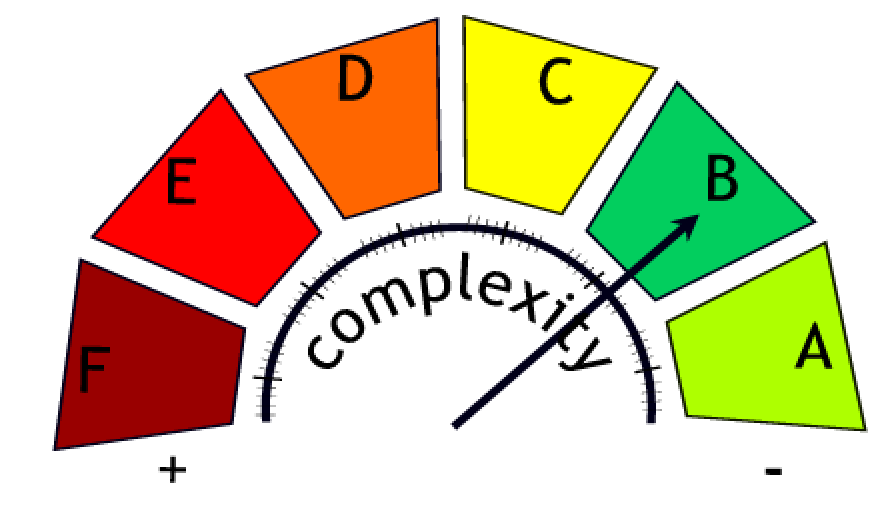
What material is used and how are they made?
There is a huge amount to be said about diving cylinders. On this page, I will discuss the various production methods and types of material used for diving cylinders.There are an endless number of pages on the internet with specifications and sizes. Nevertheless, with this page I hope to provide technical divers with interesting information that can be useful for diving. First of all, a brief review of the past of pressure cylinders. The current diving cylinder with a pressure of up to 300 bar was not created overnight. The first cylinders were made of alloy copper and not much later in steel. One of the first applications of overpressure from a barrel was by Frenchman Fréminet in 1784. He used a pressure vessel with a bellows in it. He called his invention ‘La Machine Hydrostatergatique‘
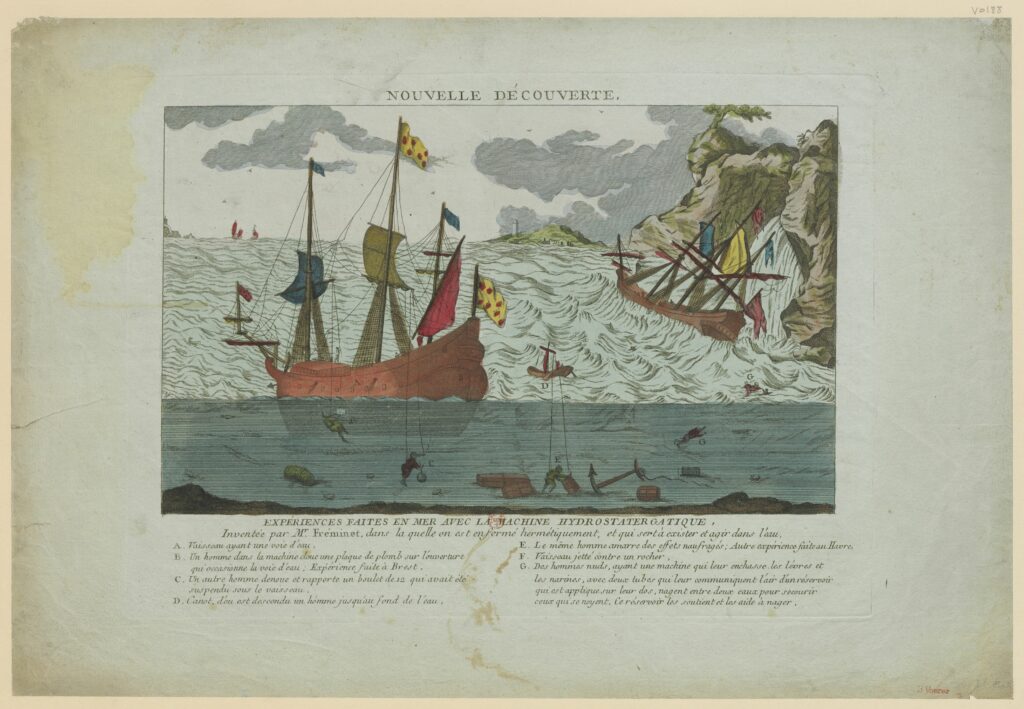
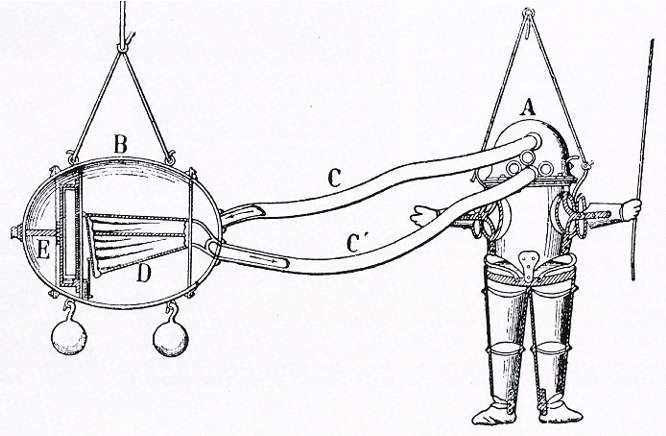
Until 1897, there were not many developments that enabled an underwater pressure vessel. A rebreather called Shamrock was developed in Germany, one of the first known models to use a pressure vessel. The very first cylinders could hold 60 ata of pressure. The Shamrock had a new type cylinder with 120 bar! Cylinders were made almost exclusively of steel.
