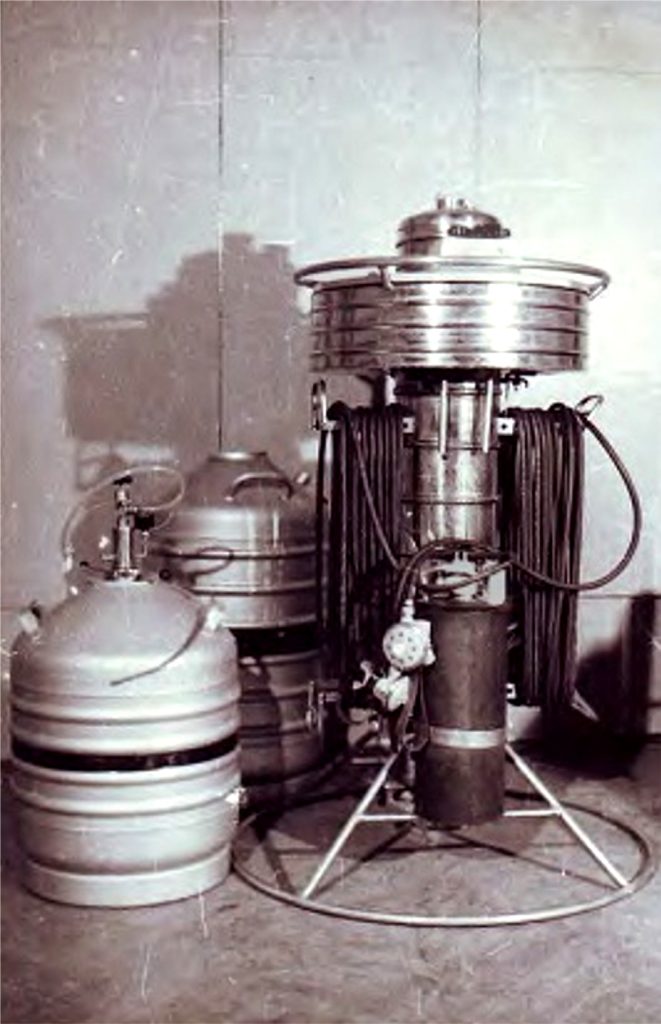
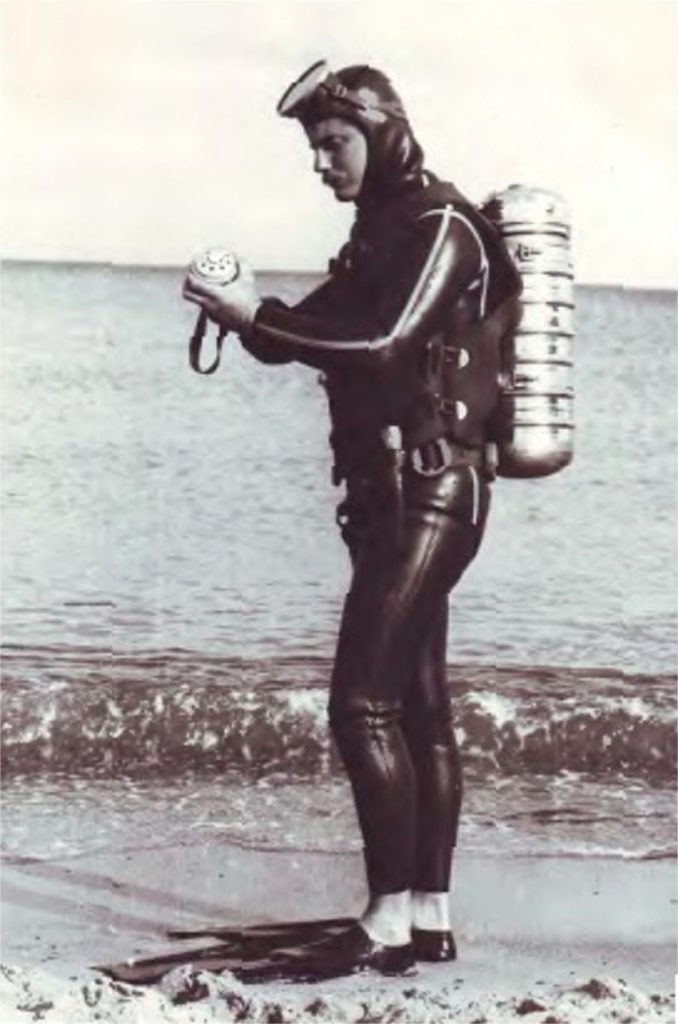
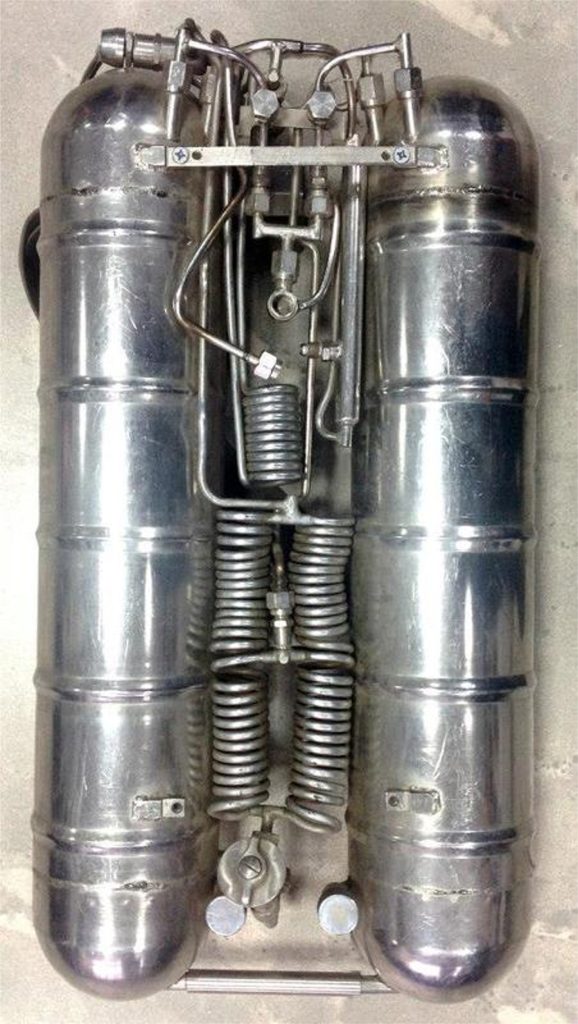
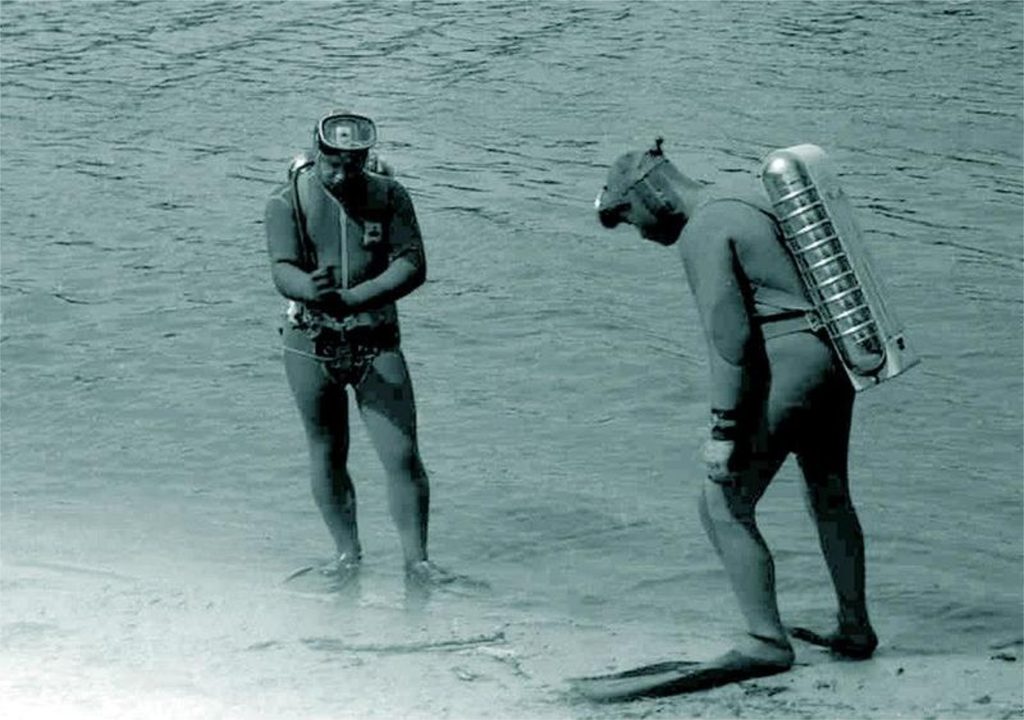
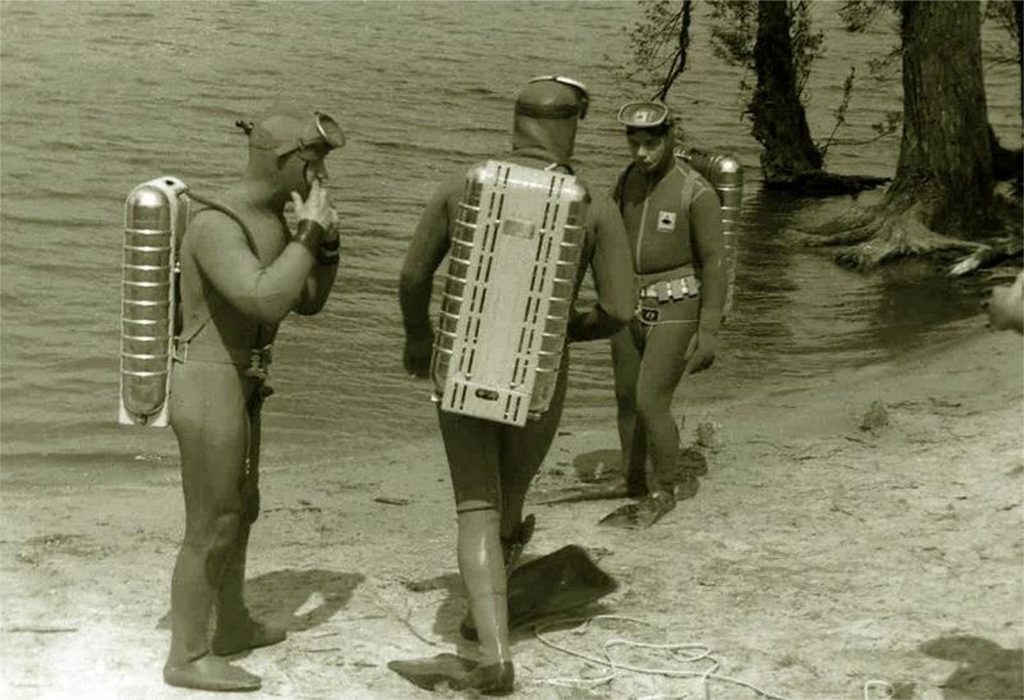
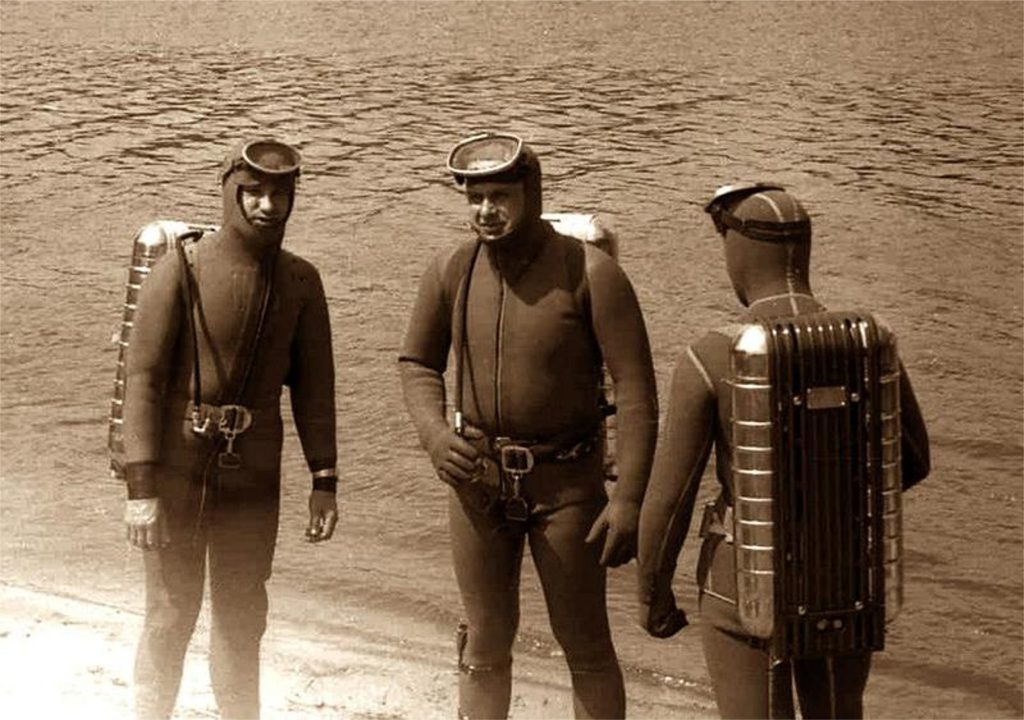
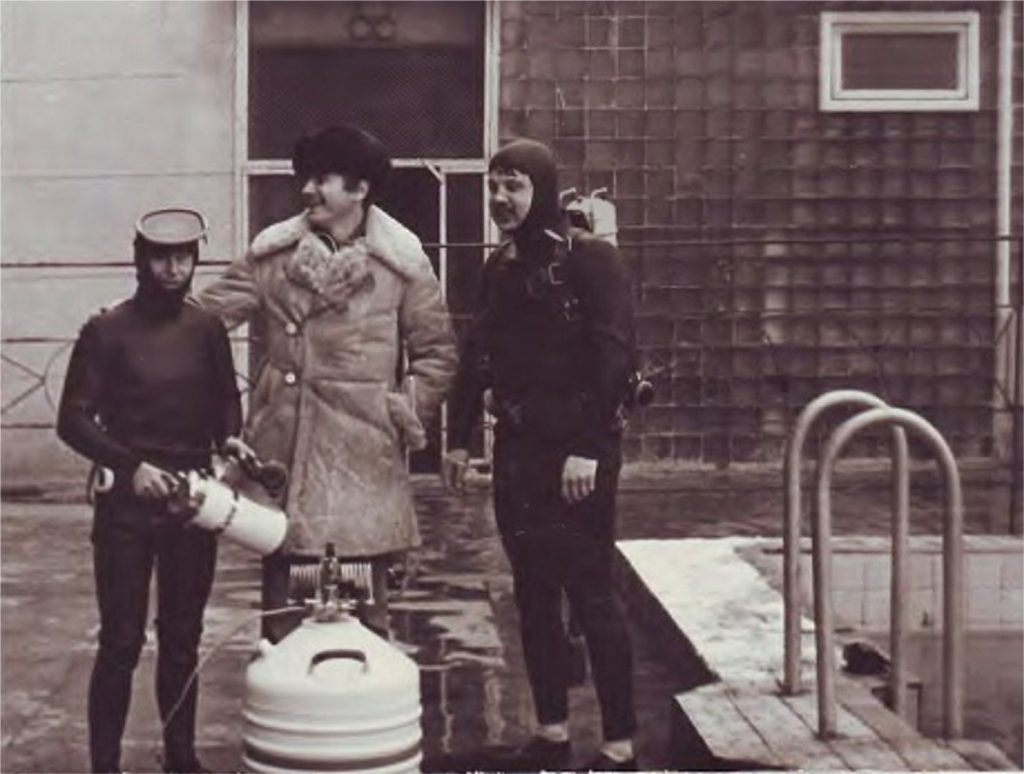
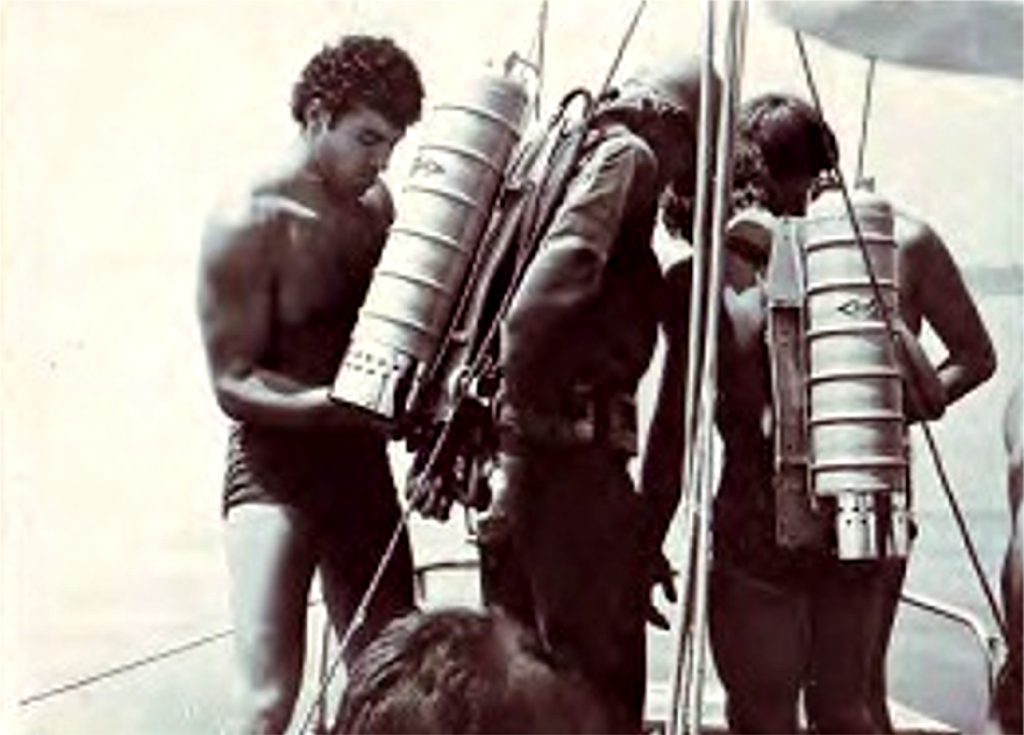
Dave Sutton sent me pictures of the later developed АЛИТО = ALITO, КРИОЛАНТ = Cryolant. A device for liquid air where there was no rebreather function but use was made of the large capacity in gas volume which made it possible to make long dives.
AK-3 is designed for various underwater technical, research, rescue and other works at a depth of 45 m. Has open breathing cycle, what is used for liquefied air or air-oxygen mixture maintained at a temperature of – 190 ° C Dewar vessels. Supply of respiratory fluid mix allows you to be under water about four times longer than using compressed of air. New single stage design respiratory machine allowed at a depth of 45 m (with breathing mix consumption 155 l / min) reduce inspiratory expiratory resistance up to 50 mm of water.
