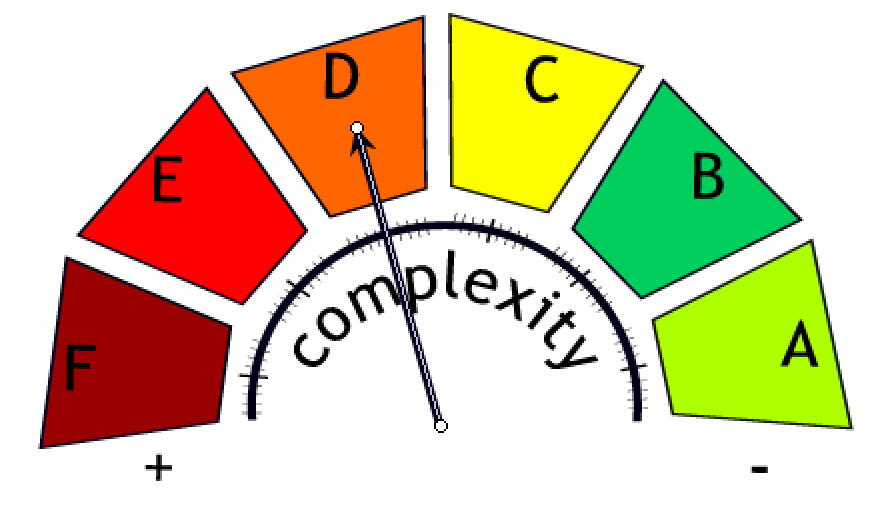
Around 1904, Prof. Dr. Max Bamberger Friedrich Böck and Friedrich Wantz patented a method of chemically converting exhaled air into clean reusable breathing air. The idea was to be able to use this substance in breathing apparatus so that no oxygen cylinder or scrubber was needed any more. The devices with chemically bound oxygen were equipped with a cartridge with chemicals in solid form. This chemical process has the advantage that the amount of oxygen produced is directly proportional to the breathing frequency. The oxygen carrier and potassium sodium superoxide was also called proxylene. From the chemicals, by the action of the exhaled carbon dioxide and water vapour, oxygen is produced according to the following chemical formula:
KNaO3 + CO2 = KNaCO3 + O2
KNaO3 + H2O = NaOH + KOH + O2
In addition to this reaction, the following takes place:
NaOH + KOH + CO2 = NaKCO3 + H2O
As a result of the carbon dioxide interacting with the potassium and sodium hydroxide, water vapour is produced which, in turn, contributes to oxygen production.
The device developed by Bamberger Bock and Wänz was called Pneumatogen and was produced in Vienna by the firm Neupert around 1905.
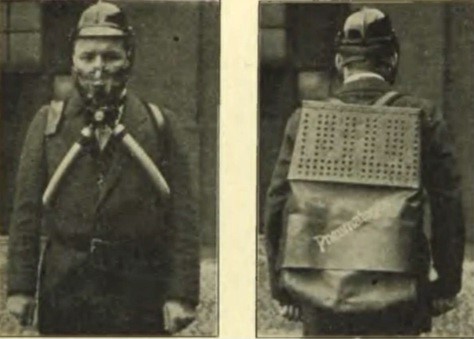
Production of the device was soon stopped and it was taken over by Dräger. Dräger produced a similar device under the name Draegerogen, but this was not successful either.
The big problem with these devices was that the oxygen supply did not start immediately when the device was put into operation, but that the chemical process had to be started first. Another big disadvantage was that the chemical process generated a lot of heat, and the superoxide forms dust when it produces oxygen.
For years, people have been experimenting with various chemicals to deal with these problems.
The following article by Dr. Albert Hloch from Berlin elaborates on the problem
OXYGEN-GENERATING PROCESS OF A NEW “CHEMICAL”
GAS-PROTECTIVE DEVICE
Dr. -Eng. Albert Hloch
Berlin
ABSTRACT: “Chemical” oxygen-generating devices, employing air regeneration by passage over alkali peroxides or decomposition of alkali chlorates are discussed in connection with their application in gas masks and other breathing apparatus.
