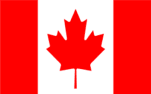
Hydrospace MARK IX semiclosed rebreather system 1966
This graphically heavy page is about the development of Hydrospace developments’ Mark IX diving system. A most extraordinary story about a genius inventor who suffered considerable setbacks in his life. The story was written in 1987 by Steve Morris. Unfortunately, I did not manage to get in touch with either Mr Wright or Steve. The website included a statement that the story could be passed on for non-commercial purposes which I am happy to do here. The very special man Michael William Wright became famous for his audio equipment. Before that, however, he made an extraordinary contribution to the diving world in the form of a semi-closed diving system using exceptional materials for the time.
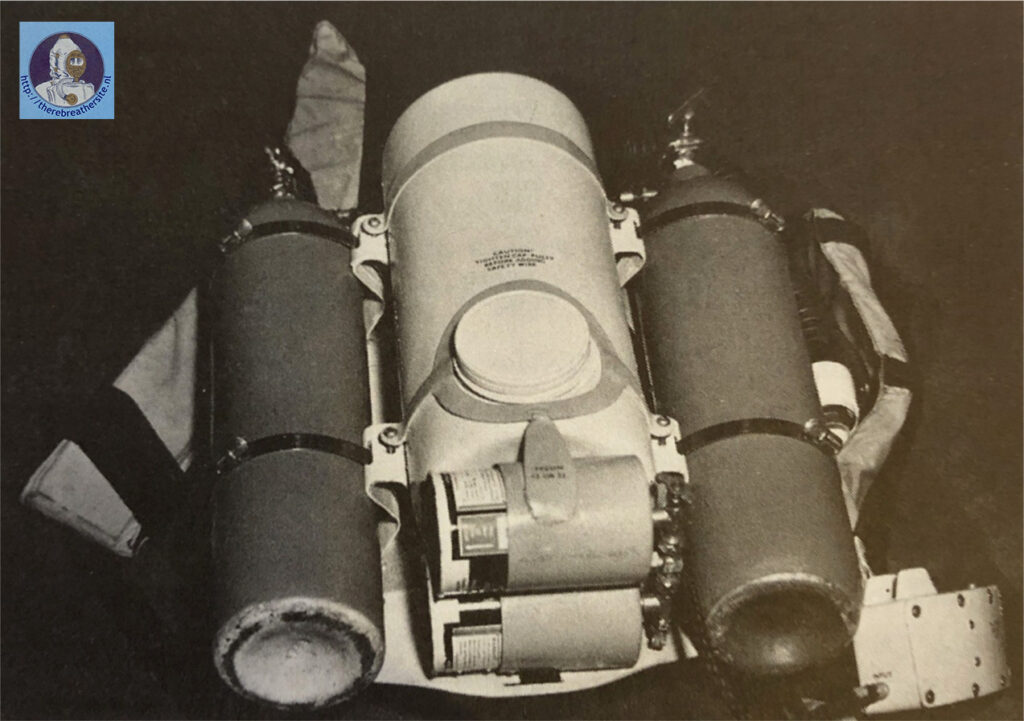
MICHAEL WILLIAM WRIGHT
The father of the famous Canadian audio brand Dayton Wright (1970-1985)
Scientific researcher, theorist, prolific inventor, businessman, expert programmer, popularizer, pilot, diver, humorist, painter, novelist and more. The basics of Hydrospace develpments LTD began in Winnipeg, Manitoba, then onto Minaki Ontario, in 1956
Curiculum extra ordinaire:
- Built his first electrostatic speaker and amplifier at age 15
- Studied electrical engineering at MIT
- Works with the pioneers of high fidelity who founded Bose, Fried, KLH. Trains two young people who will become the founders of Classé Audio (David Reich) and Krell (Dan Dagostino)
- Theorizes a holographic model of the human brain
- Invents a revolutionary electrostatic speaker that at its peak was sold in 50 stores in America and 16 other countries. More than 2,500 units sold despite a very high price
- Invented several dynamic multi-channel speakers approaching electrostatics (Watson Lab)
- First transistor voice coil preamplifier
- Invented 6 preamplifiers with performances never seen before in laboratories
- Great diver, invented a cold water diving system for the Canadian Navy
- Invented a muscle electrostimulation system for rehabilitation
- Invented an electrical contact treatment between two metals, the Stabilant, used today by Airbus, Bell Helicopter and several automobile manufacturers.
- Develops a measurement framework for loudspeakers based on a new concept: periodicity
- Flies his little Cessna to Las Vegas for audio shows
- Studied the music listening process under laboratory conditions
- Studied the stress of supersonic wings
- Painted, drew cartoons, and wrote a novel for fun
tekstsource: https://lemayaudio.com/dayton-wright-hommage-project.html
Here is my story,
It began at MIT, when I needed transportation at the end of the second year. Because I had written a term paper on the ‘Use of Holographic Sonar Signatures to mimic LaPlace Power Transforms to Classify Submarines’.
It was promptly classified by the Division of Industrial Co-operation – a quasi US government agency.
My mentor at MIT was Dr. Edgerton. He called me to his office and informed me that I should have entered the MIT cooperative course, where parts of the requirements were based on experience in the field . Then I could have applied for at least a Masters or a Doctorate in Engineering Physics.
I had said that they could use a diffraction grating for a source of coherent light, (remember that lasers hadn’t been invented when I wrote my paper).
Unfortunately my term paper was treated as bombshell and that’s the reason that it was classified!
When I left MIT, my Coop-Boxes (storage) in the lock-up compartments in the basement of ‘Runkle House’, an MIT dorm on East Campus, were opened and all of my papers and notes were taken. Over 85% if my textbooks were ‘stolen’. as the locks on the my two Coop-Boxes were broken.
I should explain that about a month before the end of term, a friend in the MIT Outing Cub drove me North of Cambridge, up to Peabody, where there was a used hearse dealer. He told me that he had a arrangement there to get these types of vehicles into other uses. Normally a repaint was normal so that it was not obvious what its previous use was. However, so long as the use was discreet a lot were disposed off, and generally regestered in other states.
(The Proprietor of the Funeral Home was in good health. At that time Japan had not attacked Pearl Harbour, so when the United States declared War, the Government decided as any ambulance might be needed, so that there were excellent reasons for the maintenance to continue.
There, I was able to purchase a LaSalle hearse, (as a Miller Convertible, it could be used either as a ambulance or a hearse). This was outfitted with a under-the-hood-siren and flashing red lights both at the front and the rear. It had been used for only a year in southern New Hampshire when the proprietor suffered a heart attack and died. The funeral parlour was sold and as the people already had the vehicles that were needed. It was well serviced, even to the oil being flushed twice a year.
When I bought it, the odometer mileage was about 16,000 Miles. I had a mechanic check it thoroughly and it needed only the flexible brake hoses and one new tire replaced. I found a dealer in Summerville who had a stock of new tires so I replaced all four tires. I applied for a License right away and was issued a temporary one pending certification from the mechanic that did the inspection. As there was four months remaining on the temporary license with the required insurance that so I could drive it immediately.
I had called Canadian Customs from Cambridge, Mass., and received a ruling (In my name and with a detailed description of the hearse), that I would have to quote to get through Canadian Customs (South of Winnipeg). I was informed that they would mail a copy of the ‘Letter of Permission’ to my MIT address as a matter of form. But as I might not be there to receive it in time for my departure, he would make sure that the customs office at Pembina would clear me. However if there was a problem the Customs Office in Winnipeg could be called to confirm it.
As I could leave Massachusetts right away, it would be out of Massachusetts within a month. I was able to drive it to Missouri where I had friends, then westward to Des Moines, Iowa then to south Dakota. When I attempted to get into Canada, the Customs Officer told me that I couldn’t bring it into Canada even though. Even with the ruling I was denied entry, as the Customs Officer wouldn’t check his records or even call Winnipeg.
Now stunned, I had to return to a motel in the US. It was in the evening, so I got a Motel Room. When I was stayed there, someone spotted the hearse in the parking lot. He asked me if I was interested in selling it. I agreed providing that he took the vehicle to a mechanic for a checkout. It was in excellent condition and we agreed on a price of $950 US providing he could arrange transportation up to Winnipeg.
He could transfer the title as soon as I signed the Bill of Sale. His bank was just down the street so he could pay me in cash. When he returned I signed the bill of sale. He said that he had telephoned the acquaintance he knew might be able to offer me a ride. He was driver of a three ton truck that had unloaded his fright, and was on his way to Portage LaPrairie, Manitoba and was willing to drop me off in Winnipeg.
I should explain that my mother was sharing an apartment with an old friend. She was surprised to see me. I had to tell her that I had to leave the US because of Dr. Edgerton’s advice.
There, I had seen the advertisement for a diving equipment supplier on Portage Avenue close to the Furby Movie Theater. I bought a green neoprene dry suit, a set of twin tanks and a regulator. As the Montreal company also sold three stage air compressors complete with carbon monoxide filters and oil separators this seemed a good investment. I had it shipped to Minaki on the CNR.
When I went to pick it up I noticed that the Regulator was labeled the ‘Gagnan patent’
(JWB: ‘process’). The neoprene diving suit neck seal was a chrome plated cycle wheel rim. This seemed a bit strange but it worked
At that time Cousteau wasn’t mentioned. Well, although it took over seven hours to fill the short tanks, I was able to inspect several concrete boathouses where the weight of the concrete wasn’t heavy enough to prevent their movement in high water conditions. Some of the boathouses were insured and the Pulp and Paper Mill in Kenora had to accept responsibility as the dam was operated for their benefit.
I began working for the General Construction Superintendent at Whitedog Falls, G. S. As I had experience in surveying in Minaki (My uncle was the surveyor for the port at Churchill Falls, Manitoba and now had been working for the CNR for many years). At MIT I has taken a side course on surveying, so I was co-oped to do some surveying work, fist as a ‘chainman), then as a interim surveyor in the winter months.
(To recap this, part of the cold water diving suit development began in 1956 when I was working for The Hydro Electric Power Commission of Ontario. I was initially hired as an assistant to the General Construction Superintendent. Well within a year I was now reclassified as ‘a field superintendent’)
This allowed me to use a mixed crew of carpenters, electricians, riggers, crane operators, truck drivers etc., to handle urgent jobs by bypassing the usual line-of-command. Providing that I didn’t step on any toes we were able to expedite many problems.
During my year I was assigned the task of sorting-out some steel building parts that were dropped off at the temporary CNR spur at Pistol Lake. There were tons of parts ranging from heavy beams, turnbuckles of varying lengths, cross-bracing down to bracing plates + all the hardware needed, (all in tagged bags). All I had to guide me was the building catalogue that listed about a hundred different steel pre-fab buildings. It was a very daunting task, because the field staff were part of the strike against the manufacturer!
I spent three days in sorting through the steel structure so I was able to tell what was what. This way I could estimate what had to go first and last so that there was some order to the shipments North to Whitedog Falls, G. S. The shipments began the second week and each day I had to go to the construction site steel-yard to see that the components were placed were the last pieces needed were at the back. Some pieces that were classified as urgent (such as the beam anchor plates had to be placed exactly where the surveyors said that they would be used). These anchor bolts had to be imbedded in concrete at least over a foot deep. This often required the use of jack hammers to drill holes for the anchors.
This phase took a month of part-time work on my part as I was doing my usual tasks at the same time.
The top Superintendent at Whitedog Falls G.S., was an ex-Canadian UDT diver. As I was the only experienced skin diver at Whitedog Falls Hydroelectric GS, I was co-opted to do some of the diving to clear the de-watering pump intakes. Then I was asked if I could do something about the severe ‘toefill’ leaks through the downstream cofferdam.
In the winter as I was the only qualified diver there, over three weeks I made eleven successful dives, clearing debris from the de-watering pumps intakes. The superintendent was able to expedite the orders for three ‘Constant Volume Suit’s’ (diverted from, no doubt, a less urgent job). That was the first time I learned about Cousteau.
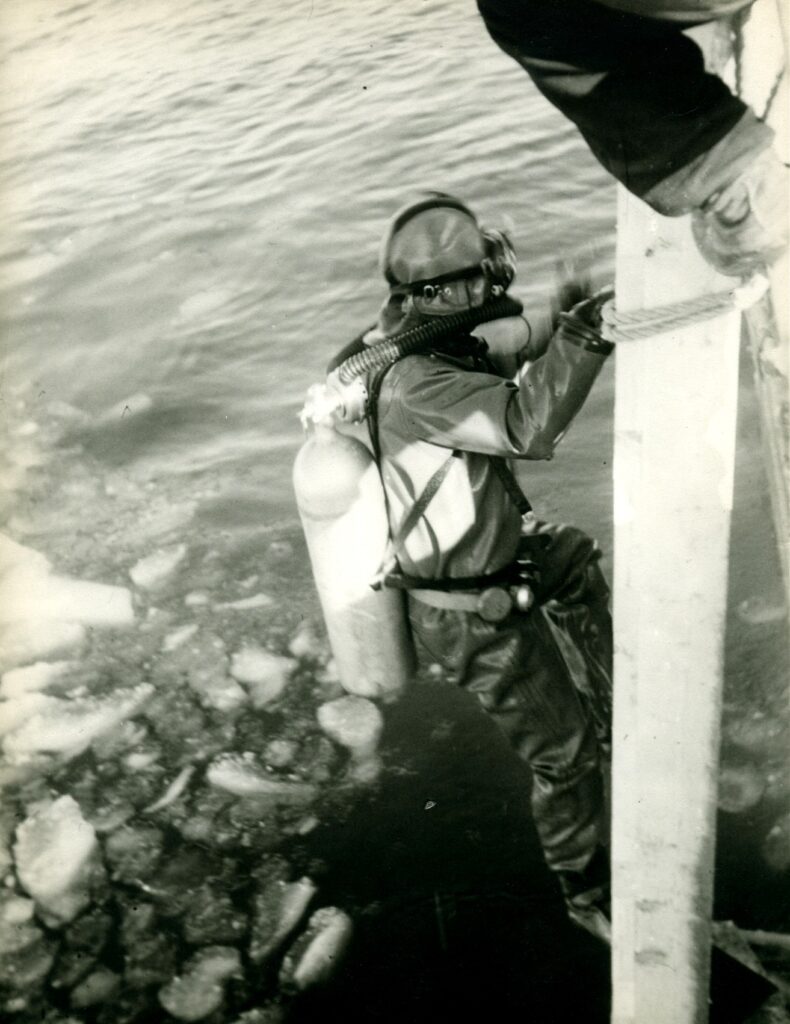
Whitedog Falls GS – New Constant Volume Suit -Feb, 1956
At the time the air temperature was about -25 degrees F. At the time the air temperature had dropped to -33 degrees F. Thank heavens, one of the suits fit me (I was 159 Pounds at the time). There was another diver, however as he weighed 198 pounds, I had to drive up to his quarters (he was married) and he didn’t want his wife too see him. It took me twenty minutes to extricate him from the suit; he couldn’t stretch the thick moulded neoprene neck by himself. Consequently he couldn’t dive until he lost weight.
I rigged a one foot piece of sacking on the end of a well varnished broom-stick handle to use as a ‘suction probe’. On surfacing I was able to direct the trucks to where the cofferdam was leaking.
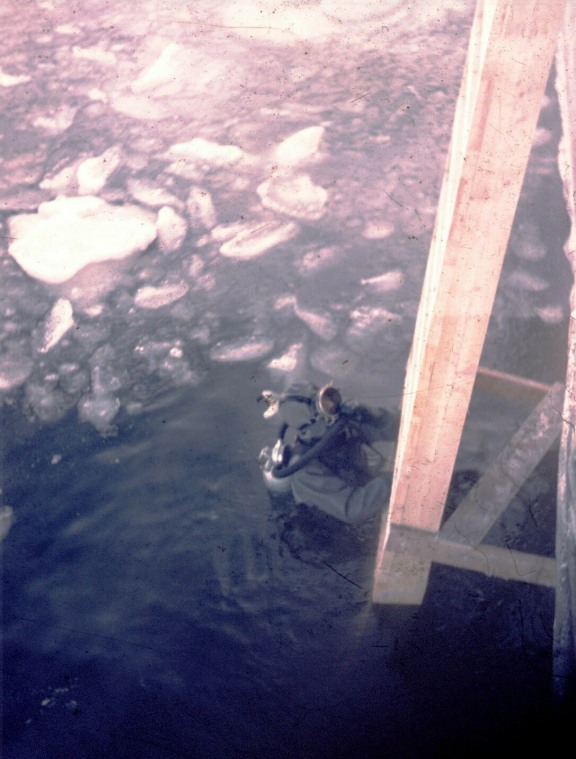
Another Whitedog Falls GS This is another Constant Volume Suit diving experience the temperature under the water was about + 33 degrees F, whereas ten feet above the surface it was -37 degrees F (and that was when the Northwest wind was only 6 MPH!
This is the first proposed connector layout for the backpack connections.