The presence of two components of liquefied gases allows when charging devices depending on the set immersion depth and exposure time make up the necessary gas mix so that step decompression mode turned out to be minimal. The mixture is made up by weighing oxygen and nitrogen separately and further mixing them.
Technical specifications of Cryolung AK-3
Depth of immersion – 45 m.
Mass apparatus on the air: filled respiratory mixture – 24 kg; without respiratory mixes – 16 kg.
Dimensions – 680X350X140 mm.
Number of vessels – 2.
The mass of the breathing mix is 8 kg.
Volume respiratory mix – 6900 l. Volume reserve breathing mix – 500 l.
Safety factor on the outside double pressure – 9 kg / cm2
Stock strength to internal pressure three times – 25 kg / cm2
Installation pressure – 5.8 kg / cm2
Tripping safety valve – 10-15 kg / cm2
Positive buoyancy +1 kg.
Negative buoyancy – 2 kg.
Refueling time apparatus – 3 – 5 minutes.
Preparation time apparatus to work immediately after refueling – 8 – 10 min.
Preparation time apparatus to work pre refilled – 1-2 minutes
On the air can breathe from the apparatus no more – 10 min.
Thermal insulation vacuum vacuum screen – 10 -3 mm Hg.
Resistance on the inhale-exhale – 50 mm waters
Non-waste storage time – 12 hours
Cryolang ALITO AK-3 is made of stainless metal and is anti-magnetic.
Brass available and aluminum parts are covered with anti-corrosion coating resistant to the effects of sea water.