“Chemical”oxygen-generating-gas-protective devices, also known as ,,self- contained” or “recycle-type” devices, provide the wearer with an artificial oxygen atmosphere which is isolated from the surrounding air and is generated, during use, through chemical reactions taking place in the device itself. Efforts are being made to eliminate by this design principle the need for compressed oxygen, stored in high-pressure cylinders, at 150 atm, and for related highpressure lines and reducing valves , because of which oxygen-generating gas – protective devices of older design are so heavy and sensitive. Elimination of compressed oxygen would not only significantly reduce the weight of the device, but would also make it unnecessary to replace the empty oxygen cylinder. The need for replacing this cylinder makes it difficult to use such self-contained devices, particularly in certain areas and for certain uses, e. g. , military applications. Because of the limited range of protection provided by filter devices – since the war (World War I) generally known as “gas masks”-efforts to simplify self-contained devices providing total protection are of practical interest.
The “chemical” oxygen-generating devices currently on the market, do not satisfy these requirements. The oxygen-generating substance in these devices is an alkali peroxide. The exhaled air is allowed to pass over the peroxide to remove the carbon dioxide and water vapor contained therein and, simultaneously, to generate oxygen. The air regenerated in this manner is then reused. Although this idea of a “chemical equivalent” of human lungs, first proposed by Bamberger and Bock (1), seemed very attractive, its realization proved to be very difficult for the following reasons: a) The heat given off by the reaction causes an excessive rise in temperature of the inhaled air (above 60° C); b) the expansion and sintering of granular alkali peroxide with progressive use results in increased resistance to air flow which exceeds the permissible limit (160 mm H2O); c) since the reaction of the peroxide with exhaled air is sufficiently rapid only at somewhat elevated temperatures, during a certain initial use period (“breating induction” period, 2-5 min) the device does not produce the required amount of oxygen. Attempts have been made to eliminate these deficiencies by use of special peroxide processing techniques (addition of catalysts, introduction of 6% water); however, this approach is handicapped by the fact that the storage stability of the material is reduced by the water of hydration.
In contrast to this type of oxygen-generating apparatus, a new, recently introduced device (Inhabad GMBH Naszogen geräte, see other pages in the Rebreathersite Vademecum) generates oxygen by thermal decomposition of alkali . chlorates. Here, the oxygen-forming process is independent of the breathing activity, in contrast to alkali peroxide-type devices in which this process is supposed to be regulated by the breathing. In the new device, as in equipment using compressed oxygen, carbon dioxide must be removed from the exhaled air by passing this air through cartridges containing granular caustic alkali. The new device is thus not based on the principle of simultaneous oxygen formation and carbon dioxide absorption in a single, reaction. This indicates that, even after 25 years of development, it was not possible to apply this principle to gasprotective devices.
A requirement for oxygen generation, in gas-protective devices , by thermal decomposition of chlorates according to the equation ;
KCL03 = KCL + 3/2 O2 + 9. 8 cal
is that it must be controllable. A sudden, non-regulated evolution of the total amount of oxygen required for a certain use period, as previously proposed for gas-protective devices, would make it necessary to store the oxygen. This could be achieved
a) under conditions of practically no pressure, in gas-tight containers, e. g. , rubber bags, which however, cannot be used in portable equipment, because of their excessive volume (a 300L capacity would be required for a 2-hour use period) or
b) under pressure, in thick-walled, heavy containers, requiring pressure-reducing valves for removal of oxygen.
Both these situations are to be avoided, however.