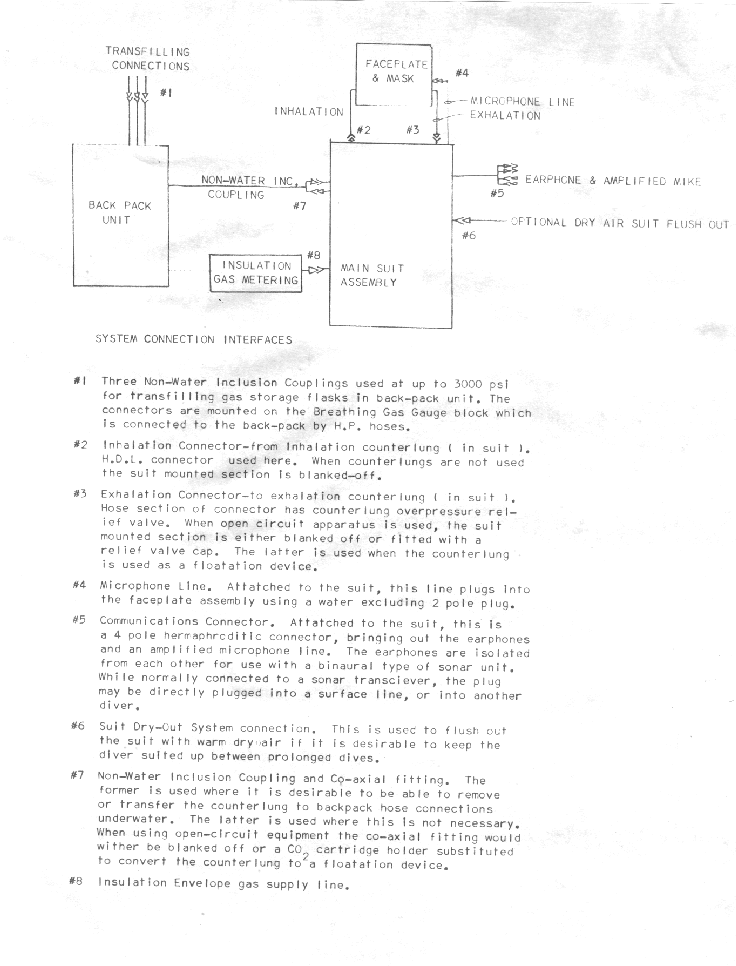
Later I found that stainless steel non water inclusion 3,000 psi high pressure fittings were far too costly
I returned to MIT in the fall. At that period the Polio epidemic had hit Boston. Calls went out to students asking for any person who had any type of medical training to volunteer. As I had taken the St. Johns Ambulance courses in Winnipeg I was assigned to White Nine in Boston’s Hospital. There I met Haven Emerson there on a service call (His father was a co-inventor of the Iron Lung).
I worked there for two and a half months, four days a week. Because some parents lodged complaints, we were reassigned to the Triage unit.
I also got a part time job maintaining the Sound System in MIT’s music library.
Then, I got a student employment offer from one of the staff of MIT’s staff in the department of Food Technology, Dr. Lyons. He was very liberal on his assignments. I was asked if there was anything that interested me? I replied, that I was curious about. I said that I found something peculiar in the causes of boles on Oak and Maple trees. I thought by charting the distribution of boles in the US, we might be able to locate some unexpected deficiency in the soil.
Quite unexpectedly, the common factor was a total lack of zinc in the soil. Dr. Lyons was startled, and went to retrieve some studies on the occurrences of prostate cancer in men. The correlation was well above the statistical mean. Several weeks later, he said that eliminating most chemicals that were linked to cancer, the correlation was astounding. He said that he believed that he could write a paper and submit it for peer review. He added, that my name would be attached to his paper as research associate. He added that zinc deficiency might be linked to breast cancer. I added that there might be another link to cell mutations downwind of chemical industries and steel mills. He told me that he was very concerned about hydrogenated fats and expected that margarine might be a serious problem.
He was terribly concerned about the amount of ‘useless drugs’ that were being released based on a peer review where the personnel were affiliated or associated with the manufacturer of the drugs. He said many times that a peer review had to be based on an expert or experts that were totally disassociated from the manufacturer!
Otherwise, there was an obvious conflict-of-interest!
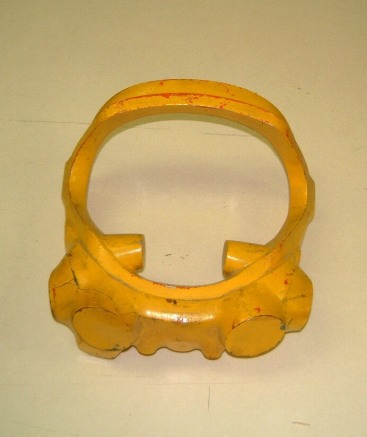
This aluminium casting had over seventy hours of machining as well as very extensive hand labour. It was stolen from my room in Boston. Someone else spotted it in a scrap bin and kept it. Two and a half years later I ran across it in a pawn shop where I was looking for a flute. I paid $30 for it however I had not saved the rough mouldings that were made from this pattern. Nor had I saved the set-up jigs.
My first diving in the Massachusetts area was with the Newton Nautileers. In the winter, we used to dive partially under the ice in a quarry.
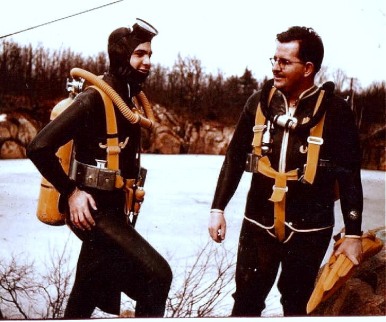
I had renewed my contact with Jerry O’Neal whose back-pack Jeff and I used. I had purchased a 1958 hearse and after painting in cream and blue, installed a heater in the rear. I insulated it, then lined the interior with Naugahyde. Because the floor was elevated to load a coffin easily; this left enough space under the plywood floor. So that I was able to fit some compressed air cylinders under the floor; with the cylinder pressure valves staggered and visible along the side under the open rear passenger door. I installed a cylinder manifold behind the driver’s side in the partition wall. I mounted several shock-bearing hold-downs on the plywood floor. I intended to place a twelve volt AC air compressor. The ambulance/hearse was another ‘Miller dual purpose vehicle that could power a roof mounted siren). It came with a a higher amperage Leece-Neville alternator so that there was plenty of power. Unfortunately the hearse’s selenium rectifier stack was almost fried. I was able to fabricate a three phase Silicon rectifier array and redo the voltage controller so that it worked.
(As an aside, when I returned to Minaki, the station-master slipped on the ice and fractured his knee-cap. Because of the weather aircraft were unable to land on the thawing surface of the bay. The road from Minaki to Kenora was impassable as the OPP vehicle was stuck in the mud about three miles from Minaki. I was called by the OPP and asked, because my vehicle had sixteen inch tires they, thought I could make it out to Kenora.
(When in Boston, I had installed ‘air-lifts’ to elevate the vehicle, as in the North shore above Boston we had to drive over rough roads. So we were able to get him to Kenora with no problem.)
I accepted an employment offer from The Albert an J. M. Anderson Co. Ltd., in Boston to head the R&D division. As they had large contracts with the Navy and I was developing cold water diving apparatus the US Navy was quite interested. As part of my R&D, I was able to begin some cold water diving work. I was able to get access to a host of different types of foam. Neoprene, Cloprene and several other types were selected for testing. One stuck in my mind only beause of it’s potential toxic side effects.
A Japanese Manufacturer was promoting some foam that was based on foam based on rice. They sent us several samples. I selected three samples. As we had to use a foam ‘slitter’ down in Providence, Rhode Island, we were able to use one of his smaller units on Saturday; as it was free.
Two of the the thinner samples were ‘bordy’ far too stiff to be used in a ‘skin-diving’ suit. The other thicker one seemed fexible enough to employee the ‘slitter’. But on the initial, (and thank heavens-we were able to stop the ‘slitter’ when a ten-inck ‘slit’ had been done; the free gap stank of ‘burnt feathers’ it was sickening and we started to cough. So we gave up as the side effects were terrible. I saved a small sample in a Pyrex bottle. I went to a ‘rubber expert’ at MIT. He told me that a major component of the smell was ‘Hexane’ , l-hexane and possibility of l-hexane; a very volatile fraction notable for its stench. His opinion was that it might have been the result of a ‘bad cure’. Hexane is very dense and it takes a long time to dissipate however some are very light and the volatility of these ‘fractions’ can result in some toxic side effects!
On my return to Boston, I made some suits for my skin-diving friends in the Area. I was a member of the Newton Nautileers and The Boston Sea Rovers.
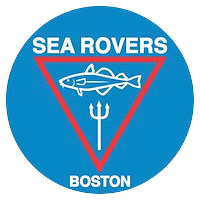
Boston Sea Rovers Copyright
In the beginning, I used 1/4 inch closed cell unlined neoprene foam. Then I contacted Rubatex and asked if it was possible to apply a knit fabric to the inside of the neoprene. On the first trial sheet, the fabric was a buff color and the black neoprene was spotty, as there were areas where the fabric had not been coated. It was a promising beginning, and on the second run it was perfect. I was able to order a dozen sheets. They said that some would be supplied in a different color of fabric. Anderson paid the nominal cost of the runs.
The Freon gas was valved into the closed cell neoprene suit using a 1/4 inch by a seven inch diameter insulating pad. This pad shielded the diver’s skin from direct contact with the expanding Freon as it could cause frostbite. At that time we were able to purchase one pound contours of Freon 11 from any car parts supplier.
At the time Freon was incorrectly classified as a respirable gas, (We didn’t know about the mis-classification for five years), so we thought that it was safe to use only as an insulating gas by limiting the diving depth to eighty-five feet.
We found that it could double our exposure time in the cold waters of the North Shore of Massachusetts.
By this time, I had to assume the role of rubber engineer as the one employed at Anderson had suddenly developed cataracts.
However, the board of Directors at Anderson Power Products seemed unsettled as to where they wished to do their R&D. So the diving part was put on hold as they wanted to split between Load Cells and High Voltage Research using BIL (Basic Impulse) testing. I was to design a portable BIL tester with a maximum voltage of 200 KV. When I drew up a reasonable cost projection it was quite obvious that they had little concepts of the costs. They said that if I could reach 120 KV they would fund the more expensive components to reach 200 kV. Thank heavens Cambridge is full of electronic and war surplus dealers. I went to Eli Feffron in Cambridge and was able to purchase the components for a five stage Marks Bridge for $250 allowing me to spend more on the fabrication of the high voltage insulating components. I needed the high voltage insulating materials. Part were in sheet form and others were in the form of various sizes of heavy wall tubing.
In four months I had a working unit, including a portable wire mesh cage. The remote controls were twenty five feet away from the shielded enclosure.
Then Anderson Power Products had an Request For Quote for Pacific Gas and Electric and we had to stop the BIL project.
Now I had to find a way to rig sensors on a transformer-tap-changing switch. A bit pissed off, I remembered seeing the same Consolidated Electro Dynamics strain gauge tester we had used at MIT for testing supersonic aircraft parts under thermal shock. However there were plenty of spare vacuum tubes and all the galvanometers were working. I even had a roll-film developing unit that were used for aircraft camera shots. It fit the film used in the Consolidated Electro Dynamics strain gauge unit. The installation was on two six foot relay racks. Again I went to Eli Effron in Cambridge who purchased all MIT’s scrap. He was able to locate the stuff I’d used at MIT.
I had to rent a step-van to transport the stuff from Cambridge to Boston. It took four days to set the stuff up, thank heavens there were plenty of spare vacuum tubes and sealed roles of the film. It was up and operating in time. I mentioned that I had bought a war surplus air-based camera on trip into Winnipeg. It had lots of rolls of high contrast Kodak film and the light-proof developing tanks.
(I found that these were the same as what I’d used in Minaki several years before).
Then Anderson suddenly switched me to the scheduling department to see if I could locate any surplus manual punches and card readers. I located the number of card readers and the needed punches. The idea was that upon entering a department the card would be read and upon exiting the department a designated punch would be used. I found a grad student that was cognisant with computerised scheduling and together we were able to construct a 15 station demonstration unit. It performed well above specifications.
Oh well, I should have anticipated another reassignment! However Andersons board were too conservative. (Remember that the founding company, Albert and J.M, Anderson had turned down Bell, who wanted Anderson to make a prototype of a ‘telephone’ switchboard!)
I was very concerned about the choice of Lexan ™ for the moulding, as it was hydrophilic, not good in a hot and humid atmosphere. I was overruled.
Over a year after I left Anderson I found out that my name had been dropped from the patent for the either-end connector; which I first designed for a loudspeaker connector for audio use. Granted that it was limited on power handing ability but I had scaled it up to handle 400 amps.
Leaving the R&D consulting group in Boston was a financial blow, however, I contacted the Diving Trials and Development Dept.(DRET) where I was well received. It was suggested to me that I was able to construct a workable prototype, it could be tested at DRET in Downsview.
When I returned to Canada I received an offer to propose an R&D program for the development of a cold water diving suit from the Canadian Government. I had made contact with the Downsview Diving R&D Branch. With some trepidation, I accepted. As my parents had moved to Minaki and I had a small lathe in the workshop. Having considerable experience with neoprene latex and having some knowledge of the various types of man-made insulating fabrics, I moved to Minaki for 7 months. At the time I couldn’t buy solvent based neoprene’s in less than fifty gallon drums. Therefore I resorted to the use of Neoprene Latex, that was in five gallon sizes. It was coagulated by diluted acetic acid then dried with hot air. If improperly done, it could be porous and weak and prone to delamination.
There I was able to develop the rudiments of a suit, including a mixed gas rebreather system. I was able to use fiberglass to mould a hard-hat that provided protection for the divers head. I made a three pane faceplate with the oral-nasal mask pressed against the diver’s face by latches. The faceplate seal was an extension of the outer neoprene helmet. Under this were felt pads for adjustment. I was able to use a kid’s wheel rim as the rigid core of the neck seal between the neoprene cuff on the helmet and the cemented-in-place neoprene suit seal.
Essential to the system was a mixed gas re-breather unit. Small Oxygen cylinders were available from Canadian Liquid Air in Winnipeg. I made arrangements to lease two of them for three years as well as a small lab-cylinder for Helium.
The CO2 absorbent canister was a bit of a problem. I solved it by cutting a large cardboard rolled oat package. Then I covered it with several thin layers of resin impregnated fiberglass. After sanding it down, I used a fly cutter on the upper flat face, to make an five inch opening. By pouring near boiling water into the hole, I was able to strip out the cardboard. I realized that I hadn’t allowed for the small perforated slit stainless steel baffles that were needed to contain the Baralyme C02 absorbent. I had to cut off the ends to allow these pieces to be inserted. The inlet was mounted at one side of the container leading to the upper plenum. This allowed me to braze in a one inch diameter stainless steel tube at the lower plenum slanting it slightly so that it connected to exhaust breathing mix. The two cylinders were strapped on both sides. As the two cylinders were longer that the C02 absorbent to be mounted between them. I used a sander on the surface of the canister to slightly reduce the diameter. Then after assembly, I patched the slits with fiberglass. After the sanding, I used a two-component epoxy paint on the canister.
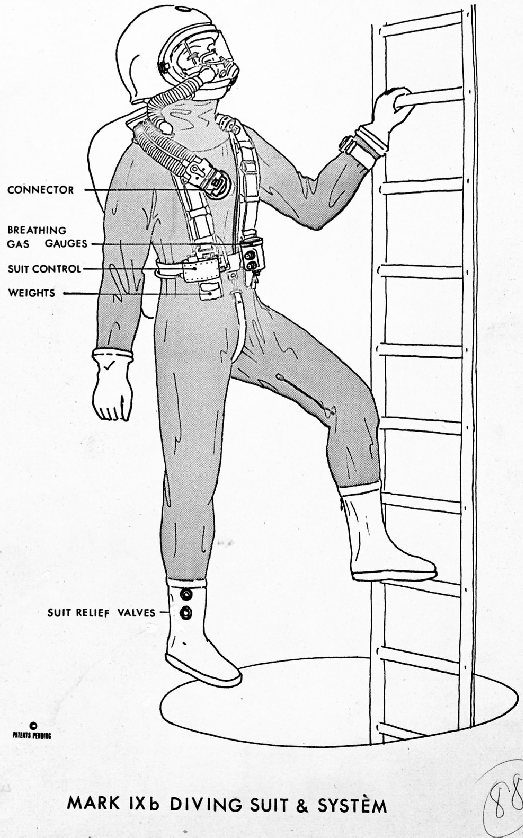
This was my impression of how the suit would look.
I spent several months on both the design and on the consecution of the helmet. The right shot was to ensure that the cushion sorrowing the diver’s face was comfortable. The left shots the bare helmet without the suit. I was working on a dual (cross) ratchet adjustment. It was surprisingly efficient. I experimented with castable soft moulded inserts that were put inside the black dipped neoprene. Thea inserts were hard enough to keep the seal in place and soft enough for the divers comfort.
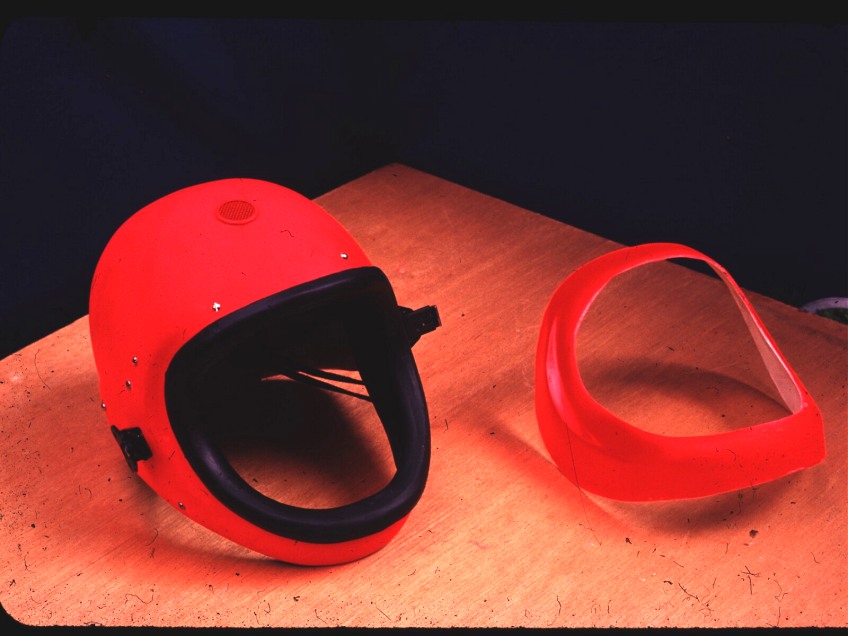
Initially we selected Freon as the insulating layer of gas for shallow dives. At the time DuPont claimed that it had no adverse physiological effects on the human body. Therefore, we chose it for use at depths no greater than eighty five feet.