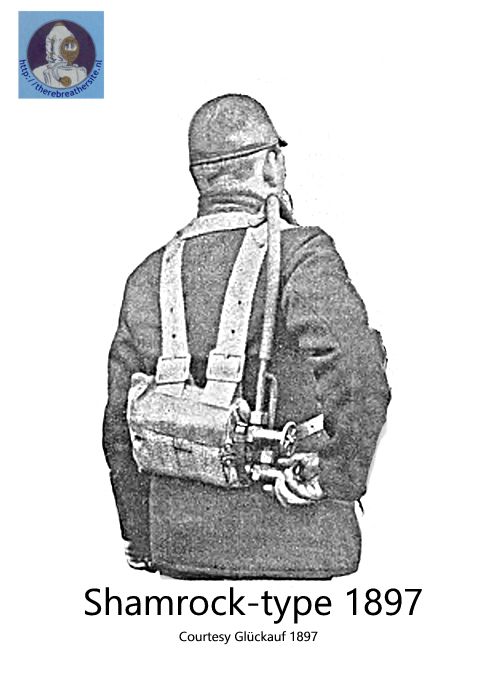
During World War I, pressure cylinders came increasingly into use. Unfortunately, often for evil purposes such as storing battle gases. Chlorine gas and mustard gas were the gases that inflicted terrible injuries. Oddly enough, this did lead to the further development of cylinders with higher pressures. In WWI, 120 bar was the standard.
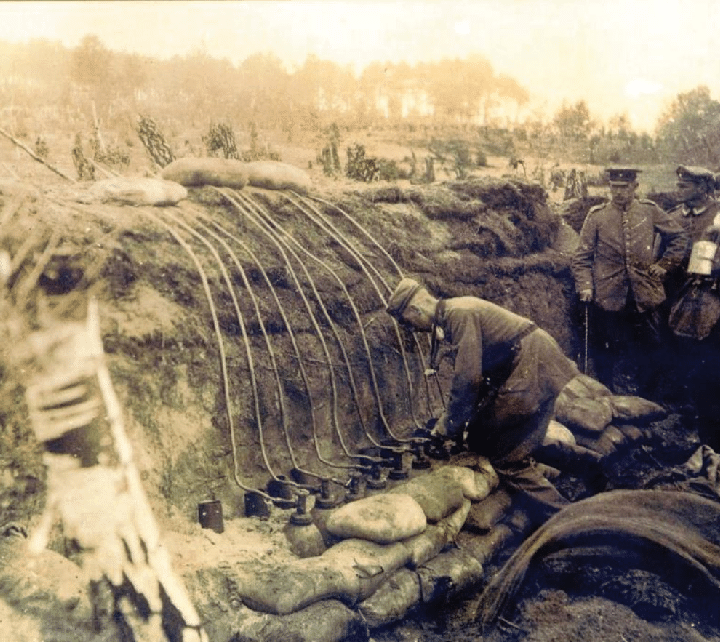
Between WWI and WWII, pressure vessels evolved in terms of construction and materials. One particular step was that the German Luftwaffe made Aluminium gas cylinders for its pilots. The British captured these from downed aircraft and used the cylinders for their charioteers, divers on minion submarines that attacked underwater ships with rebreathers. Unique was the high pressure these cylinders could hold. As early as 1943, cylinders were found from the Luftwaffe that could hold 225 ata of oxygen!
