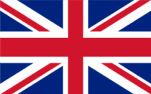
Royal Navy EOD rebreather
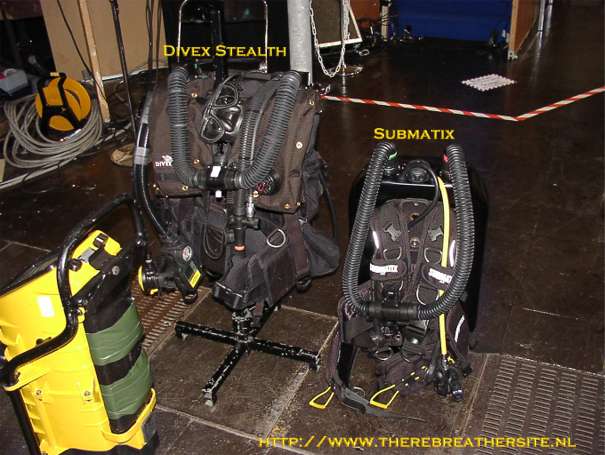
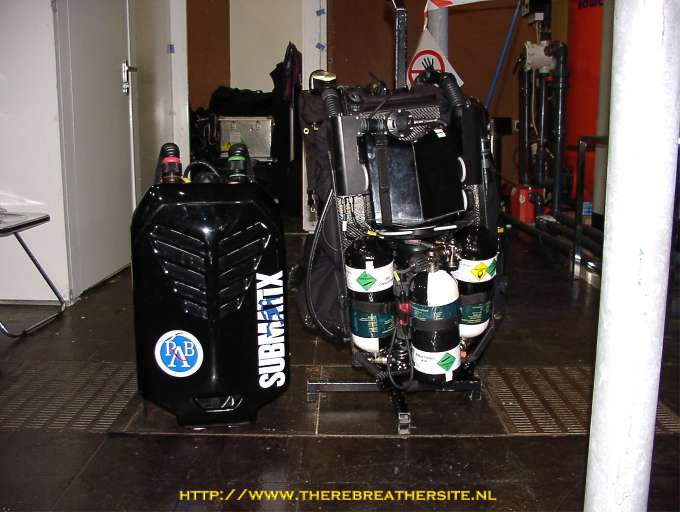
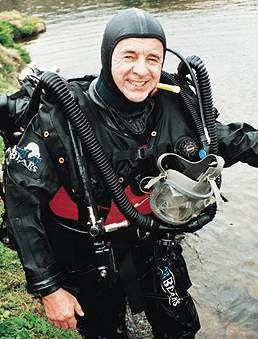
UCI Editor John Bevan visits Divex in Aberdeen to try out the Stealth rebreather, and to look at other products the company makes for the military diving market.
Following a period of steady decline in the offshore diving industry, particularly in the North Sea, Divex took the decision in 1995 to enter the defence industry. This began with the winning of a contract to build sixteen recompression chambers for Royal Navy diving and submarine rescue operations. The company’s progress since then has been outstanding by any standards. Today Divex is the largest supplier/manufacturer of diving equipment to the UK MoD, and has extensive experience of supplying military diving organisations worldwide.
kitting up Divex’s military rebreather, Stealth, is a prime example of the company’s ability to identify a customer’s requirement and come up with the most successful solution, even when set against all the established competition.
The story of Stealth started in 1995 when the Royal Navy put out a tender inviting proposals to provide the next generation of Explosive Ordnance Disposal (EOD) and Special Forces rebreathers. Using experience gained from the manufacture of the Secondary Life Support SLS bail-out rebreather used by saturation divers at depths up to 450msw, Derek Clarke (Managing Director) and James Bruce (Senior Project Engineer) started with a clean sheet and began designing from the bottom up what is now beyond doubt the world’s most advanced military mixed gas rebreather.
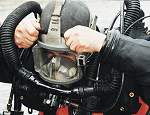
Rigorous
In 1998 Divex proudly announced that Stealth had entered service with the Royal Navy after two years of rigorous testing against other systems on the market. Today the RN has 30 sets in service and a further 25 will be added by the end of the year.
Divex’s Paul Haynes prepares the unit Since its introduction, Stealth has been internationally acknowledged and accepted. A major coup was the adoption of the set last year by the Federal German Navy for Mine Counter Measures and EOD operations. This was achieved in the face of stiff competition from both Draeger and Carleton Technologies. After 12 months of testing, the German Navy has already taken delivery of its first consignment, the total order being 205 complete systems over three years.