I was able to employ some small Clippard valves to make a gas regulator for the suit insulation layer. The counter lung system was inside the suit itself to minimize heat loss. I had made a simple connector pair that was centered of the front of the suit so that the backpack could be removed easily.
After several months of development I had a workable design I was able to test it in the Winnipeg River in May. The water was still very cold!
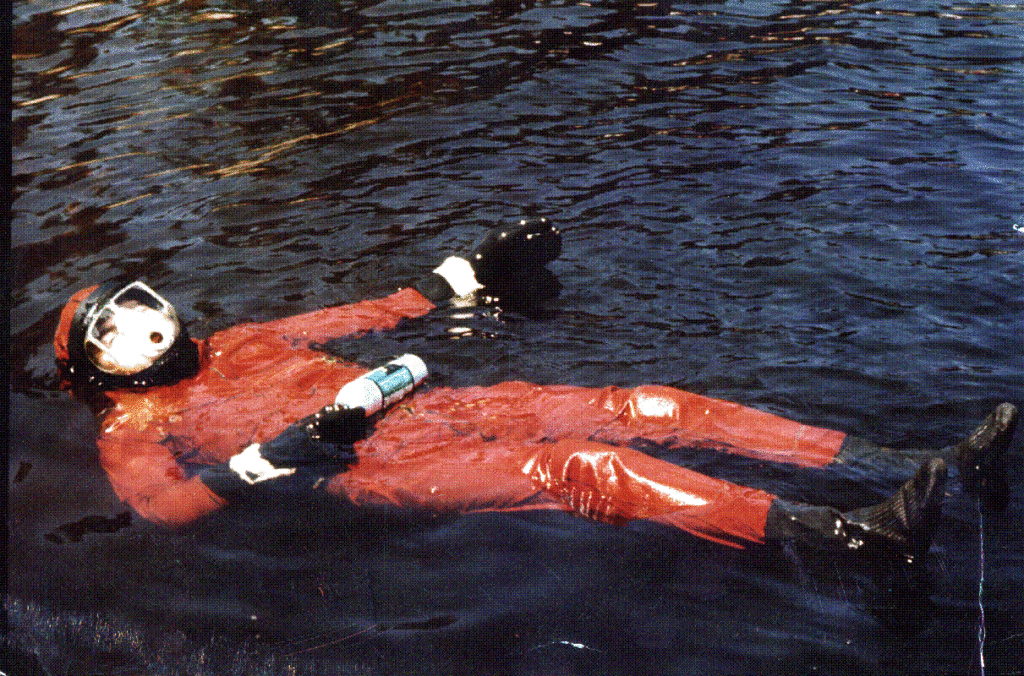
Floating on the surface wasn’t a real test. Nevertheless, the water was cold, so after two hours when one of my neoprene covered shoes began to leak it was painfully obvious that more work was needed. I recoated the defective shoes with a solvent based neoprene coating. That stopped the leak. (It was hard to get as the solvent that was used as a thinner could not be shipped in containers more than a certain size!
The rebreather was almost ready. So it was ready to try once more. It was warm enough that I was able to dive with the rebreather for five hours at a depth of twenty feet without any change in my core temperature. There was at least seven more hours left according to the pressure in the O2 tank.
However I didn’t have an underwater camera so that I couldn’t record the event. My ankles had to be weighted and at that depth balance was unstable and I did not want to rig up a teather as it would not be safe. Unbeknown to me, the wind velocity increased. My tender began to jerk in the line and I had to surface. But this cold water diving suit did keep me warm enough to continue.
So in the early fall, of 1961 we formed Hydrospace Developments Ltd.
(When I was at MIT, I was told that whenever an unknown person asks for any type of research, an important thing to do is to verify their Bona Fides. The first step, is to do a Due Diligence on them before you sign any agreement!)
About nine months after we formed Hydrospace Developments Ltd., we received an offer from Magna to purchase it from the shareholders for $80,000 + some shares. A condition was that I had to be under contract to Magna for three years. Then my shares would increase. Ever year afterwards I would receive a bonus. It was a good deal for the shareholders as they would get some shares in Magna.
Magna insisted that all the shareholders had to agree to the sale. As most were near Ottawa (or Picton) I had to drive in the area to get the contract signed and witnessed. Magna placed a limit as they said that Magna’s Board had to vote. Unexpectedly, two shareholders could not agree, and I had to wait for another three weeks as Magna told me that the deal would not be approved if there was any more delay. By the time I returned to Toronto, Magna stated that our shareholders had waited too long. As I expected, some of our shareholders were irate, even after I mailed the contract papers by registered mail. Afterwards I found out that Merritt Harding was telling several shareholders that Magna would up their offer if the shareholders would delay. Of course he was wrong!
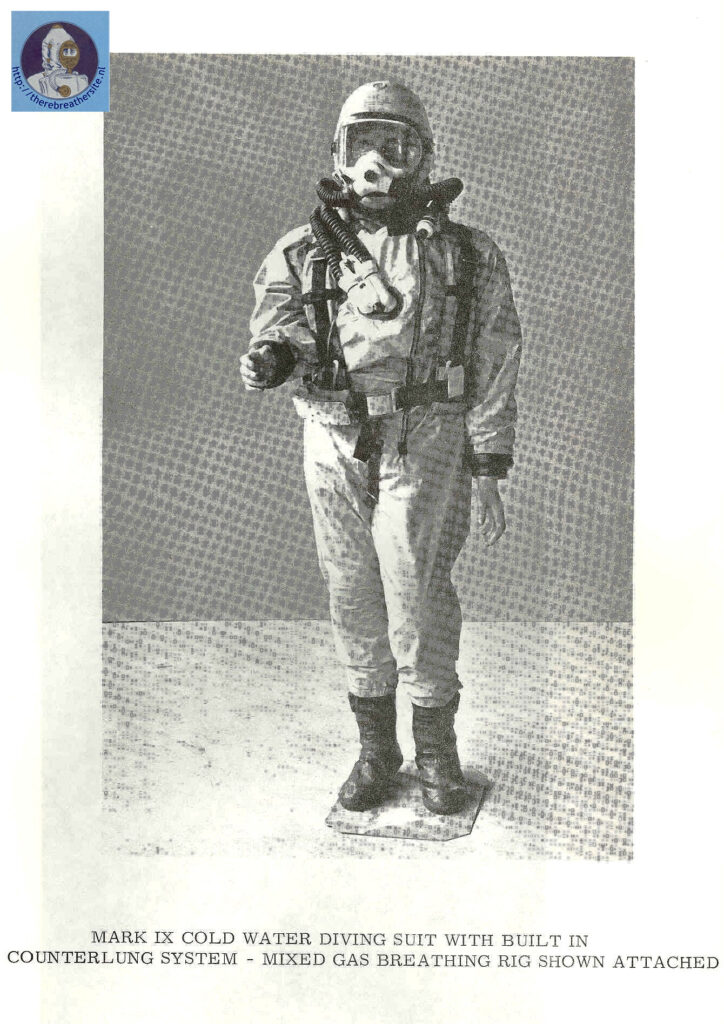
As I had been contacted by Westinghouse’s Undersea Division to advice them on production of fast methods of the production of prototype parts, such as cast epoxy, Shaw process or bronze and aluminum casting (using lost wax techniques), I spent a week with three experts.
Jerry O’Neal, of the Boston Sea Rovers, (I was a member), Haven Emerson and Alan Crassberg has been working on the Smith Mountain Dam; using saturation diving techniques. M. H. was furious with me probably as he realized that I that was very well connected. Anticipating that he might make a similar move on our company (as M. H. was the companies principal creditor, he’d served them with a Demand Note, M. H. had seized all their assets, then put them into bankruptcy).
However as I had formed Wright Electroacoustics in Boston, Mass., and by consulting and R&D, by 1958, I had accumulated $45,000 after taxes. I invested the money in a note that matured in five years. So that gave me enough to by property in Canada I had seen a piece of real estate in Richmond Hill , where the TD Bank head called the mortgage, it was listed under a ‘Power of Sale’. I contacted the bank and was advised to retain a real estate broker to place an offer. I was told that the property had been owned by a welding company and had a high amperage service plus a furnished second floor apartment. There was only one thing that made me hesitate. I had seen a pair of oil filler surface mounted plates in the gravel surface parking lot on the south side. As the building wasn’t that old, there wouldn’t be any accumulated leakage. I knew that I would be able to switch to gas when it was available.
I contacted Grant Reality on the east side of Mount Pleasant Avenue. I gave ‘Grant’ a certified check for $250 to bind the offer and was told that he wound act for me with the bank. I told him if it was accepted by the bank I would be able to back it up with another $20,000 + brokerage fees and whatever land transfer fees that were needed.
I waited two weeks and Grant told me that the property had been perched by the Department of Lands and Forests of Ontario. Well so be it. Under law the amount of my deposit had to be returned.
(I waited for several months, the amount was never returned. As I had left my address at the Hydrospace Developments Ltd, plant) so I was really pissed off when Merrit Harding informed me that he had deposited my check. to TD bank. I had signed it on my account at the Royal Bank and Merritt Harding had no cause to complain. So I knew that I had to be very careful with this unscrupulous jerk!)
Six years later the TD bank wrote me a letter telling me that I owed them $4500. I went to the bank and found that Merrit Harding had opened an account there under Merrit name and Ben Ackerman as a co-signer.
So I was still concerned that Merritt Harding would pull the same kind of stunt on Hydrospace Developments Ltd.
You see, Merrit Harding also had three other companies that he was backing; a lawn care company, a company specializing in Payrolls (Bemish Construction) was one, the other one was an Insect Control company. MH was too cheap to realise that the MonRobut computer needed an air conditioned envioment to operate. The two people involved had to take home three IBM computer
typewriters to cool off and dry out. The office was damp and humid and the cork clutches would malfunction.
We went down to Annapolis to Westinghouse to show them a prototype of our coldwater diving suit and have it tested in their pool. However I received an urgent message from two of the people on Doncaster Road, that M. H. had taken over. I had asked them to call me immediately if M. H. was planning anything weird!
Unfortunately for the demonstration, when I was away, our landlord at the time; M. H., had accumulated usurious rentals on all the office equipment (typical was a monthly rental of $150 for an IBM typewriter that we’d used for nine months). I was able to borrow the money to build a mezzanine at the South-eastern corner of M.H.’s three units in Doncaster Road in Thornhill. Remember that I lived upstairs in a ‘furnished’ area and had the ‘lost wax R&D’ under it.
Then at M.H. insistence (remember at the time as a student at MIT, I was able to approve structural up to a well-defined limit; with my seal on the drawings I was able to obtain approval. So I designed the structural steel for a mezzanine in the second unit and built most of it myself . Again M. H. paid only for the steel and lumber. Then after it was built and inspected, he claimed that my work as a professional engineer wasn’t worth the pay.
To recap it again a frend in the area telephoned and told me that he’d that he had seen M. H. leaving a ‘Demand Note’,for Immediate Payment on my desk. Interrupting my visit to Westinghouse, we left right away. We got back at seven PM on Friday night on the long weekend.
I had contacted a rental agent in Richmond Hill, paying a renewable months rental for a small office on Enford Road. The rear had been rented to a Kitchen Cabinet Manufacture, and in the summer reeked of particle board glue. The eye irritation was too much but we had no choice.
Later I found out that the property was registered to Lawerance Construction Company (there seemed to be some confusion about the title).
By working all of the weekend I was able to move everything up to a temporary rental place on Enford Road in Richmond Hill. By Tuesday AM, everything had been moved. I countered by leaving a ‘Demand Note for the payment of the engineering less Merritt Harding’s rental charges’. Mine was much higher.
Then, as I received signed and witnessed affidavits from all of the other people he’d put into bankruptcy. I had got out just in time! Case closed.
I withdrew some of my available funds and began R&D word on liquid crystals investing $28,000 + in a long term project. A semiconductive polymer was the the result, (Now named ‘Stabilant 22’).
About 1994-5 I met Dr.David Turner. He was an accredited hematologist to NASA. We were discussing the problems of motion sickness under weightlessness. They had tried several drugs; but there were too many side effects. I had used Ginger when I had to errect a 120 foot tower at our cottage at Minaki. One of the mill super’s at the Pulp and Paper Mill in Kenora had to climb up the interior of the Mill; he told me that one of his staff had recommended ginger to stop ‘queasiness’. So I suggested it to Dr. Turner.
When I met with him three weeks later he told me that I worked! He asked me if I could think of anything else; I told him at MIT, I knew a group of physiologists that were working with test pilots. They suggested magnesium, vitamin B12 and vitamin D in large doses. It seemed to work for some pilots. So he suggested to his NASA colleagues that it was worth investigating.
I also knew about Vitamin E Succinanate; a water soluble form that was much more effective form as it acted very fast. The Vitamin E when combined with Vitamin E Succinanate was very effective as it acted on the sarcoplasmic reticulum to prevent the accumulation of Heparin that was the cause of cramped muscles.
At Hydrospace Developments Ltd., we went to the US Navy diving seminars, at that time I was an expert on Diving in cold water conditions. I remembered a paper on Vitamin E’s effect on promoting circulation in the Sarco-Plasmic Reticulum to prevent the build-up of heparin that was the cause of muscle cramps in cold water. So I brought it up in one of the seminars on Clearance Diving. It was adopted!
The following shots are some of the items that were crafted as part of the saturation diving suit and support system in 1959 to 1964.
We contacted The Miner Rubber Company in Quebec and worked with them for two years to obtain a thicker gauge of neoprene with an off-white knit lining inside the suits. I was able to design all the parts for these suits and had the complex moulds machined by Steve Elmer. His company was called The General Machine Shop. (I also designed some plastic moulds for him). I took three years to make all the moulds and Armet Industries in Guelph did all of the moulding. Over forty years later the rubber parts are still strong and fresh unlike the expensive self-sealing zippers that began to crack twelve years later. We had ordered plenty of spares, packing these in talc and storing them in a cold location. Nevertheless, four years after the zippers on the suits began to crack, the stored zippers did the same thing.
Here is a list of the ‘rubber’ parts we had custom made:
1) Wrist-cuff seals. Essentially these were made of moulded elastomer. The initial design was oversize as we could not obtain data un the size of divers hands. We had to assume that there would be some flexibility in the wrist-cuffs mouldings.
2) Neck ring seals with a bronze insert that was moulded flat. This had to be bent a bit to conform to the diver’s body. We had a special steel die made to bend the bronze insert imbedded in the elastomer and with several modifications and a change in the bronze alloy we had little difficulty in bending two dozen of the neck seals.
3) Tightly accordion folded neck seal for the diver’s helmet.
4) This had a split-contoured monel piece with an over-center & spring loaded clamp).
5) ‘Rubber’ parts were made on the both legs and on the top of the divers head. (Two valves were used, the front one was for the interior of the helmet), the one just to the rear, was for any gas from the insulation itself. A dual stacked valve for both legs and one for the top of the diver’s helmet. The design was made with an over-center moulding for the diaphragm & the tapered valve seat at the center of the stacked valves. In a year of testing under simulated and actual diving use (where we taped colour change lest indicators under the these valves and on the diver’s under suit there was no change. These dives were made in cold water so perspiration would not be a factor.
6) Seals for fittings on the moulded ‘front and rear bib’ were moulded in place.
7) There was a brass backed clamp with a inner ‘rubber’ part on seal for the self-sealing zipper ends.
8) Just to the right, on the chest, there was a ‘rubber’ molding designed for the use of an external source of breathing gas. This was polarized and made so that when uncoupled or recoupled, it was spring-sealed. This allowed the use of a dual (intake and exhaust) breathing gas source. It was also designed for a different counter-lung application.
9) There was a place for a dump valve so that a diver would not be lifted upwards if any fitting failed.
10) On both sides of the diver’s ‘rubber’ helmet, were internal earphones with a gel padded internally vented ear cup.
11) A contoured gel cushioned oro-nasal mask cold be strapped in place before the faceplate was lowered and sealed in place.
12) There was a ‘rubber’ faceplate seal that was cemented to the ‘rubber’ flange part of the helmet.
13) Added to the cushion around the diver’s face was a gel filled ‘bladder’ similar to the oro-nasal mask. It also was donned when the gel was heated enough so it was ‘moulded’ to the diver’s facial contours. In the initial field tests it proved to be so comfortable that it was adopted as standard. There were ear cushions for the diver. As shown on the photo, these had a flap around the ear; this flap was free to move on the outer edge, and it worked well; however in extended use, it could be irritating and were also changed to a gel cushion.
It was necessary to insure that the diver could equalize the pressure in hi ears, so a small bypass was added. Although there was a thin ‘rubber’ membrane that separated the diver’s ears from the suit’s pressure, this had to be equalized. Communication to and from the diver was planned. As can be seen a neoprene covered electrical cord was attached to the diver’s inner helmet. At the end was a monel cylinder counting the signal processing devices needed to convert the unusual pitch distribution of the diver’s voice to what could be understood by others. Needless to say, all was in stereo. It was believed that enhanced delay apparatus could be made part of the ‘sonar’ communication. Selective filtering could also aid the diver recognize another diver’s voice.
As can be seen, we employed nickel electroformed parts for most of the metal helmet as well as for the stamped and machined parts the latches. Ether the tender or another diver with free hands had to be able to uncouple the faceplate. We designed a pull down device (similar to that used by astronauts) to ensure that the diver’s neck wasn’t strained.
Although we had to abandon the concept of any type of Freon as part of the insulating gas, the circulation of the mixed gas inside the inner suit might be reduced by the use of proper seals as well as venting valves. The techniques of gas analysis are well known and purging is now essential to eliminate the diver’s own ‘gas’.
