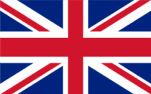
Fire brigade & Mine Rescue Oxygen rebreather
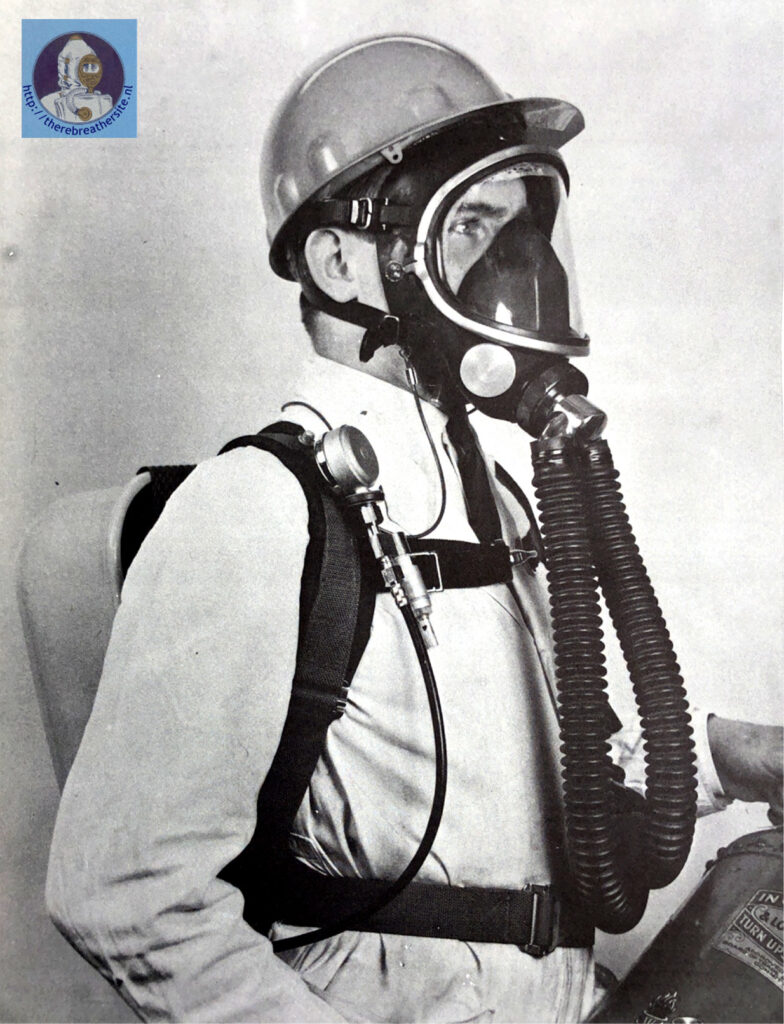
The Minox was developed as an “inspection” apparatus, to enable untrained mines inspectors or managers to wear as it was fully automatic, being accompanied by a full rescue team. It wouldn’t be used as a team of 5 or 6 for instance except for training. In the 60’s Siebe Gorman developed this closed oxygen system both for mining rescue and fire brigade operations. Produced in large numbers, it is a back-worn device with breathing hoses passing under the left arm. The system is designed so that it can be taken apart without using tools.The unit has several clever additions compared to other closed oxygen systems. For use in an environment with hazardous gases, smoke the system could be fitted with a full-face mask and for the use in mines with a mouthpiece and nose clip.
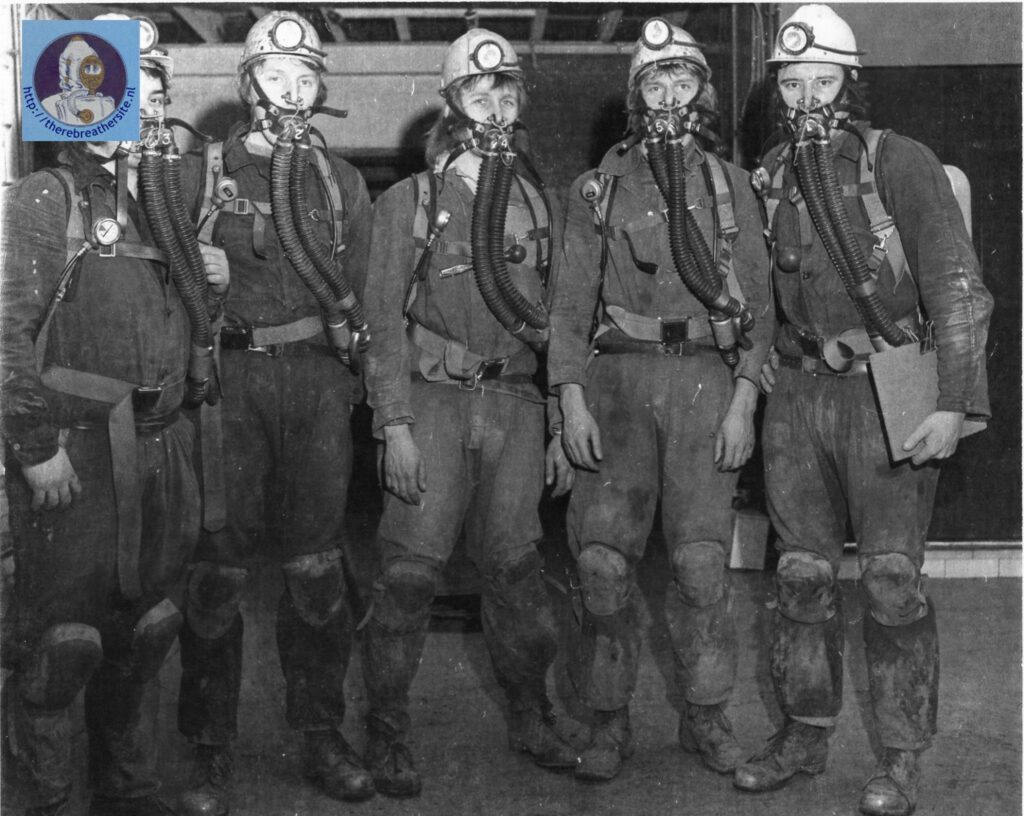
The unit is equipped with a 1.1 kg protosorb cannister and a 2 litre oxygen cylinder. With this configuration, an operating time of 1 hour with a 25% reserve could be achieved in heavy work. A Siebe Gorman innovation was the replacement of the traditional pressure regulator with a dosing or flow control unit that is significantly more compact. The unit delivers a flow rate of 6-8 litres per minute.
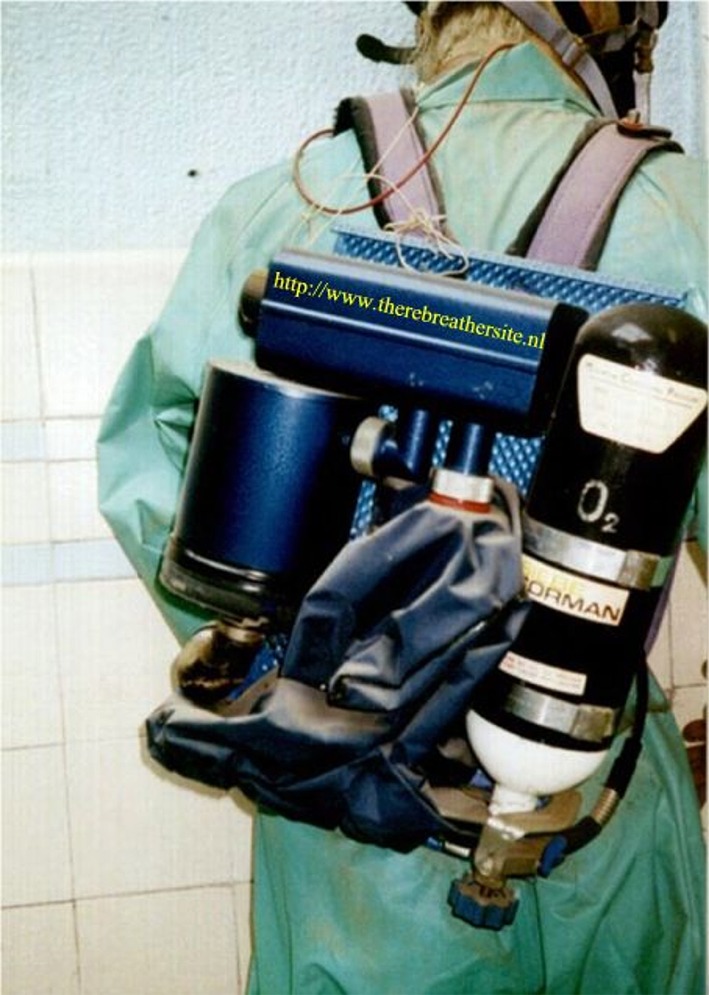
The back-worn device can be disassembled entirely by hand. On the left side of the back is the scrubber, above which is a rectangular compartment containing a special substance to cool the breathing air. This substance consists of crystals of sodium phosphate activated by water vapour. During this process, heat will be extracted from the environment, creating a cooling effect in the medium from which the heat is extracted. By conducting the breathing air parallel to the sodium phosphate trapped in a copper pipe, the cooling effect will cool the breathing air. So, in effect, a small chemical refrigerator. This technique is already very old because even books from the 1930s mention this cooling technique, and the cooling system with Sodium Phosphate was applied to the Proto unit in 1921 already!
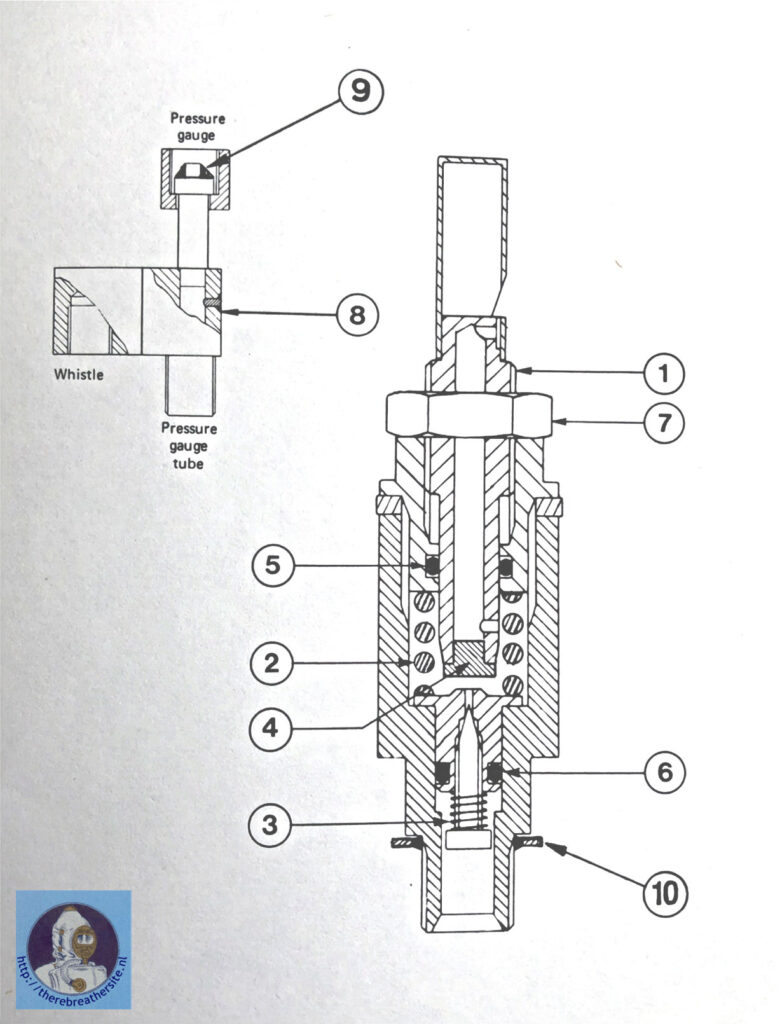
The pressure gauge worn on the shoulder fulfils another safety function together with the pressure indication, namely an acoustic signal if the pressure in the cylinder should become too low. The signal consists of a whistle that is activated when the pressure is too low. Another feature is the initial high flow rate of 7 litres per minute that will automatically flush the entire circuit and then decrease to 2 litres per minute. Between the flow control valve and the cylinder is another silica gel capsule that dries the oxygen during filling. This will reduce the moisture content such that the unit can be used down to -16gr C. The connecting hose between HP controller and the pressure gauge is equipped with a manually operated valve that can be closed in case of damage to the hose so that the oxygen can be used without the cylinder will empty. The contralong is made of rubber-coated nylon making it lightweight and particularly strong.
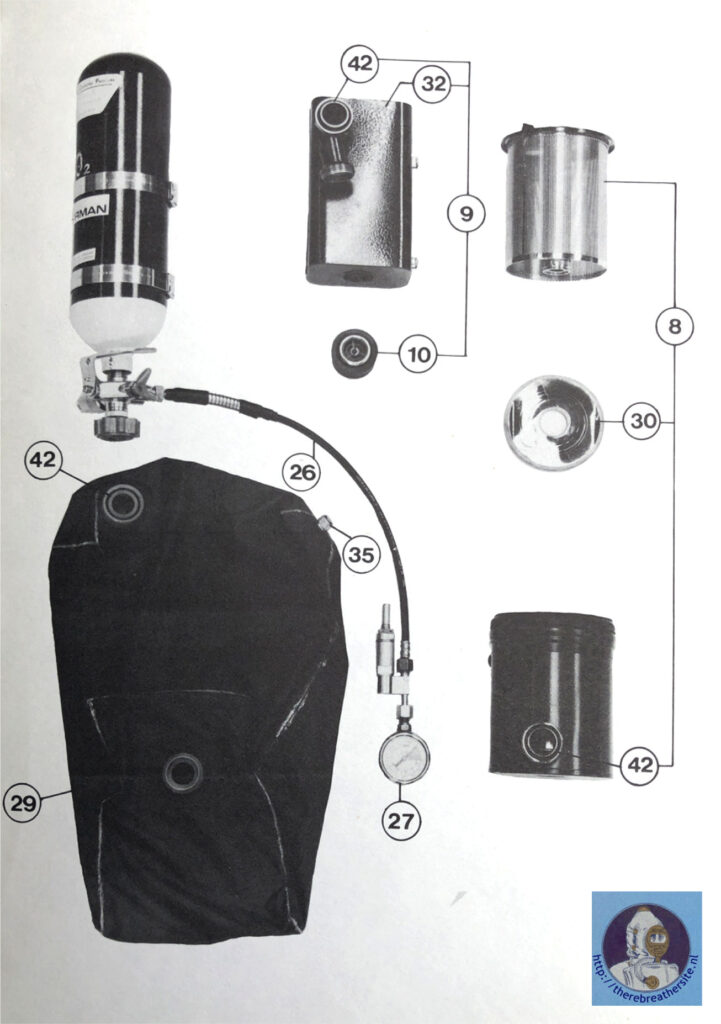
The entire unit is made of first-class materials, extremely compact and very cleverly constructed. Even 60 years after production, all components are still in good condition. Unfortunately, rubber does prove to be prone to ageing but these components can generally be easily replaced.
Finally, I would like to thank everyone who contributed to put this article together.