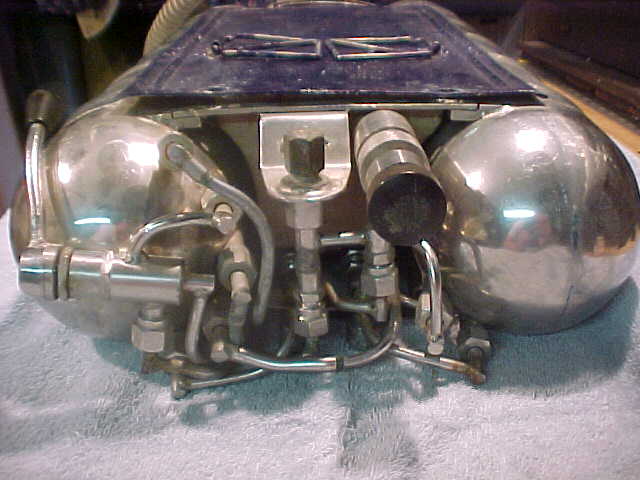
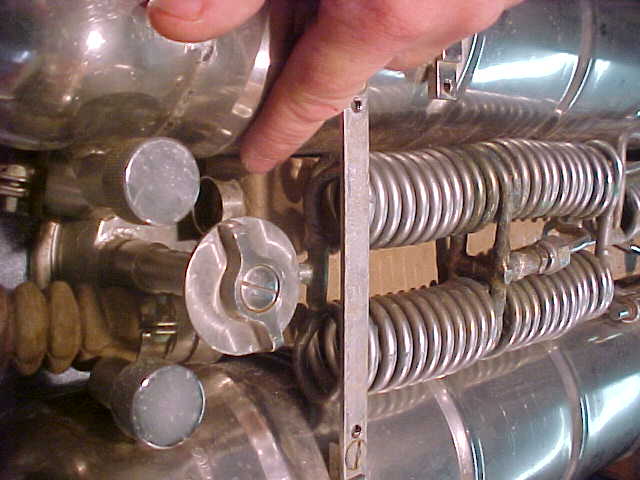
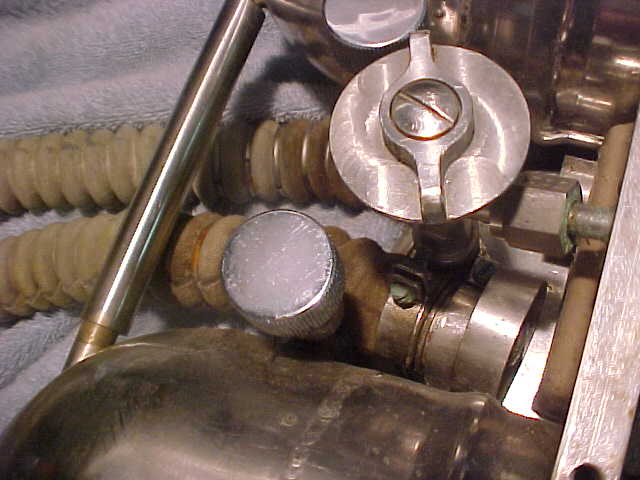
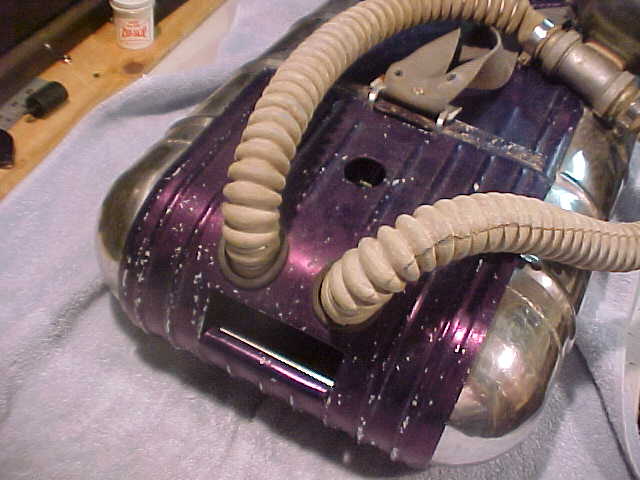
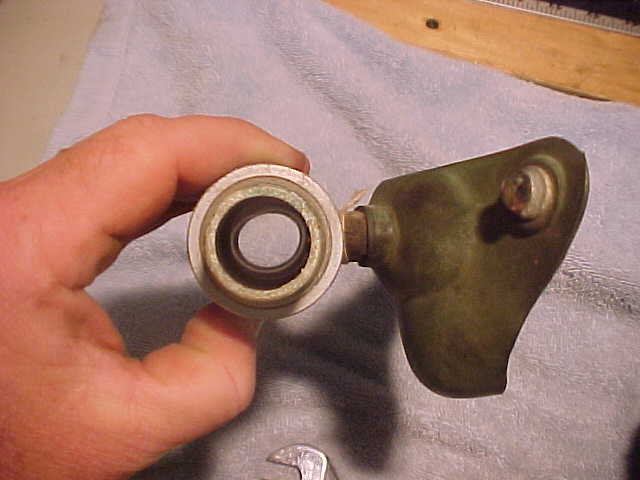
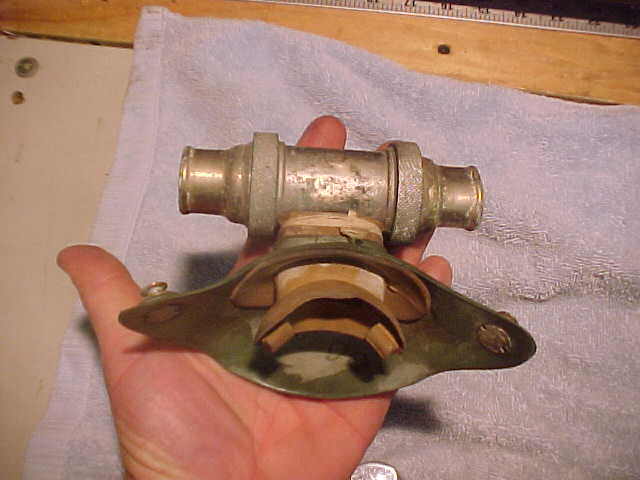
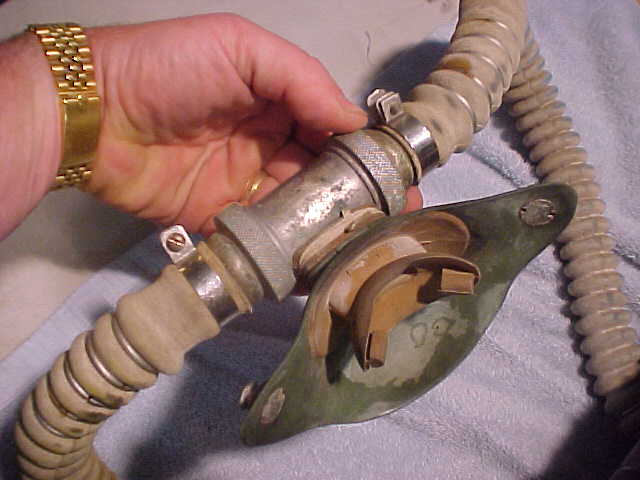
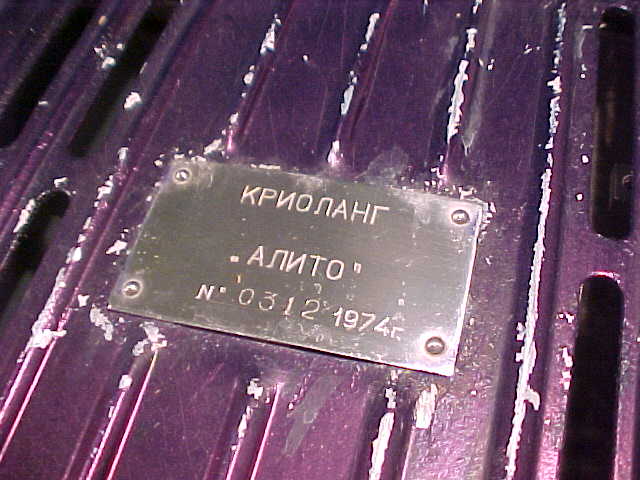
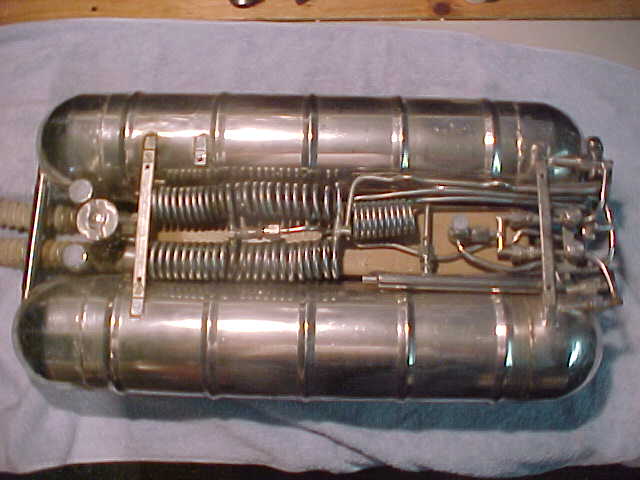
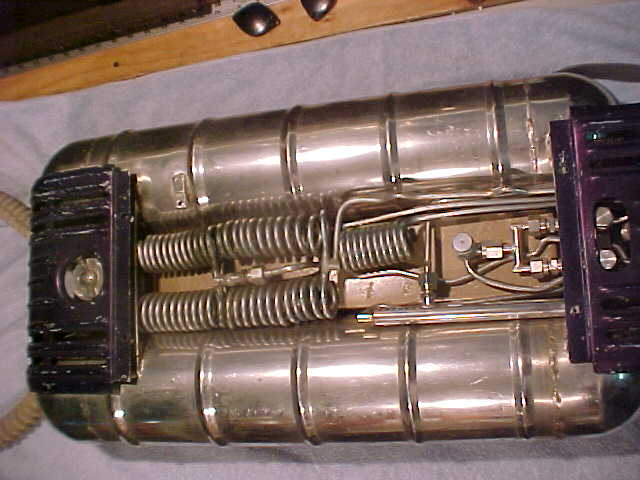
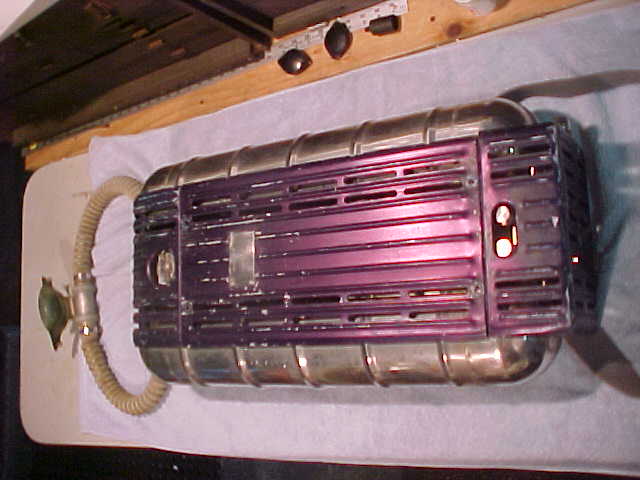
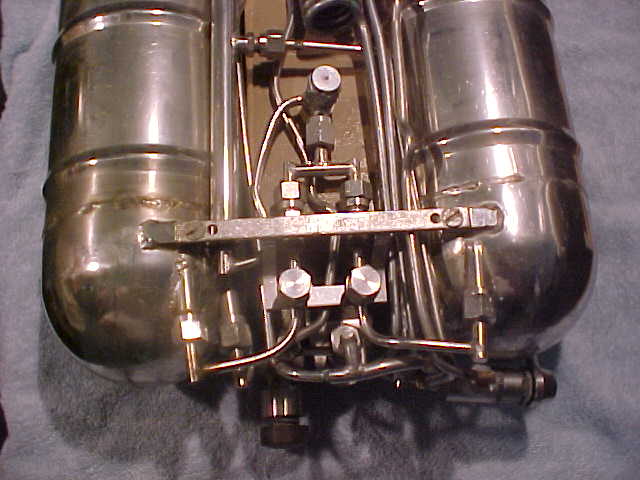
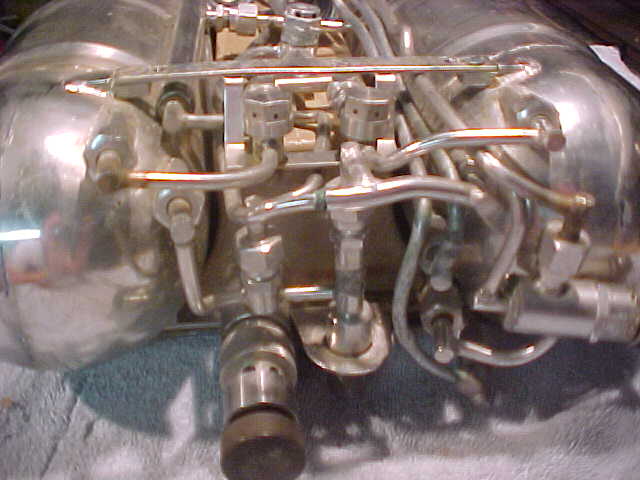
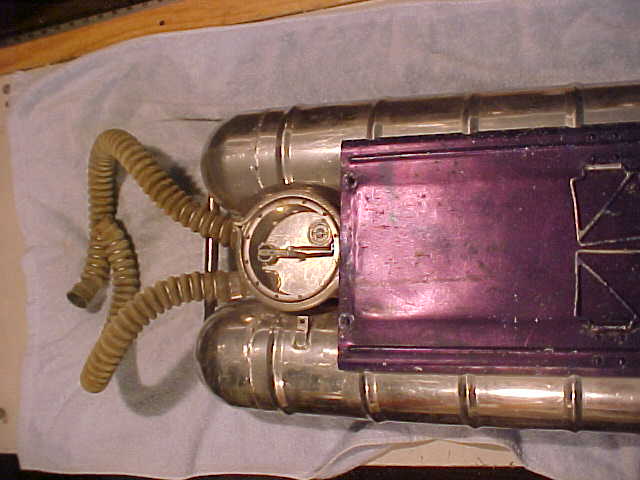
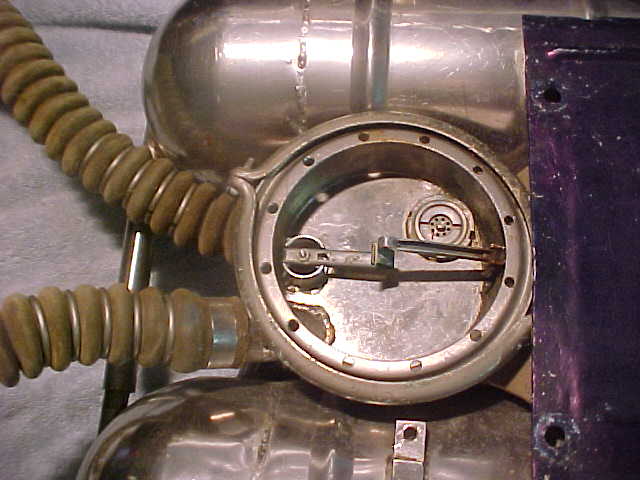
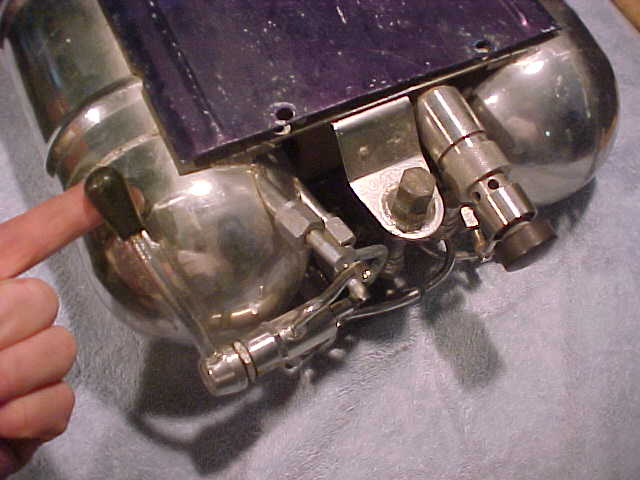
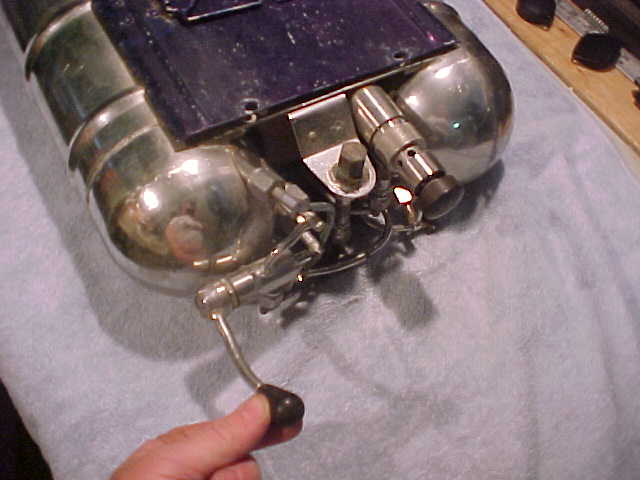
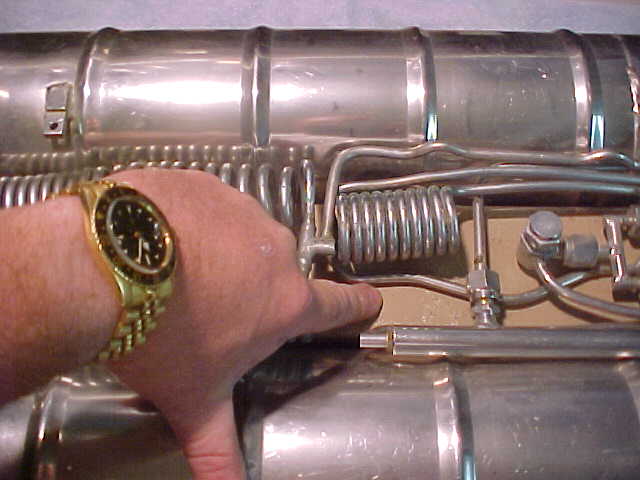
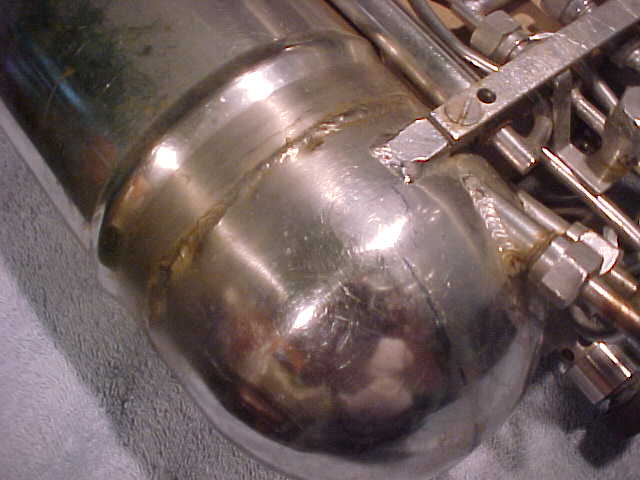
USA Jim Woodberry 1965
In 1965, Jim Woodberry designed a diving system that operated on liquid air. His invention was not a rebreather either, but it did form the basis for cryogenic diving systems in the USA. The system worked with two Dewar bottles with an initial pressure of 5.8 bar. The system contained 6.2 litres of liquid oxygen-nitrogen mixture with which Woodberry made dives to a depth of 40 metres. The system was then put into production by Jordan Klein and Cryogenic Systems Inc. Information about the further development of the system I have not been able to find to date. Additions are most welcome.