14) This brings us to the production of urine. We designed a two sealing tube system that would function if the diver wore a personal urinal during diving. During unsuiting, the inner part cold be self sealing as the heavier suit was removed. Then the butyl intermediate suit could be removed leaving the diver free to take off whatever other personal deices.
15) Although the external diving suit is the major part of the system, and therefore is covered with reinforced ‘rubber tee-ring’ attachments, connectors (especially the fore and aft ‘bibs’, as well as the harness attachment ‘hard points’, the design allows unusual flexibility in choosing the devices needed for any assignment.
Initially, we used a Lexan (TM) vacuum formed part for the faceplate as it was easy to vacuum form. But four of the first vacuum formed faceplates shattered. No person that was in the department knew that Lexan (TM) had to be dried thoroughly before it could be vacuum formed. o the next run was OK. But the vacuum forming was fine for the prototypes but was too distorted to pass Quality Control in production.
However we anticipated having a real set of metal dies made to manufacture the final faceplate! We could use an electroformed die on both the male and female parts, backing up the thin surface shells with beryllium-hardened copper.
In order to make the C02 absorbent container, we had first to make a wooden pattern box. This, when heavily waxed, could be used to produce a thin fiberglass shell. Just enough layers would be used to construct a sturdy lay-up. The box to the left of center shows the flattened area where the venturi supply fitting was mounted. The right one shows the ribbing for the straps that secured the tanks.
In the same Thornhill complex was an expert pattern maker. This is his work!
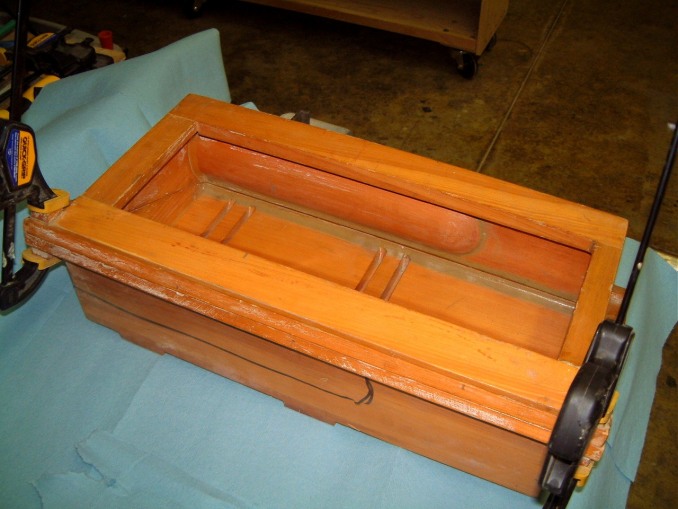
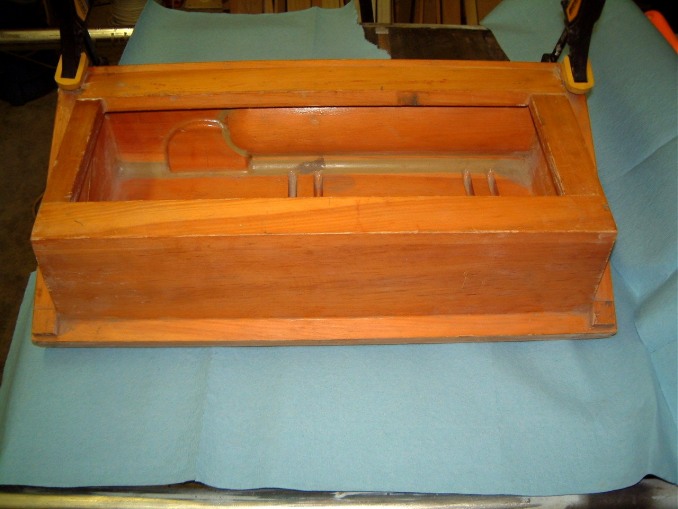
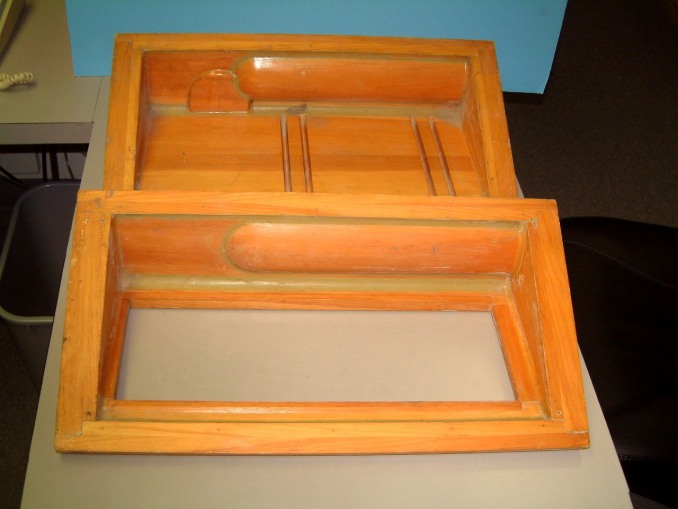
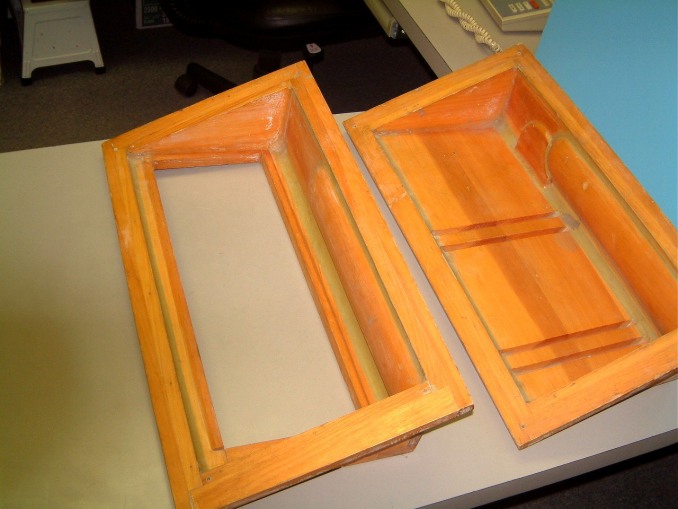
Part of what we needed to produce was a mixed gas re-breather This had a screw type filler for the C02 absorbent. Here is the fittings I designed. We were able to purchase four US Navy Certified oxygen metering valves for our use, These had very positive detents with pre-lockable mass-flow valves that could be pre-set for use with three inert gas mixtures. J. F. removed them after he was dismissed as well as the four matching counter-lungs
The left fitting is for filling and dumping the C02 absorbent. The next two are the inlet (showing the valve) and connector. The third one shows the assembled exhaust connector. The assembly on the right shows the outer inlet and its connector with the inner venturi ‘supply jet’ circulator. On the extreme right, is the brass insert that connects via a looped copper pipe to the outside tank and in both cases is silver soldered. These fittings are made with holes around the outside to ensure bonding with the laminate. By the use of slow-setting-time mixtures we never had a delamination.
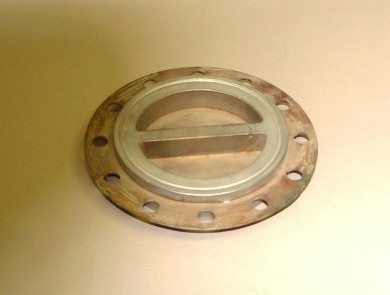
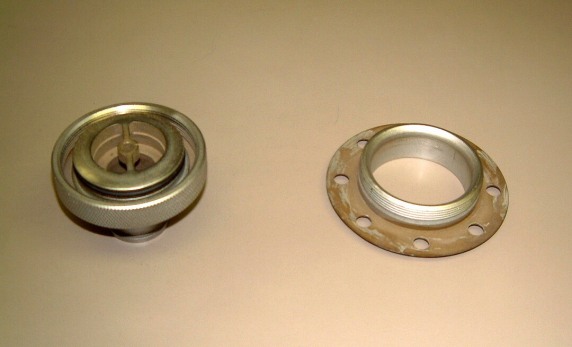
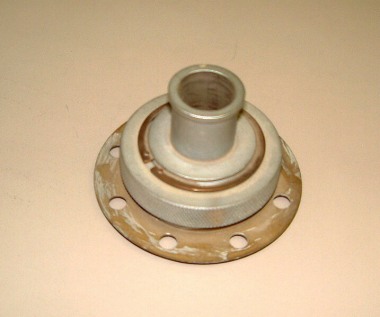
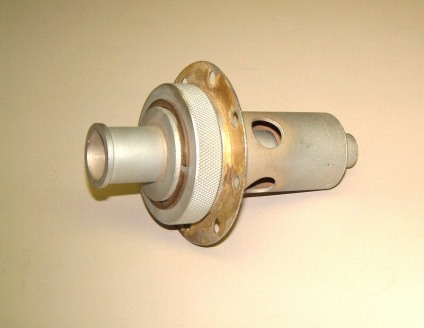
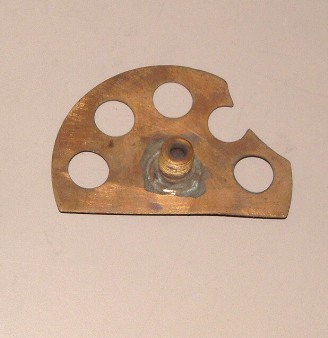
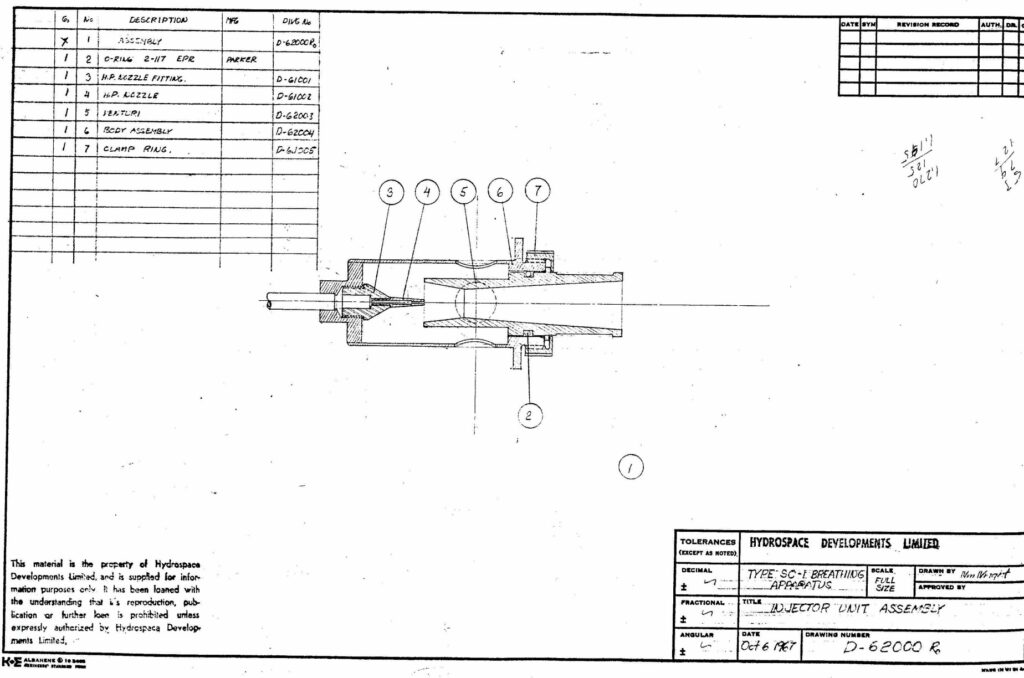
This is the drawing for the venturi and injector
We had to make some other right angle connectors. A typical example is shown below.
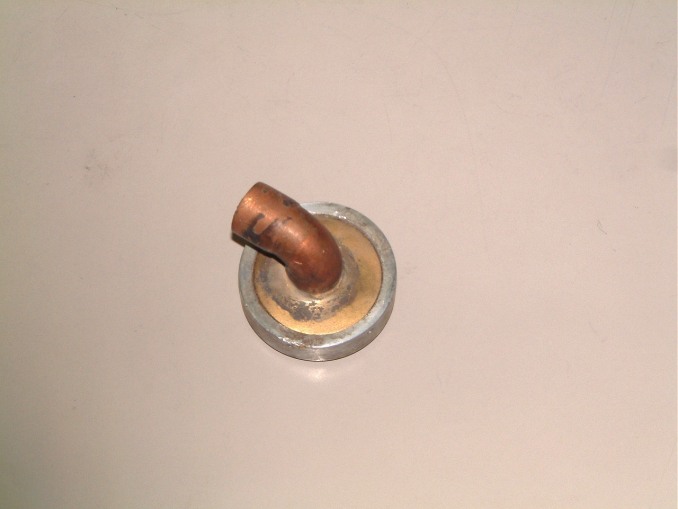
Next is one of the over pressure vent valves.
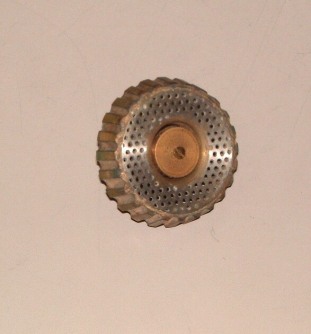
16) There was a place for a dump valve
Because some divers had problems gripping the valves we machined oversized handles.
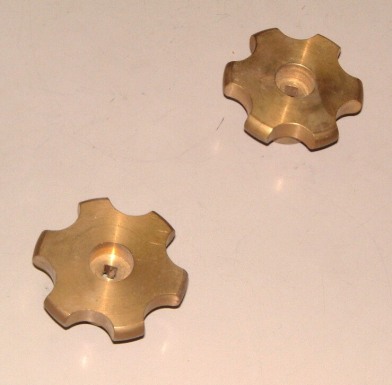
I had to design some other fittings two of which are here.
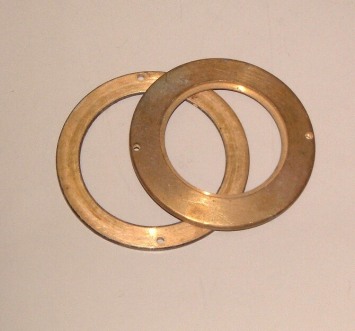
I made a drawing of the what I thought just how it would be configured.
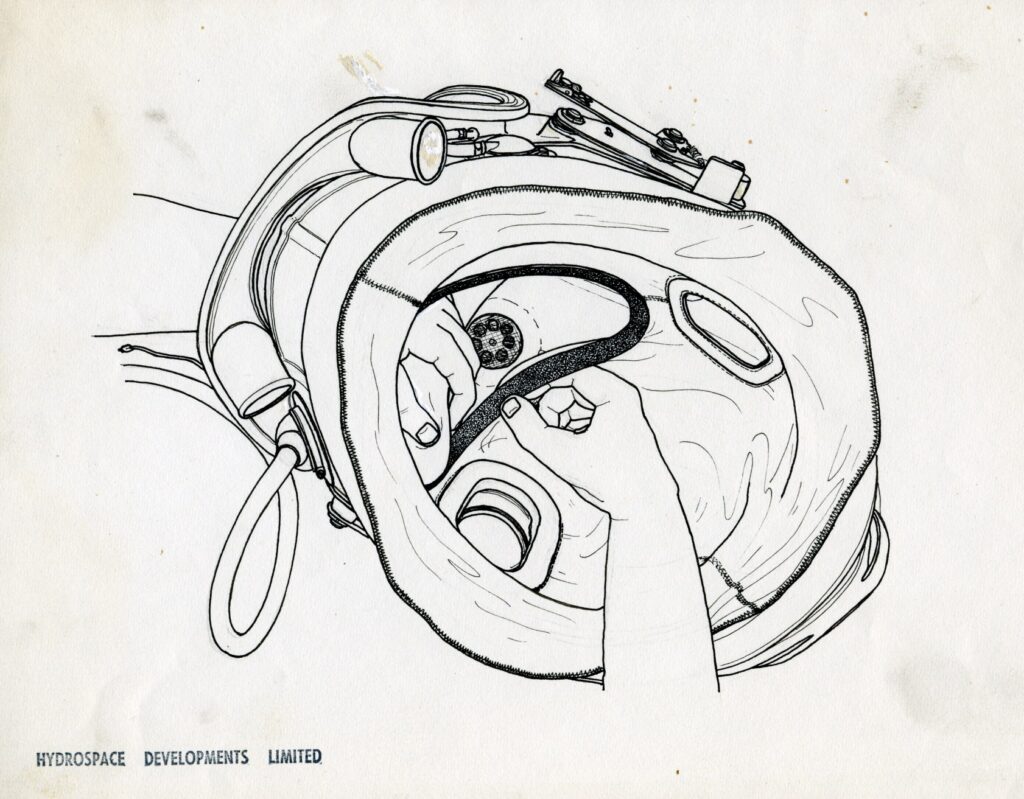
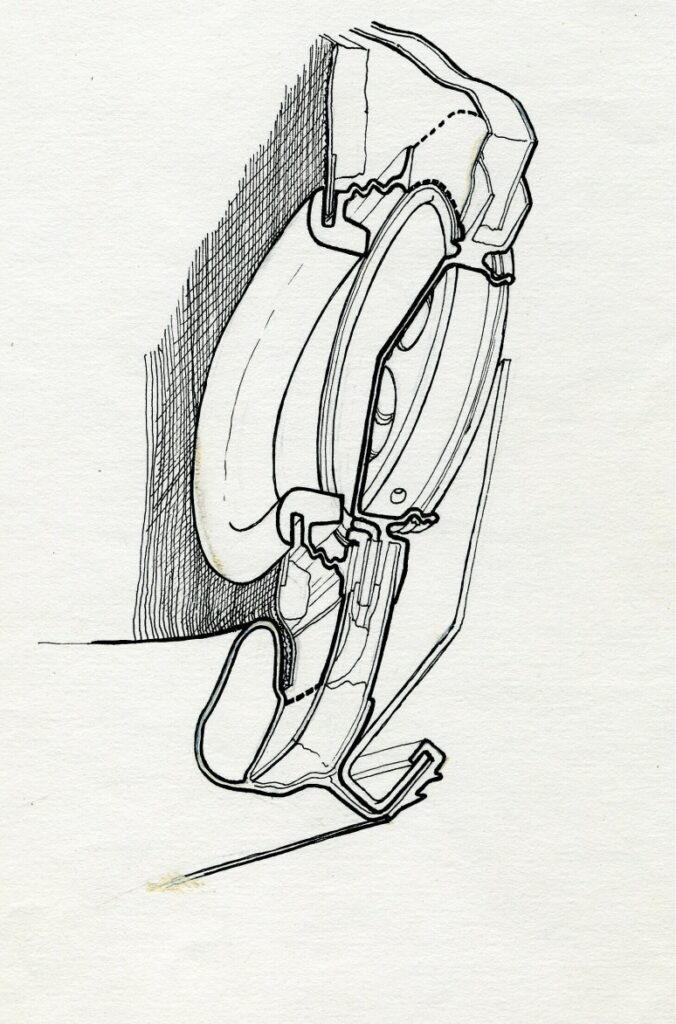
The left one shows how I intended to use a narrow Velcro strip to keep the detachable (and washable) lining inside the helmet. Next to it is a section through the first design of the earphone. Later, the inner part was replaced by a gel filled neoprene dipping. It was set in dilute acetic acid. Then I placed a chilled gel moulded pad and sealed it in place using neoprene cement. Before the diver first used the helmet, we heated sufficiently to melt the gel which moulded it to the diver’s head. It gelled within four minutes. We found that these customized pads were very comfortable.