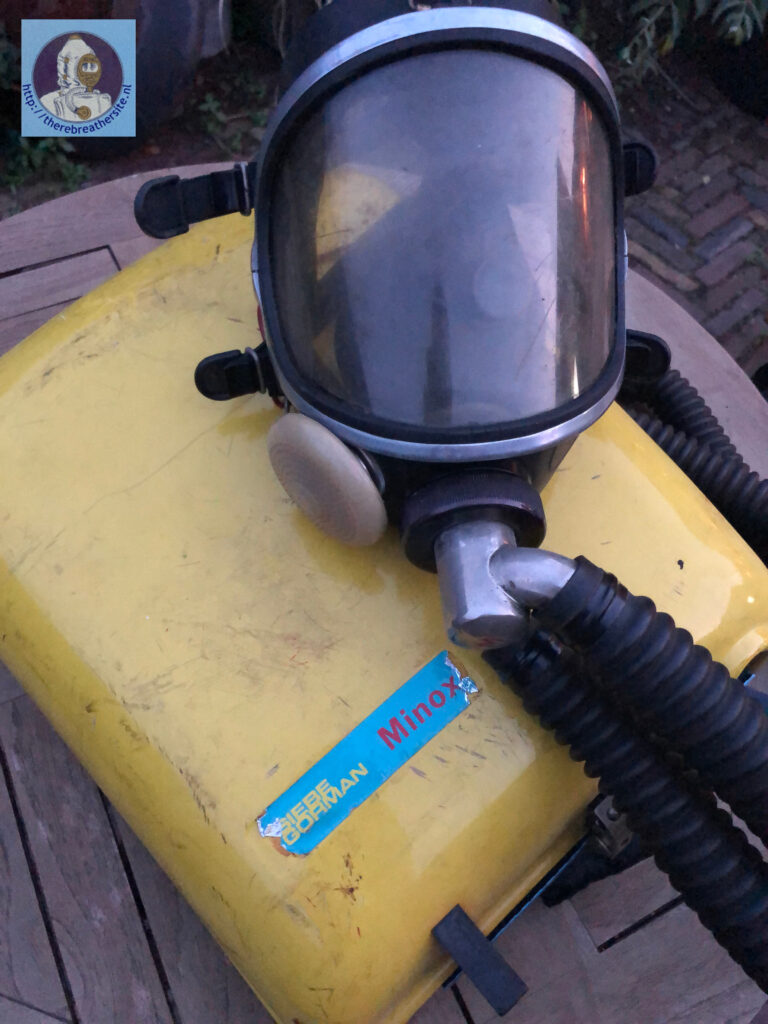
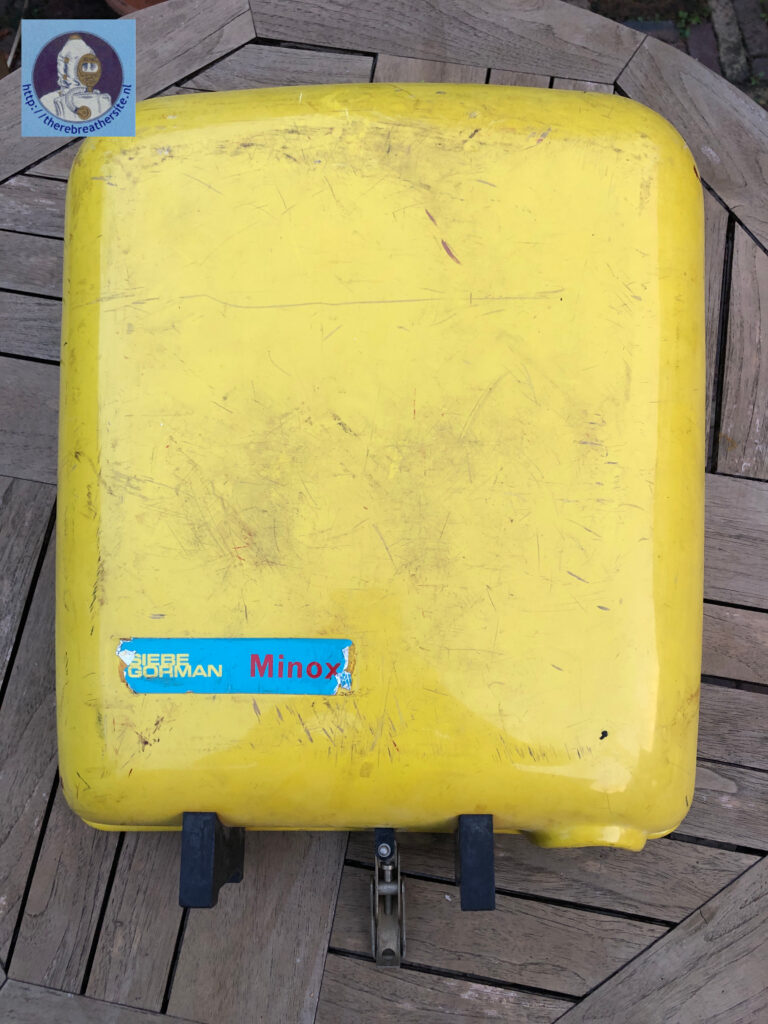
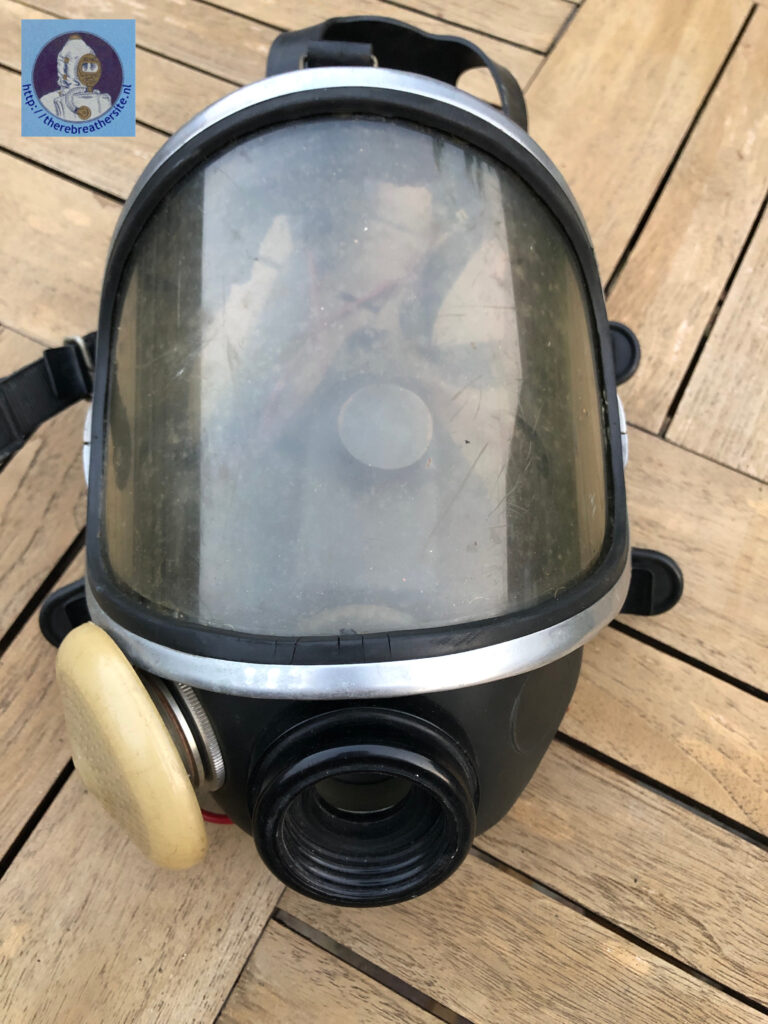
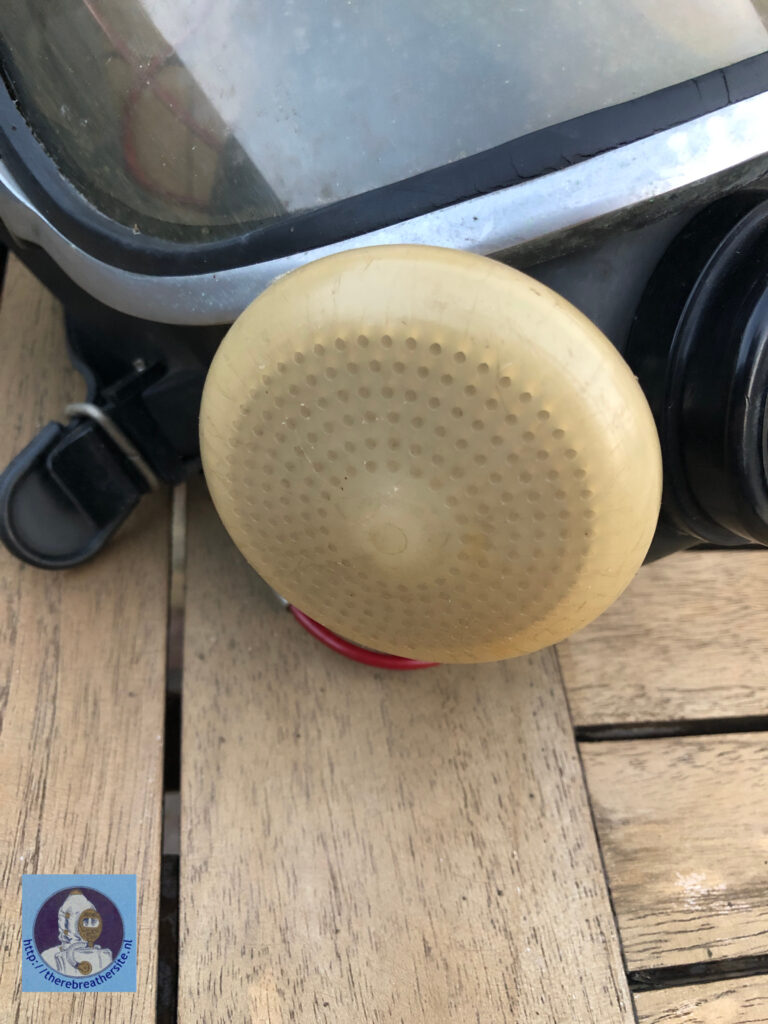
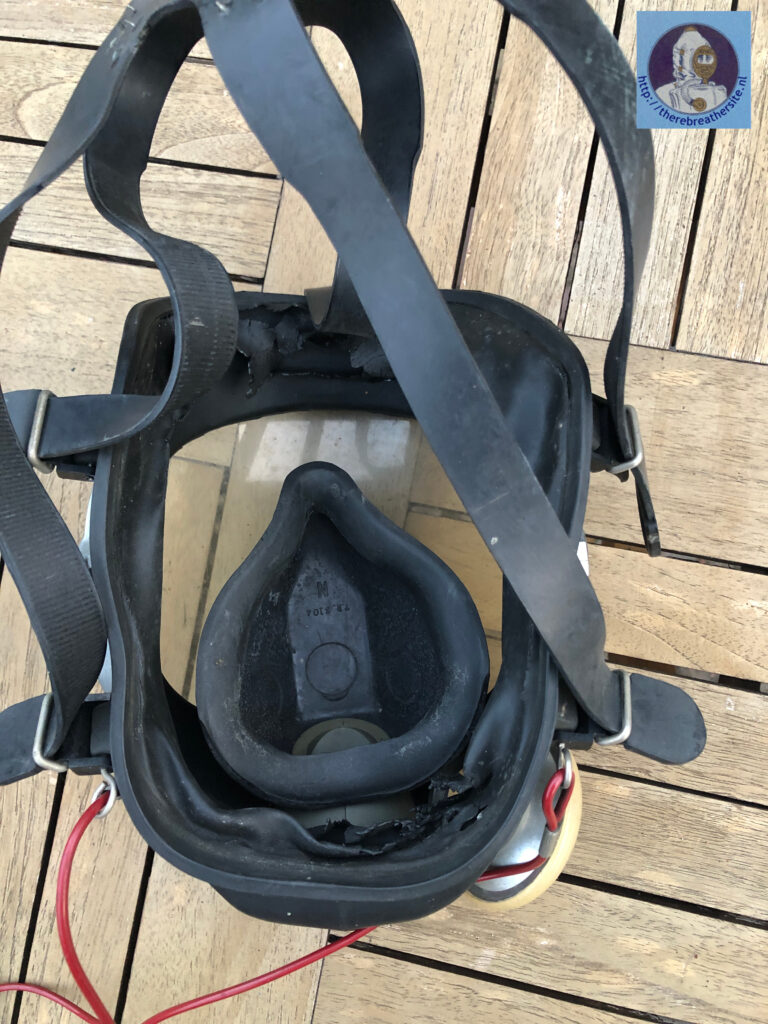
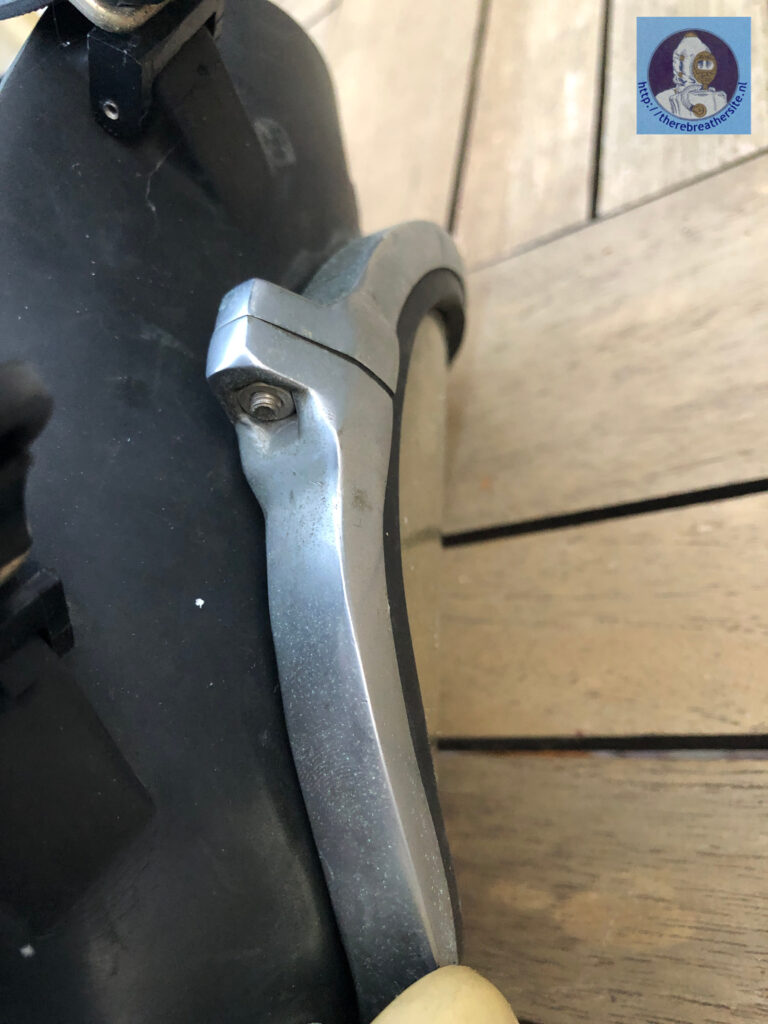
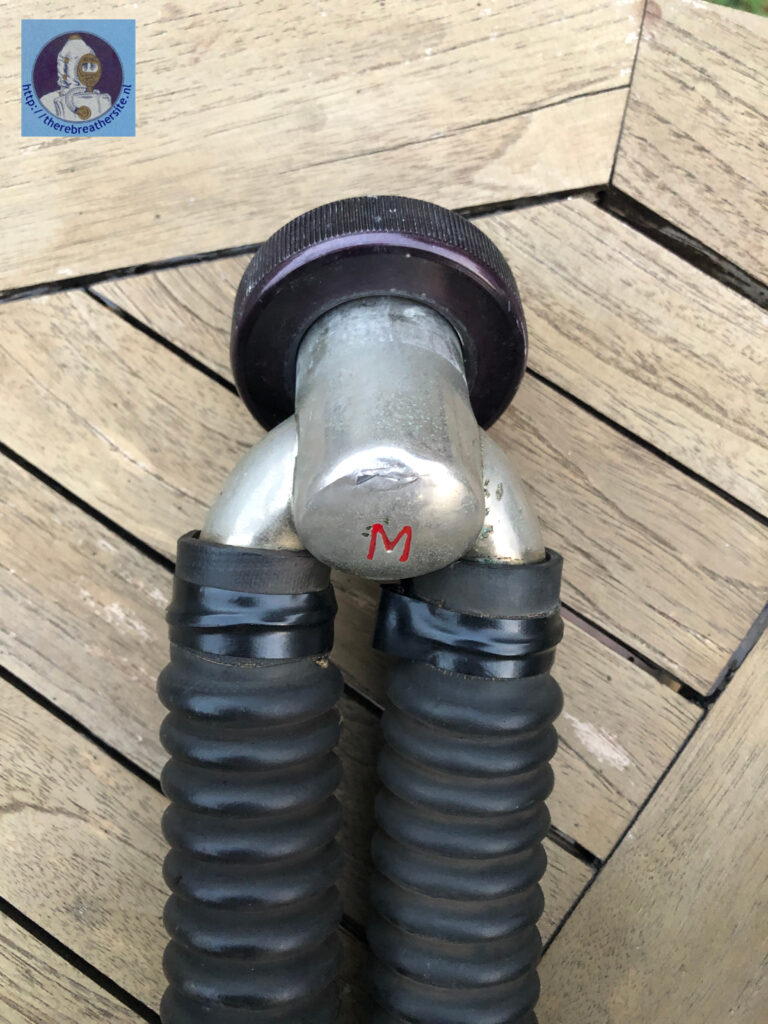
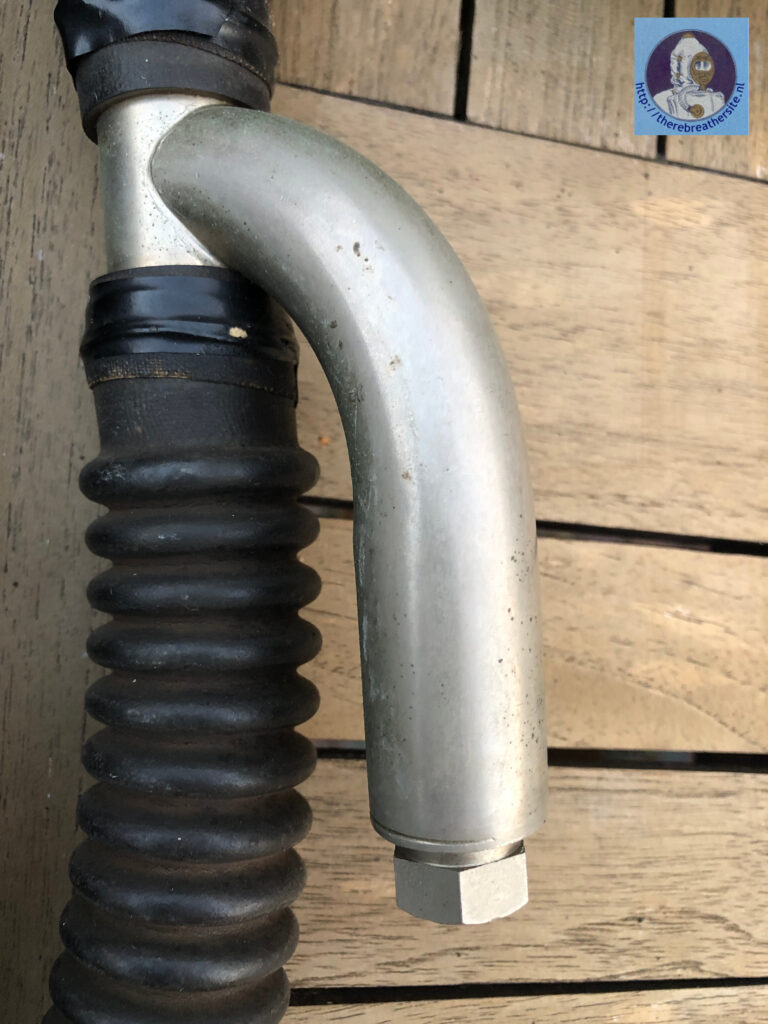
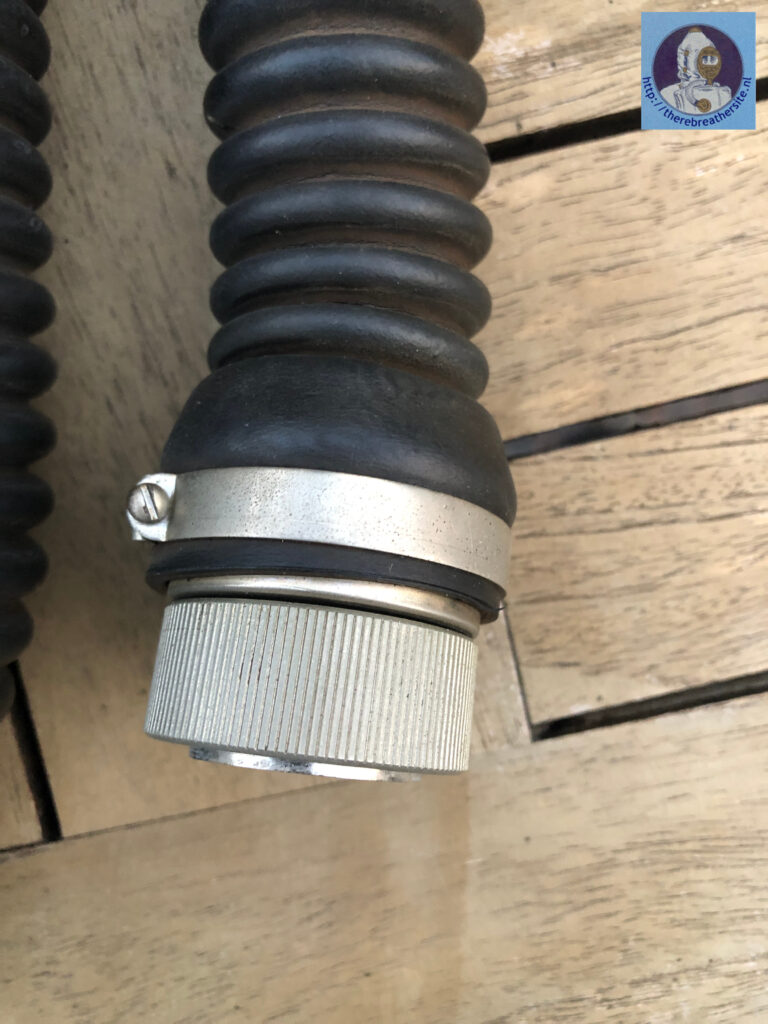