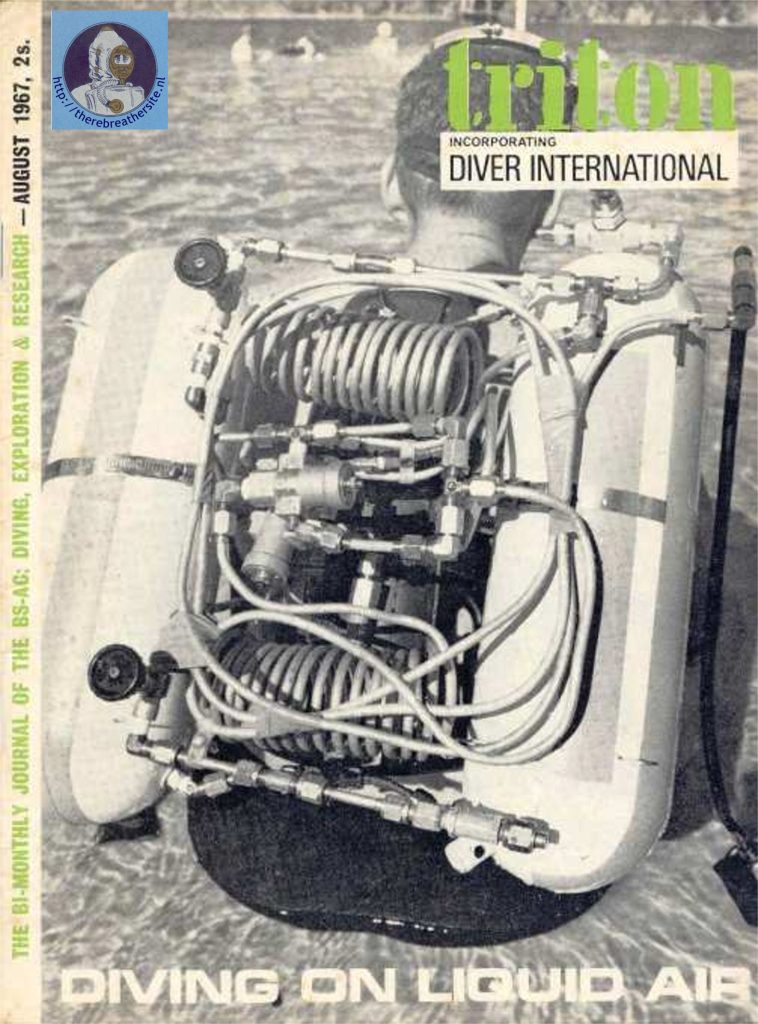
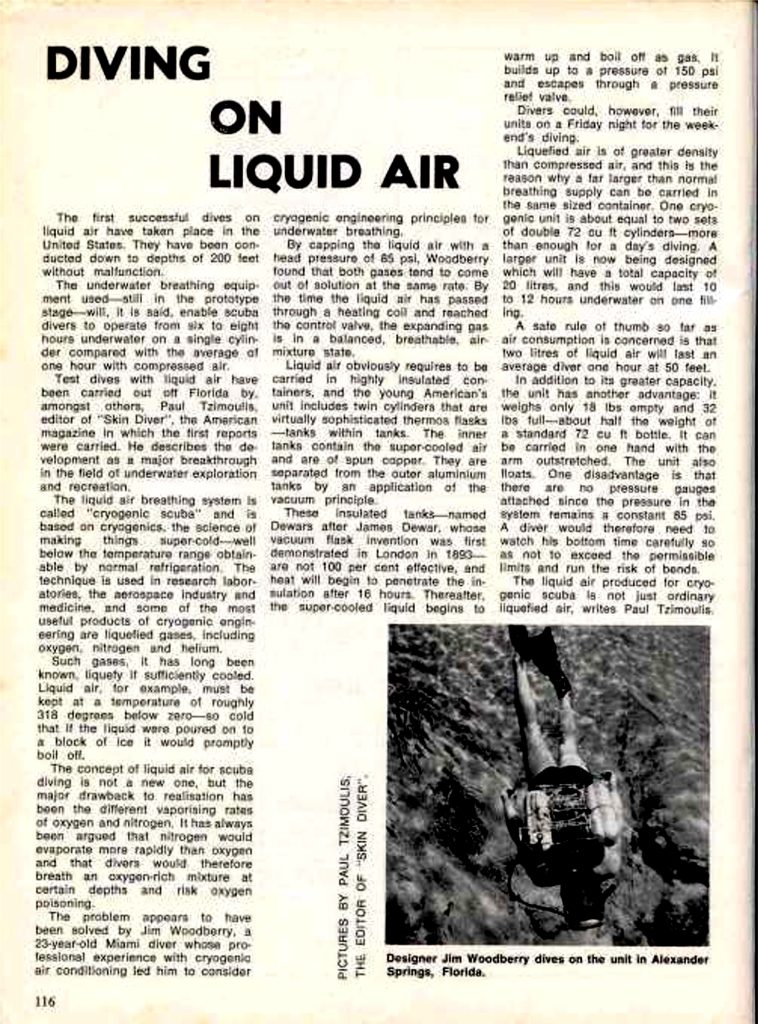
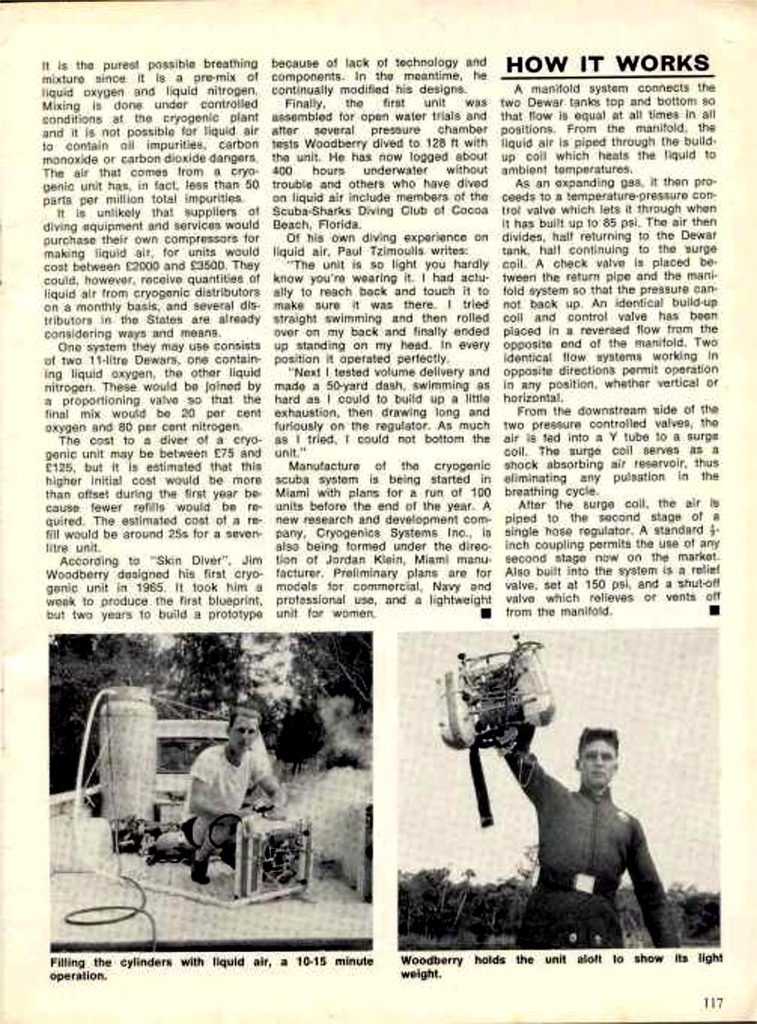
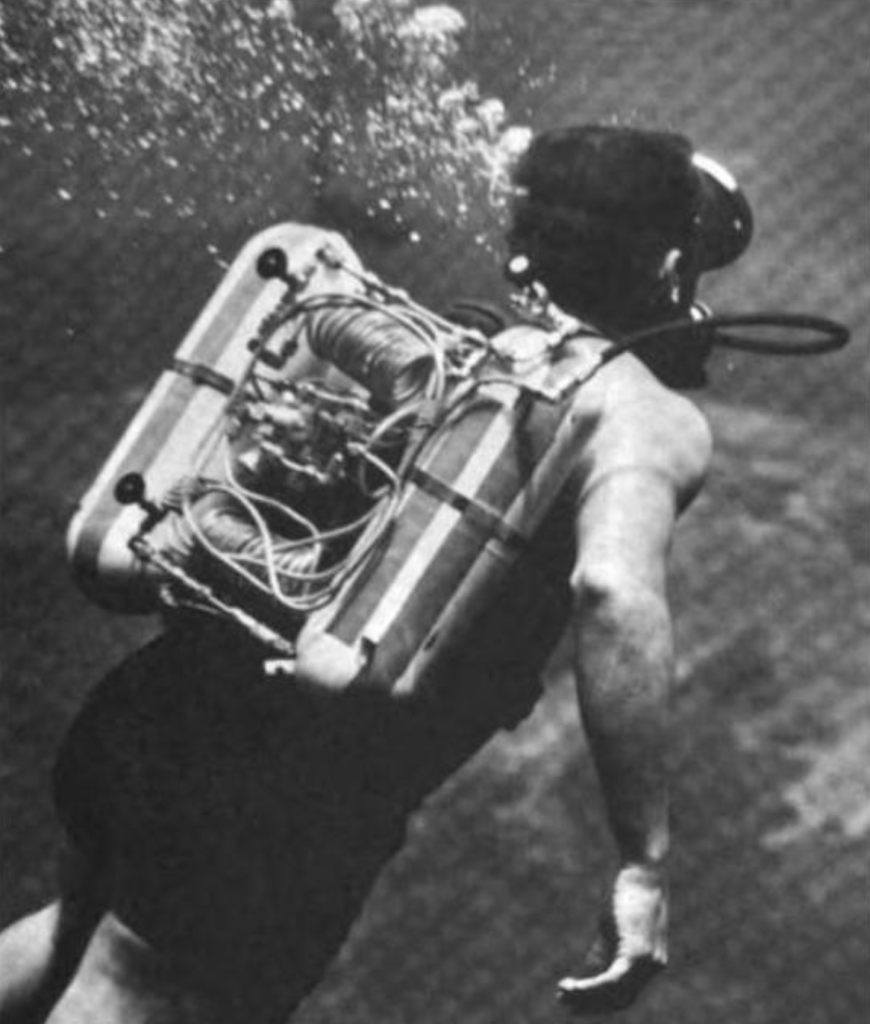
In 1965 Halbert Fischel together with Tony DiChiro and Larry Cushman and Dave Joss designed and tested a cryogenic diving system capable of taking the diver to 307 meters of depth with diving times up to 5 hours. The units used a technology with a cryogenic scrubber system. The energy for reaching these low