The actual ‘hard-hat’ was a custom fiberglass part using some (jig) rivited-in place metal parts.
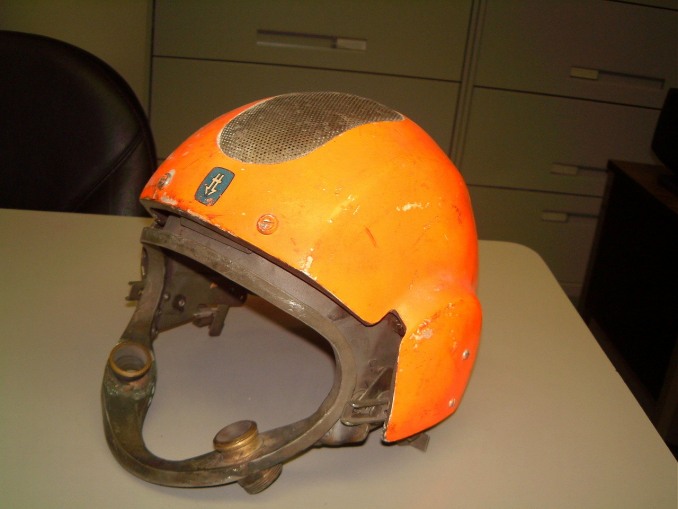
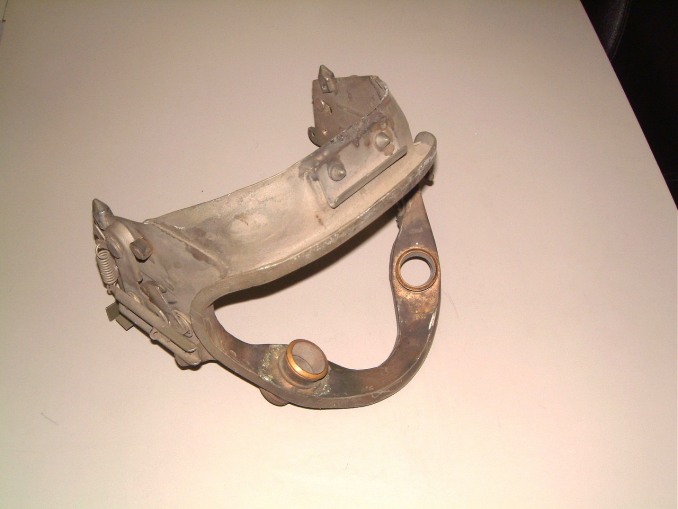
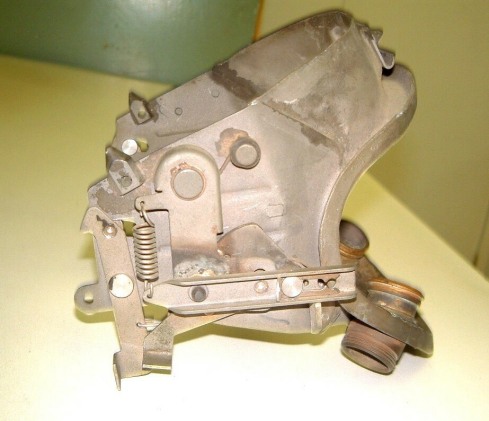
This helmet protected the diver’s head. Underneath this was the ‘rubber’ encased and padded head of the diver. Remember, this suit was designed for saturation diving and therefore had to be much more rugged than otherwise. A problem arose fourteen years later when a group of the suits had been stored and some of the ‘rubber’ reinforcing began to stiffen up a bit.

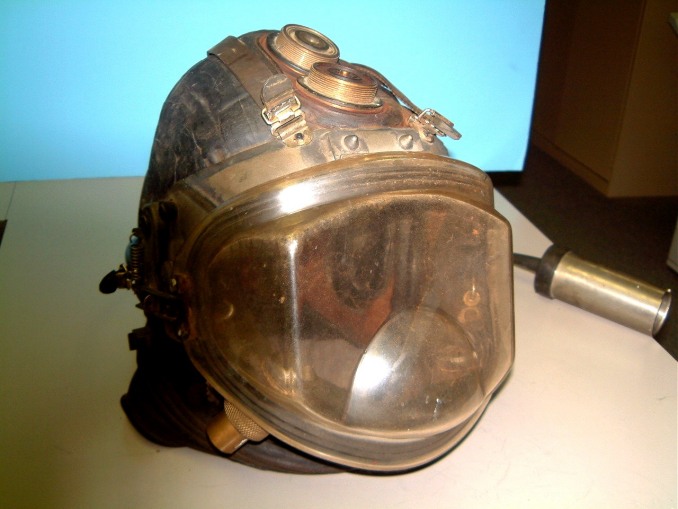
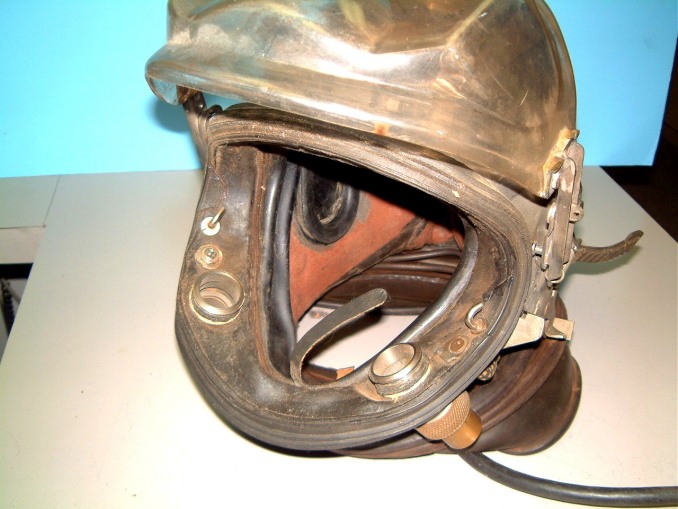
The first vacuum drawn, Lexan (TM) face cover for the helmet was sealed by a moulded neoprene part. As you can see, the first vacuum formed parts had problems in optical transparency.
(As I stated, it took me two days to determine the problem. The raw stock hadn’t been properly dried before it was formed. We would have had to go back to the manufacturer to obtain distortion free parts).
I should add that we had considered manufacturing a very large two piece Lexan shell for medical use for post radiation therapy. But I heard some disquieting rumors about outgassing of poly-carbonate. The dies for that large a part would have been at least $1,200,000 Can.
Unfortunately, at that time the steel lobby was so powerful that we were unable to obtain insurance on the wound fiberglass decompression chambers we were manufacturing! Even though we pressure tested them to eight hundred PSI without leakage.
There were five moulded neoprene straps running radially around the rubber helmet to secure it. The main problem was that the prototyping process we had to use involved in too many layers of material. The result was that the prototype was heavy and too stiff. The fiberglass layup was too thick and the protective part didn’t fit properly. We laid up some thinner shells, however at the time carbon fiber materials were too expensive and almost unavailable. We began to make an much lighter and thinner helmet of epoxy. It fit properly and even though the suit was too heavy it would have to be used for trials.
Another problem was more difficult to solve, as I had to do most of the work by myself.
In the center was a five inch diameter hole in the web of straps. These are the straps with the neoprene helmet.
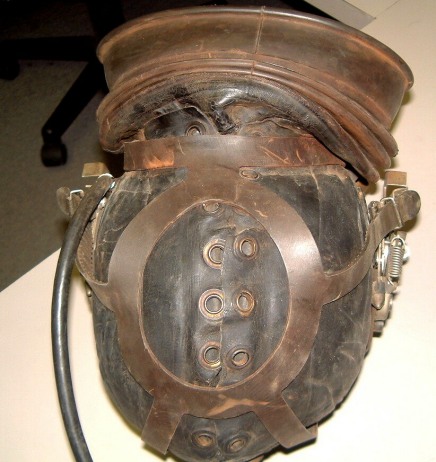
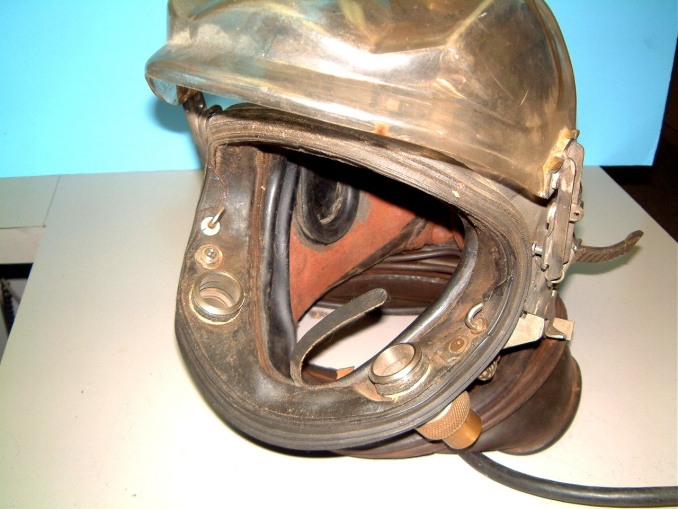
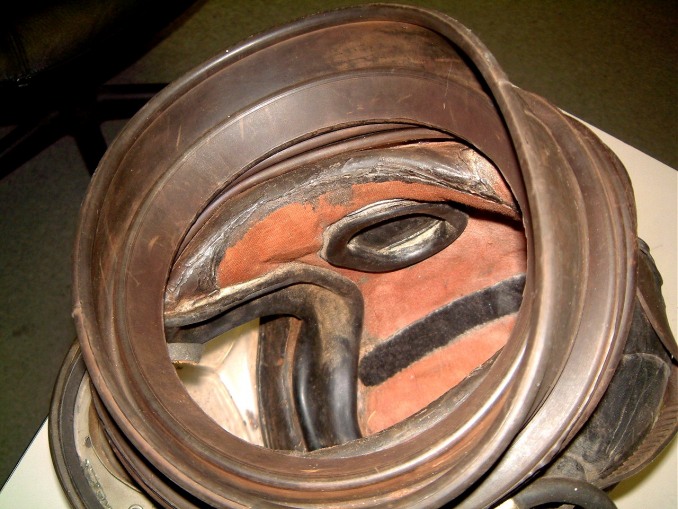
The amount of custom-built moulds started to be alarming.
The picture below shows;
16) Neck ring seals
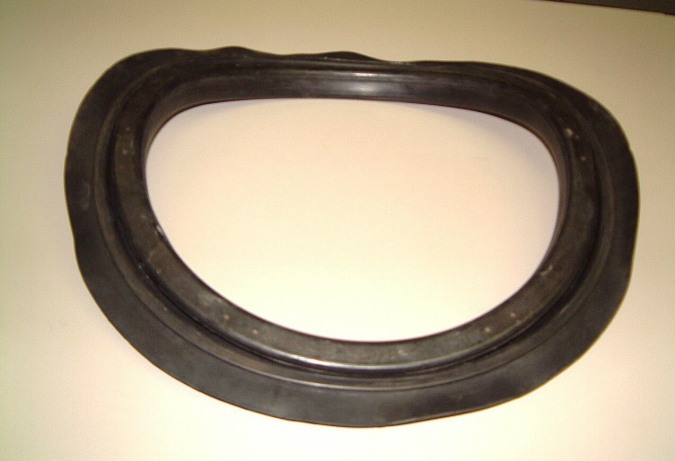
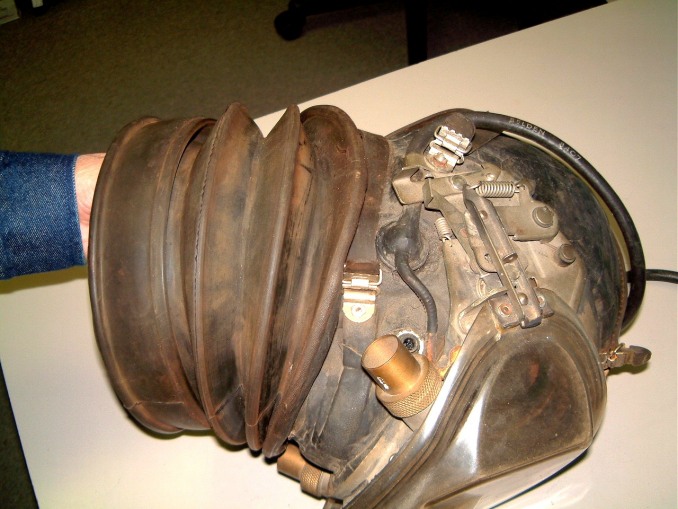
17) Tightly accordion folded neck seal The picture shows the construction of the tightly corrugated ‘rubber’ neck. This was deemed necessary so that the diver could look around. The roller enabled tie-down restraint that acted as an anchor wasn’t needed as much as the pressure differential at the median depths of saturation diving differed little. This was a classic case of over design, as I could have eliminated one of the corrugations on the neck.
There were some details that needed special attention such as breathing hose connections and other moulded parts.
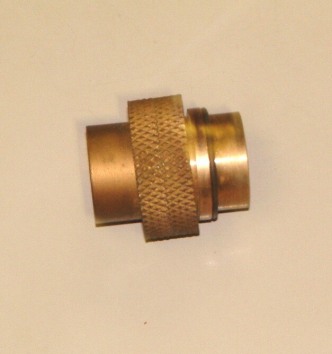
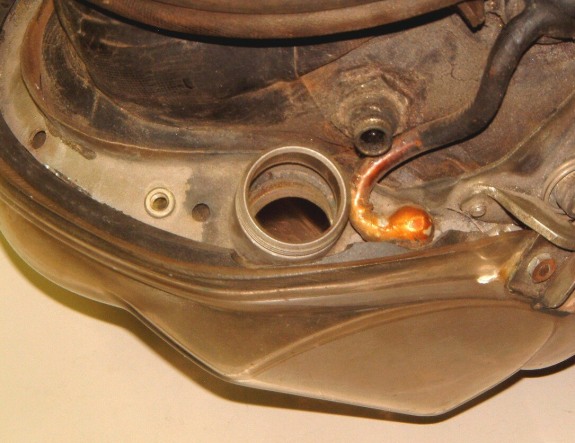
As I mentioned, we developed an over-center (toggling) diaphragm where the tapered seat of the valve was at the center. Because this way the diameter of the diaphragm was very large in comparison to the actual (valve) seal. We stacked two of these units allowing a small bead of ‘rubber’ on the outer diameter of each diaphragm (of the stack) to ensure a seal.
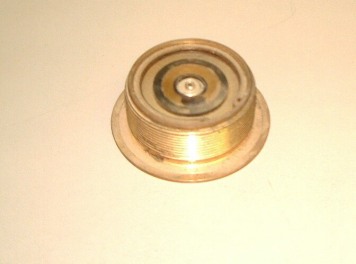
This simple valve assembly was tested on a fixture for several months of constant cycling (seven per second under a pressure differential of fifteen feet of water) with no leakage! This was the equivalent of well over 10 years of diving.