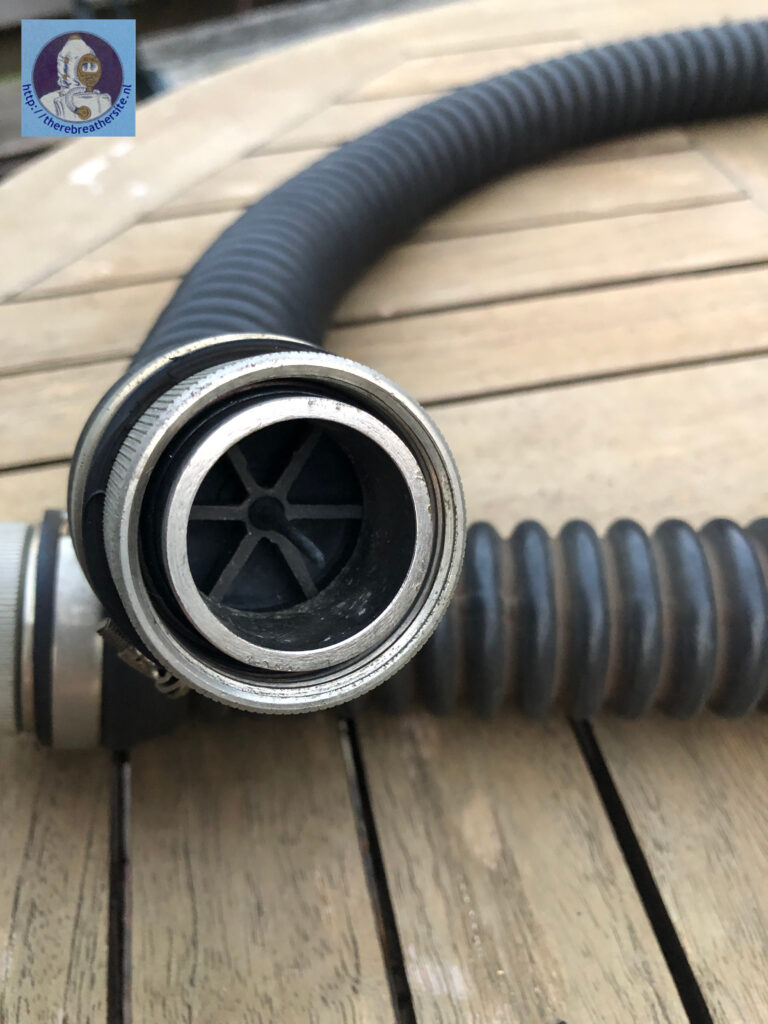
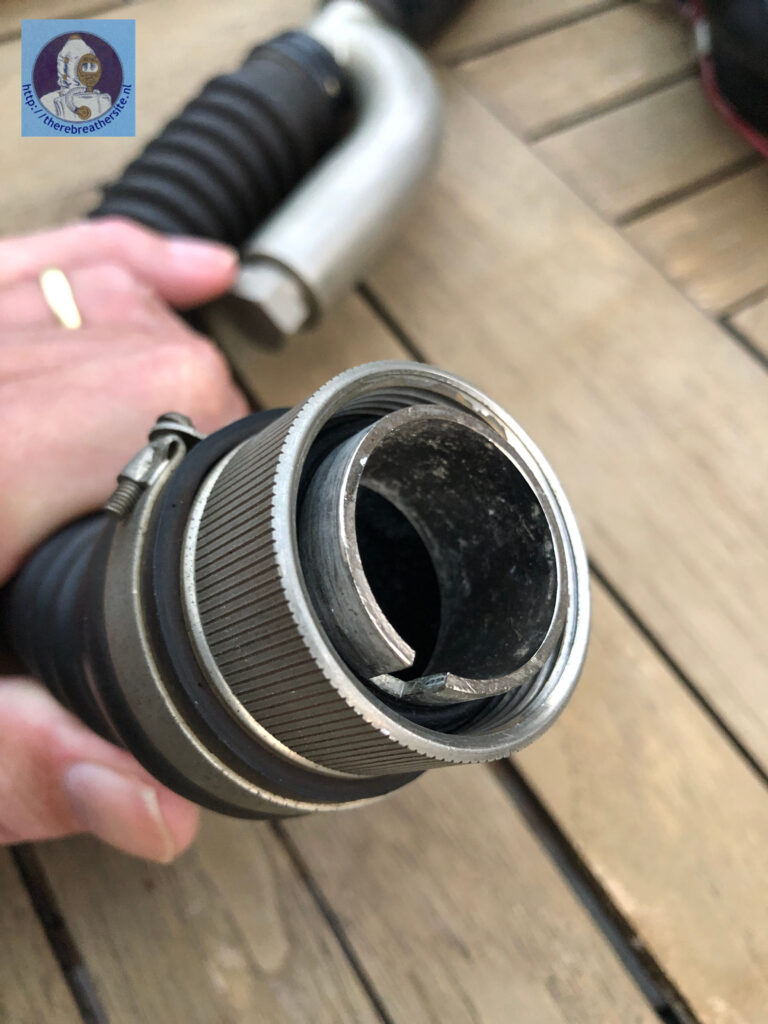
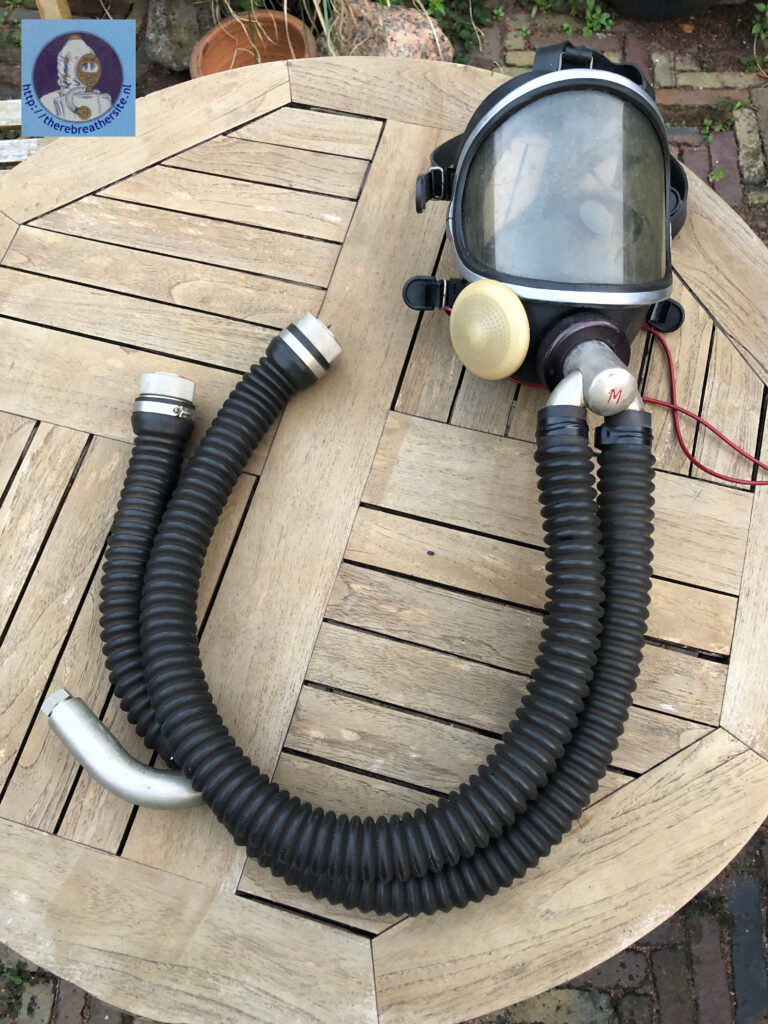
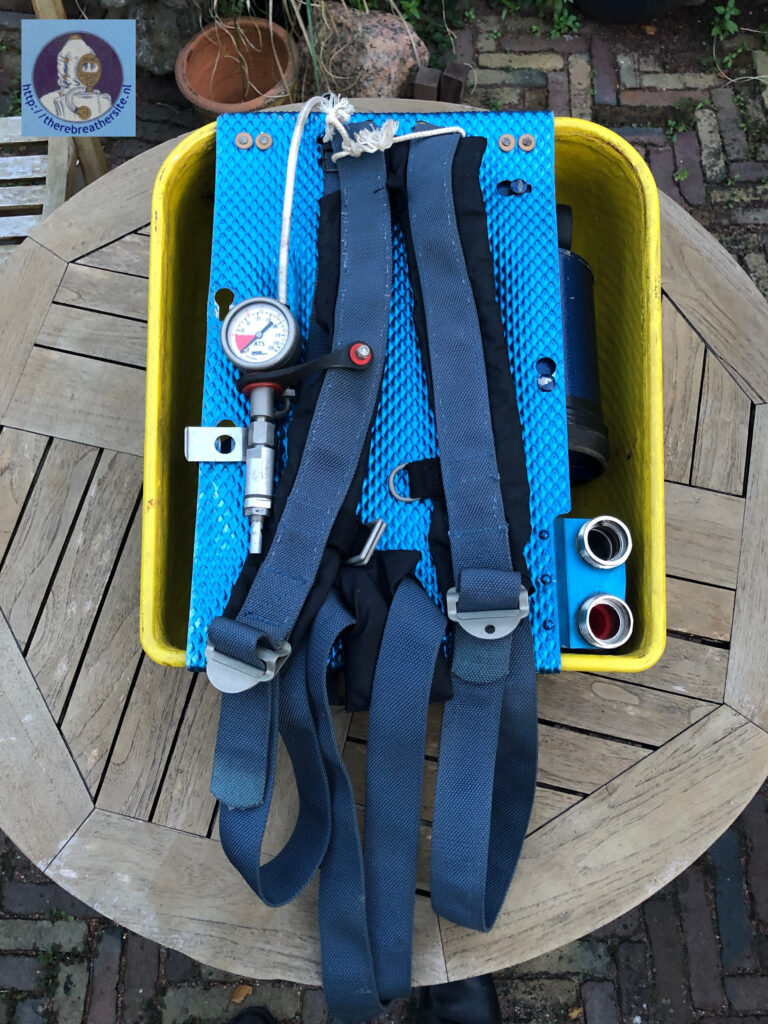
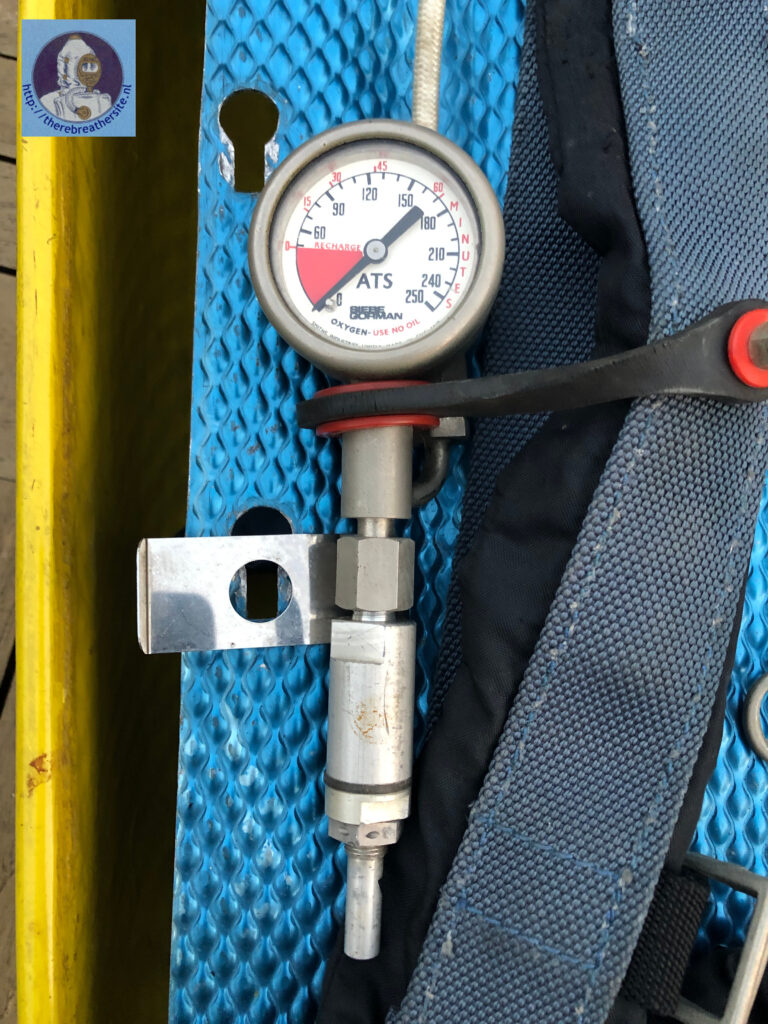
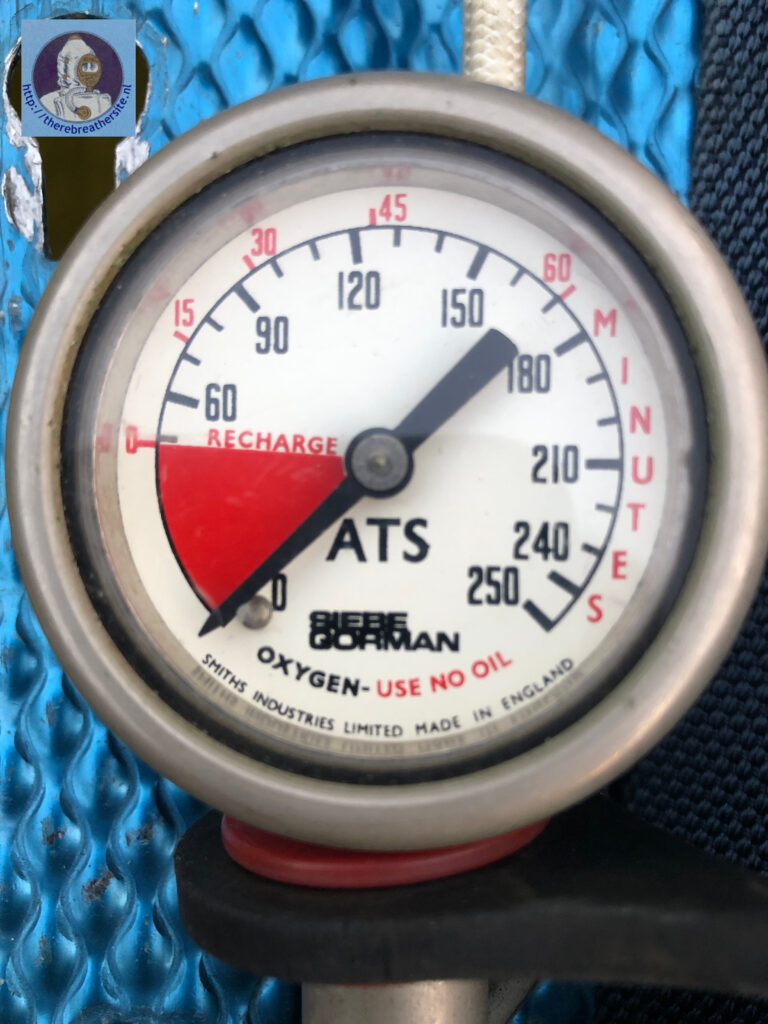
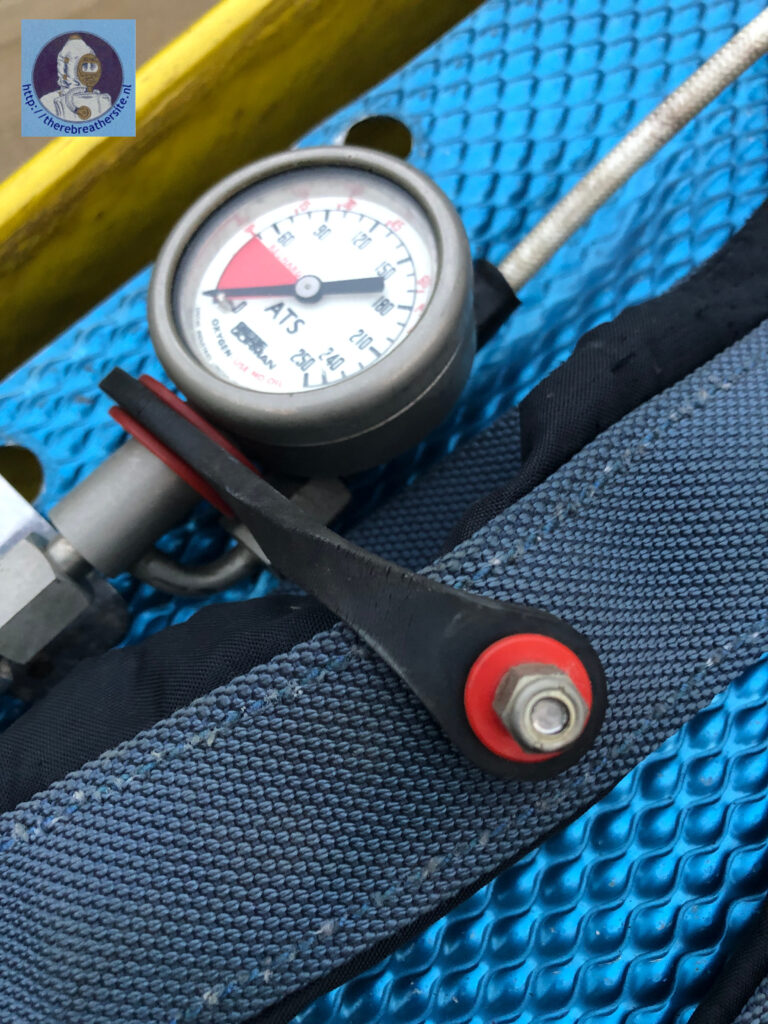
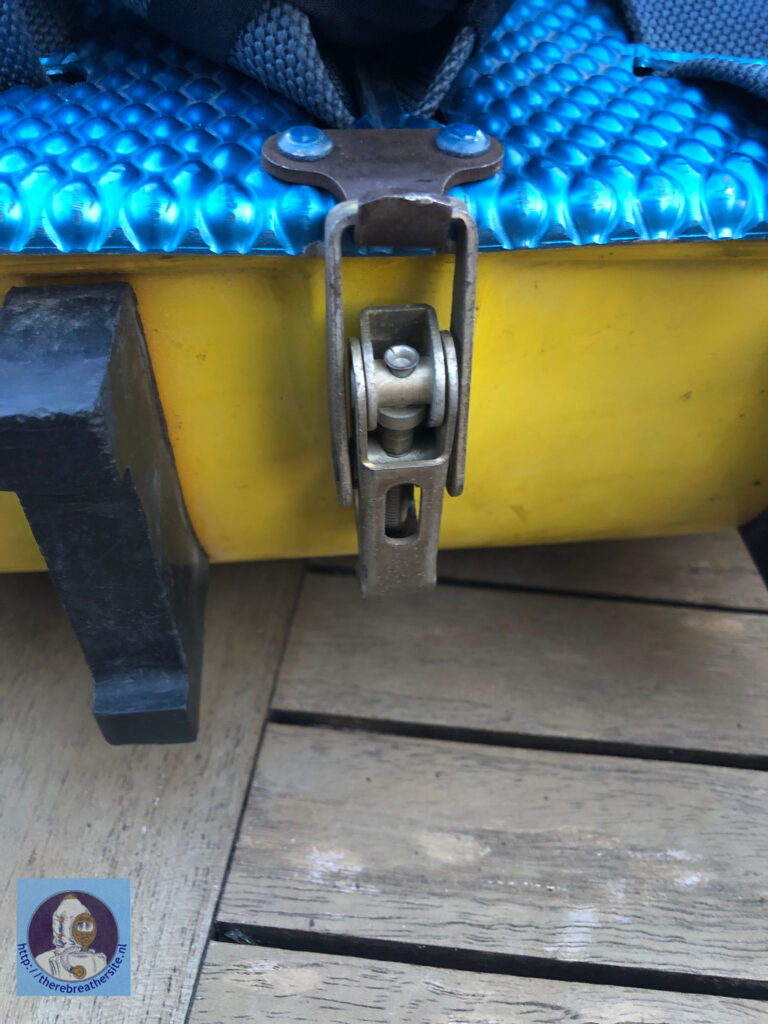
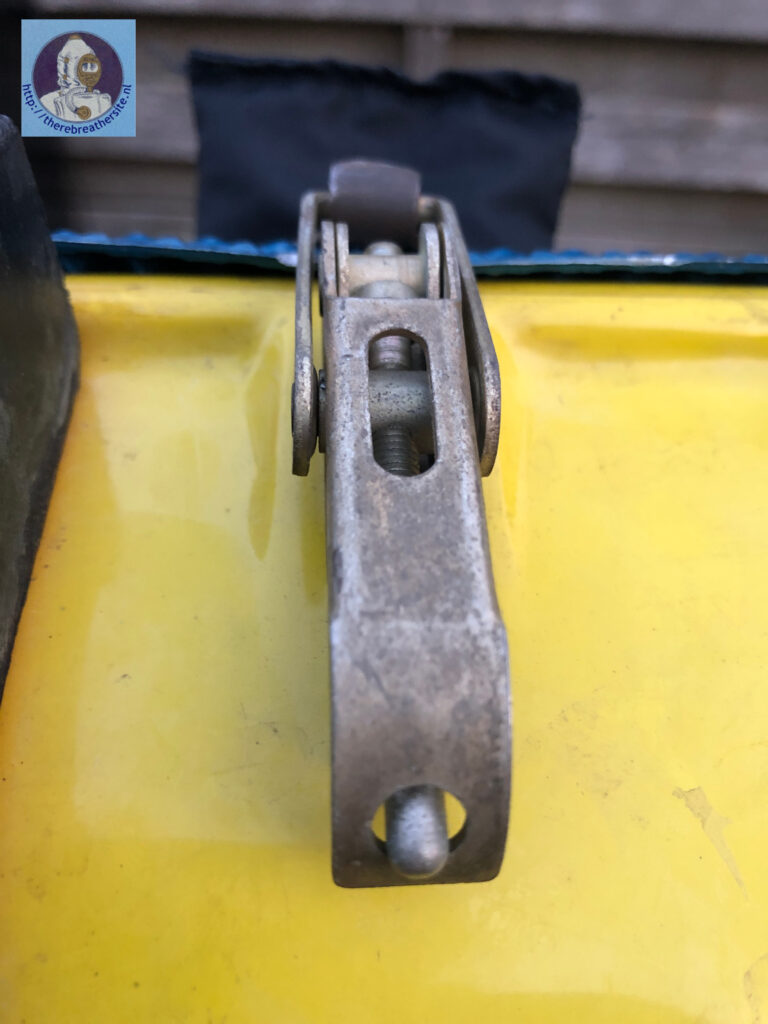