The French Navy has now tested Stealth to 80m at sea and 102m in wet chamber
trials; and other navies are also opting for the set, with the Italian, Spanish and Singapore navies being the latest.
Divex’s Stealth is an amazing success story!
So what is so special about the Stealth rebreather that has catapulted it to the forefront of rebreather technology? There was only one way to find out – suck it and see!
I eagerly accepted the invitation from Dave Smith, Divex’s Sales and Marketing Director, to visit the company’s headquarters in Aberdeen and to try the set out.
By coincidence, Lt. Luis Nunes, a Mine Clearance Diving Officer of the Portuguese Navy was also carrying out an evaluation of the Stealth during our visit, including some diving trials. The diving site selected was a flooded quarry outside Peterhead. The water temperature was a generous 5¼C. Well, it was the middle of June after-all!
We had the Divex ÔA-team’ in attendance. Our Diving Supervisor was Bob Thompson, Senior Technician, and diving partner Paul Haynes, Military Equipment Specialist and an ex-military diver who participated in the UK MoD testing of Stealth back in 1996. After our Portuguese guest had concluded his dive, I suited up and paid attention to the pre-dive briefing from Paul and Bob.
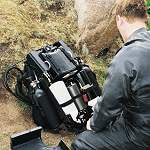
Simplicity
This is when I pleasantly discovered the relative simplicity of Stealth’s operation. I quickly appreciated the effort that must have been invested in its design because, despite the complexity of the set’s internal operation, the primary user interaction was reduced to monitoring a single LED light inside the mask. For all normal operation this was a steady green light, which meant that the diver had absolutely nothing to do to operate the set.
checking the data display module before the dive A secondary liquid crystal data display module was conveniently hung alongside the right arm. The display included current and maximum depth, elapsed time, and the status of a variety of components and consumables. Most of this data did not require the attention of the diver, and only if the green LED mask light started to blink or turned to red did the diver have to refer to the display module to check the set’s operation.
As we descended, Stealth automatically raised the partial pressure of oxygen (PO2) from 0.5bar at the surface to 0.9bar at our 12m bottom’. Had we continued deeper, the Electronic Oxygen Controller would have continued to gradually raise the PO2 to 1.3 bar. From 18msw down, the PO2 would then have remained fixed at 1.3 bar regardless of the depth.
With changing depth, the speed of response of the mixture to maintain this partial pressure is well ahead of any competitors because the Electronic Oxygen Controller was designed to control within a miniscule 0.02 bar of the oxygen set point. The PO2 is monitored by three independent sensors. The dual redundancy electronics package operates a voting system between the three sensors, so that if one began to fail it would be voted out by the other two.
The next thing I noticed as I prepared to dive was the relatively light weight of the set, a mere 23kg. When I put on the full-face mask, I was also impressed by the imperceptibly low work of breathing. Paul pointed out, and required me to demonstrate, the simple switch operation on the front of the oral-nasal mask for the changeover from closed circuit to open circuit bail-out – a fundamental safety feature.
Once in the water, or perhaps I should say liquid peat, we made our way over granite boulders down to 12 metres. As we sank into the dark brown gloom, I mused that by adding a little flavouring we could sell this water as Guinness. As the depth increased, I could sense the extra diluent gas (air in this case) being automatically added into the breathing loop to compensate for the compression of the counterlungs. On the bottom, Paul carried out routine checks.
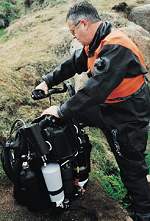
Green LED
A steady green LED light in my mask reassured me that everything was working normally and that the set was doing all the thinking for me. I could relax and devote my entire attention and both hands to the job in hand (crawling over granite boulders). The set’s low profile meant I could hardly tell it was there. It was so quiet that I could distinctly hear Paul’s occasional comments to the surface over the Divex through-water communicator.
After a circuit or two of the bottom (the boulders all looked remarkably similar and the bottom was singularly lacking in the usual supermarket trolleys or other useful reference points, we began our ascent.
The set could have given me 3-6 hours at the bottom of the quarry, and with the controlled oxygen partial pressure of 1.3 bars it could have given me a maximum no-decompression depth of 18msw – very beneficial I was told for Special Forces divers covertly locking in and out of submarines.