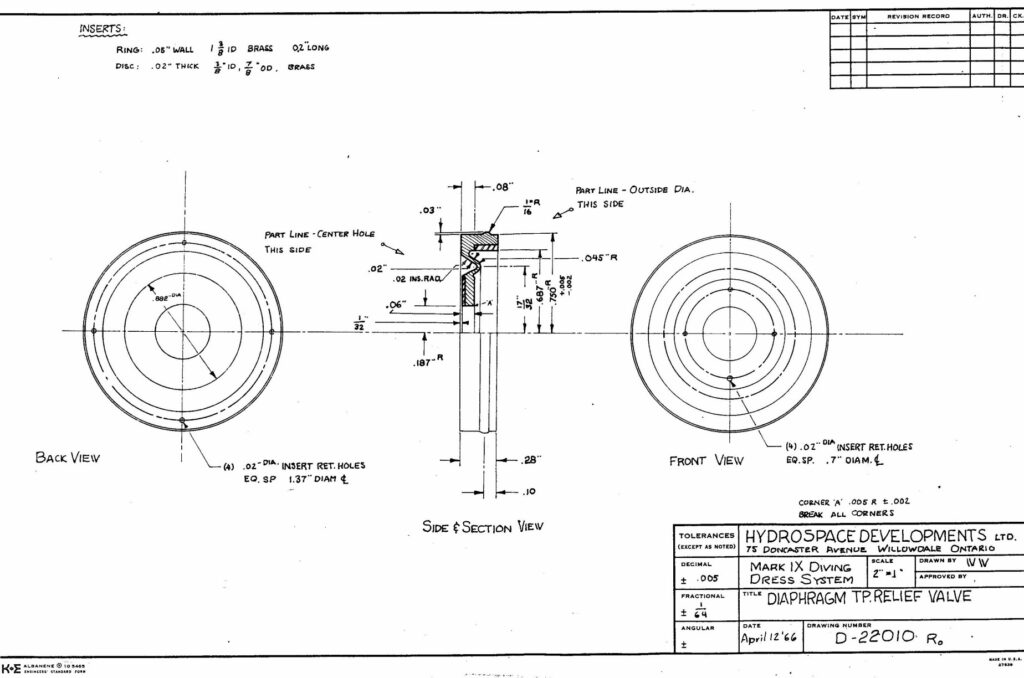
This is the design drawing for the valve.
The oro-nasal mask had to be worn comfortably for as much as ten hours per day. We developed a non-toxic gel to fill the ‘sealed’ cavity around the mask. The oro-nasal mask was retained by spring clips on each side. These worked very well!
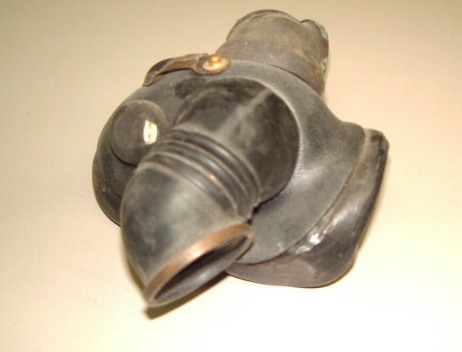

The melting point of the ‘jell’ was about 126 degrees F. In all the diving setups we conducted the diver’s face cooled down the ‘jell’, making it much firmer without causing any discomfort.
Later in the design of the oro-nasal mask we added a wider flange under the divers chin and resorted to a double ‘bladder’ seal; the outer one was the gel and the inner one was a silicon-aerolite powder with enough nitrogen-helium mix to soften a little, however under pressure of diving, it got harder as the depth increased and therefore retained its comfort for an extended period. This was so successful we did the same to the sealing system surrounding the divers face and the divers stereo earphones. We altered the drivers as well, to a water-proof voice-coil design. The miniature mike was altered to the same specification and we provided a dual throat mike option as well. The intent was always to balance comfort with a low stagnant gas volume. We were able to allow more head room and altered the helmet lining fabric to a chamois-like material that was retained by narrow Velcro strips.
Looking at all the custom moulded ‘rubber’ parts we had to design and make in two and a half years, still makes me shudder. A typical example is shown below. We made some die insert modifications to prevent mixups in just where the could be used.
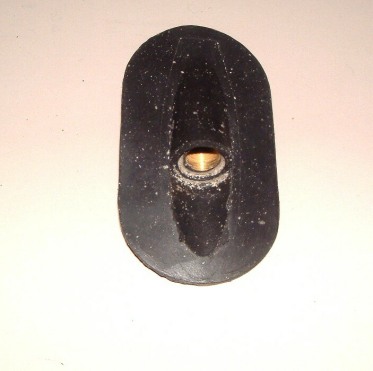
This simple part had an internal threaded brass fitting vulcanized into the ‘rubber’. It was used for anything that had to be passed though the outer suit. These includes the various gasses, these used gas tight connectors that were designed so that they could not be interchanged.
A similar fitting was used for the urinal, as the urine had be disposed of. So rather than using a bladder inside the suit itself, (as these had a bad tendency to leak inside the suit)! Remember that some of the dives were as much a ten hours long and frequently the divers drank hot coffee to warm up. If the diver was able to take over an hour long break, his whole helmet could be removed, for shorter breaks, the diver could use a large straw for drinking.
We had a singlechoice: a strap-on urinal, manufactured by Davol. This wasn’t too sanitary because when it was cold; it’s seal to the diver wasn’t reliable.
Obviously carbonated soft drinks were banned because of the gas that could cause pain on the dvers ascent.
In retrospect, I had also developed a much flatter urine outlet valve, it was located well down on the divers right leg. This was essentially a variation on the double non-return valve as used on the top of his flexible helmet. As we had more room on the divers leg, the mounting flange was deeper. Thus it didn’t protrude where it could snag. It had a different type of valve. This had a raised bar that the diver could grip with thicker three finger gloves. However in normal use it was more often switched off or on by another diver.
I could not locate the engineering drawings for either the ‘rubber’ mould or the actual parts. We always made plenty of these specialised small devices as we had to order enough milled compound to make it worth while to setup and run the moulding process.
The theft of these small specialty parts really bothered me. As I stored this class of mould in our plant. (The usual weight of the ‘rubber’ mould was between 15 to 35 pounds) whereas the ‘rubber’ moulds for the full collar that was eventually part of the outer diving suit was from 250 to 650 pounds. Remember that these types of ‘rubber’ dies were often quite complex; this made the desigh a bit of a chore as the die had often had to be assembled in advance before the ‘rubber’ compound was ‘injected’ into the die. In some cases this required part of the die to be bolted to the upper part of the press and the lower part to be bolted to the bottom part. Sometimes, we were able to use massive ‘tapered’ guide pins to align the halves together.
OK we see the necessity of the in-water disposal selection, but what happens when the diver is out of the water for a long time? Where is the urine get drained? We always used a very short length of tubing just outside the inner leg with a drain that has three openings along the tubing that act as low pressure non-return valves. At the very end of the drainage system, is the rounded (bright very blue) end. This valve is screwed shut (five half turns), to shut the valve completely. This makes it socially acceptable as the diver does not leave any trail. This system worked efficiently and it was worth the expense at this stage of the development.
Now the deeper tasks seem to involve lest pressure change and there are more wetsuits with a regulated flow of heated water to warm the diver. Obviously there is a real problem if the water fow isn’t constant. There has to be a balance between the maximum water heat, (A higher heat requires a lower flow and a more moderate heating needs more flow).
(There was a system in the 70’s that used heated mercury inside a network of small diameter tubes to keep the diver warm. It never was popular and it was discontinued for obvious reasons!)
A problem that was ignored for years was that any diver has to be very mobile; in other words, he is in whatever position that allows him access to the item. In extended duration diving, whatever the type of reservoir that has to be used; it cannot leak!
Remember that it has to pass through the first layer skin tight insulation that was about an eights of an inch thick; then a gas tight butul rubber layer (first designed for nerve-gas use), then a thicker lawer of reflective over a layer of Flalon (TM) , (a micro tube insulation that is water impermeable, we had to have two of these on hand as some water always seemed to get into this layer)!
On the inside of one lower leg, there was another drain connection. Remember that each of the tubes had a non-return seal and it was very rare that there was a leakage. At the last drain fitting there was a larger fitting that was normally left open to drain. However this valve was large enough that it could be rotated (five half turns) to seal it, preventing soiling of a lock.
Typical of the special connectors were a dual non-water inclusion coupling system that were designed for the corrugated hoses that were part of a system that could be used for emergency or portable breathing gas connections. The photos show brass parts as they were easy to machine. The final fittings could be machined from Monel if magnetic signatures were a problem, otherwise extensive use of stainless steel was normal.
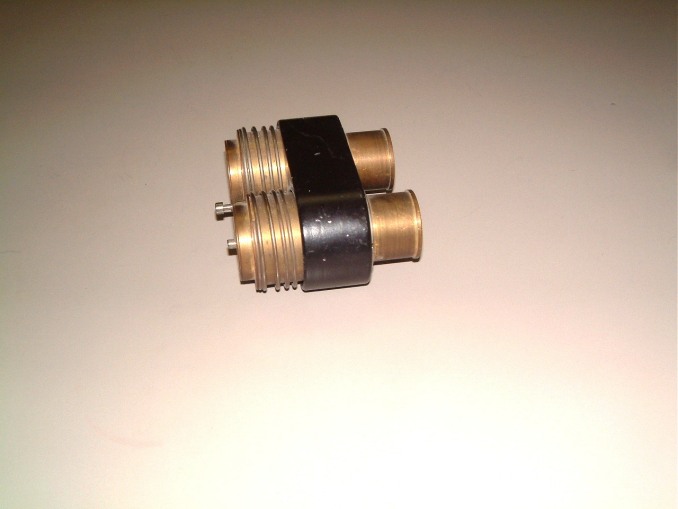
As I stated, this was the dual-hose connector, the mating connector mounted on the left side of the lower outer suit. There Is a closed sealing plate there now, below the suits left arm.
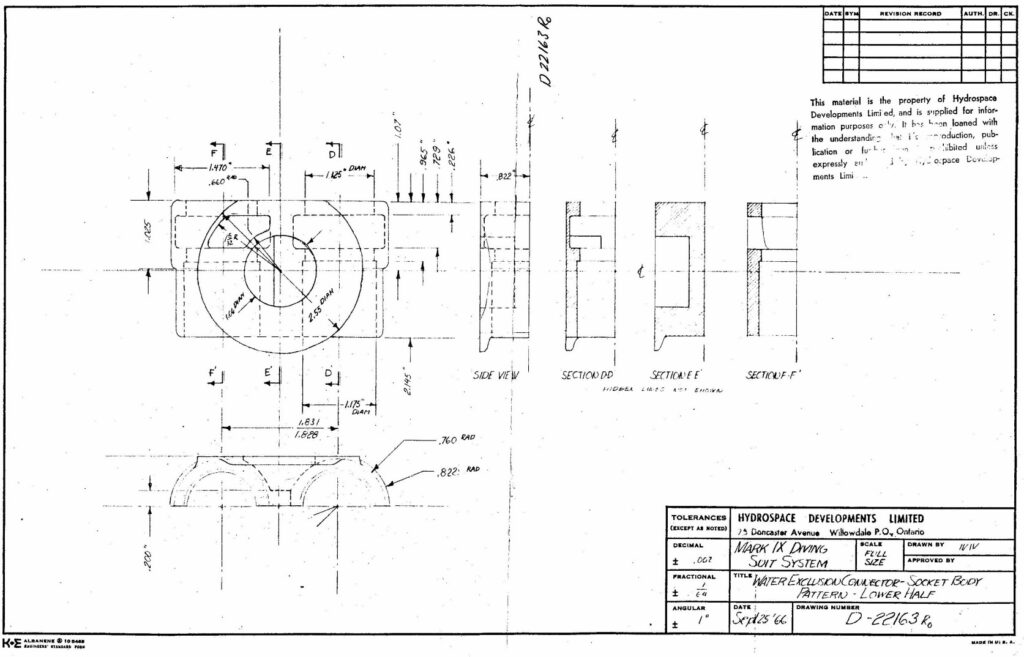
This is the drawing of the diving suit mounted, machined base of the non-water inclusion coupling. The upper half is still missing. The two pieces were cast in tough epoxy. Then they were machined and the other parts fitted. Close inspection will reveal that there are separate paths for the input and output. The base was then epoxied to a wide metal part that formed the connector for the internally counterlung.
We had a tough reinforced neoprene counterlung system that was laid-up to conform to the divers upper body. There was no buoyancy unbalance and these ‘counterlungs’ didn’t interfere with the diver’s agility!
But we had to out-source the ‘counterlungs’ as we didn’t have the abiliy to mould the needed shape ‘with rolled-over edges’ that could meet the very stringent non-leak specifications!
I have been sorting out the drawings in whatever spare time I can take. Somewhere I have several photos of the various stages of the development of the suit.
I even have drawings of my version of the Diving Computer. We attempted to get a license but Spar Aerospace blocked it for several years. They never even were able to put it out on the market.
With these ‘multiple layer’ diving suits there was a inner gas-tight butyl rubber suit originally produced for use in toxic (nerve) gas usage. Minor Rubber of Granby, PQ manufactured it in rolls. This material was very easy to fabricate and we were able to achieve a gas-tight bond!
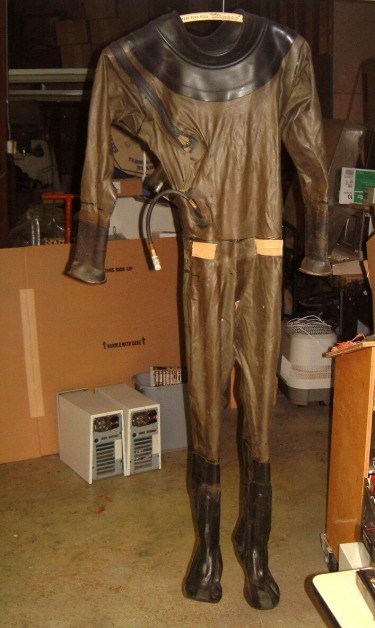
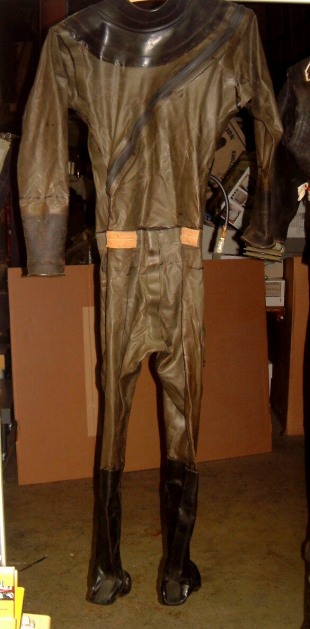
This gave us an extra layer of protection against contamination of the respirable gas from contamination. What was first planned for Freon at shallower depths paid off. The butyl rubber suit had laid-up feet that matched the boots on the suit itself. With mixed-gas diving helum was often added to guard against nitrogen narcosis. With time several other inert gasses were part of the mix and the half-times had to be calculated!
We had also designed a much thinner suit that could be used with fins. We were able to import some of the pre-formed parts from England. Remember that we had to design all the lighter scale rubber mouldings for this lighter suit. This had to be put on hold, as we didn’t have the staff to complete the manufacture of all of the re-designed parts. I was just able to use a small ‘a heated rubber moulding press’ to make about a dozen set of parts!
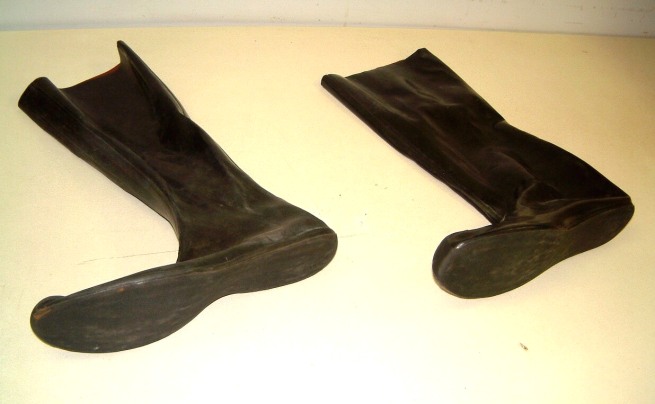
To return to the first design. It was made by numerous specially fabricated parts in the suit. Then I had to embark on a lighter design! As an example we needed thinner ‘rubber’ boots without heels. So I had diving fins made of cast urethane that would fit the boots. However they were too stiff to be employed. Then I found that with the correct moulding technique the rear part could be cast in place with a more elastic urethane. It had an unbelievable bond to the more rigid moulding at the front of the flippers.
Browsing through some spare cartons, I located one of the insulating suits that fit under the main (external) suit and the inner buty rubber suit. This was made of Flalon (TM) , a material that had a hollow core and thus emulated wool. This suit had a double layer of Flalon with a thin aluminized heat reflective layer.
The quarter inch felt boots were sewn on the ‘boots’ as shown to the right. I am still attempting to photograph this insulating suit.
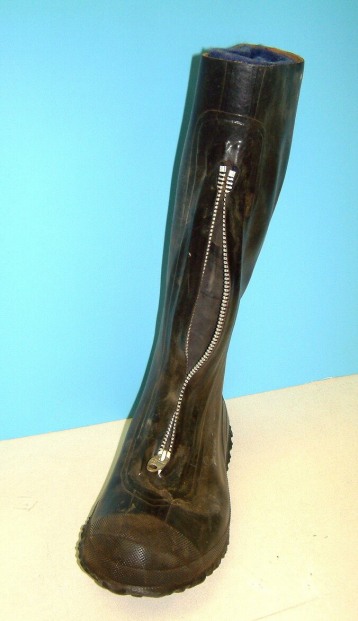
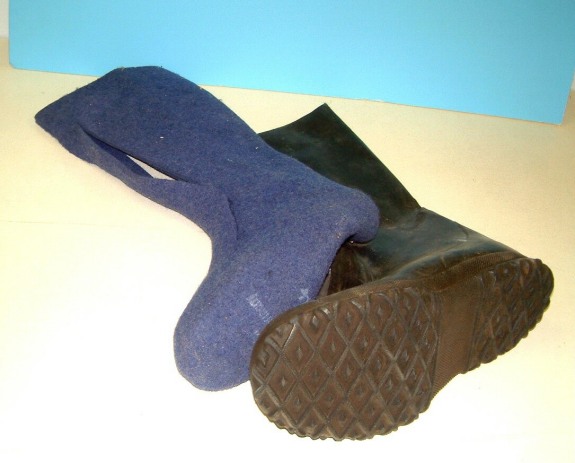
I have to go back, as these earlier boots had a felt liner made by the Code Felt Company in Perth, Ontario. The inner feet were designed to fit perfectly and there wasn’t any ‘play’ that could result in the accidental disruption of a dive.