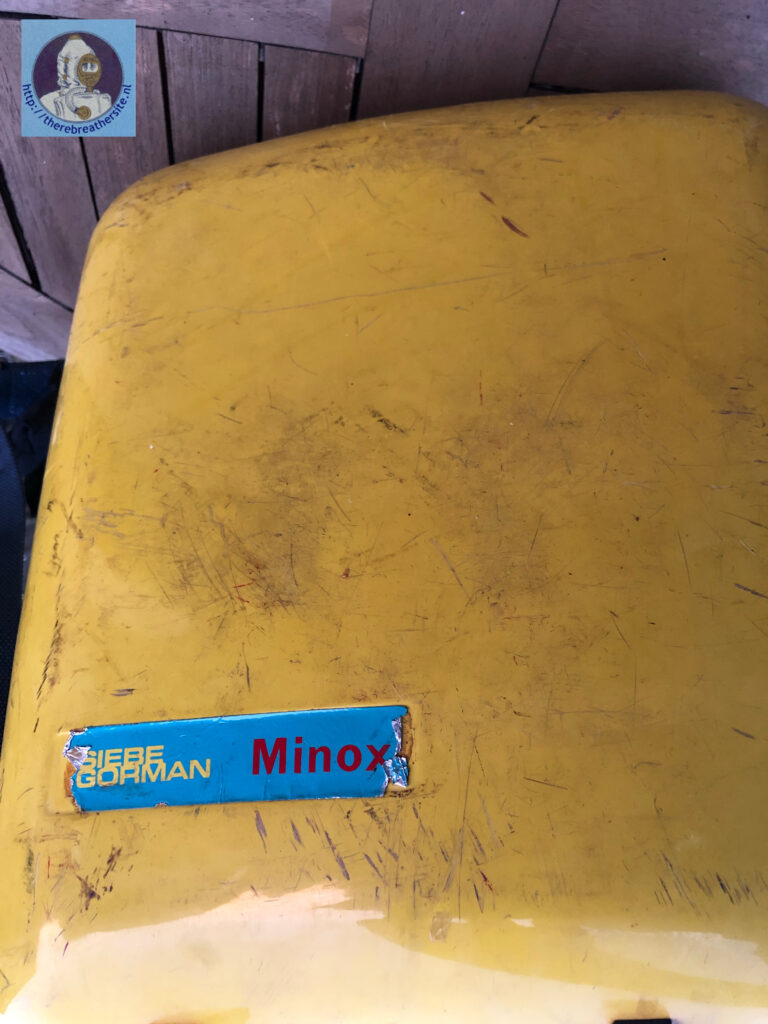
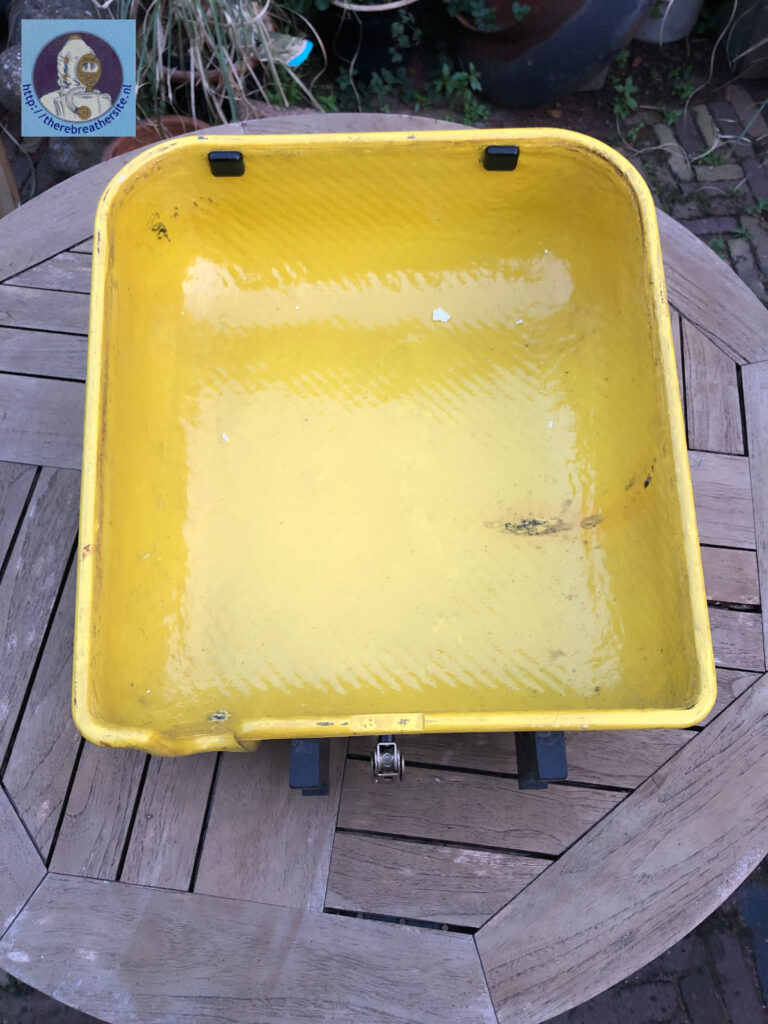
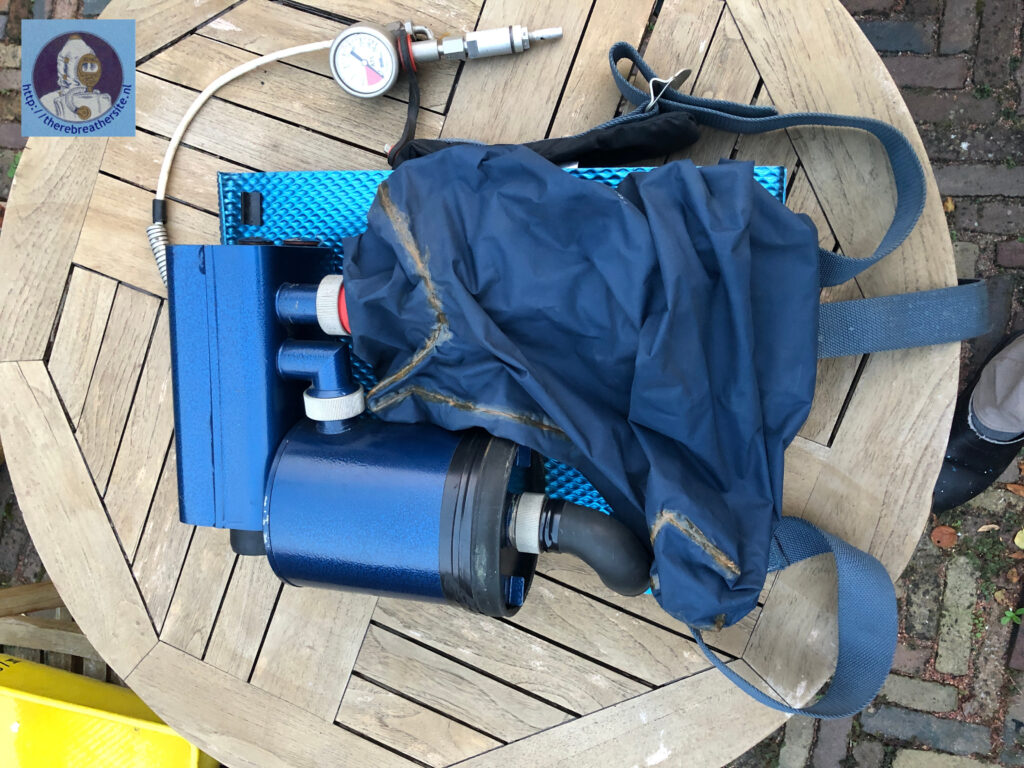
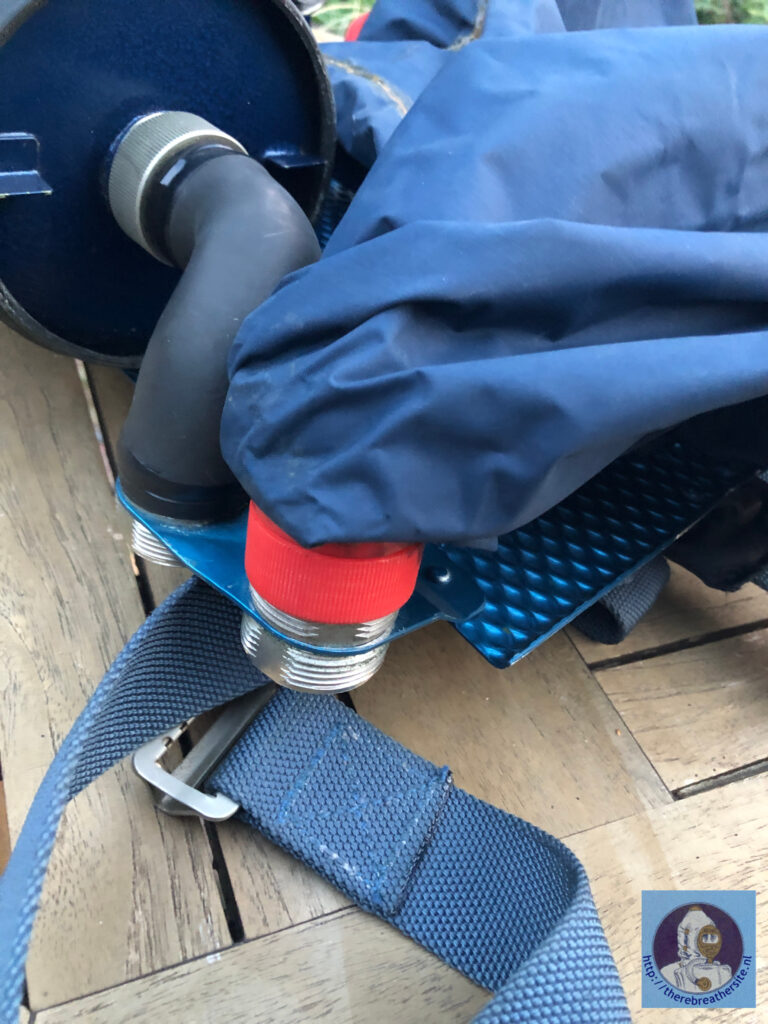
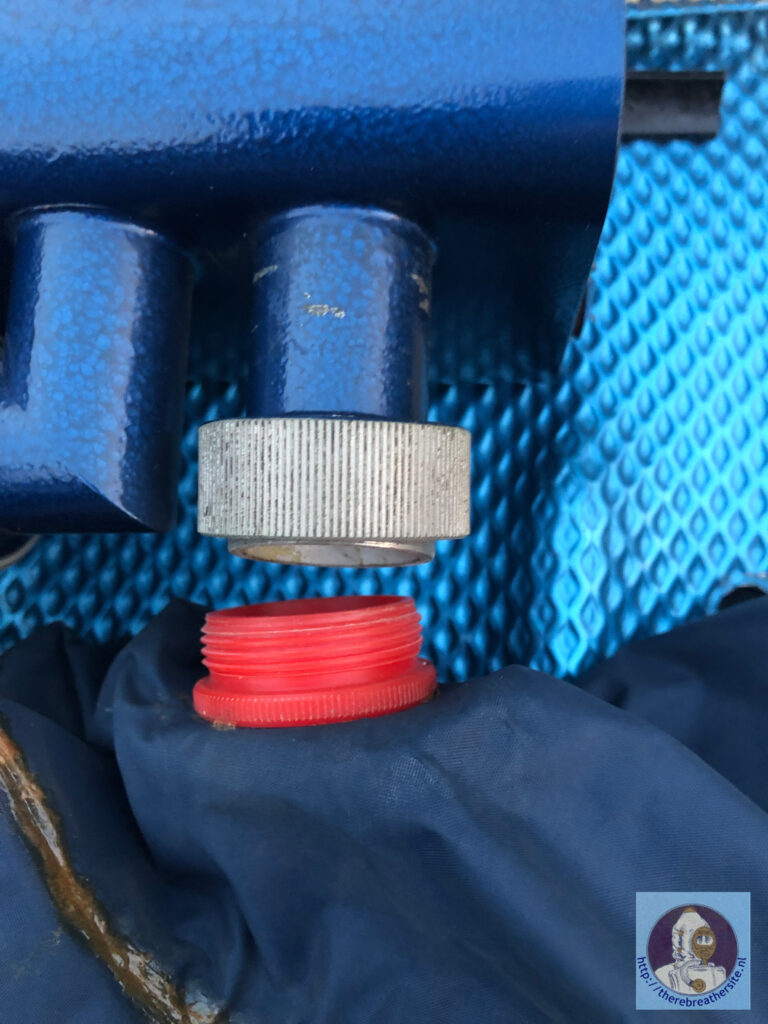
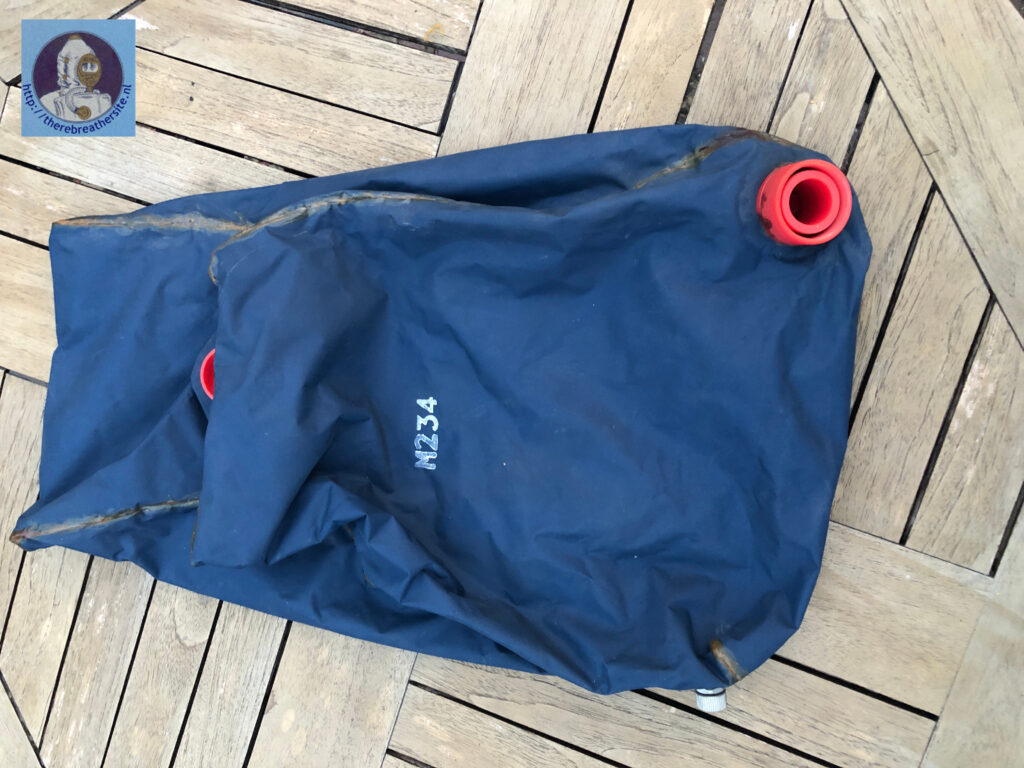
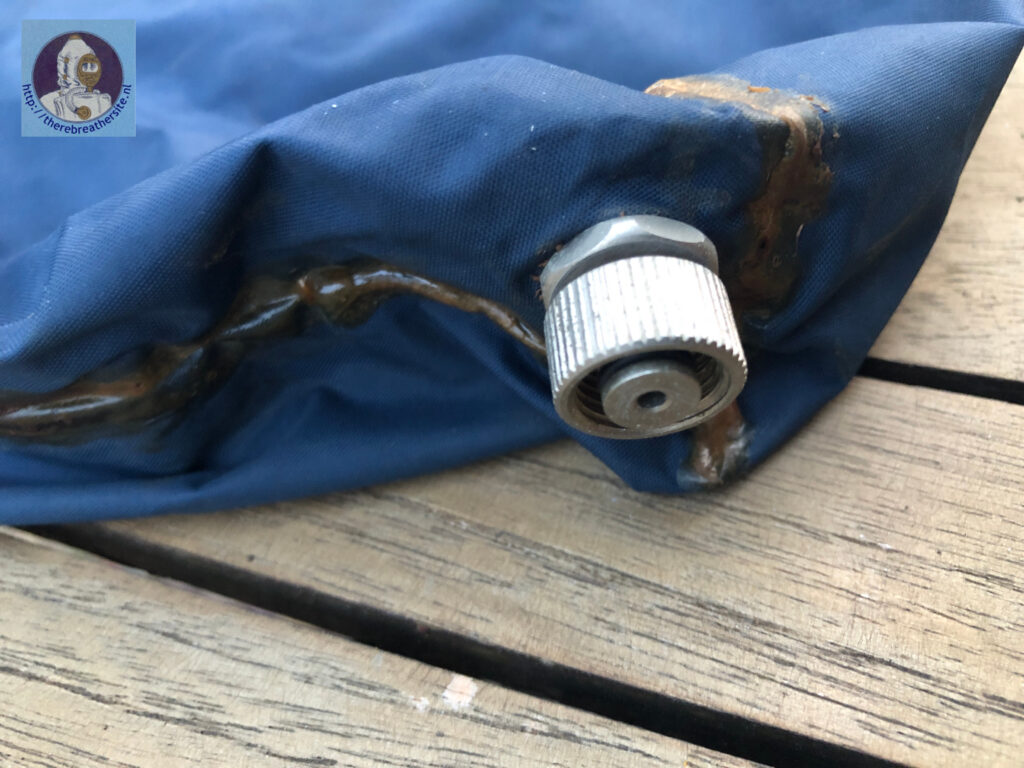
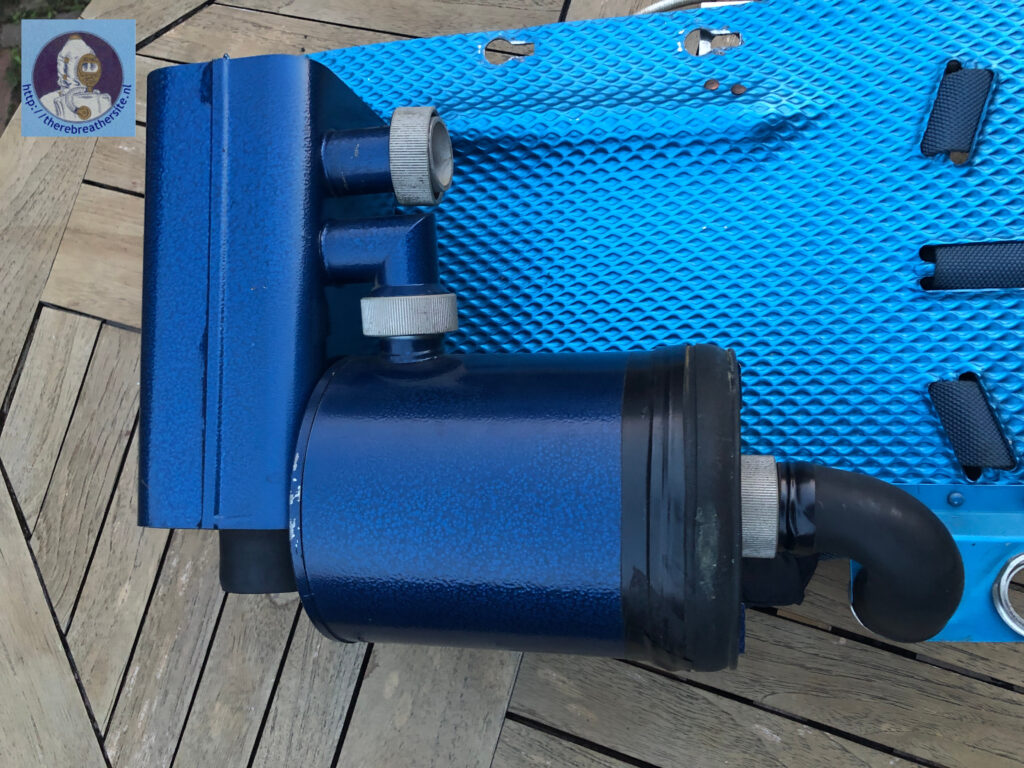
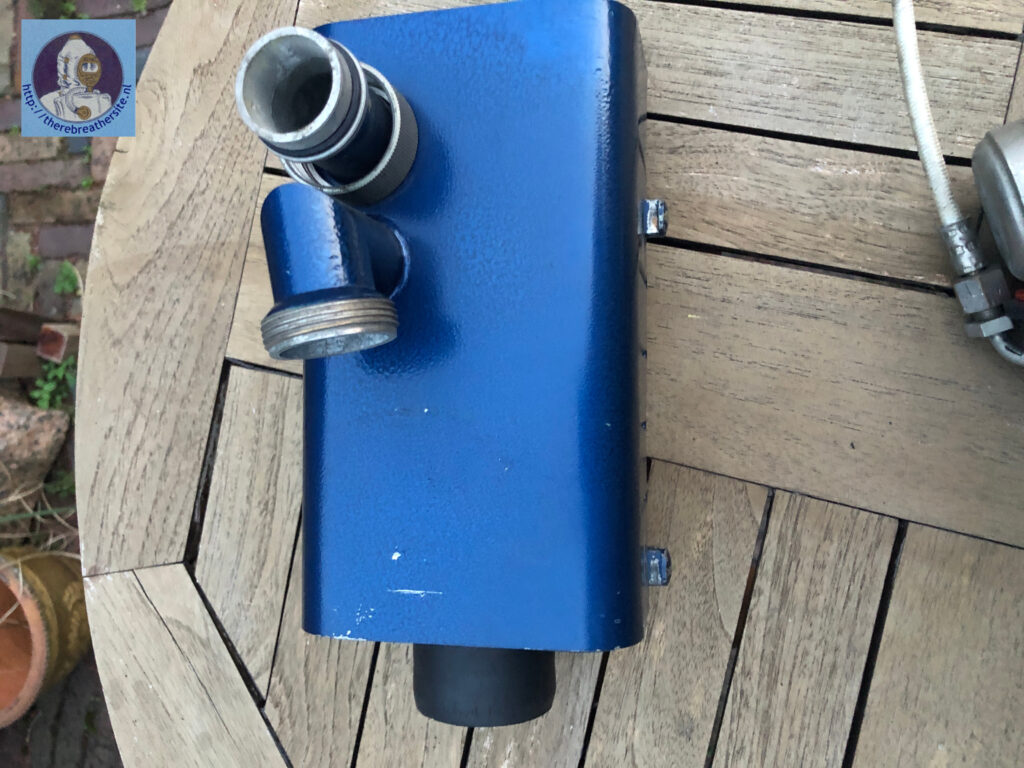