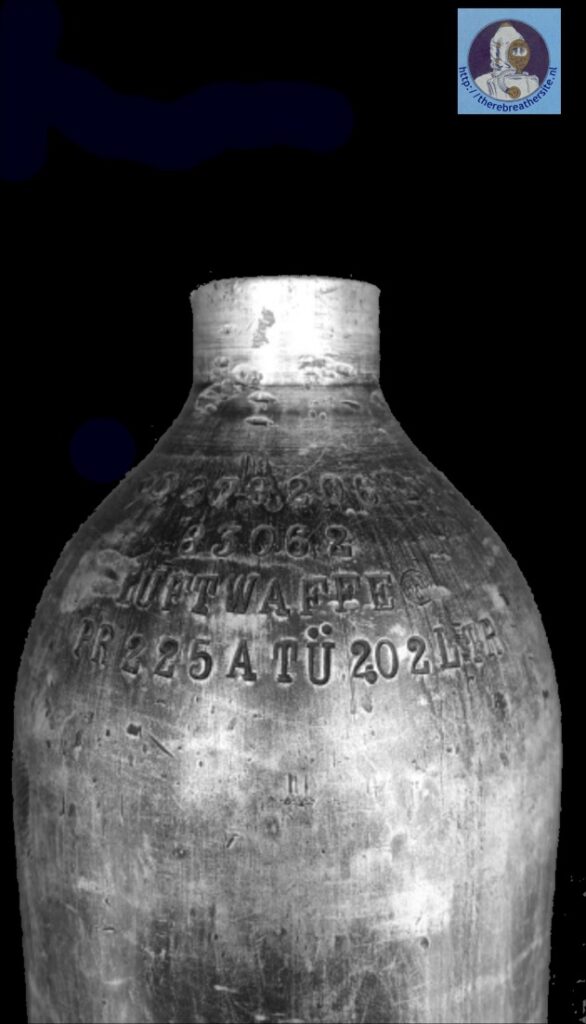
Around this time, 150-bar and 200-bar systems were on the market. Shortly after WWII, diving pioneer Ted Eldred was active in Australia with his Porpoise sport diving rebreather and the first cylinders for sport divers became available in America.
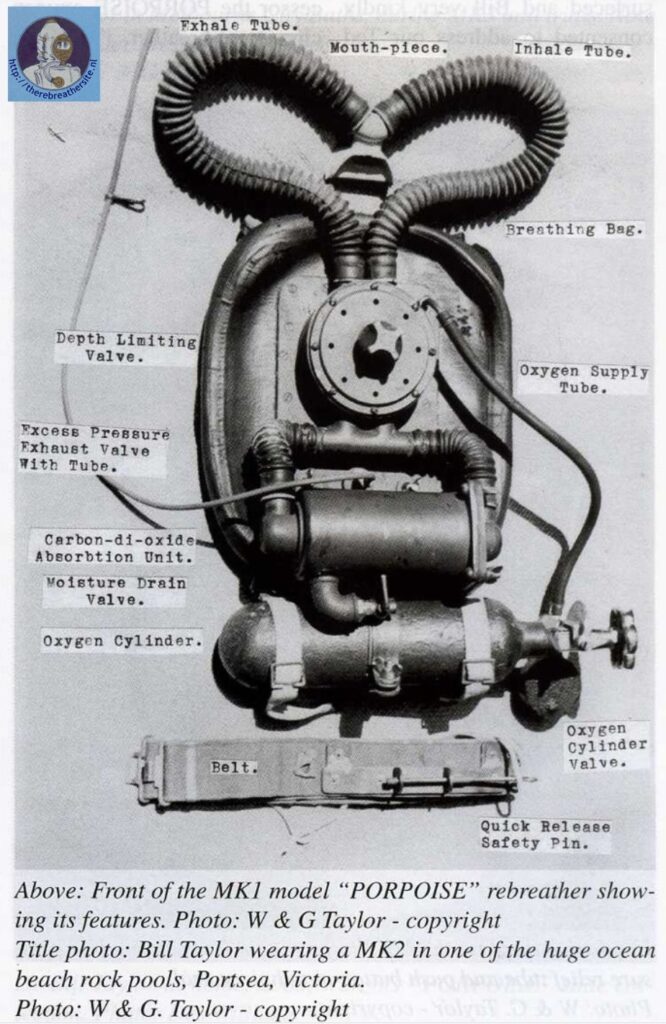
After this, developments were rapid and diving clubs were established all over the world and a market took off that led to new factories and manufacturers of diving equipment worldwide including cylinders for sport diving.