Ascending was a slightly novel experience because this time, in addition to ensuring the adequate venting of my drysuit and Stealth integrated buoyancy compensator, some additional attention had to be paid to the venting of the counterlungs. A standard exhaust valve had to be opened to ensure continued comfort of breathing during the ascent as the gas in the breathing circuit expanded.
Following a most enjoyable dive, and useful quarry reconnaissance, I soon realised that I had become an instant convert. This was what the Stealth rebreather was all about. The next step was to return to the luxury of Divex’s indoor training tank to try out yet another of the Stealth’s unique features. Once back at Divex’s headquarters, I was shown around their state-of-the-art lecture room. Then, as if driven by osmotic pressure, we ended up at the training tank. Rigged once more in the Stealth, I climbed down the ladder into the tank.Waiting for me at the bottom was what looked like a twin SCUBA set.
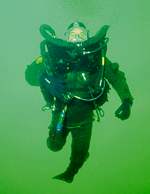
Add-ons
However, this was a special rig called the Supplementary Breathing Supply (SBS). Among other add-ons, it had a special whip fitted with a quick-connect-disconnect termination. The primary purpose of the rig was as an additional emergency gas supply for decompression stops, for the SBS would normally be deployed beneath the dive boat.
The exercise for me was to disconnect the open-circuit emergency bail-out supply hose on the front of the Stealth Dual Mode Full Face Mask (while continuing to breathe in the closed-circuit mode), connect to the emergency SBS supply, then switch to the external emergency gas supply on open circuit. As of this point, the diver has a plentiful supply of open-circuit gas for his decompression, including 100% oxygen for the shallower stops.
The next diving exercise was a demonstration of the Divex Digicom 1000 Diver Through Water Communicator (DTWC). For this I was kitted out in a SCUBA air set with full-face mask. A small communications transceiver was strapped to the side of the air cylinder, the straps of the mask housing the two earphones. This tiny through-water communications unit can operate over a range of up to 1000 metres, and following a competitive tender it is now in service with the Royal Navy, the last of over 800 units being delivered last year.
Once back in the water, I tested communications with Paul – perfect! There was a press-to-talk button on the front of the mask.
This demonstration did not take very long because there was not much I could talk about from the inside of a tank, other than how remarkably clean it was.
With the wet session over, it was time for the debriefing. I was particularly interested in the design of the rebreather, and I wanted to know what made it such a superior set.
First, the Stealth has been designed to be as simple as possible to operate and to maintain in the field without specialist technical support. For example, no tools are needed to dismantle or assemble the set. Second, whatever hypothetical component or even procedural failure occurs, there is sufficient redundancy and/or fail-safe modes to permit the dive to be safely aborted. You only need to see the 2-inch thick Failure Mode, Effect and Criticality Analysis documentation to see the amount of work that has gone into this. The report documents the potential failure modes of every single component that makes up the system from a second stage diaphragm to a resistor on a printed circuit-board. Using this information, failure modes critical to the safety of the diver were designed out.
Rapid response
The rapid response of the set to changing depth and consequential adjustment of the mix to maintain the oxygen partial pressure is a major safety feature that greatly reduces the risks of hypoxia, hyperoxia and decompression sickness – diving risks with which we are all familiar when using open-circuit equipment, but which are further increased when using rebreathers. The facility to switch instantly to open-circuit on the diluent mix with a simple turn of the valve at the oral-nasal mask is a fundamental emergency safety feature.
Yet another extremely important feature in the routine 3-monthly maintenance check of the set is the ability to check the linearity of response of the three oxygen sensors, in situ, up to 2.5 bars PO2. It is understood that other manufacturers check only up to 1 bar (ie, calibration in 100% at sea level).
Another of the many unique features of Stealth is the Data Acquisition capability. After diving, a PC can be linked to the set to download all information regarding the status of the equipment throughout the dive. This is extremely useful to military dive planners.
The set comes in two different configurations – the Stealth SF for the Special Forces, and the Stealth EOD for Explosive Ordnance Disposal and Mine Counter Measures.
The tour of the Divex facilities was an impressive experience. Where the Stealth sets were being assembled and tested, James Bruce, co-designer of the Stealth, showed me a bank of 10 sets undergoing final assembly.