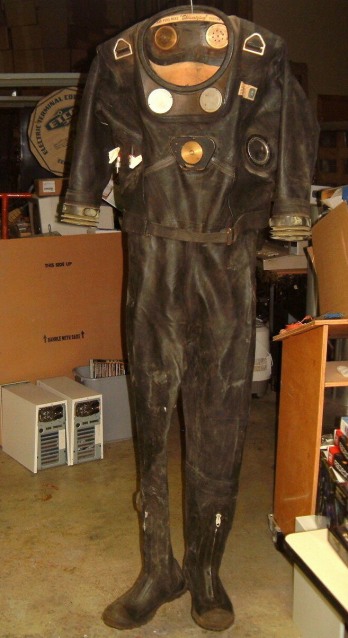
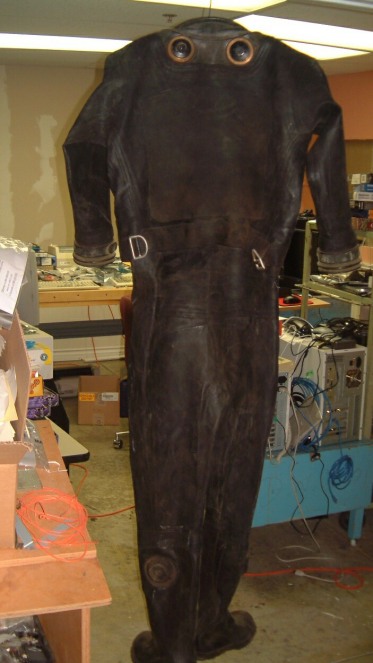
The front of the older outer suit is shown here, next is the rear view.
There was an obvious problem. The sealing zippers (manufactured by B. F. Goodrich) came in several options. We selected a type that was made with open ends. That required a sealing clamp with a wide top and a narrower bottom. As can be seen from the shots, it was manufactured so that it sealed on both the inside and outside with moulded Neoprene (on both faces) to clamp on the zipper. The screw clamp has an o-ring seal.
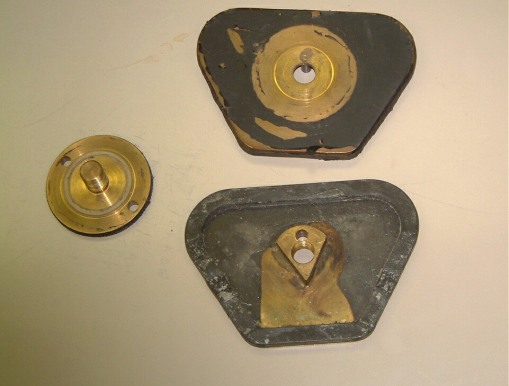
This was painted with a urethane modified epoxy that for 14 years was flat black, now almost forty years later the paint is peeling. The zippers, (and suit were packed in talc), however when we exhibited the suit about 1974 in the US, we had to remove the talc and clean the suit. Somewhere the detergent they was used stripped away the waxy coating and part of the zipper began to crack. None of the rest of the suit deteriorated including the curing adhesive used in fabrication. (comment – we were in the process of re-design to comply with the requirement for a lighter outer suit for saturation diving – as well as a much simpler design when WW moved from of Canada and we were not able to collect the remainder of the contracted fees).
There is a knit elastic inner suit that is the very first garment that the diver has to wear. It has an antibacterial coating that is also anti-chafing. Part of the suit (especially the cuffs) have very thin moleskin linings.
For the initial tests specially rigged apparatus was used. An example is below.
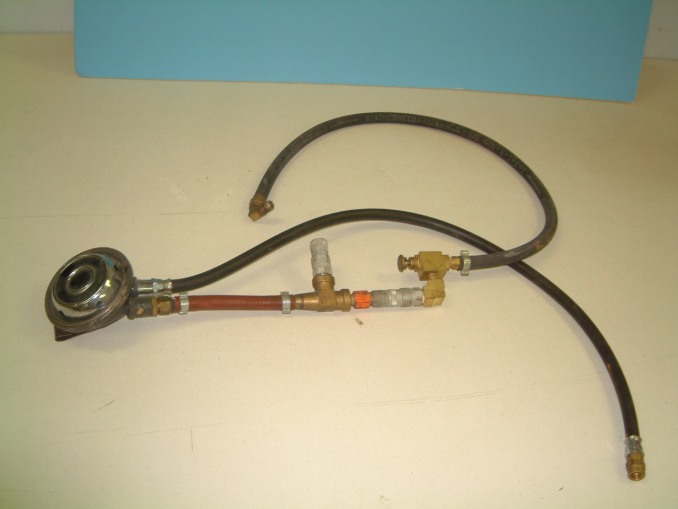
Some close-ups are below, such as the large fitting on the left side of the suit that was for an non-water leakage dual coupling that could supply an emergency source for breathing gas.
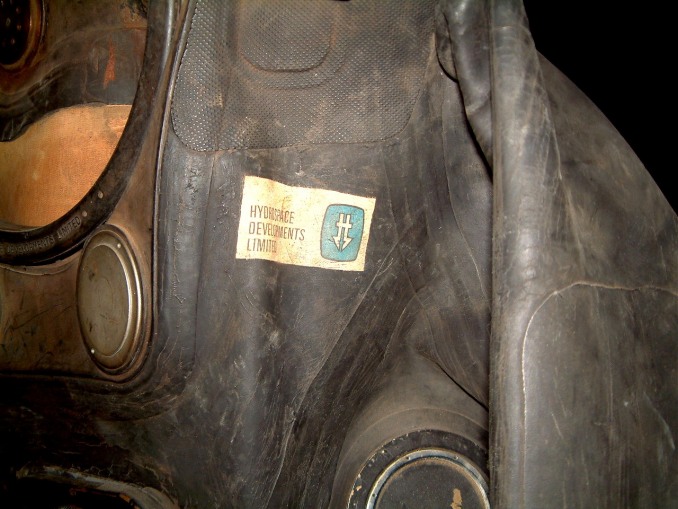
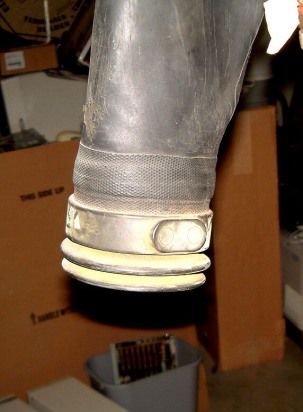
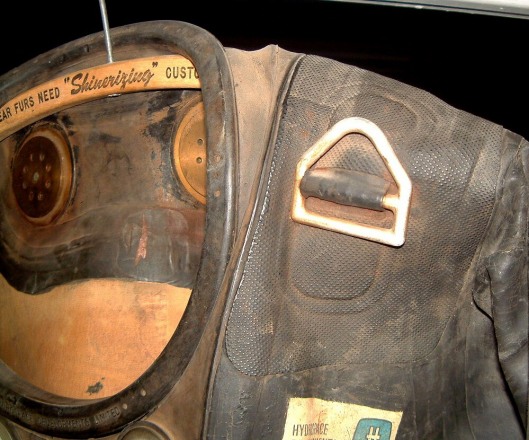
Wrist cuff seals
These suites were used in many actual dives. We had to redesign some of the monel parts replacing them with stronger stainless steel parts. Some things had to be redesigned so that the diver’s three finger ‘gloves’ could be used. As can be seen on the wrist’s provision was made for a heated water supply fitting on the cuff.
This type of suit was designed to accommodate several different uses. The ‘bib’ had two fittings on the rear and two more on the front. Short corrugated hoses connected to each side of the electro-formed part. These hoses were moulded so that there was a minimum amount of clearance between the corrugations. We used a tightly wound stainless steel coiled spring to further reduce the gap.
In this configuration, the breathing mixture was carried in a back-pack. Thus the reason for the fittings on the rear of the ‘bib’. There were two ways that this suit could be used. A set of counterlungs could be added inside the suit itself. This minimized the loss of heat on extended frigid water dives. The suit was designed for extended use in frigid water. In warmer conditions, less insulation would be needed.
Hydrospace Developments Ltd., also manufactured Portable Decompression Chambers. These were designed to mate with the Hyperbaric Chambers uses in most hospitals. In 1976 the flange specification was made a standard. We sold some to universities specializing in diving for underwater archaeology . As these chambers would fit in a single engine Beaver on floats, they were popular. Afterward we learned that this chamber was able to fit several other aircraft. We had a customer call us from Greece where a helicopter was able to carry a diver back from a deep diving site where the due to an unexpected regulator failure he was forced up to the surface without proper decompression.
The passenger in the right seat is able to control the chamber ‘remotely’ as he can communicate with the diver. As the controller makes a recording of the pressure during treatment, it can be checked afterwards.
A set of four tanks is able to supply the breathing gas for an hour. A larger cylinder can be used with aircraft that can carry larger loads.
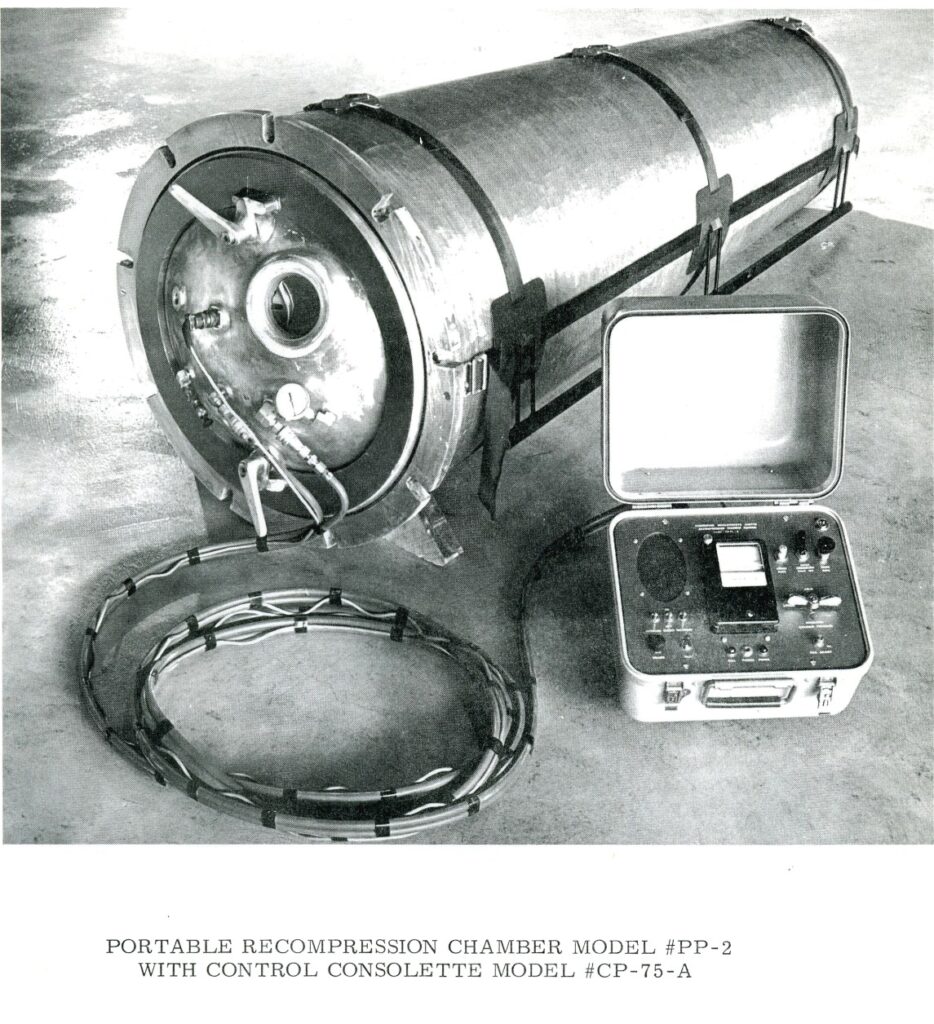
We marketed these until we were informed that we were unable to get liability insurance. The lobby for US Steel Institute was able to ban all non-ferrous pressure vessels. So we were not able to sell them to any US based company. However we found out, that these could be sold for hospital treatment. This would allow a much-more sophisticated control system to be employed as these much larger (diameter) systems did not have to be portable. As they had two identical Lexan ™ halves, it would reduce the cost of tooling. One possible problem was that both shells were held together by pieces of extruded aluminium. So a lot was resting on the seal. As designed it was a wide extruded band manufactured of a class of elastomer that was impervious to degradation by oxygen. Another concern was would both halves be easy to separate? There was the possibility of the use of a type of device that could hinge, either at one side or attached to a central location. As this could be incorporated in the design of the moulds it did not seem serious. But there was more worry about the cost of the injection mould! Discussions were made with the manufacturers in Denmark. They made it very clear that nobody had the needed experience with an injection mould of that size, especially with Lexan ™ .
Recompression System Information.html
J. F. from BC, contacted me requesting a job as a experienced diver citing his friendship with Ben Ackerman. I agreed to retain him only as a part subcontractor for $350 a week for any diving that was required, he was responsible for paying his own taxes. Thank heavens that I had a signed agreement! At the time I was drawing $100 a week.
As Spar Aerospace insisted on not licensing the decompression ‘computer’ so I designed a six gas electronic equivalent. Spar threatened to sue. I dropped it. Now the same thing is common. Spar never made it.
To bolster Hydrospace Development’s income, they bid on a contract to erect an offshore tower in Lake Ontario. I was doing R&D myself ; where I had applied for a patent on the condition that the Canadian Governments Inland Waters Branch would not divulge the anchoring method that I intended to employ.
I had developed a mooring for a mast system. It used three screw in anchors on each of the three guy wires. Each set of screw-in anchors was at a mutual angle of sixty degrees. This way vibration on the guy wires could not ‘work’ the anchors free. Until this time NRC had been relying on four hundred pound concrete weights to anchor the masts on the sandy bottoms. And every time a storm blew in, the masts would topple. Using my system the mast weathered four seasons without a problem.
We also received another contract from the Governments Inland Waters Branch to perform a bounce dive to a depth of 400 feet to retrieve a string of Nanson Bottles (employed for retrieving samples of water these devices were set to capture the samples over time-the usual method is to employ a water-soluble filament that would not affect the water sample). The string was somehow caught and had to be cut free. The Vessel used was the Theron. The Theron was mentioned by Vilhjamer Steffanson. It was registered in Norway and was used in arctic exploration. I knew that her captain was very fond of brown goats milk cheese and Norwegian roe paste (it is packaged in tubes – I remembered that Leonard Holst of Holst Point, Minaki used to ask me if I ever located a source – he would order some. So with that knowledge I was able to buy three pounds of cheese and a dozen tubes of roe. So after we boarded the Theron I was able to present the captain with a present. We were seated at the captain’s table during the voyage.
( Footnote: My uncle ‘Agar Wright’ was a surveyor for Captain Charles in Churchill where he corresponded with Vilhjamer Steffanson).
I hate to say it but have learned the hard way, that I can never trust the Canadian Government, for it immediately called for bids on other anchor locations. They had no intention of respecting our signed agreement. Because the Canadian Patent System requires strict non-disclosure, before a patent can be granted, I lost my patent! To make matters worse, I was informed that I would have to apply for a very expensive way to recover any of my rights. Phooey! (I learned three years later that JF might have made copies of the patent application and may have disclosed it to a competitor.
Hydrospace Developments Ltd. Had been contacted by Walter Wolfe of Montreal, to bid on a offshore (surface) facility for 5 to 6 divers and a submersible Diving ‘bell’ .
As we had just completed two new suits using monastral orange pigment, we took them to Miner Rubber to be autoclaved. We had just received the injection Lexan faceplates and had redesigned the outer hard hat so it was able to fit. I made four of them and there wasn’t any clearance problem.
I had redeigned the urinal so we could use saline solution to inflate it.
We proposed that a heavy base plate could be dropped down using the cranes on the well platform. Once it was placed and secured by weights, the guide cables world stabilize the bell as it winched down to the heavy base plate. Not only would it stop the pendulum effect that increases when the hosting cable shortens. This would decrease the time spent in shift changes essential when sudden storms threaten a drilling rig. I found out by accident when J. F’s bank called me as John Flury’s boss that J. F. was having a large amount of funds transferred to his account by Walter Wolfe in Montreal.
The contract was handled by B P,E, S, & W; through W.B. (W.B was later employed by C, B).
Unfortunately KD Marine had borrowed funds from a Hong Kong Banking firm; they insisted on a short delivery schedule as WW wanted to have as many rigs operational. We didn’t know where he obtained financing. We did know that he wanted the rig to be ready for use in two years. When we were contacted this was possible, but Wolfe kept delaying things monthly (probably to obtain financing), until we told him there was no possibility that it could be ready in seven months. We had no idea that Woolf was so deeply in debt. He tried to flog some property he owned along the banks of a river where he had his ‘plant’ to a Cousin of mine. I knew where it was located as the summer before, a commercial aircraft had flown over the area and I thought was able to observe the location of Woofe’s property. I wasn’t sure that I could locate WW’s area. But I was able to observe that excepting for the riverbank where there was a wide strip of development, the area further inland seemed to be swampy. I thought the sale was a scam as no developer would be able to build a large airport in the limited space.
Then he offered to build the complex himself on the basis that we would be compensated for all the months of planning and design. It never happened as W. W. had relocated off shore and the lawyer Walter.B., involved didn’t check to assure us that the R&D count be licensed to another similar company in another country!
I don’t have the special non-water inclusion mating-connector anymore; as it and other fittings were stolen by J. F. (a former employee), that gained access to our plant well over the two months after he’d been dismissed for cause.
We’d changed the locks on all the outside doors but were required by our landlord to give him a duplicate to one on the inside doors. Protesting that was a breach of tennants rights was useless.