In the mid-1950s, PST and another company started making aluminium cylinders of 6061 alloy for the US Navy. The manufacturing process was very different from the way aluminium cylinders are made today. These round-bottomed aluminium cylinders are illegal for most purposes in the US because they do not have a DOT designation.US manufacturers of steel diving cylinders included Pressed Steel Tank Co. (PST), Norris Industries and Walter Kidde Co. Italian firm Faber makes US Department of Transportation (DOT) approved cylinders that were sold under various private labels. Faber cylinders are now distributed by Blue Steel Company. In the early 1990s, Heiser manufactured steel cylinders under the Beauchat brand name for sale in the US. Due to their excessive weight, these cylinders were not popular. In 2004, Worthington, a Canadian company began distributing its steel cylinders under different brand names.
The newly formed Luxfer USA, Ltd. , with special DOT licence SP6498, began producing aluminium cylinders in late 1971. By using a 6351 alloy in a cold extrusion process, the cylinder did not need a bottom plug like the earlier military type. The Luxfer-approved cylinder had a flat bottom like all aluminium diving cylinders made today. To be equivalent to the steel cylinders popular at the time, Luxfer made its cylinder 6.8 inches in diameter to fit into existing non-adjustable backpacks, and with a similar working pressure of 2,475 psig. To achieve the 72-cubic-foot capacity, the Luxfer cylinder was made longer, but as a result, it stayed afloat at about 11 pounds when nearly empty. Divers soon dubbed it the “float”.
In 1987 and 1988, the phenomenon of SLC (Sustained-load cracking) became known and cylinders of type 6351 were subjected to additional testing and later switched to another aluminium alloy of type 6061.
Having arrived here, we have taken a short journey through the history of the creation the of the diving cylinder. Let’s look further into the material types that are common today and what their specific properties are for use in and with rebreathers.
Diving cylinders must be made of a particularly strong material. The pressure in a filled cylinder is very high and the force pressing on the wall of the bottle is immense! Taking a 10-litre cylinder filled to 200 bar as an example, the total force exerted on the inside of the cylinder will be calculated as follows: Height of the cylinder internally 545 mm, cross-section 170mm internally, surface area 3365 cm2 x the force exerted by the pressure is 200 bar = 200 kg/cm2. This results in a force of 673 tonnes! Would the valve of the bottle be cut off, the bottle could rise 200 metres high and end up 400 metres away. Realise this when dealing with bottles! Bottles can fail in several ways. The bottle can fail mechanically, in which the wall will rupture and all the gas will be released with explosive force. Another way of failure is if the valve of the bottle snaps. The gas will then escape from the cylinder with great force, turning the cylinder into a rocket. The last form that mainly occurs with oxygen-filled cylinders is failure due to heating. An oxygen fire can greatly affect the mechanical strength of the cylinder, causing the wall to fail. If the cylinder is also under pressure, it is a hybrid explosion. This explosion has a combination of overpressure and explosive combustion. An example of how this effect manifests itself in film of all three types is given below.

Diving cylinders are mainly manufactured from 4 material types:
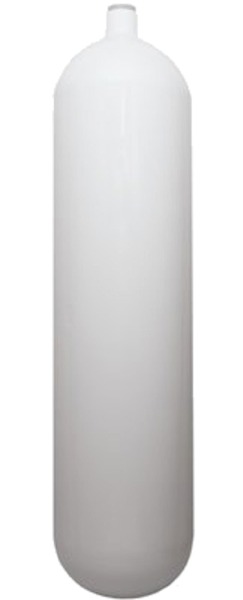
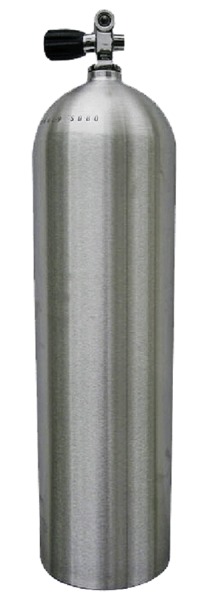
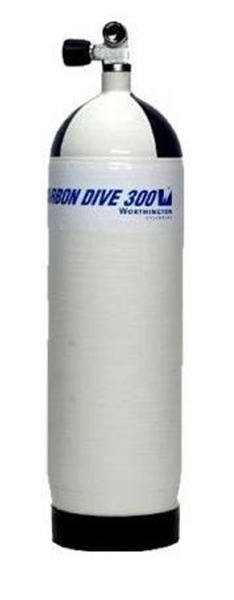
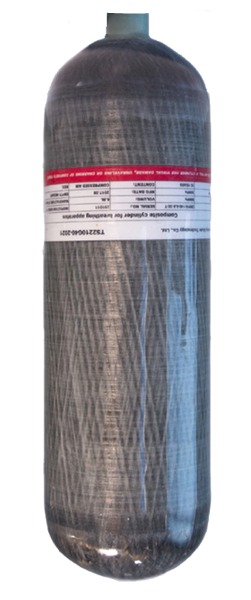
Steel
Aluminum
Carbon whoop_wrapped
Composite
In the videos below, you can see how a steel an aluminium and a composite cylinder are produced.