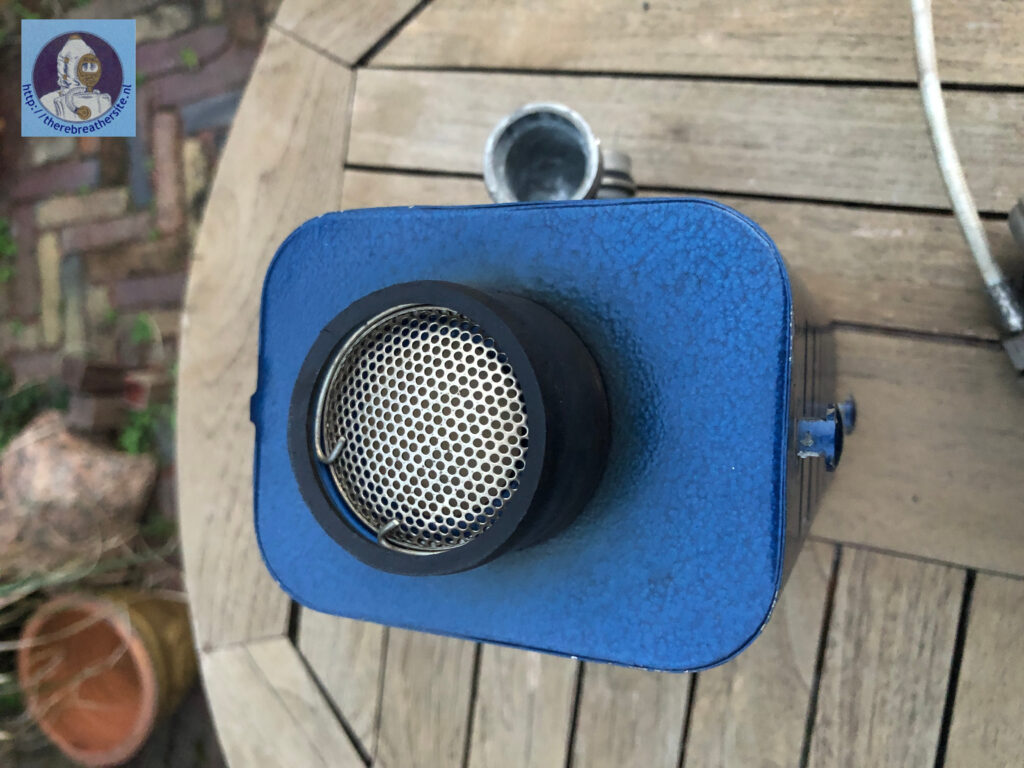
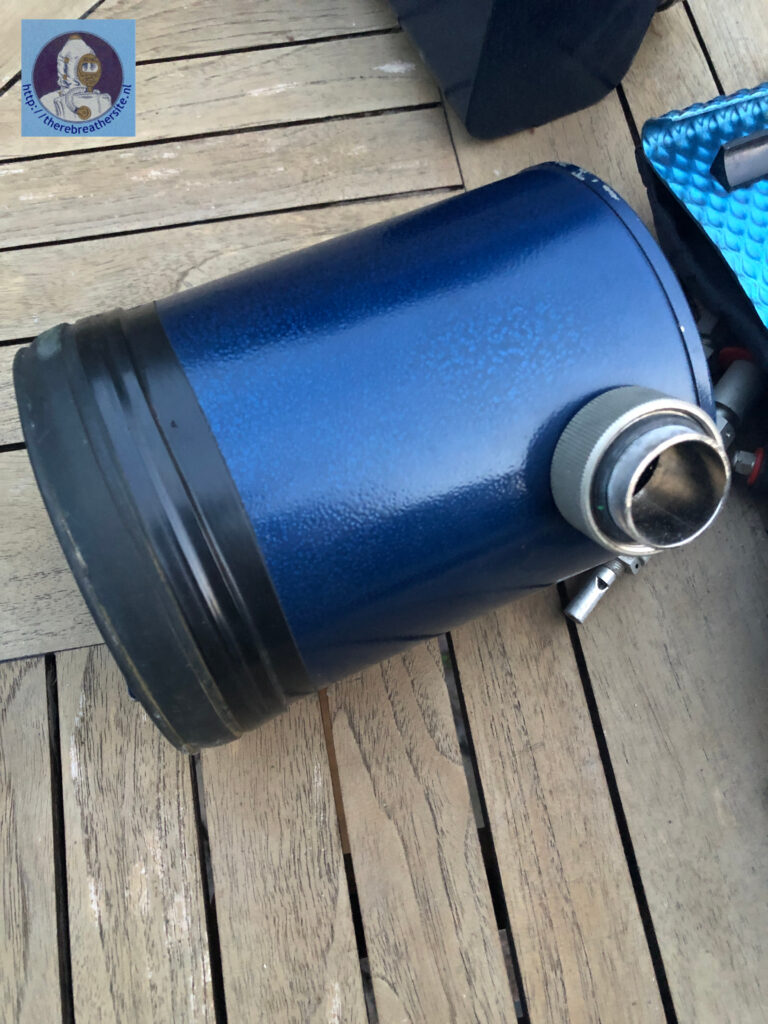
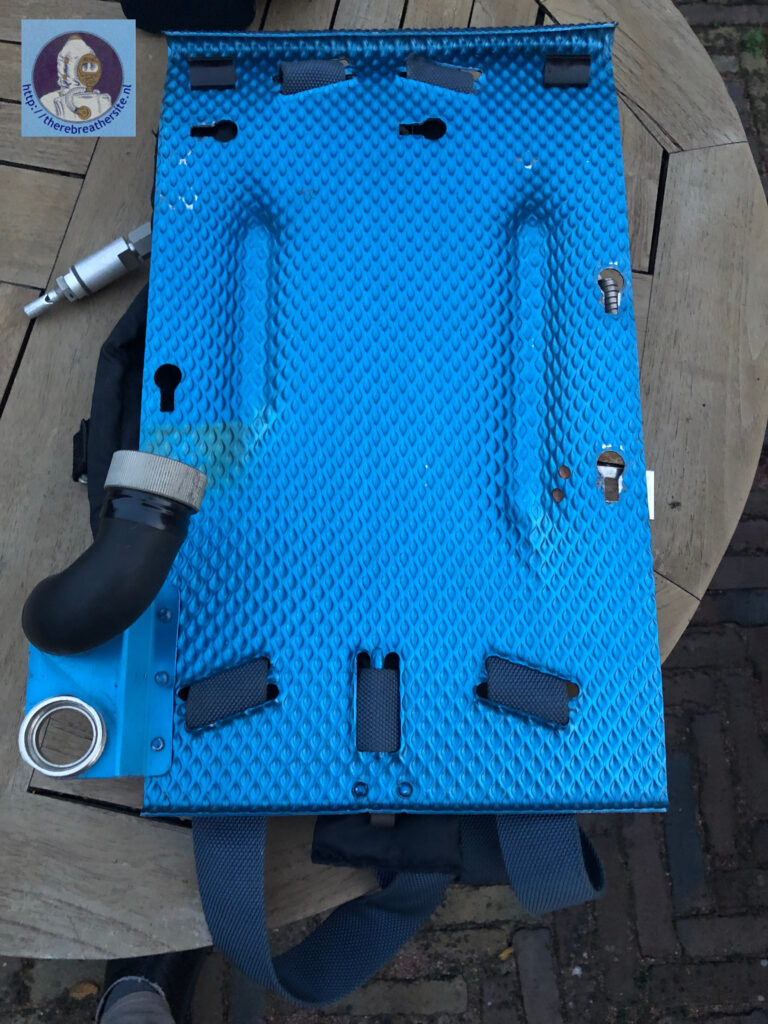
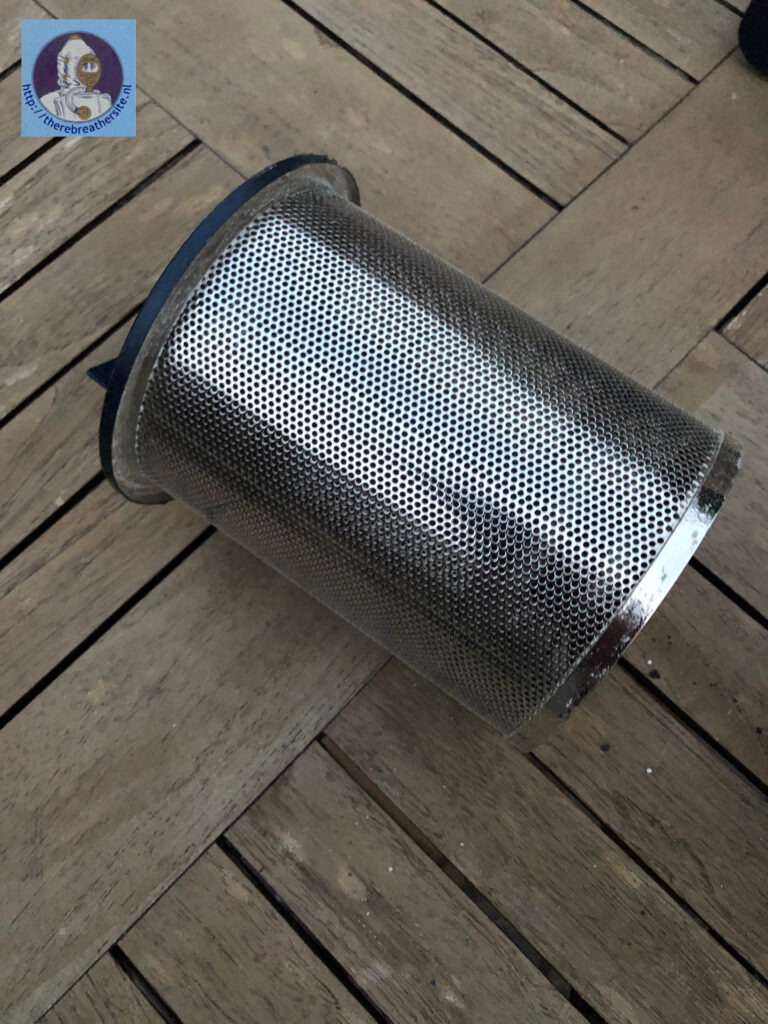
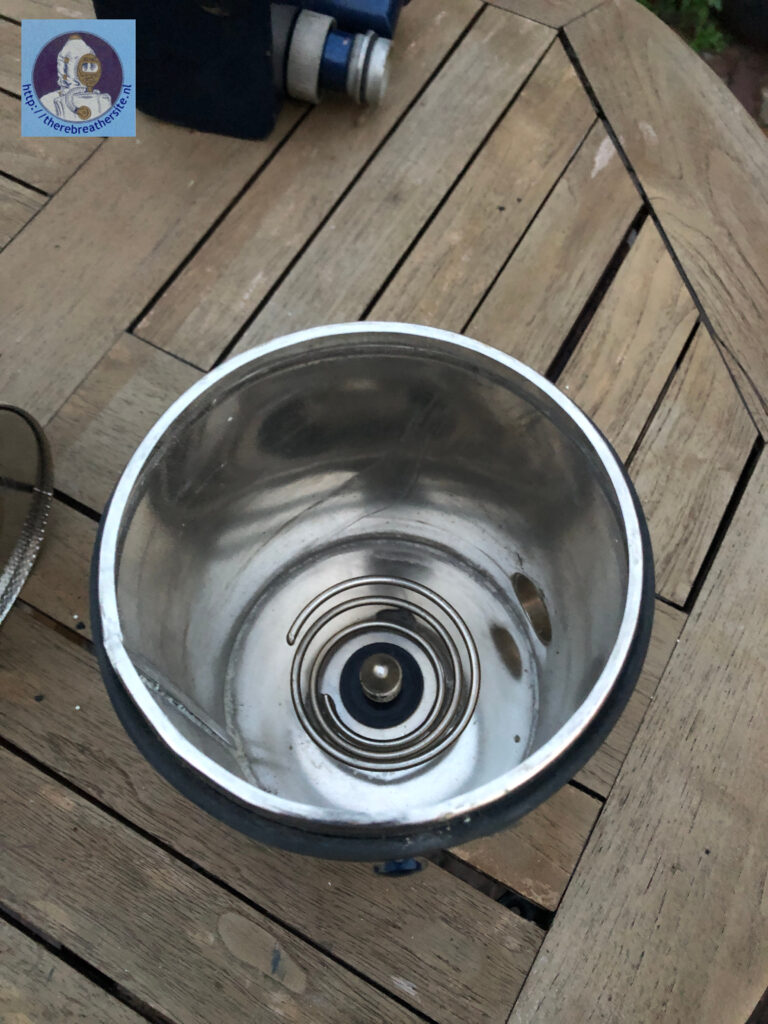
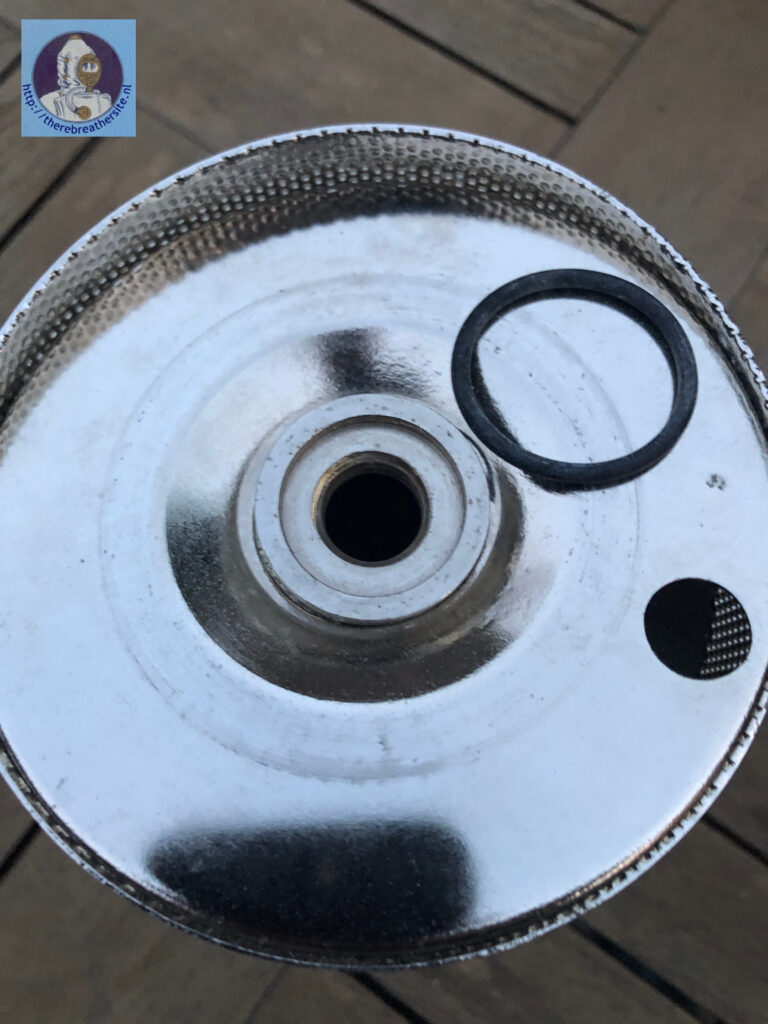
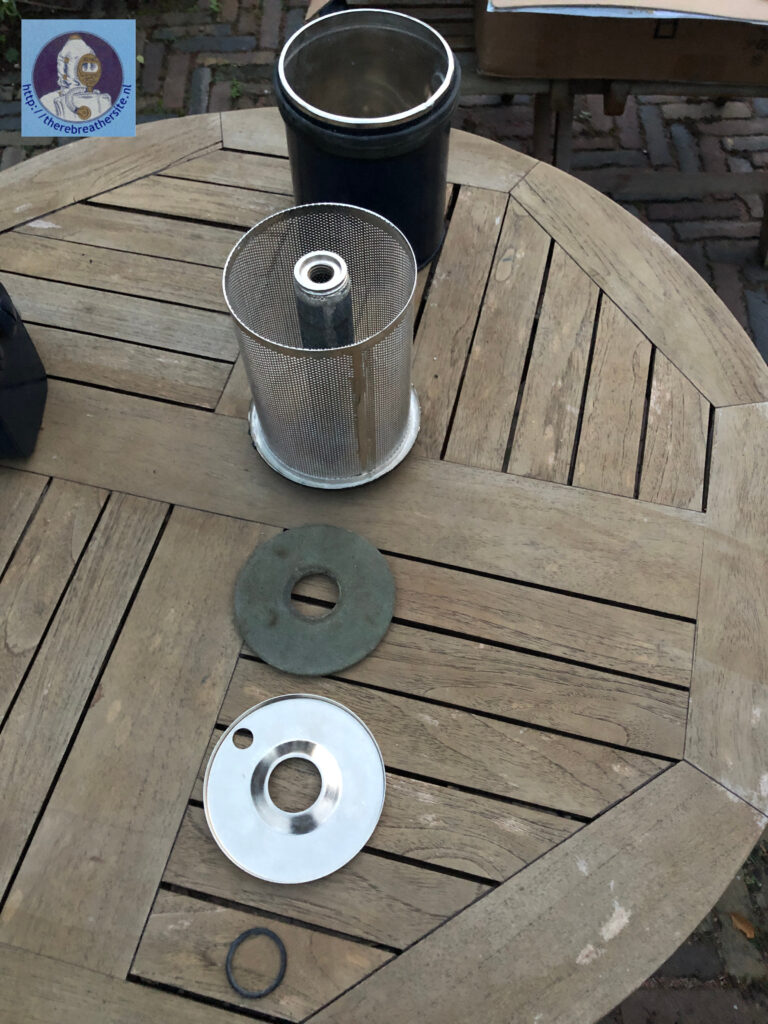
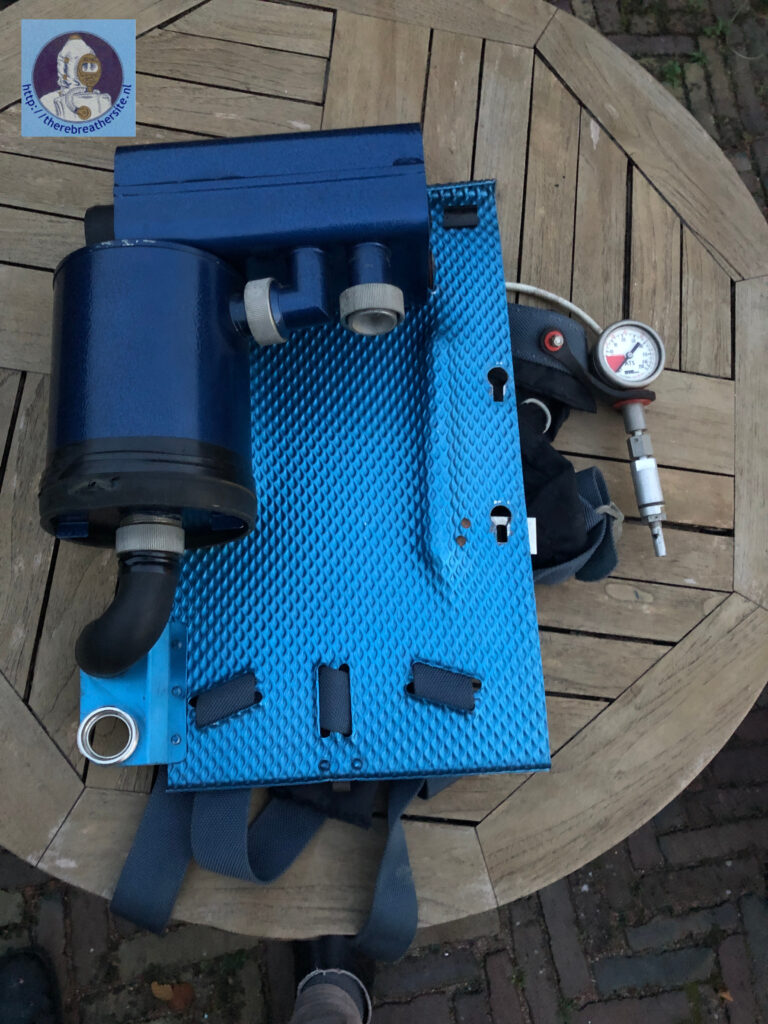
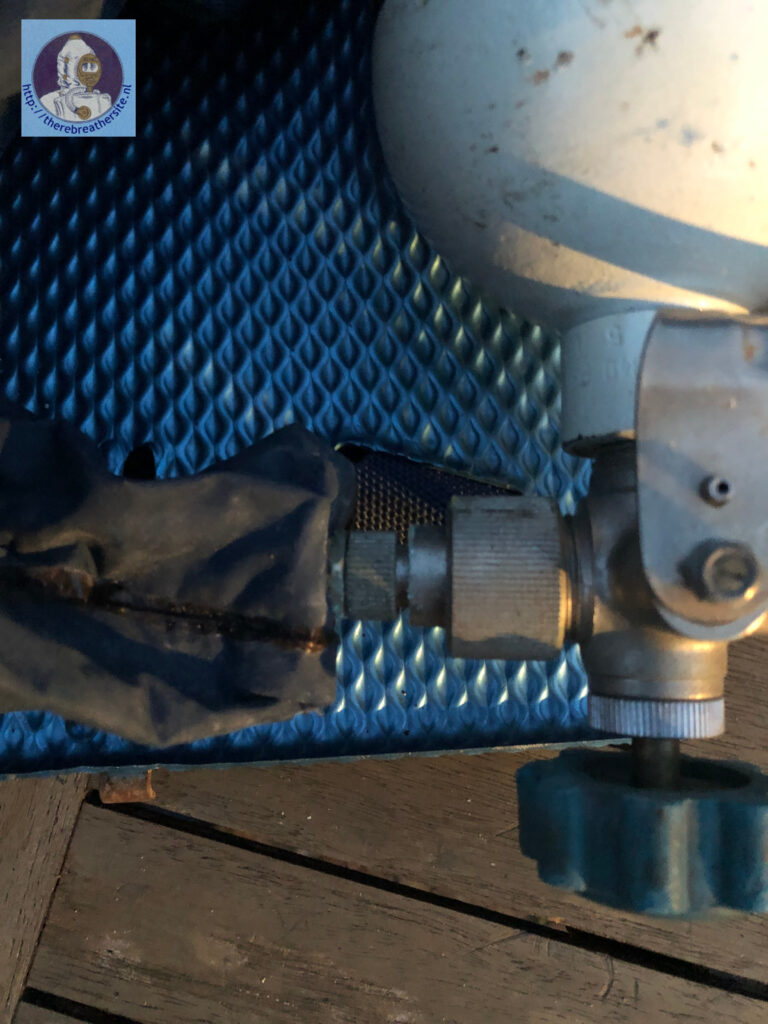