Meanwhile, in separate workshops, I saw the assembly lines of several of the other military products, including:
- Oxymax Oxygen Rebreather. This provides up to 3 hours’ endurance and is simple to use and maintain.
- Enclosed Space Diving System (ESDS). This is for diving in extremely confined places, such as the space between the casing and pressure hull of a submarine.
- Dirty Harry. This breathing system is used by military and commercial divers in polluted waters.
- Diver’s Electronic Beach Reconnaissance Aid (DEBRA). An electronic compass, Doppler velocity log, GPS, automatic logging of depth and height above the seabed, all fitted into a hand-held board, revolutionises beach reconnaisance.
- DCC refurbishment and maintenance. Divex provides refurbishment and maintenance for many RN compression chambers.
- Enclosed Mine Lift Bag (EMLB). The Mine Lift Bag has entered the 21st century with Divex’s EMLB, which is now computerised and endowed with its own Ôintelligence’. It can vary its inflation time between 0 and 90 minutes and delay its inflation for up to 45 days.
- Diver Hand Heating Equipment. For protracted operations in cold water to maintain manual dexterity and protect the health of hands.
- Therapeutic Hyperbaric Oxygen Rebreather (THOR). This is designed for injured divers who require hyperbaric oxygen treatment.
- Counter-terrorist equipment. Divex also supplies a range of maritime counter-terrorist equipment used by Special Forces who have responsibility for assaulting offshore installations should they fall into terrorist hands.
What is DIVEX?
The Divex vision statement reads as follows: “For Divex to be the first choice of international underwater operators for products, support services and technology”.
In order to consolidate its position in the diving industry and deliver on this vision statement, Divex has, over the years, acquired a considerable number of well-known companies. On the diving equipment side, these include:
General Diving Systems
Submarine Products
Sub Sea Services
Underwater Instrumentation
Foundrometers
Spiro Diving Services
Dive Dynamics