JF talked our landlord’s son into unlocking our plants inner door. The result was that I lost several thousand’s of dollars of special diving equipment. When I went to the police to lay a charge, (at the time he was an employee of KD Marine, and had moved from Quebec to an offshore location near Italy).
Then I received a telephone call from a BC rental agency that specialized in Deep Sonar Apparatus, J. F. claimed that he had lost $22,000 of sonar apparatus when a boat capsized.
But the reason for the call, was that the same apparatus had been returned for service to the manufacturer. The rental agency was being sued by their insurance company and I was a former employer of J. F.! When I explained to them that J. F. walked off with a hell of a lot of both my own diving gear including a four stage electric 2800 psi breathing air compressor along with the needed filters as well of that owned was owned by me, not Hydrospace Developments Ltd.
Although by this time I knew that J. F. was a Swiss citizen and suspected that he hadn’t yet served in the Swiss Army
Four months later his plane had to make a weather related landing in Switzerland where he hadn’t served his time in the army, he was arrested and had to serve in the army.
Hydrospace Developments Ltd received only $5,500, and endless promises. Then Wolfe began incorporating a series of offshore companies. Finally he incorporated another company in Scotland.
Then Revenue Canada began to raise hell as J. F. hadn’t paid his taxes in BC, nor had he paid any taxes on what he was transferred to his account in Ontario. I gave the name of the bank he used when he was here and gave them a notarized copy of our subcontractor contract. I was informed that so long as J. F. stayed out of Canada he was free. But if he came back to Canada I was to notify Revenue Canada.
The final blow came when our landlord decided that he could increase the rent on our unit . He has thought that when he decided to pave over the gravel, he could jack-up our rent. My lawyer read the lease and stated that our landlord was ‘stupid’ at best. So I said ‘no-way’!
Then he conceived and end-run. If we wished to keep the same rental, we had to agree to move to another unit, at our expense. When I protested, he locked us out.
As I had reported the theft to the police about three weeks previous, so when I was locked out the police assumed that he was attempting to cover up his malfeasance and ordered him to allow us free entry so that we could relocate in Richmond Hill.
The new Lexan (TM) moulds for the tooling were made by nickel-plating a copper plated (and therefore conductive), epoxy casting. After about an inch of nickel was plated, the epoxy was carefully removed and the nickel was chrome plated to make it durable. Then the back of the die was reinforced and trimmed. We had a Shaw process casting made to form the mating die. After some machining to ensure that the three faces were parallel, we had over a dozen pieces of the face plates moulded and trimmed. We destroyed one of them in impact testing There were no fractures, but lots of dents.
(We were just attempting to prove to our own satisfaction that the parts that I had ordered would allow me to continue).
They met all of the specs! So I began to make a proper helmet out of stronger and lighter epoxy. I sawed a manufactured helmet in half and widened it. Then I used fiberglass to patch the helmet up, finishing it off with Bondo ™. to add to the width of the model helmet as needed to allow for the latching mechanism. Then I used the needed grade of sandpaper, as well as crocus paper, to obtain a mirror finish. This gave me a model for the outside of the helmet. I had to spray it with a water soluble parting compound.
I was then able to ‘pull’ a dozen parts. These were made from epoxy with a series of varying weave fiberglass reinforcing. After trimming them I then spayed them with a two component epoxy finish.
It took me a week to move by myself. I continued to salvage as much of the material I owned personally and as most of the rubber moulds were paid for personally or hadn’t yet been paid for yet and I had possession or all the bills, I had all of the proof I needed. so there wasn’t any problem.
But some of the ‘special rubber moulds were missing’ these included the parts for the silicone oral/ nasal face mask. It was a major loss! I had spent four months in its it’s design; it avoided the problems inherent in the old oral/nasal mask; that did not have a foolproof ‘retention’ part that would ‘lock’ it in place! However the new design was partially moulded of a stiffer silicone rubber; and the parts that fit the divers face and under his chin used a softer durometer silicone. We made certain that it had no possible detrimental reaction with the divers face. This allowed us to add a chin contured extention to hold the oro/nasal mask in place. Because there were two different durometers of silicone involved in the mask, the extensions needed for the connections to the rigid frame were easier to ‘lock’ in place.
As I stated, because of the circumstances we were forced to move too hastily and did not have the time to assure myself that all of the ‘special’ silicone moulds were there when we moved. Remember that I had over 6000 pounds of assorted rubber moulds to sort out and pack. There was a mess left from J. F. s ‘raid’ on my personal stock. As an example some of the custom Lexan parts were wrapped in special packing material to avoid scratching All of it was double packed so I asumed that the large double taped cartons were intact.
I have to admit that I did not think that J. F. would have the time to take as much of (what I had paid for- my personal components), as he did. That may explain why J. F. was able to take so much of my stuff. I remember that our landlord remarked the we must have been doing very well because J. F. had a large van with double wheels on the back.
Miner rubber had made over fifty feet of Hypalon Rubber using Monastrel Orange. It was very stable; so we had four diving suits fabricated; two had black rubber boots, and the other pair had two pair of non-return relief valves on the lower legs; that way the diver would be stable head upward or head downward (a swimmable version).
We had to abandon these boots as there wasn’t, any way that the diver could swim.
However, I was able to make a custom made pair of nickel-plated foot moulds for the divers (uninsulated) so called swimmable feet. I then was able to get five pair of the larger swimmable feet; by first using a water solution of sprayable ‘felt’ – and by wrapping it up tightly I was able to achieve about a 3/16 of an inch build-up to the larger outer swimmable boot; this used Hypalon Rubber that also used Monastrel Orange. Now it could be used be used with the largest sizes of swim-fins. The diving suit and the swimmable footware (with two non-return valves), were also stolen!
Remember J. F. had been fired for cause.
On December 20th, 1975, I received a letter from Revenue Canada telling me, (in essence), that although I had been taxed twice (once from Ottawa (and though there were two other directors of the corporation I was the easiest target). Then I received a duplicate statement from Revenue Canada’s Toronto Office. When I lodged another protest I was told to disregard this as it was an obvious error. The duplicate billing would be ‘reconciled’!
It never happened, so the amount that I now owed had been doubled!
Part of my error was that part of winding up the company were legal fees, I had included them as legal disbursements, but this was disallowed. Once more my amended return was somehow lost in the files! Now the excuse was that was it was sent in too late to be used. Even though I had begun sending it by Registered Mail and it was date stamped; it was disregarded.
Again I filed a protest; and I both phoned and sent a letter to be sure that the correction was made. Then to add insult to injury I was told in a extremely sarcastic manner I was told to retain a tax accountant to ‘sort out the matter’.
Although I was left with only the protypes of two suits and some unfinished spare parts, all of which I had purchased personally. I had transferred the titles to another corporation.
However, I had to undergo another several months of harassment. That’s when I began to think that some well-connected person could be orchestrating the whole matter!
Although I had kept records (some with the serial numbers from the manufacturers – which I had another ‘shell’ company pay for). The police had at least been able to track them to a Quebec manufacturer. Then they could not be tracked further. So what was I to do?
I had to abandon this R&D effort. Now it was quite certain that W. W. was involved; but I could not track him down! (I learned three and a half years later that WW had moved to Scotland and I didn’t have the funds to lodge an action).
The ultimate betrayal came when my patent agent in Toronto asked me to loan him some detailed drawings so that he could win a patent case in Europe. My drawings proved that I had proceeded the European filing by many years. I agreed upon minimal compensation; providing I should receive two complete diving suit system’s including tanks, regulators, decompression gauges etc. My fee was well over $25,000, and in exchange I would receive the aforementioned diving equipment, shipping, insurance and import duty’s + all taxes prepaid. I was informed that if he won the case and within a couple of months I would receive the new diving suits. As they has to be shipped by sea, I should expect some obvious delay. So I called him several times over three years, but there was always more BS. The promised cold water diving equipment never arrived!
Going back to K D. Marine, we always wondered why he moved offshore. We later made a connection when a Montreal associate told us that Woolf’s law firm was involved in financing a potential Prime Minister (B. M), and WW was putting up the money to repay the loan. When Woolf’s creditors were paid, Wally W was able to return to Canada.
The theft stopped part of the project and for personal financial reasons I was unable to hire more staff. I had developed tougher yet thinner materials, and had redesigned part of the helmet system. I had several conferences in Ottawa dealing with proposed modifications. Over a month later I went to Washington to visit the US branch. I had a photocopy of my drawings with me. The Diving development Officer was startled. He unlocked a filing cabinet and showed me a duplicate of my drawings. However the title block now read Bendix Corporation. It was very obvious.
I began to file for a patent for the ‘Holographic Sonar Return’ with Featherston Haugh in Winnipeg, Manitoba. They referred me to Smart and Bigger in Ottawa, Ontario. I first filed for a patent on the diving suit system, on the surface chamber (with a provision that to save weight on the surface chamber’s wound fiberglass cold be used). However as the weight of the submersible unit was not a problem, it could be a suitable grade of steel. As pendulating of the submersible was a serious hazard we proposed the use of air powered constant tension winches on the ‘base plate’ to act as a guide against pendulation, especially when the submersible component was above the water’s surface. As the hoisting cable becomes shorter the conservation of energy makes the pendulating effect hazardous. That was a major problem with any heavy submersible.
Then as I had not applied for a patent on the ‘Holographic Sonar Return’ system , I applied for a patent.
The black suit system was workable, but a less cumbersome helmet was needed. As the prototype helmets were stolen, I had to start from scratch. (I later found that WW had paid for the Lexan mouldings so I didn’t have the funds to order more).
As I stated I made a presentation to the Canadian Armed Forces diving officer in Ottawa and several weeks later I recognised my prints at the US facility in Washington, my title block had been removed and a Bendix title block substituted!
Remember that I had some moulded (three axis), faceplated made out of polycarbonate (Lexan tm) plastic. These six moulded parts were very strong, durable and impact proof.
Remember, that was the time that J. F. gained illegal access to our plant. Because of the theft, I was forced to move very quickly and didn’t have the time to tell what had been stolen. I rented a truck myself as I had to move up to Industrial Road in Richmond Hill. Only then did I realise what was missing. I estimated that well over $27,000 was stolen, including the Lexan (TM) face plates! As J. F. was no longer in Canada, the police couldn’t do anything!
As I said, I applied for a patent on the holographic filter. These drawings (that had to be revised to qualify), were to be part of the patent application
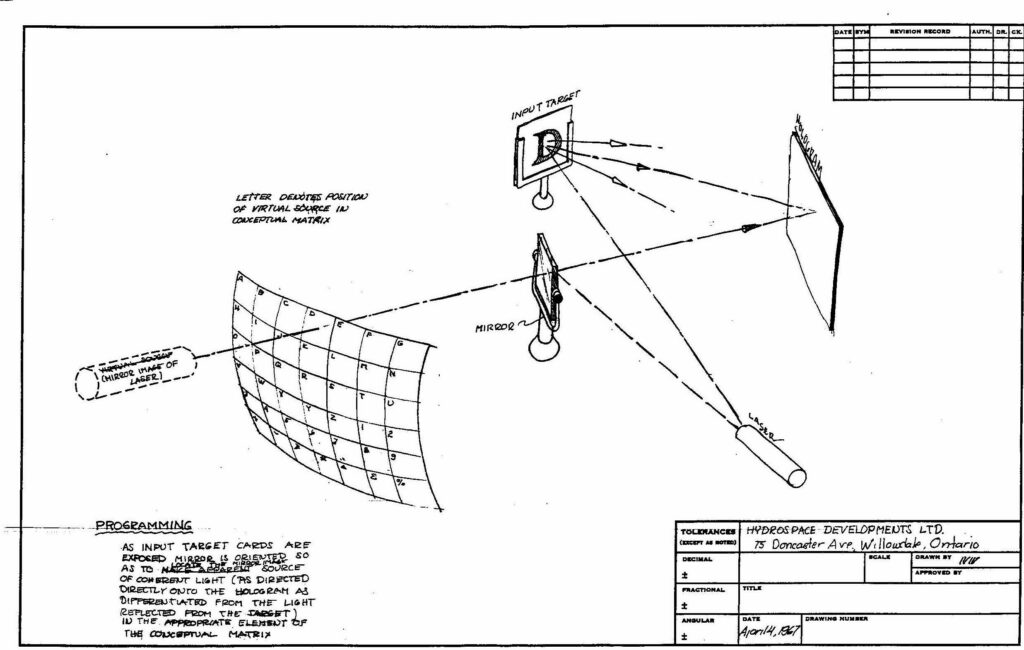
This is the ‘programming’ part of the complex filter.
Next is the reading (or output section) of the complex filter.
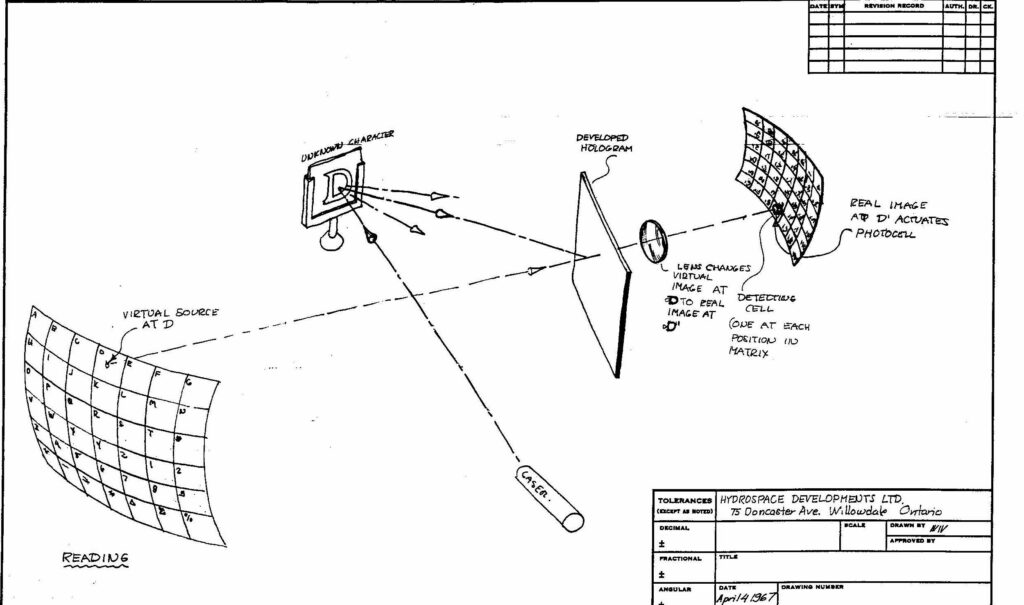
The obvious refinement is to produce a thicker transparent storage medium where tend of thousands of holograms can be stored. This requires the ability to tightly focus the ‘beam’ on and in to a very selective focus, where the data can be ‘written’. At this time the current technology doesn’t have the resolution. When near X-ray wavelengths can be employed the amount data that can be stored will be almost unbelievable!
We didn’t have the funds to complete the application because we were not paid for the design and because JF took so much of my own diving equipment including my high pressure (four stage) compressor as well as two Heinke regulators!
Thank heavens, all fitted. I had to wait while three of the maiting ‘non-water-inclusion’ couplings (for the backpack’ unit), were machined and (dyed to a selected color).
I managed to complete only one backpack before we had to move up to Richmond Hill.
Then I had to deal with the Canadian tax department. Because J. F., hadn’t paid the taxes on a lot of his income. That was one of the reasons he took off.
Settling this illegal claim took me the better part of a month of correspondence; and the end consequence was that I had to fold Hydrospace Developments Ltd.
I decided to get re-involved in the production of ESL’s. I had a 36″ x 64″ single ESL on display at the CNE. This led to the design and construction of a folding array of ESL’s for use in a nightclub. This led to the formation of Dayton Wright Associates Ltd. (Five years later I was able to get the fabric on a 1/4 inch Hypalon foam) and was able to fabricate some diving suits for friends.
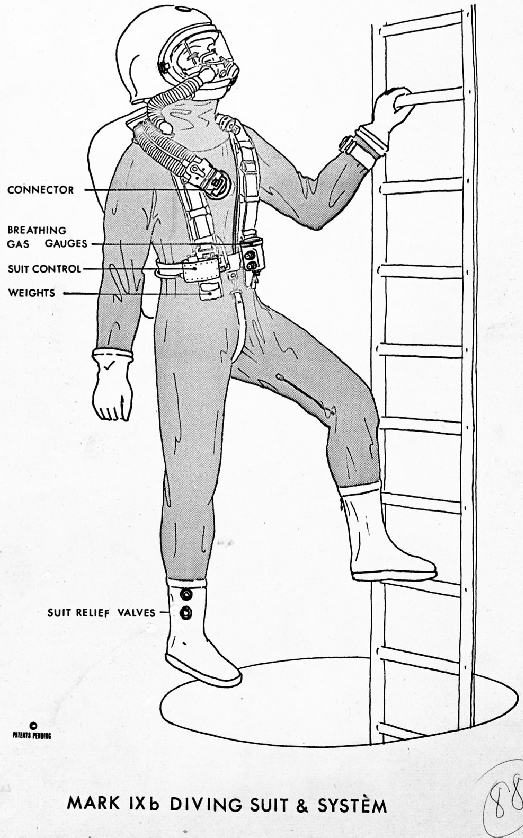
I would particularly like to learn more about the history of this system. Any information is welcome.
Where interest disappears, so does memory.
Johann Wolfgang von Goethe 1749-1832

Therebreathersite was founded by Jan Willem Bech in 1999. After a diving career of many years, he decided to start technical diving in 1999. He immediately noticed that at that time there was almost no website that contained the history of closed breathing systems. The start for the website led to a huge collection that offered about 1,300 pages of information until 2019. In 2019, a fresh start was made with the website now freely available online for everyone. Therebreathersite is a source of information for divers, researchers, technicians and students. I hope you enjoy browsing the content!