Mannesmann 10 l | Luxfer Alu 10 ltr | ||
Steel (DIN 3171) | Aluminium (DIN 3172) | Difference | |
Height | 545mm | 655mm | Alu +110mm |
Diameter | 178mm | 176mm | |
Weight | 10,8 kg | 12,5 kg | Alu +1,9 kg |
Volume | 11,4 l | 14,6 l | |
Pos. weight in water | 0,6 kg | 2,1 kg | Alu +1,5 kg |
Wall thickness | 4 mm | 12,5 mm | |
Strength | 900 N/mm2 | 275 N/mm2 | |
Dangers | corrosion | Corrosion/heat/oxidation |
Van der Waals formula, also known as the van der Waals equation of state, is a mathematical model used to describe the behavior of gases and liquids at various temperatures and pressures. It was developed by Dutch scientist Johannes Diderik van der Waals in the late 19th century as an improvement on the ideal gas law, which was unable to accurately describe the behavior of real gases.
The van der Waals formula takes into account the non-ideal behavior of gases and liquids, which arises due to the fact that molecules in these substances have a finite size and interact with each other through attractive and repulsive forces. The van der Waals formula is written as:
P = (R*T)/(V-b) – a/(V^2)
where:
- P is the pressure of the gas or liquid
- T is the temperature of the gas or liquid
- V is the volume of the gas or liquid
- R is the universal gas constant
- a and b are constants that depend on the specific gas or liquid being described
The first term on the right side of the equation, (R*T)/(V-b), is similar to the ideal gas law and represents the pressure exerted by a gas in the absence of attractive forces between molecules. The second term, -a/(V^2), represents the pressure decrease due to attractive forces between molecules and is known as the van der Waals correction term.
The van der Waals formula is useful for predicting the behavior of gases and liquids under a wide range of conditions and is often used in engineering and other fields where the properties of gases and liquids need to be understood.
However, due to the van der Waals curve, a corrector factor will have to be applied which at pressures of 300 bar will result in a 10% volume difference!
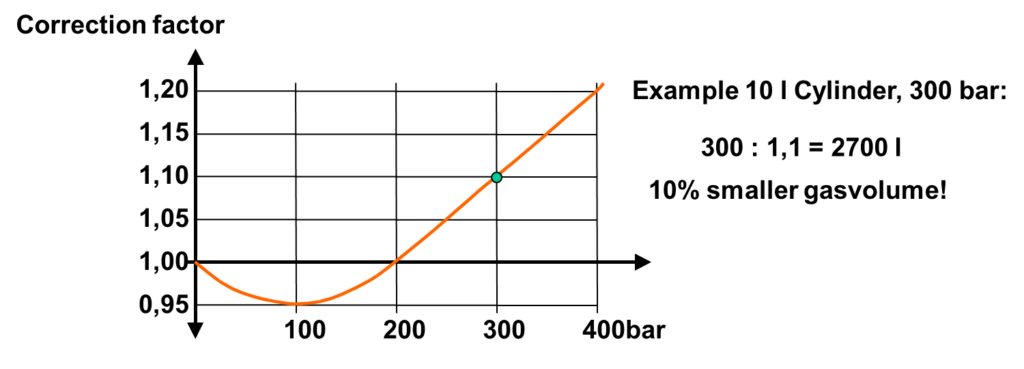

Therebreathersite was founded by Jan Willem Bech in 1999. After a diving career of many years, he decided to start technical diving in 1999. He immediately noticed that at that time there was almost no website that contained the history of closed breathing systems. The start for the website led to a huge collection that offered about 1,300 pages of information until 2019. In 2019, a fresh start was made with the website now freely available online for everyone. Therebreathersite is a source of information for divers, researchers, technicians and students. I hope you enjoy browsing the content!