Kinergetics
Gas Services
Circle Offshore
UWI Circle
Plus, on the hyperbaric systems side:
Aqualogistics
Kinergetics
Clearbook Engineering
Magpie Engineering
Mara Engineering
Offshore Marine Engineering
Seaforth Engineering
Hyox
Article kindly provided by Underwater World Publications Ltd.
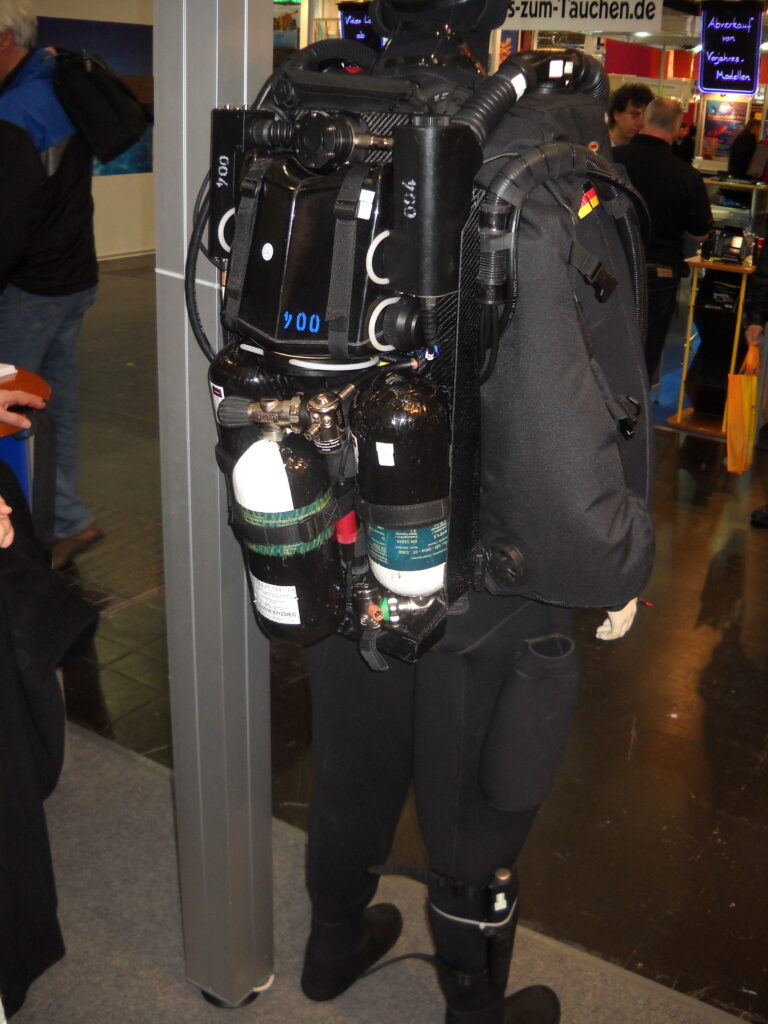
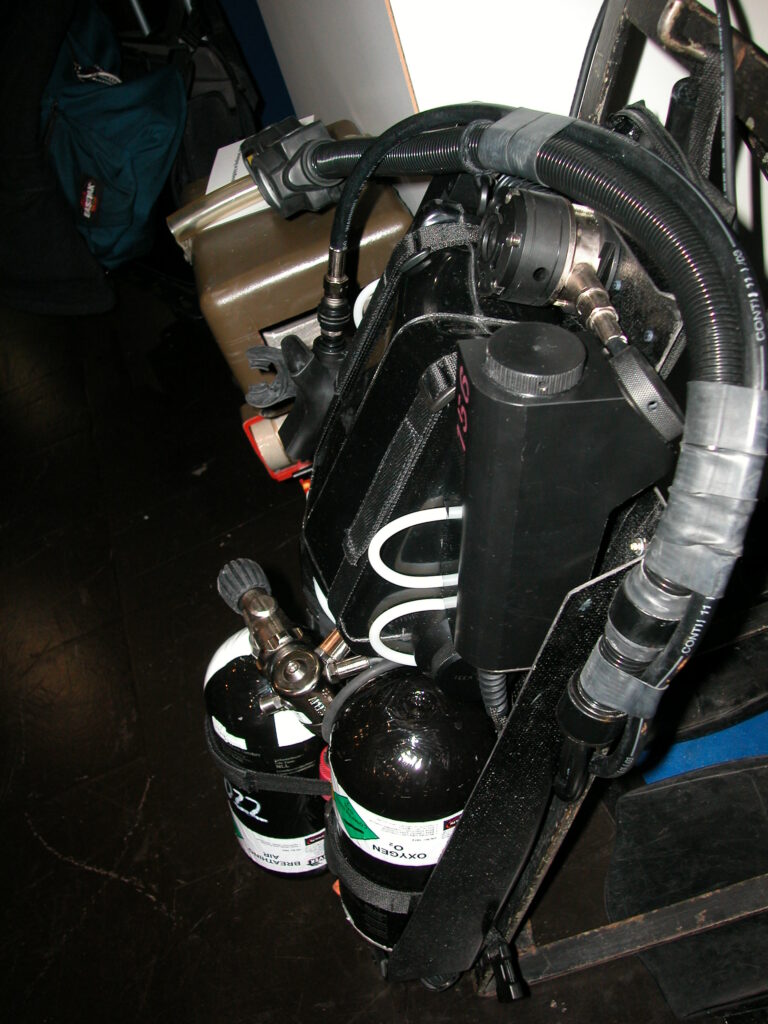
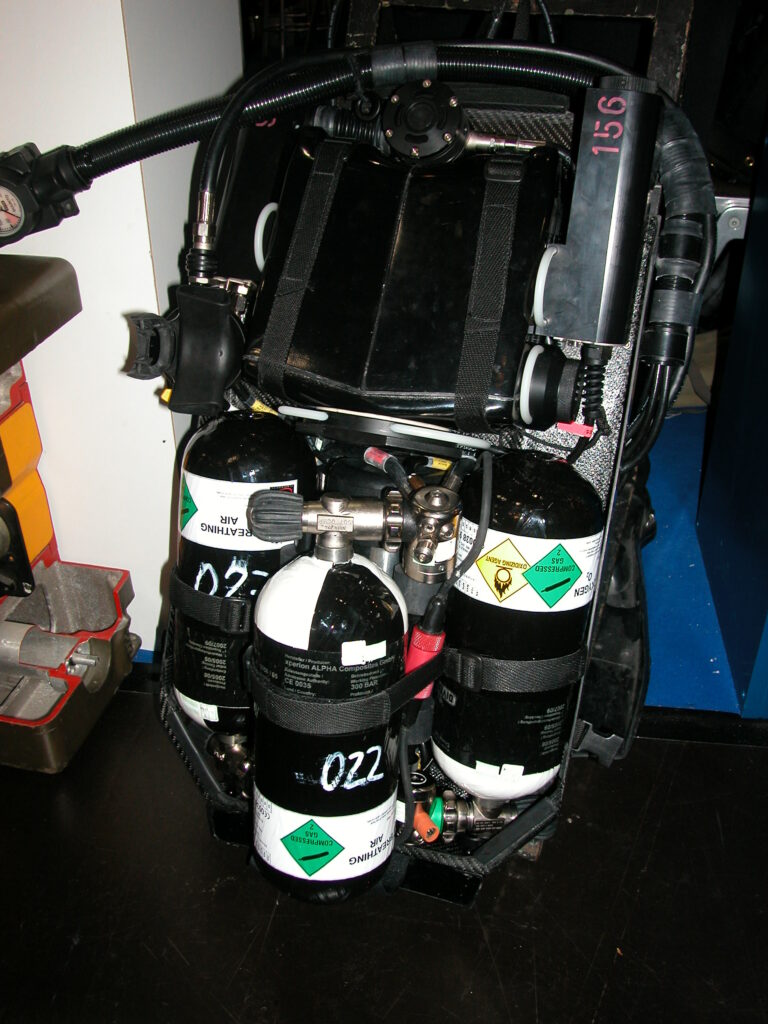
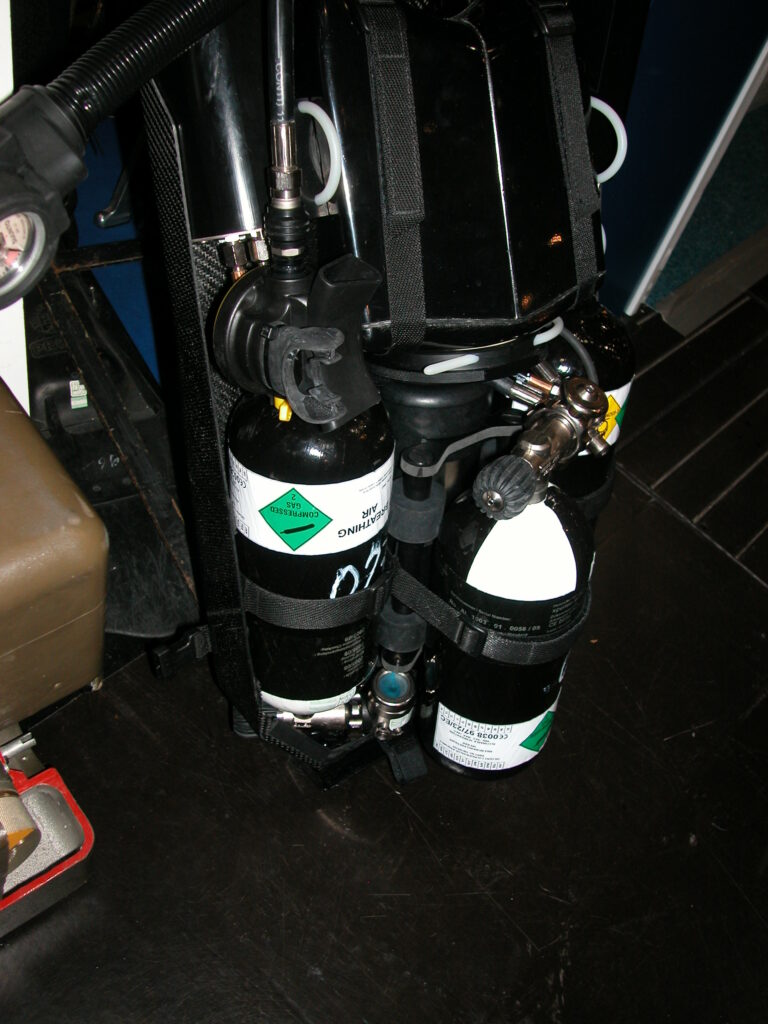

Therebreathersite was founded by Jan Willem Bech in 1999. After a diving career of many years, he decided to start technical diving in 1999. He immediately noticed that at that time there was almost no website that contained the history of closed breathing systems. The start for the website led to a huge collection that offered about 1,300 pages of information until 2019. In 2019, a fresh start was made with the website now freely available online for everyone. Therebreathersite is a source of information for divers, researchers, technicians and students. I hope you enjoy browsing the content!