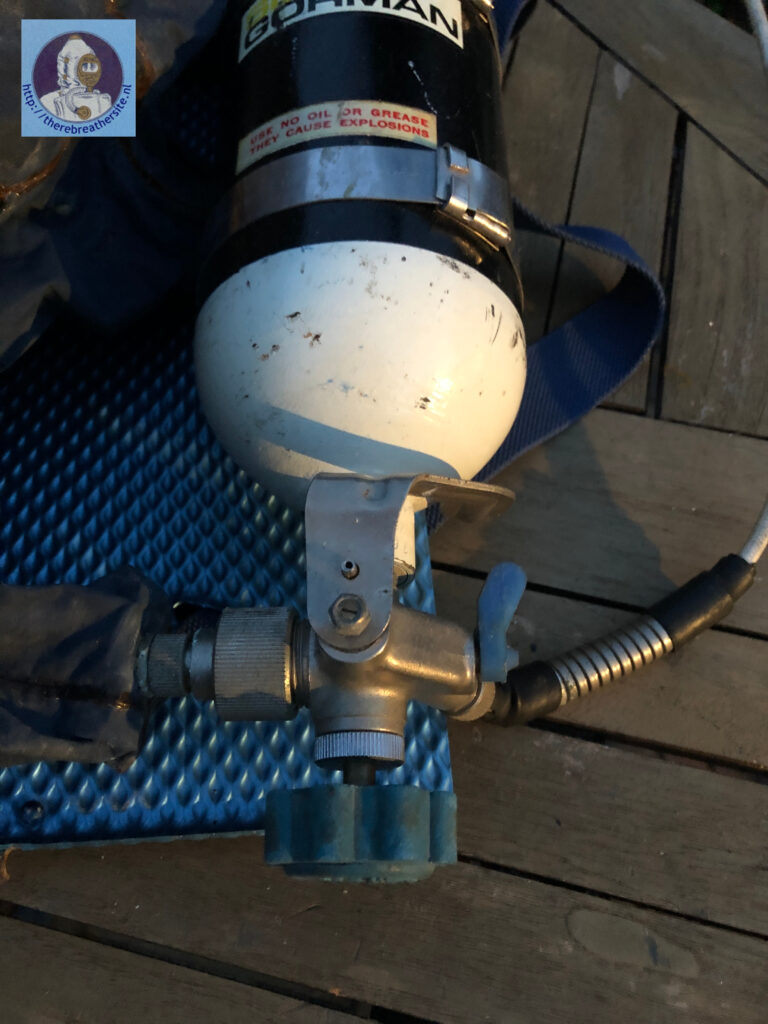
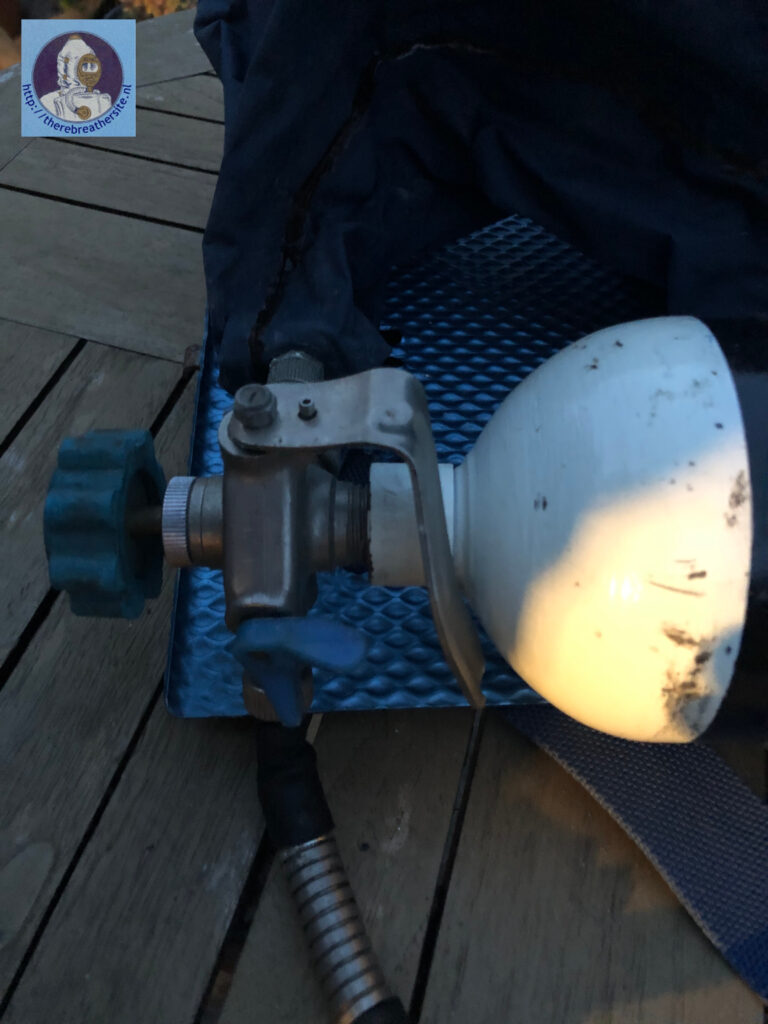
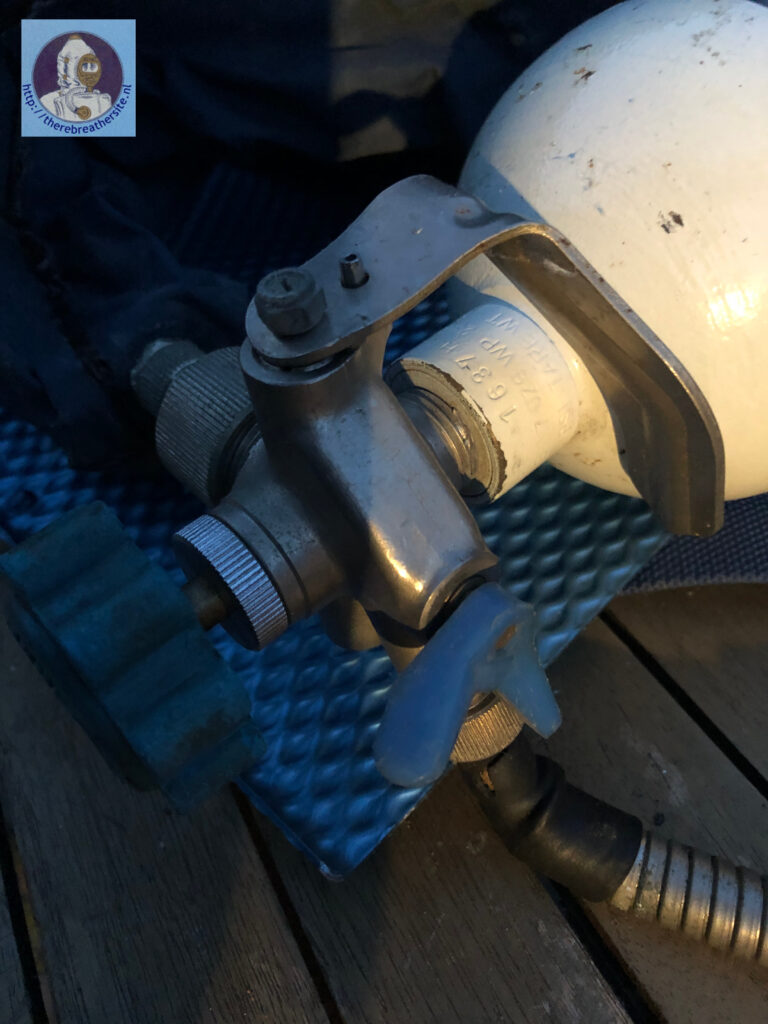
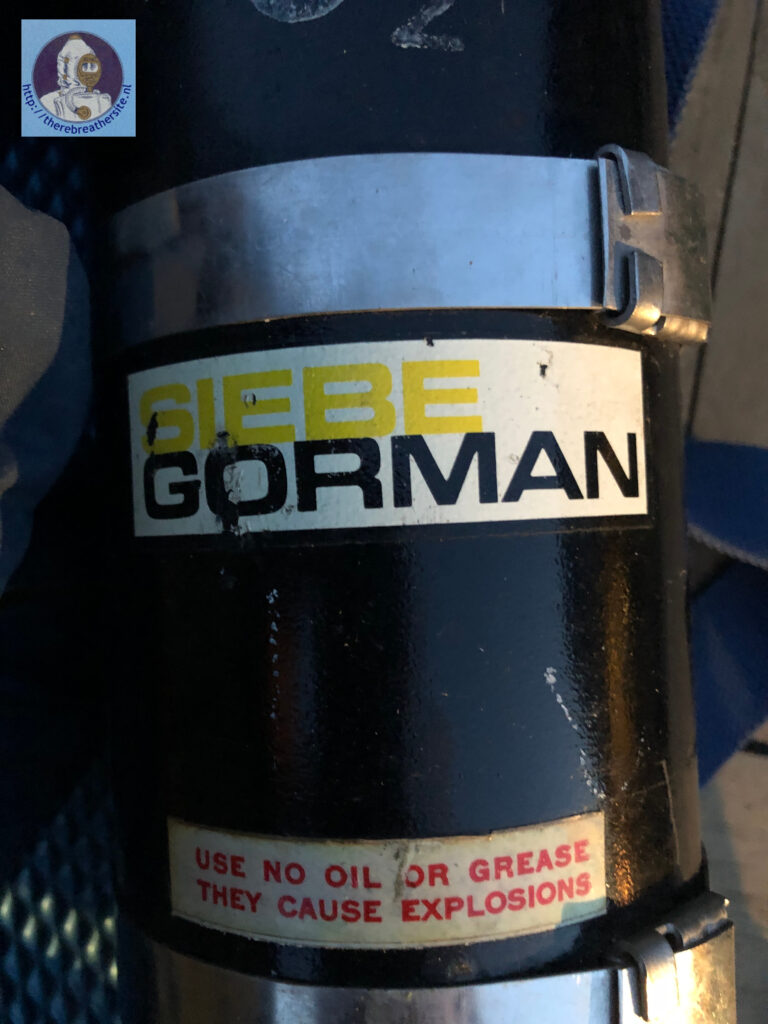
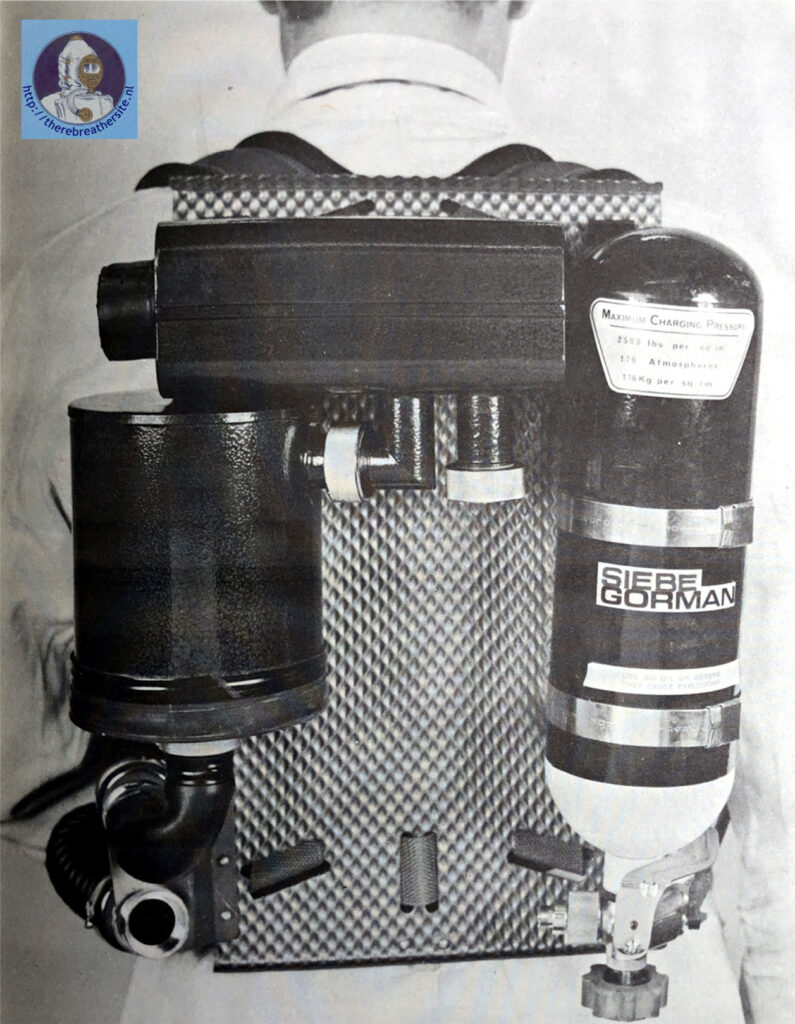
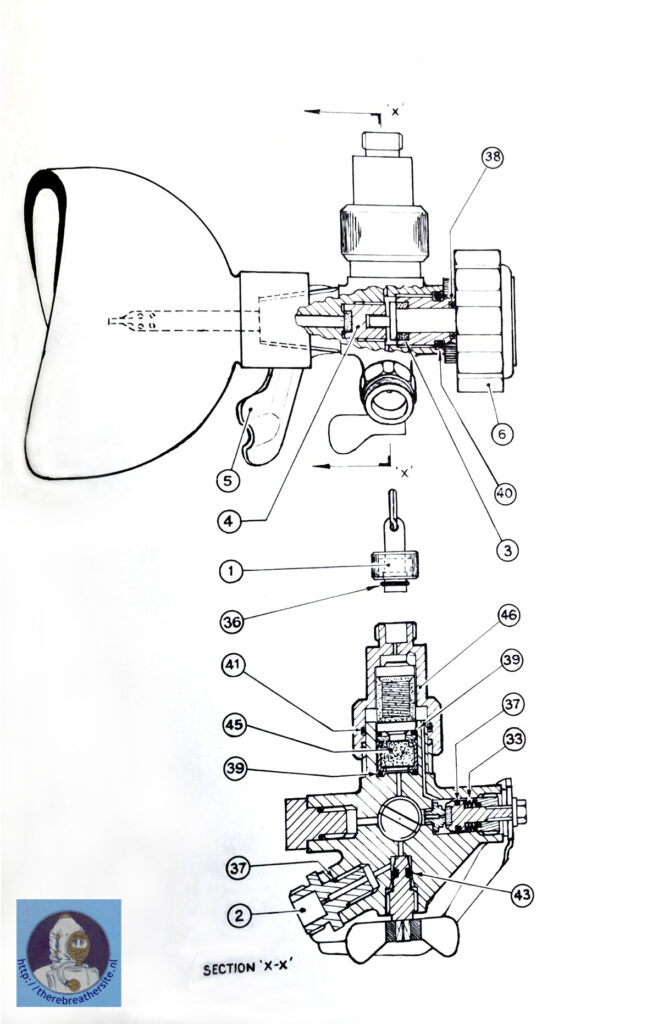
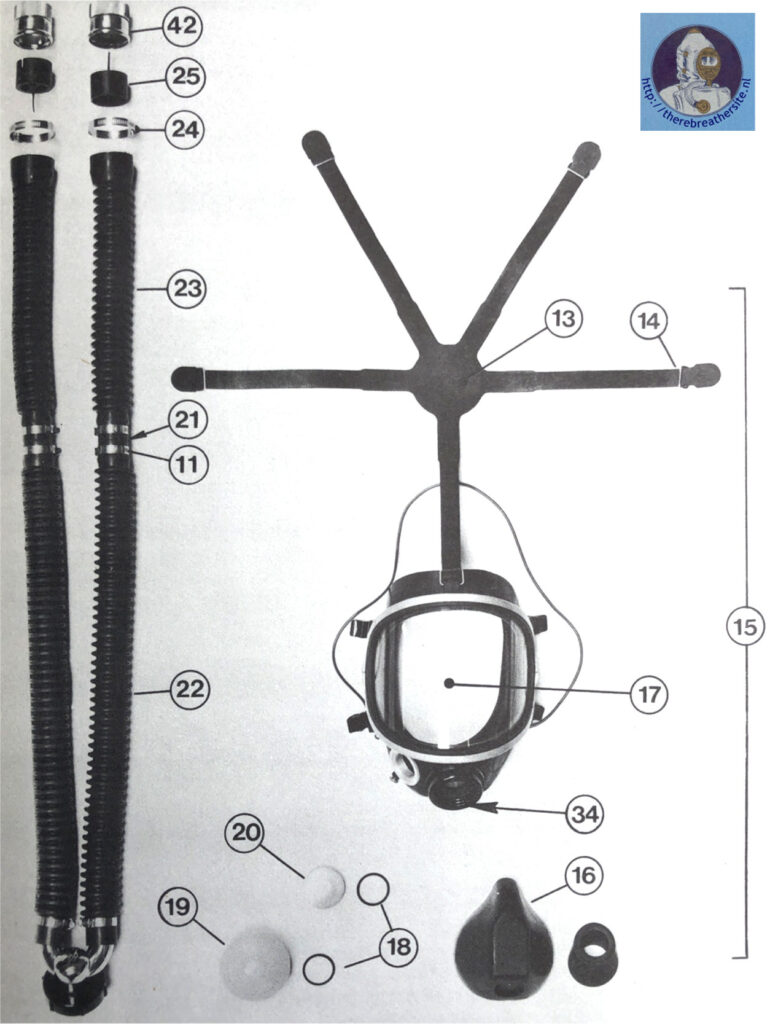
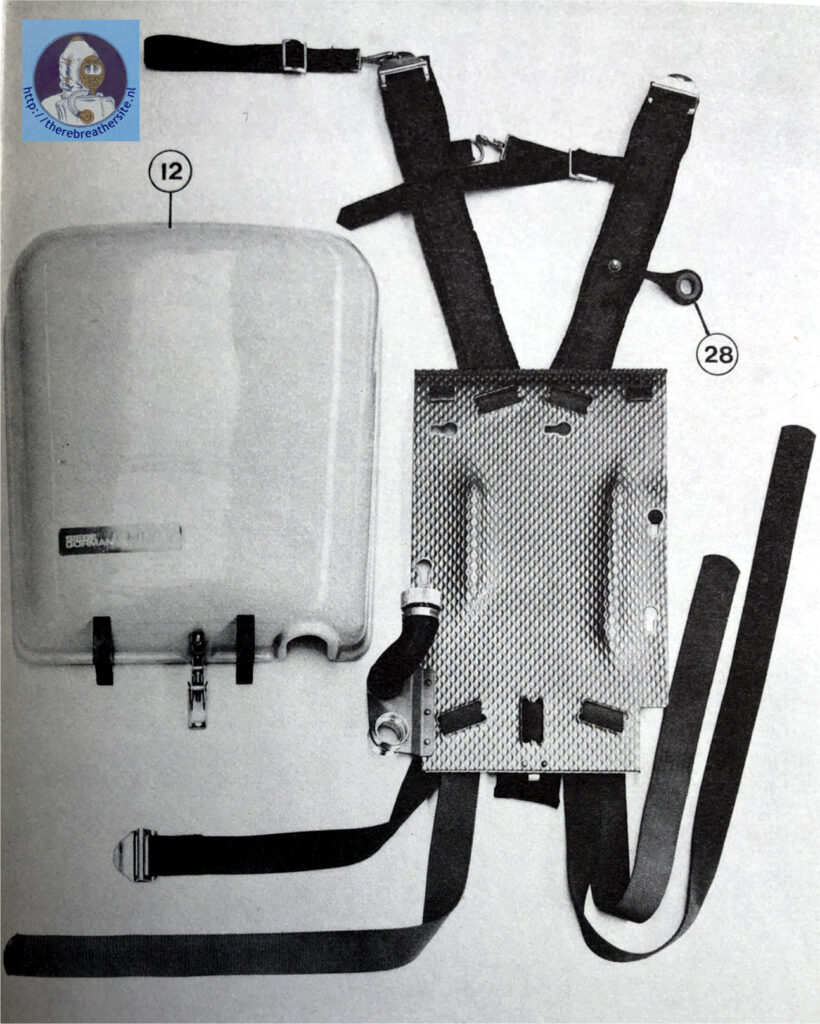
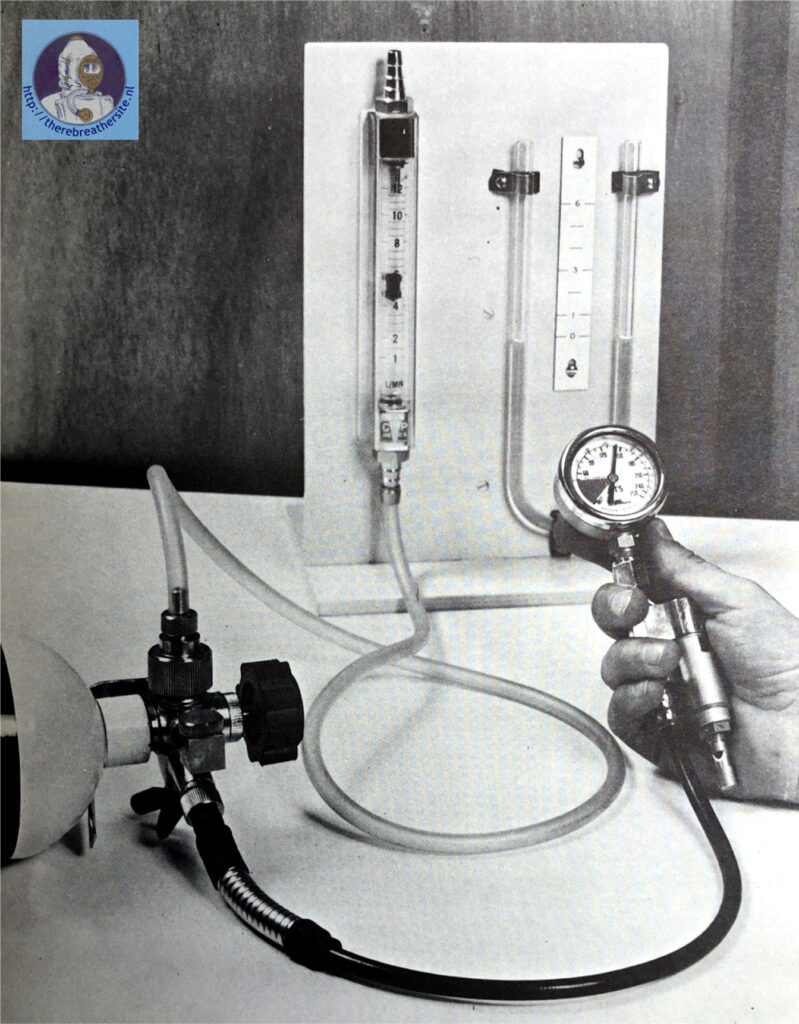