temperatures was achieved by taking liquid nitrogen during the dive carried in 1 cylinder.
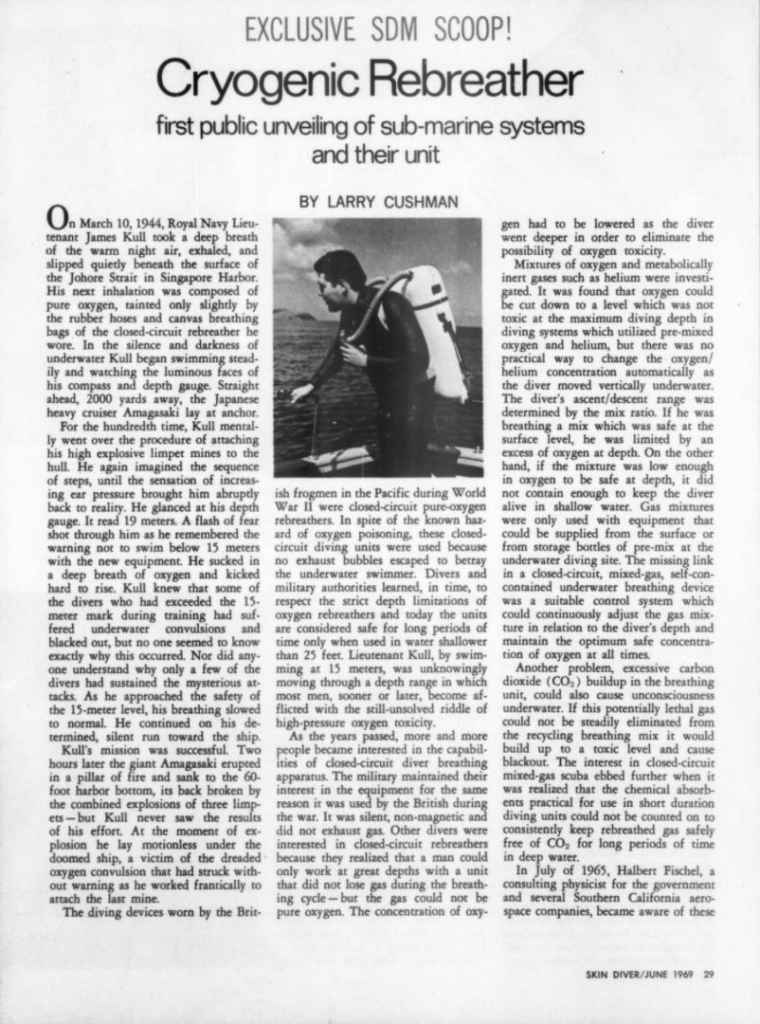
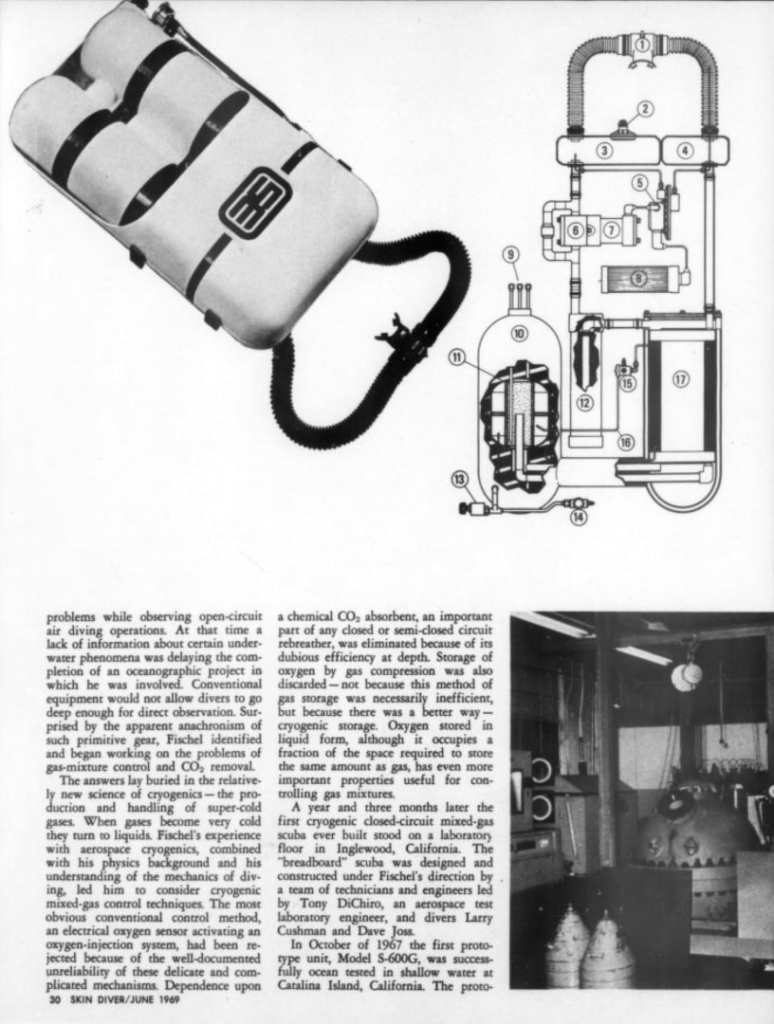
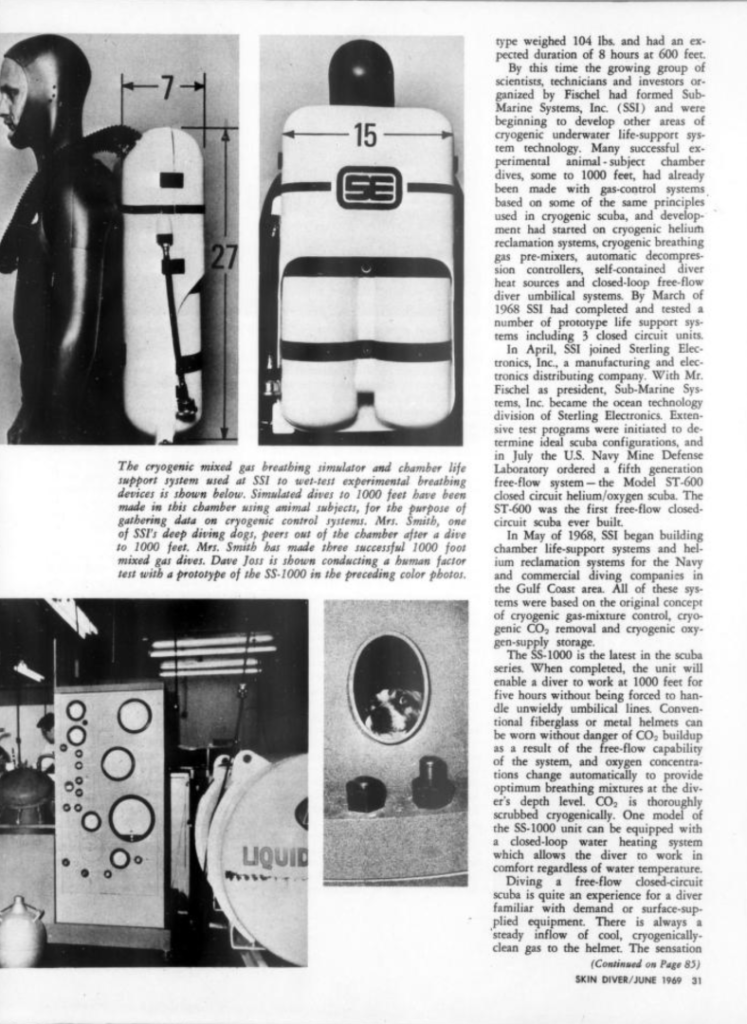
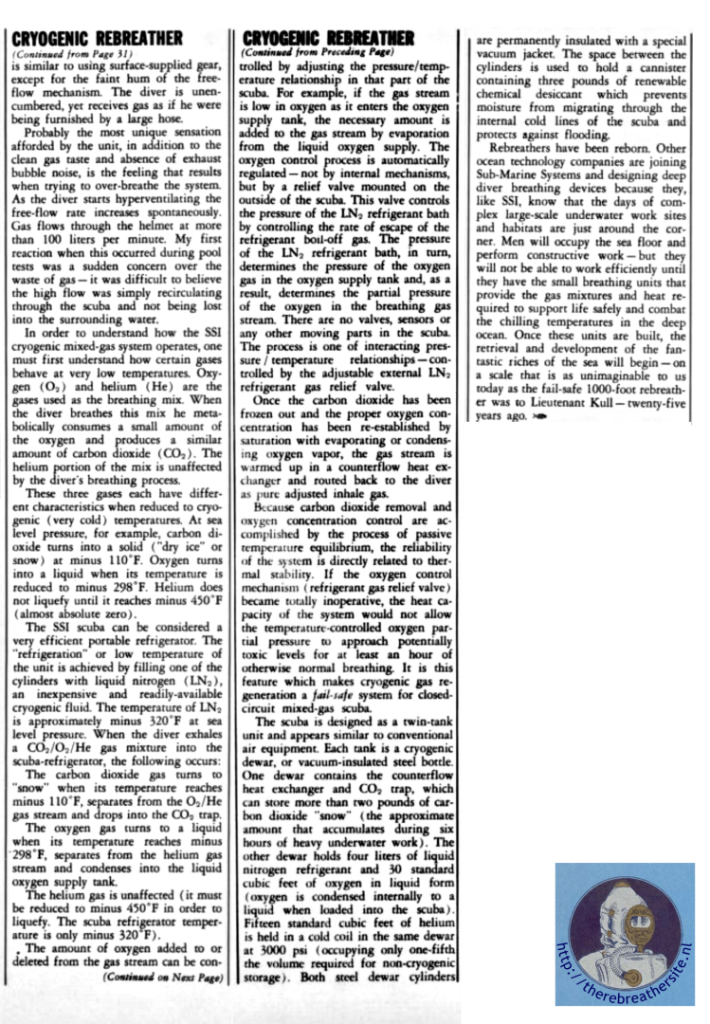
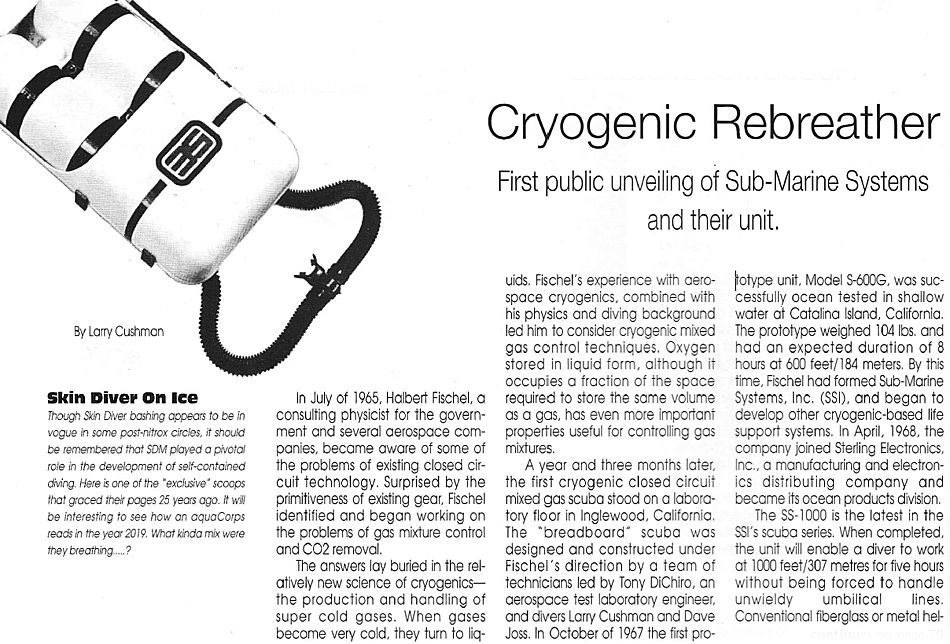
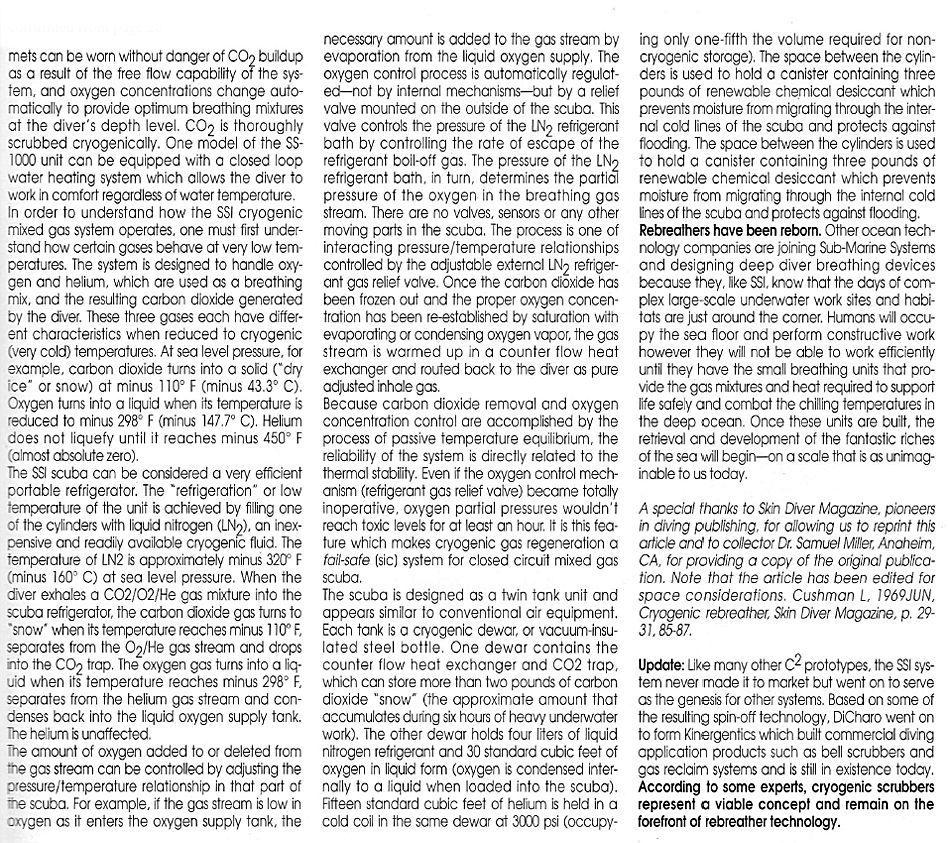
Halbert Fischel of Sub-Marine Systems Corporation (A Sterling Electronics Company) wrote an in-depth article in 1970 on the evaporation energy and the calculations describing the partial oxygen and co2 production. You can read this extensive technical article here!
Modern developments
NASA and the Office of Mine Safety and Health Research (OMSHR) have been trying to resolve current technological issues with cryogenic life support so that it can be successfully commercialized, and develop new applications for cryogenic technologies in life support targeting current issues in the mining life-support industry.