The oxygen supply must, therefore, be regulated so that the oxygen requirements of the wearer are satisfied both during light and heavy work conditions. According to specification guidelines for gas-protective devices used in mines, issued by the Prussian Commission for Mine Safety, such devices should be designed for an average oxygen consumption of 1. 31/min, corresponding to a marching rate of 6 km/ hr. In addition, they should provide enough oxygen for a peak consumption of 3 l/min for a minimum of 1 min and a maximum of 5 min. In the new device(INHABAD), oxygen generation from chlorate occurs at a rate of 2. 5 1/ min, which satisfies total oxygen requirements for medium and high work conditions. During peak activity, corresponding to an oxygen demand of 3 l/min, the wearer obtains additional oxygen from a breathing bag which is inserted into the breathing cycle, and has a capacity of 7 liters. This bag is filled with oxygen produced in increased amount during the starting period. Thus, during the period of peak activity lasting at the most 5 min, 2. 5 l of oxygen is removed from the bag, with about 4 liters still remaining.
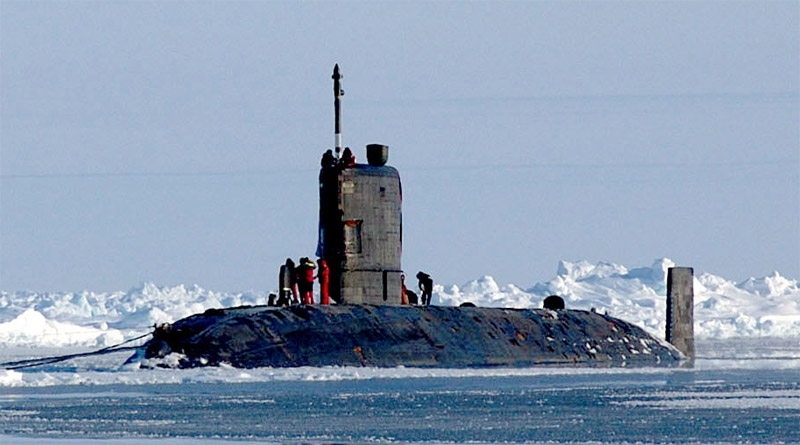
Royal Navy submarine Tireless
oxygen candle accident
2007: Royal Navy submarine Tireless accident:
Yesterday’s accident in which two sailors were killed aboard the Royal Navy submarine Tireless did not involve any of the submarine’s machinery or installed systems, it has emerged.
According to US and British naval sources, the explosion instead involved an oxygen candle. Some news sources have said oxygen candles are “equipment” which is “fitted” in submarines, giving a misleading impression of what they are.
Oxygen candles are consumable items not unlike large marine flares in construction and use. When lit or initiated, they give off oxygen rather than regular combustion products. They are carried for use in an emergency, where the normal atmosphere equipment is unserviceable or inaccessible (perhaps flooded) and the submarine cannot surface. In such a situation, sailors may need to replenish local oxygen levels while awaiting rescue or a chance to escape – hence the candles. They are normally stowed in the escape compartments forward and aft.
Escape compartments are pressure-tight airlocks where submariners can retreat in the event of a disaster. From there, depending on the situation, they may be able to escape to the sea surface using specialised breathing sets. But in some circumstances – if the sub is too deep, or if the sailors have been under too much atmospheric pressure for too long – it may be better for them to wait until rescuers can reach the scene.
Like any oxidising material, oxygen candles present a fire and explosion hazard – the more so in a confined space. All submarines, and indeed surface fleet units, are full of things like this. Emergency breathing apparatus, diving sets, smoke markers, flares, munitions, medical gases … the list goes on. Every warship is a highly dangerous industrial facility, full of hazmat. Tireless has suffered a relatively normal industrial accident.
Today, rescue equipment is used daily in mining and industry. Worldwide, thousands of devices are carried daily by technicians to their workplaces. In an emergency, the rescue device provides approximately 20 minutes or more of oxygen to breathe in a contaminated atmosphere. These devices are often equipped with a ‘starter’ and are usually fitted with a nose clip and goggles. The design of these devices is subject to constant improvement. The special properties of superoxide were also used for a long time in the field of diving apparatus. In the USSR, for example, O-3, a superoxide, was used in addition to the scrubber to extend diving times. The exact composition of these super oxides is subject to trade secrets. The trick is to compose the material in such a way that oxygen production is constant, heat is limited and gas delivery time is maximised. The cartridges for underwater use have a bad reputation because the substance can react explosively as soon as it comes into contact with water!