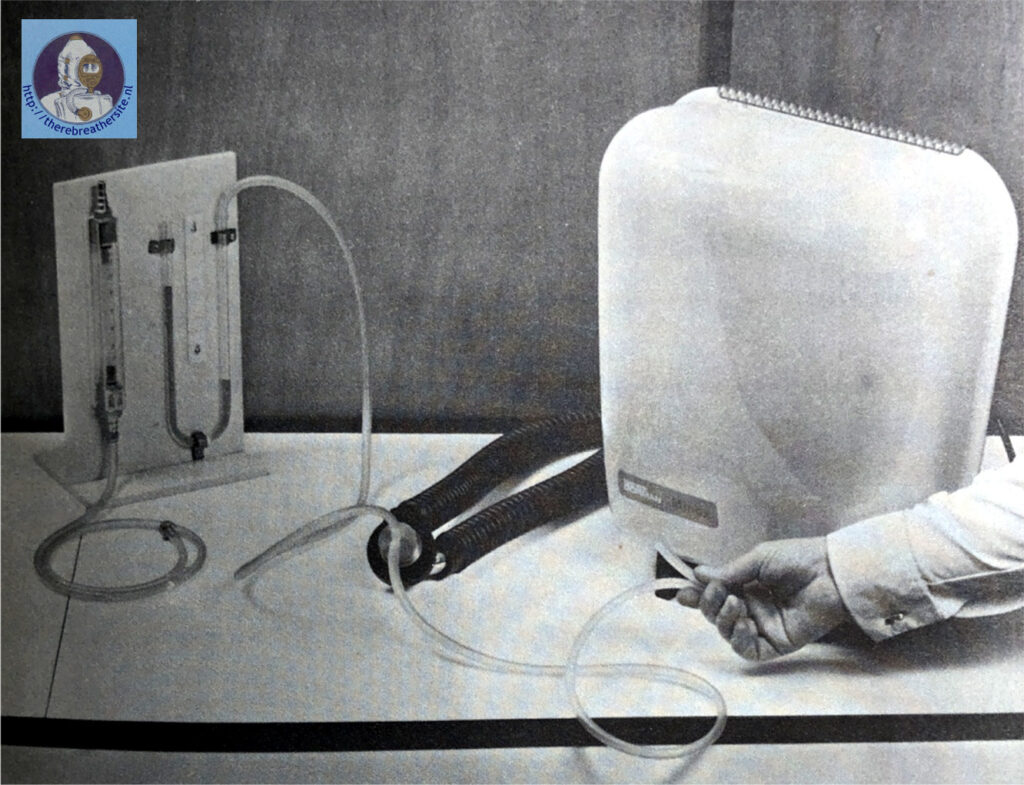
A special thanks to Brian Robinson for his fantastic contributions to this document! Rescue1UK

Therebreathersite was founded by Jan Willem Bech in 1999. After a diving career of many years, he decided to start technical diving in 1999. He immediately noticed that at that time there was almost no website that contained the history of closed breathing systems. The start for the website led to a huge collection that offered about 1,300 pages of information until 2019. In 2019, a fresh start was made with the website now freely available online for everyone. Therebreathersite is a source of information for divers, researchers, technicians and students. I hope you enjoy browsing the content!