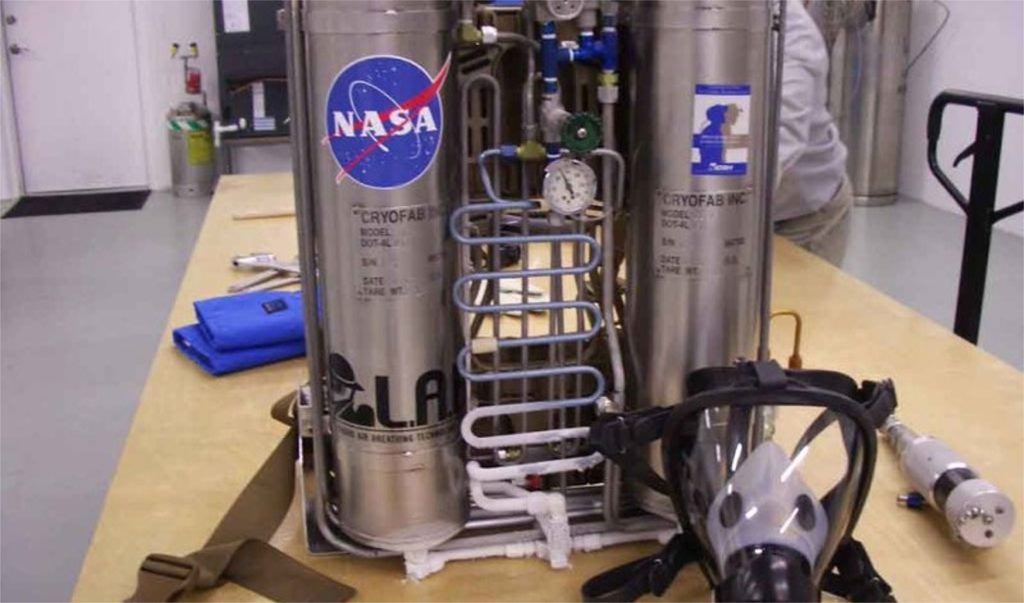
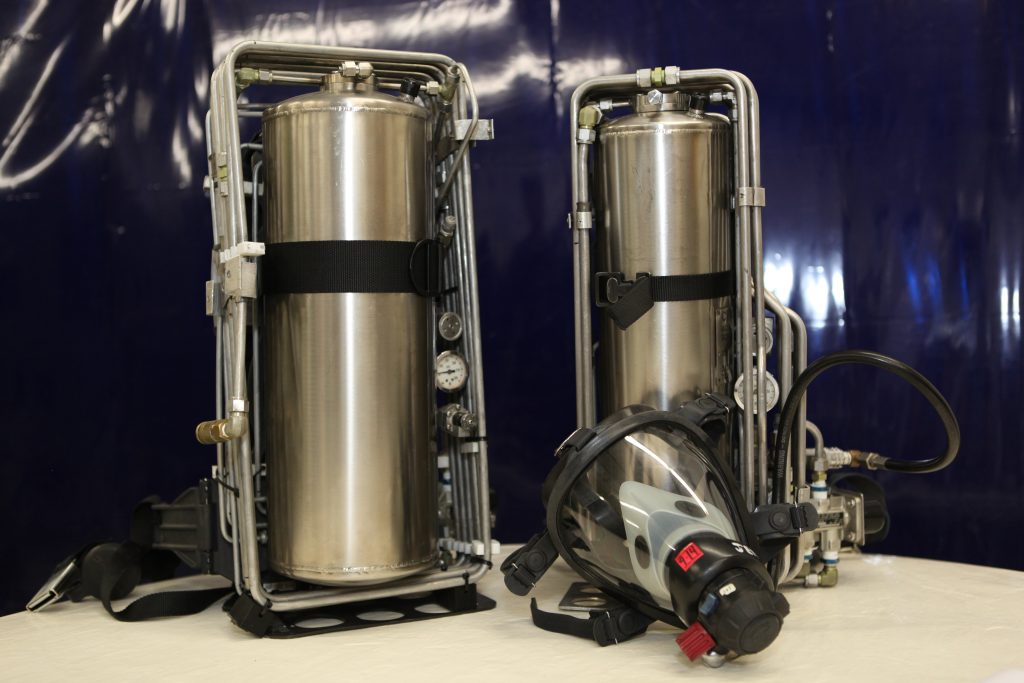
The prototype systems are under development at BCScryo LTD in the UK
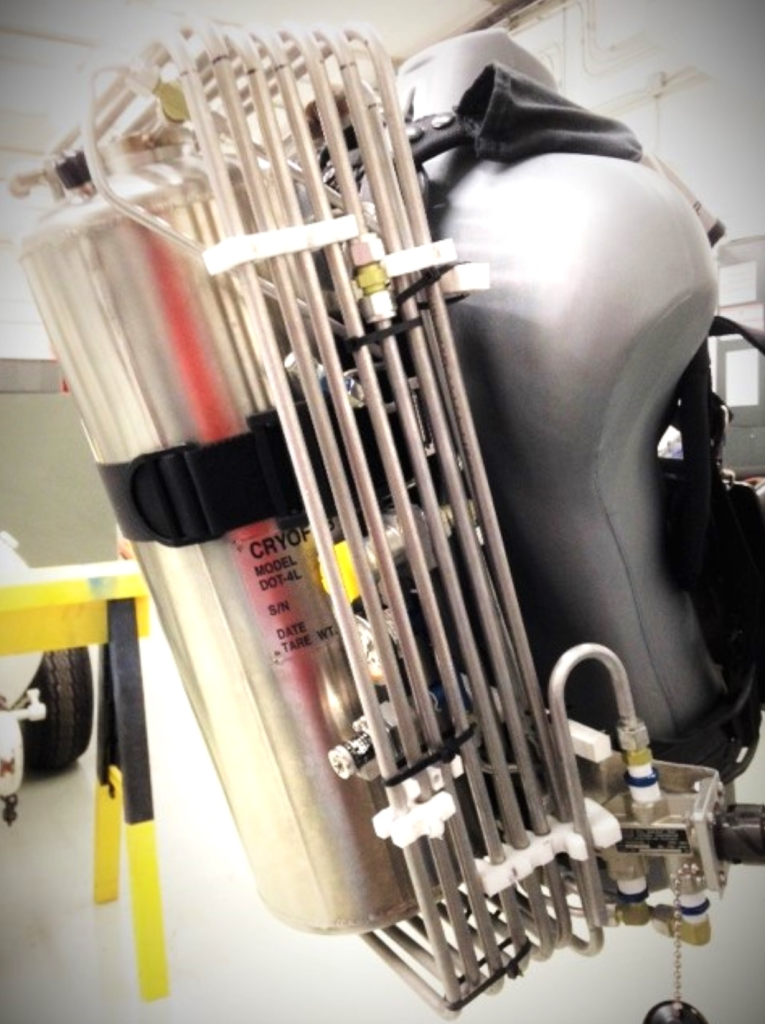
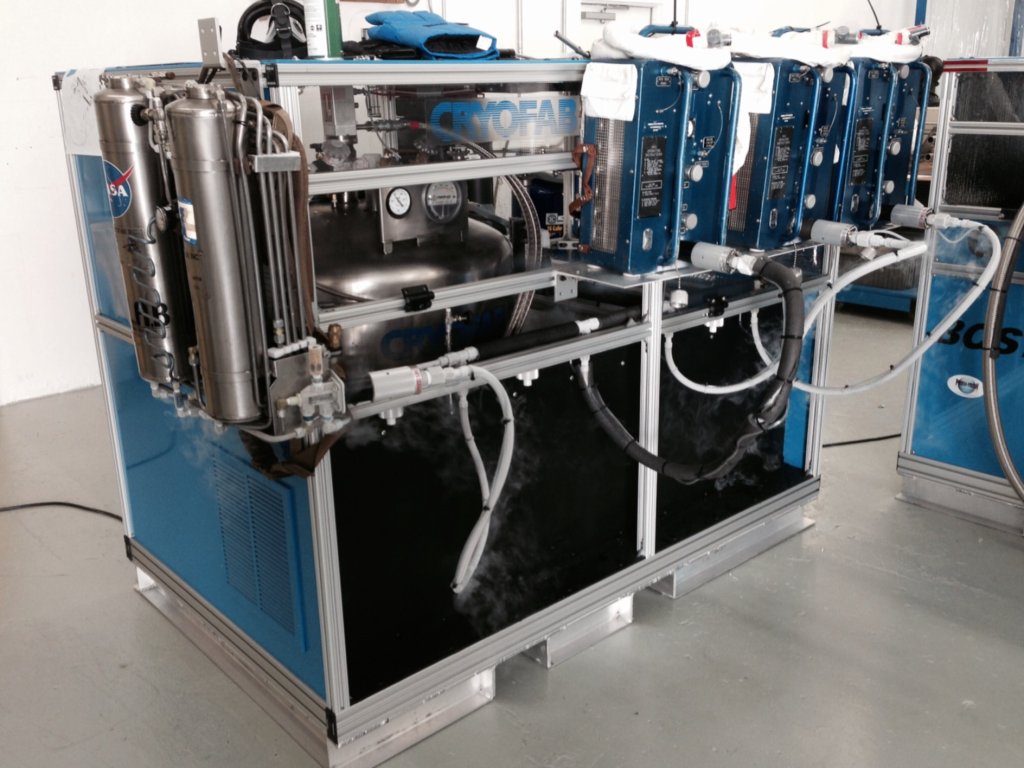

Therebreathersite was founded by Jan Willem Bech in 1999. After a diving career of many years, he decided to start technical diving in 1999. He immediately noticed that at that time there was almost no website that contained the history of closed breathing systems. The start for the website led to a huge collection that offered about 1,300 pages of information until 2019. In 2019, a fresh start was made with the website now freely available online for everyone. Therebreathersite is a source of information for divers, researchers, technicians and students. I hope you enjoy browsing the content!