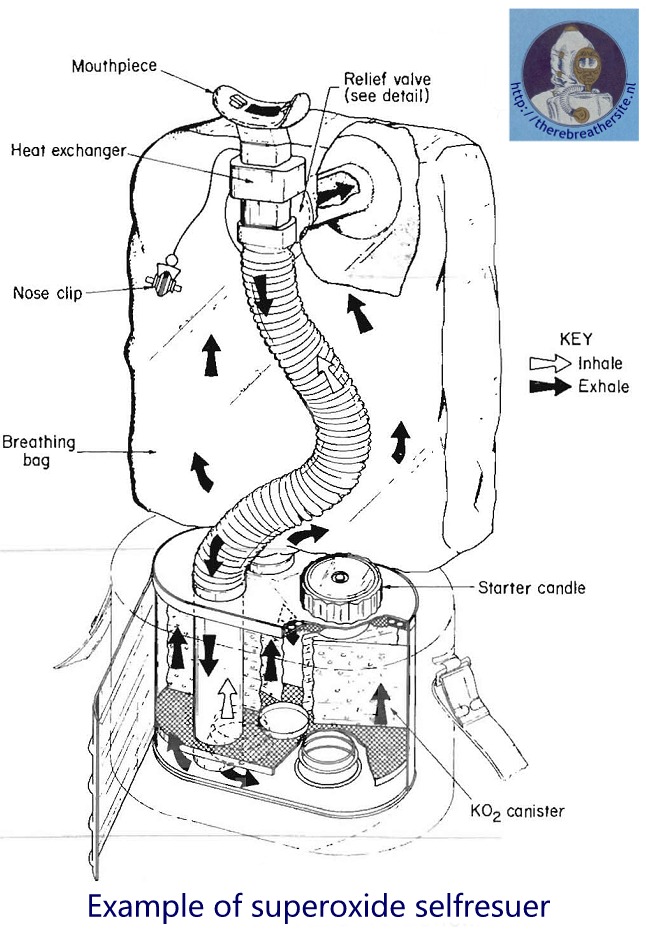
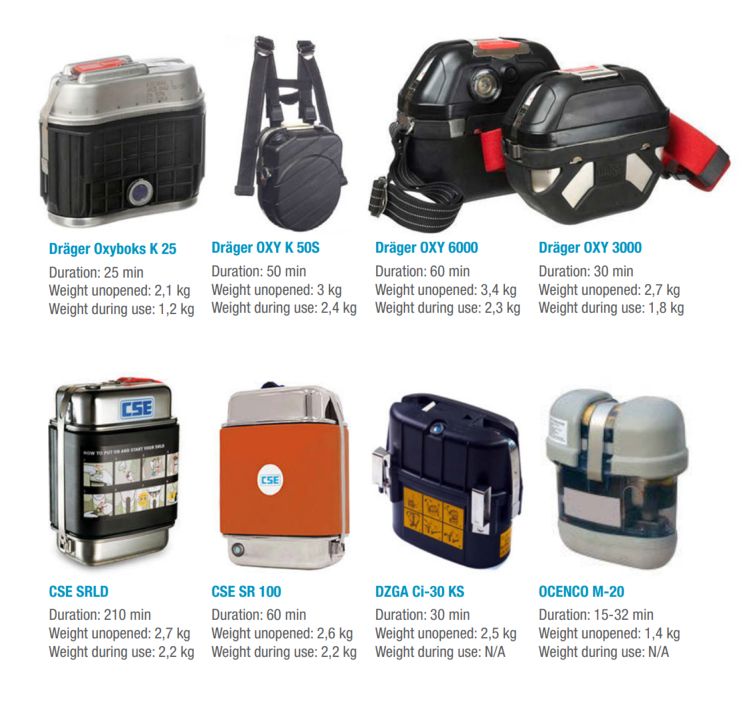
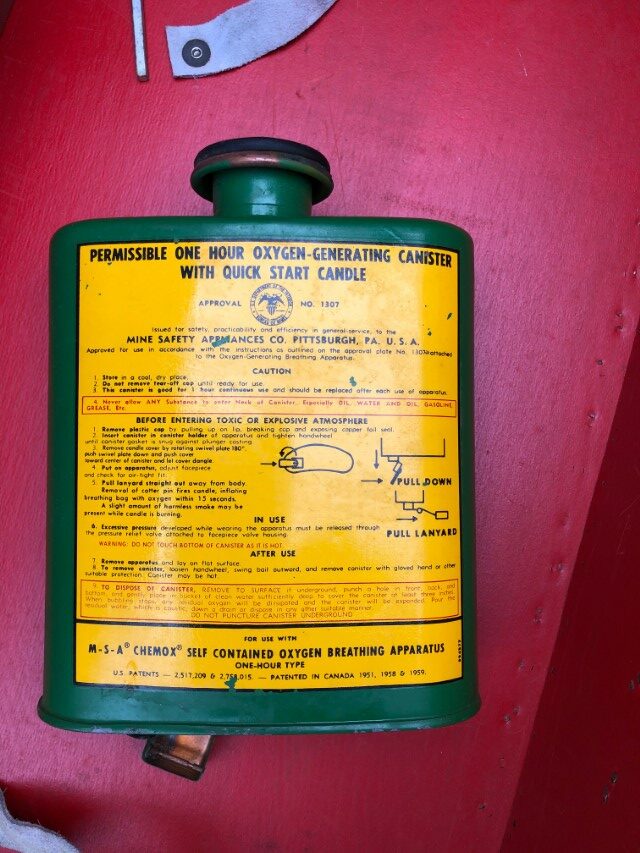
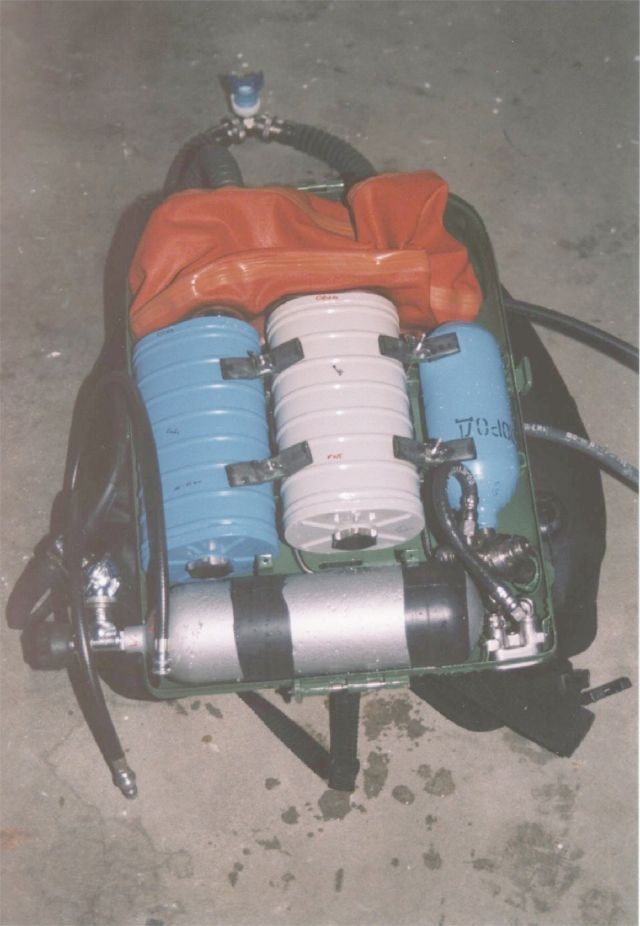
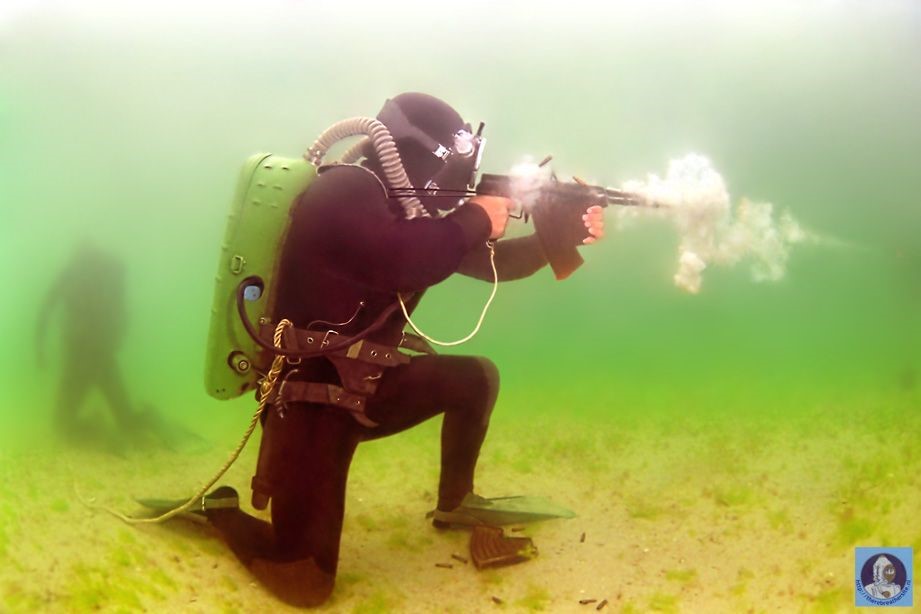
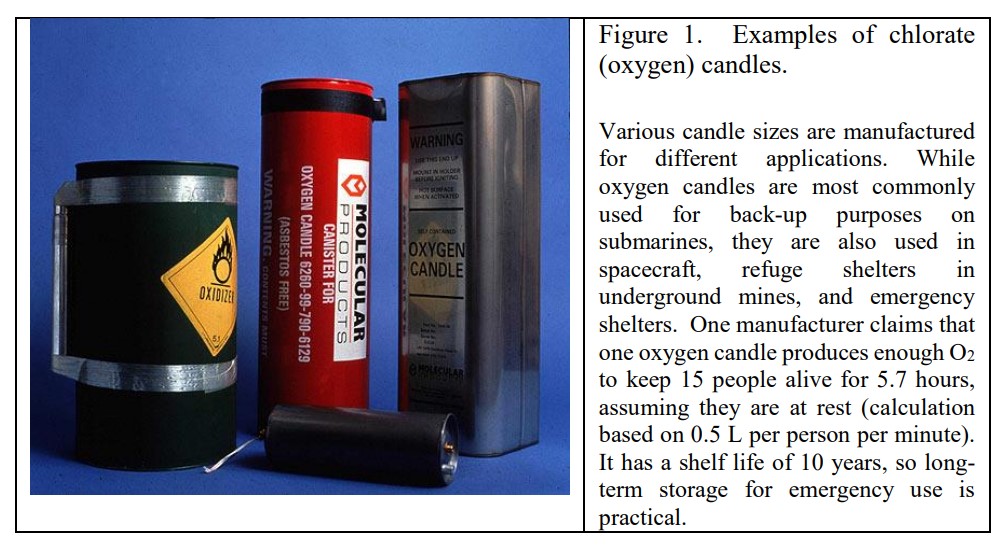
All information of breathing apparatus using alkali superoxide or units that work with chemicals is welcome. If you can contribute with technical infomation all information related to this subject is welcome!
Thanks to Anders Sandström, I have been given the opportunity to offer you an insight into the modern way of developing and prototyping a product from concept to working model. Anders made this work as his Bachelor Thetis for Industrial Design. His website can be found here: http://Sandstromanders.com and by email at Anders.Sandstrom@epiroc.com , thanks Anders!
Video Courtesy Valery Muckin